Introduction
In warehouse management, striking a balance between cost and service is crucial for optimizing operations.
This delicate equilibrium can greatly affect a company’s overall business performance.
When cost and service are properly balanced, warehouses can operate efficiently while meeting customer demands effectively.
In this blog post, we will explore key strategies for achieving this balance.
Understanding the Cost Factors in Warehouse Management
When it comes to warehouse management, understanding the cost factors is crucial for maintaining a balance between cost and service.
Let’s delve into the different aspects of cost factors in warehouse management.
Fixed Costs
- Fixed costs are expenses that remain constant regardless of the level of production or activity in the warehouse.
- Examples of fixed costs include rent, utilities, insurance, and equipment maintenance.
- It is important to carefully monitor and manage fixed costs to ensure optimal financial health of the warehouse.
Variable Costs
- Variable costs in warehouse management are expenses that fluctuate with the level of production or activity.
- Key examples of variable costs include labor, transportation, inventory carrying costs, and packaging materials.
- Identifying and managing variable costs effectively is essential for cost control and efficiency in warehouse operations.
Importance of Identifying and Managing Cost Factors
Effective cost management is critical for maintaining profitability and competitiveness in the warehouse management industry.
By understanding and managing cost factors effectively, warehouse managers can achieve a balance between cost and service.
This not only helps in optimizing resources but also in enhancing customer satisfaction levels.
Warehouse managers need to constantly analyze and evaluate both fixed and variable costs to identify areas for improvement and cost-saving opportunities.
By optimizing cost factors, warehouses can improve operational efficiency, reduce wastage, and increase overall profitability.
Evaluating Service Level Requirements
Service level agreements (SLAs) are essential documents that establish the expectations and responsibilities of both parties involved in a business transaction.
When it comes to warehouse management, SLAs play a crucial role in ensuring that customers and suppliers are satisfied with the level of service provided.
- Explanation of service level agreements with customers and suppliers
- Discussion on key performance indicators for service levels in warehouse management
- Importance of aligning service level requirements with cost constraints
SLAs with customers outline the quality and timeliness of order fulfillment, accuracy of inventory counts, and communication protocols.
On the other hand, SLAs with suppliers specify the delivery schedules, packaging requirements, and quality standards.
Key performance indicators (KPIs) help warehouse managers evaluate the effectiveness of their operations in meeting service level requirements.
These KPIs may include order accuracy rates, on-time delivery percentages, inventory turnover ratios, and customer satisfaction scores.
While it’s essential to strive for high service levels to meet customer and supplier expectations, it’s equally important to balance these goals with cost considerations.
Warehouse managers must find ways to optimize their operations to deliver exceptional service while keeping costs under control.
Learn More: Salary Expectations for Construction Managers
Transform Your Career Today
Unlock a personalized career strategy that drives real results. Get tailored advice and a roadmap designed just for you.
Start NowUtilizing Technology for Cost Optimization
Implementing technology in warehouse management can significantly impact cost optimization.
Here’s how:
Overview of Warehouse Management Systems and Their Role in Cost Control
- Warehouse management systems (WMS) help streamline operations by providing real-time data on inventory levels, order status, and shipping.
- WMS can automate tasks such as order fulfillment, inventory tracking, and picking processes, reducing manual labor costs.
- By optimizing inventory placement and order processing, WMS can minimize storage costs and improve overall efficiency.
Discussion on Automation Tools for Inventory Management, Order Processing, and Logistics
- Automated inventory management systems use barcode scanning and RFID technology to track inventory levels accurately.
- Order processing automation tools can speed up order fulfillment, reducing lead times and improving customer satisfaction.
- Using automation in logistics can optimize routes, reduce transportation costs, and minimize fuel consumption.
Benefits of Technology Adoption in Driving Efficiency and Reducing Costs
- Technology adoption leads to improved accuracy in inventory management, reducing the risk of stockouts or overstock situations.
- Automated systems can identify inefficiencies in warehouse processes, allowing for continuous improvement and cost savings.
- Real-time data provided by technology helps in making informed decisions on inventory levels, reducing holding costs and maximizing space utilization.
By leveraging technology in warehouse management, businesses can achieve cost optimization while maintaining high service levels.
