Introduction
It is important to discuss the Welder Health Risks and their impact.
The topic focuses on the relevance of these risks to US companies and industries.
Welder’s health risks in the US pose significant concerns, with exposure to harmful fumes and toxins.
US companies are actively addressing these issues through improved ventilation systems, personal protective equipment, and stringent safety protocols.
Protecting welders from respiratory ailments, eye injuries, and skin hazards is a top priority for these firms.
This effort enhances employee well-being, productivity, and reduces workers’ compensation costs.
Additionally, compliance with safety regulations and fostering a culture of workplace safety ensures legal and ethical responsibility.
Therefore, US companies’ proactive measures to mitigate welder health risks are not only a moral imperative but also a sound business strategy, benefiting both workers and organizations.
Overview of Welder’s Health Risks
Explanation of common health risks faced by welders
- Inhalation of toxic fumes and gases
- Exposure to ultraviolet (UV) radiation
- Risk of burns and injuries
Inhalation of toxic fumes and gases
Welding involves the melting of metals, which can release toxic fumes and gases.
These fumes contain hazardous substances such as chromium, manganese, and nickel. When inhaled, these toxins can cause respiratory problems, lung diseases, and even cancer.
Exposure to ultraviolet (UV) radiation
Welders are constantly exposed to ultraviolet (UV) radiation emitted during the welding process.
Prolonged exposure to UV radiation can lead to eye injuries, including cataracts and permanent damage to the cornea.
Risk of burns and injuries
Welders work with extreme heat, sparks, and molten metal, which puts them at risk of burns and injuries.
Contact with hot metal or sparks can cause severe burns, while flying debris can lead to eye injuries. Additionally, welding equipment poses risks of electric shock and fires.
Statistics and data on the prevalence of these health risks
It is important to understand the potential health risks associated with the profession of welding.
Welders are exposed to a variety of hazardous conditions on a daily basis, which can have long-term effects on their well-being.
Despite the potential hazards, the prevalence of these health risks among welders is alarming.
According to a survey conducted by the Occupational Safety and Health Administration (OSHA), approximately 500,000 welders in the United States are at risk of exposure to toxic fumes and gases during their work.
In terms of UV radiation exposure, studies have shown that welders can receive up to 10 times the recommended annual dose of UV radiation for outdoor workers.
This highlights the significant risk welders face in developing eye-related health issues.
Transform Your Career Today
Unlock a personalized career strategy that drives real results. Get tailored advice and a roadmap designed just for you.
Start NowFurthermore, burn injuries are common among welders.
The Bureau of Labor Statistics (BLS) reported that more than 4,000 welders suffered non-fatal burn injuries in 2019.
The high prevalence of these health risks emphasizes the need for proactive measures to ensure the safety and well-being of welders in the workplace.
Employers and regulatory bodies have recognized the importance of addressing these risks through various initiatives and safety practices.
It is crucial for companies to prioritize the health and safety of welders by implementing proper ventilation systems, providing personal protective equipment (PPE) such as respirators and welding helmets, and conducting regular health screenings.
Additionally, training programs and awareness campaigns can significantly contribute to the reduction of welders’ health risks.
By actively addressing the health risks faced by welders, companies can create a safer work environment and protect the long-term health of their employees.
Read: Diverse Welding Opportunities: From Oil Rigs to Art Installations
How US Companies are Addressing the Health Risks
Implementation of safety protocols and standards
- Required use of personal protective equipment (PPE).
- Training on safe welding practices.
US companies are taking proactive measures to address the health risks associated with welding.
They understand the importance of implementing safety protocols and standards to protect their workers.
One of the key steps taken by these companies is mandating the use of personal protective equipment (PPE).
This includes items such as welding helmets, gloves, and safety glasses.
By requiring workers to wear PPE, companies ensure that their employees have the necessary protection against potential hazards.
In addition to PPE, US companies are also providing training on safe welding practices.
This training equips workers with the knowledge and skills to perform their tasks safely.
It covers topics like proper handling of welding equipment, safe working practices, and hazard identification.
Use of ventilation systems and engineering controls
- Installing local exhaust ventilation (LEV) systems.
- Utilizing fume extraction guns and hoods.
Another way US companies are addressing the health risks is through the use of ventilation systems and engineering controls.
These measures help to minimize the exposure of workers to hazardous fumes and gases.
Companies are installing local exhaust ventilation (LEV) systems, which capture and remove potentially harmful welding fumes at the source.
These systems consist of hoods or enclosures that are placed close to where the welding is taking place.
Transform Your Career Today
Unlock a personalized career strategy that drives real results. Get tailored advice and a roadmap designed just for you.
Start NowThey effectively draw in the fumes, preventing them from spreading to the surrounding work area.
Furthermore, companies are utilizing fume extraction guns and hoods.
These tools are designed to directly extract welding fumes away from the worker’s breathing zone.
By positioning the extraction gun or hood close to the welding arc, companies can effectively remove harmful fumes before they are inhaled.
Regular health monitoring and medical screenings
- Consistent medical check-ups for early detection.
- Monitoring of lung function and overall health.
US companies also prioritize the health of their welders by implementing regular health monitoring and medical screenings.
These initiatives aim to detect any health issues early on and provide appropriate treatment or preventive measures.
Welders are encouraged to undergo consistent medical check-ups to assess their overall health.
This includes monitoring their lung function, as well as checking for other potential respiratory or occupational health concerns.
Regular medical screenings allow for timely intervention and the ability to address any health conditions promptly.
In essence, US companies are actively addressing the health risks faced by welders through the implementation of safety protocols, the use of ventilation systems and engineering controls, and regular health monitoring.
These measures demonstrate their commitment to safeguarding the well-being of their workers and creating a safer work environment.
Read: Work-life Balance: A Day in the Life of an American Welder
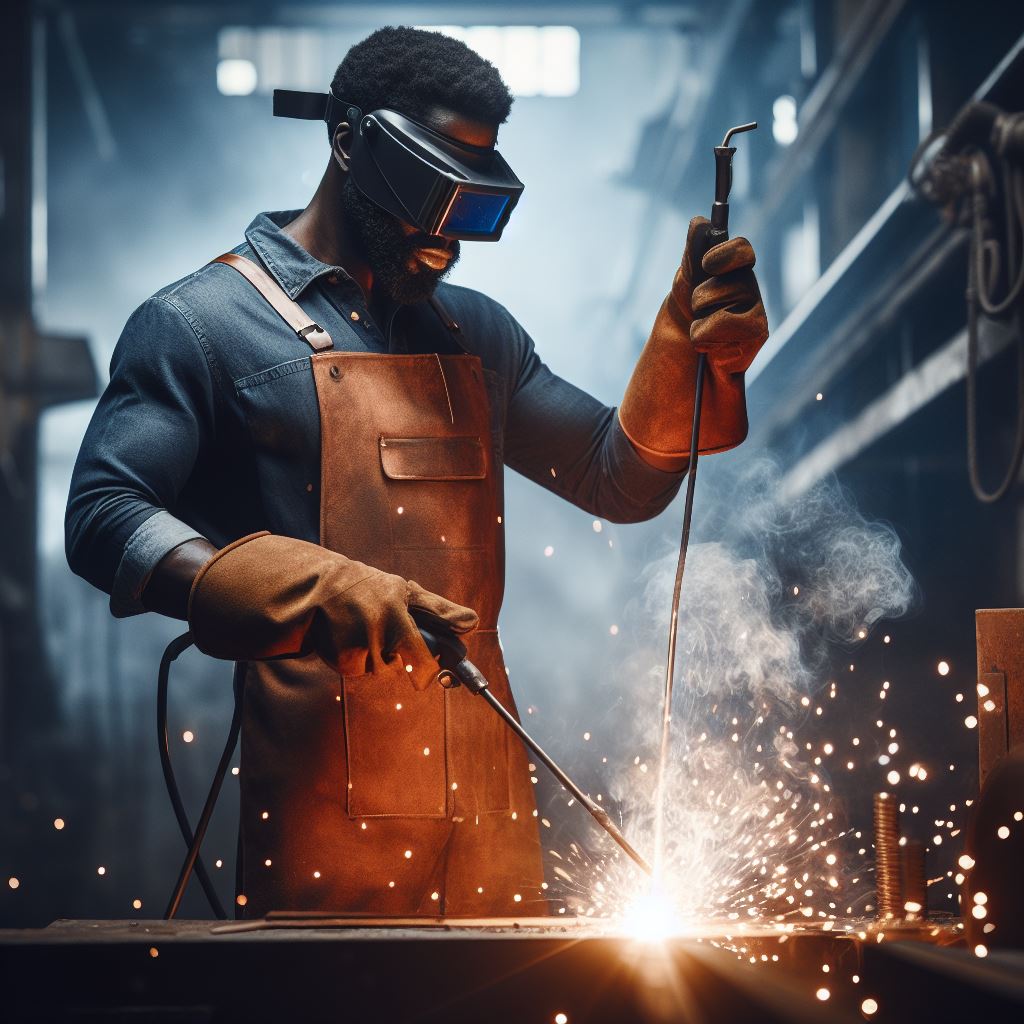
Successful Case Studies of US Companies
General Electric (GE) comprehensive approach to welder’s health and safety
- Investment in advanced PPE (Personal Protective Equipment) and training programs.
- Regular medical screenings and employee awareness campaigns.
General Electric (GE) is known for its proactive approach to addressing welder’s health risks.
They have recognized the importance of providing their workers with adequate protection and knowledge to minimize potential hazards.
One of the key measures implemented by General Electric (GE) is the investment in advanced PPE, ensuring that their welders have access to high-quality protective gear.
Additionally, they prioritize training programs to ensure that employees are well-educated on safety measures and best practices.
Moreover, General Electric (GE) doesn’t stop at PPE and training alone.
They also conduct regular medical screenings for their welders to detect any health issues early on.
This proactive approach allows them to address concerns promptly and provide necessary support to affected employees.
In conjunction with medical screenings, the company runs employee awareness campaigns to enhance understanding and promote a safety-conscious culture.
Transform Your Career Today
Unlock a personalized career strategy that drives real results. Get tailored advice and a roadmap designed just for you.
Start NowBy keeping their workers informed, General Electric (GE) aims to foster a sense of responsibility towards one’s health and safety.
Lincoln Electric innovative measures to reduce health risks
- Development of specialized welding booths with enhanced ventilation.
- Collaboration with health experts for ongoing research and improvement.
Lincoln Electric has taken a creative and proactive approach to minimize health risks associated with welding processes.
They have invested in developing specialized welding booths that offer enhanced ventilation systems.
These booths are designed to effectively capture and remove harmful fumes, gases, and particles generated during welding operations.
By improving the air quality in the immediate vicinity, Lincoln Electric significantly reduces the exposure of their welders to hazardous substances, thereby safeguarding their health.
In addition to their focus on engineering controls, Lincoln Electric actively collaborates with health experts to stay at the forefront of research and improvement.
By partnering with professionals who possess expertise in occupational health, they continuously evaluate their existing practices and explore innovative solutions to further enhance the well-being of their workforce.
This proactive engagement enables Lincoln Electric to adapt swiftly to new findings and ensure the adoption of the most effective health measures.
In general, both General Electric (GE) and Lincoln Electric serve as successful case studies of US companies that prioritize welder’s health and safety.
Through their comprehensive approaches and innovative measures, they demonstrate the commitment to protecting their workers from potential risks.
By investing in advanced PPE, training programs, regular screenings, employee awareness campaigns, specialized welding booths, and collaborations with health experts.
These companies set high standards for the industry and contribute to a safer working environment for welders.
Read: Specialized Welding Techniques Trending in the US Today
Benefits of Addressing Welder’s Health Risks
Positive impact on employee well-being and morale
- Addressing welder’s health risks shows that the company values the well-being of its workers.
- By promoting a safe work environment, employees feel valued and supported, leading to increased morale.
- When employees are healthy and satisfied, they are more likely to be productive and engaged in their work.
Reduction in healthcare costs for employers
- Health issues related to welding exposures can lead to high healthcare costs for employers.
- By addressing these risks, companies can prevent illness and injuries, reducing the need for medical treatment.
- Lower healthcare costs positively impact a company’s bottom line and can result in long-term financial savings.
Compliance with government regulations and standards
- Government agencies have established regulations and standards to protect workers from welding-related health hazards.
- Complying with these regulations ensures that the company is meeting its legal obligations and avoiding penalties.
- Employers who prioritize the health and safety of their welders demonstrate a commitment to ethical and responsible business practices.
Addressing welder’s health risks not only benefits the individual worker but also has positive effects on the overall workplace and company.
By prioritizing employee well-being and morale, companies can create a positive work environment where employees feel valued and supported.
This, in turn, leads to increased productivity and engagement.
Reducing healthcare costs is another significant benefit of addressing welder’s health risks.
Illnesses and injuries resulting from welding exposures can be expensive to treat, leading to financial strain for employers.
By proactively mitigating these risks, companies can prevent such health issues, resulting in long-term cost savings and financial stability.
Compliance with government regulations and standards is crucial for companies.
Transform Your Career Today
Unlock a personalized career strategy that drives real results. Get tailored advice and a roadmap designed just for you.
Start NowWelding-related health hazards are widely recognized, and various regulations have been put in place to protect workers.
By adhering to these regulations, companies not only avoid penalties but also demonstrate their commitment to ethical and responsible practices.
In fact, addressing welder’s health risks brings multiple benefits to both employees and employers.
It improves employee well-being, boosts morale, and promotes a positive work environment. It also reduces healthcare costs for companies, resulting in long-term financial savings.
Furthermore, compliance with government regulations showcases a company’s commitment to ethical practices.
Therefore, companies should prioritize addressing welder’s health risks to ensure the welfare of their workers and the success of their business.
Read: The Role of Unions in Shaping the Welder Profession in USA
Gain More Insights: Crafting the Future: Carpenter Apprenticeships in the US
Conclusion
A recap of welder’s health risks and their significance
Welding poses numerous health risks, including respiratory problems, eye injuries, and exposure to toxic substances.
These risks can have serious long-term effects on welders’ overall health and well-being.
The importance of US companies taking proactive approaches
US companies need to prioritize the health and safety of their welders by implementing proper safety measures, providing adequate training, and investing in technology and equipment that minimize the risks associated with welding.
Encouragement for further research and improvement in addressing these risks
There is a need for continuous research and development to identify new methods and technologies that can further reduce the health risks faced by welders.
By investing in research and improvement, US companies can enhance their understanding of these risks and take effective measures to protect the health and well-being of their welders.
It is crucial for both government agencies and private organizations to collaborate in order to address the health risks faced by welders and work towards creating a safer working environment for them.
Only by recognizing the significance of these health risks and actively addressing them can US companies protect their most valuable assets – their workers.
Moreover, these proactive approaches will not only benefit the welders’ health but also contribute to the overall productivity and success of the companies they work for.
Therefore, it is imperative that we continue to prioritize research, improvements, and collaboration in order to ensure the well-being of welders in the United States.
[E-Books for Sale]
The Big Book of 500 High-Paying Jobs in America: Unlock Your Earning Potential
$19.99 • 500 High-Paying Jobs • 330 pages
Explore 500 high-paying jobs in America and learn how to boost your career, earn more, and achieve success!
See All 500 High-Paying Jobs of this E-Book
1001 Professions Without a Degree: High-Paying American Jobs You Can Start Now
$19.99 • 1001 Professions Without a Degree • 174 pages
Discover 1001 high-paying jobs without a degree! Unlock career tips, skills, and success strategies for just $19.99!