Delve into the Subject: How to Achieve Perfect Grout Lines: Tips and Tricks
Implementing Lean Principles for Cost Reduction
Implementing lean principles in warehouse management is crucial for achieving cost reduction and maximizing efficiency.
By adopting lean strategies, businesses can eliminate waste, improve processes, and enhance overall warehouse performance.
Introduction to Lean Warehouse Management Strategies
Lean warehouse management focuses on the idea of minimizing waste and optimizing operational efficiency.
By implementing lean principles, organizations can streamline processes, reduce costs, and deliver value to customers more effectively.
One of the key principles of lean warehouse management is waste elimination.
This involves identifying and eliminating any activities or processes that do not add value to the overall operation.
By reducing waste, organizations can lower costs and improve productivity.
Discussion on Lean Tools
There are several tools and techniques that organizations can use to implement lean principles in warehouse management.
Some of the most common tools include:
- 5S: A method for organizing workspace to improve efficiency and reduce waste.
- Kanban: A visual scheduling system that helps to optimize inventory levels and improve workflow.
- Continuous Improvement: A process of making small, incremental changes to improve processes over time.
By utilizing these tools effectively, organizations can streamline operations, minimize costs, and enhance overall warehouse performance.
Importance of Fostering a Culture of Continuous Improvement
Creating a culture of continuous improvement is essential for the success of lean warehouse management.
By encouraging employees to constantly seek ways to improve processes and eliminate waste, organizations can drive innovation, increase efficiency, and reduce costs.
Continuous improvement involves empowering employees to identify areas for enhancement, implement changes, and monitor results.
By fostering a culture of continuous improvement, organizations can adapt to changing market conditions, improve customer satisfaction, and stay competitive in the industry.
Implementing lean principles in warehouse management is crucial for achieving cost reduction, improving efficiency, and delivering value to customers.
By adopting lean tools and fostering a culture of continuous improvement, organizations can optimize operations, lower costs, and enhance overall warehouse performance.
Transform Your Career Today
Unlock a personalized career strategy that drives real results. Get tailored advice and a roadmap designed just for you.
Start NowYou Might Also Like: Seasonal Work Patterns for Lumberjacks
Maximizing Space Utilization for Cost Efficiency
When designing a warehouse layout, it is essential to consider space optimization to ensure cost efficiency.
Factors such as aisle width, shelving height, and storage configuration play a crucial role in maximizing storage space.
Explanation of Warehouse Layout Design Considerations for Space Optimization
Vertical storage solutions, such as mezzanine levels and tall shelving units, can help utilize the vertical space in a warehouse efficiently.
Racking systems, such as pallet racks and cantilever racks, are also crucial for organizing inventory effectively.
Implementing FIFO (First In, First Out) or LIFO (Last In, First Out) methods can further optimize space utilization by ensuring that products are stored and picked in a systematic order.
FIFO is ideal for perishable goods or items with expiration dates, while LIFO is more suitable for non-perishable items.
Discussion on Vertical Storage Solutions, Racking Systems, and FIFO/LIFO Methods
Maximizing storage space in a warehouse is essential for reducing overhead costs.
By utilizing vertical storage solutions and implementing efficient racking systems, businesses can store more inventory within the same square footage, ultimately lowering the cost per square foot of storage.
Optimizing space utilization also leads to reduced labor costs by streamlining the picking and packing processes.
With a well-organized warehouse layout, employees can easily locate and retrieve items, increasing productivity and reducing overall labor expenses.
Furthermore, maximizing storage space allows businesses to minimize the need for off-site storage facilities, saving on additional rental fees and transportation costs.
By keeping inventory on-site and in an organized manner, companies can operate more efficiently and cost-effectively.
Importance of Maximizing Storage Space to Reduce Overhead Costs
Maximizing space utilization in warehouse management is crucial for achieving cost efficiency.
By carefully designing the warehouse layout, implementing vertical storage solutions, utilizing racking systems effectively, and adopting FIFO/LIFO methods, businesses can reduce overhead costs, streamline operations, and improve overall profitability.
Find Out More: Tips for Finding a Reliable and Skilled Glazier
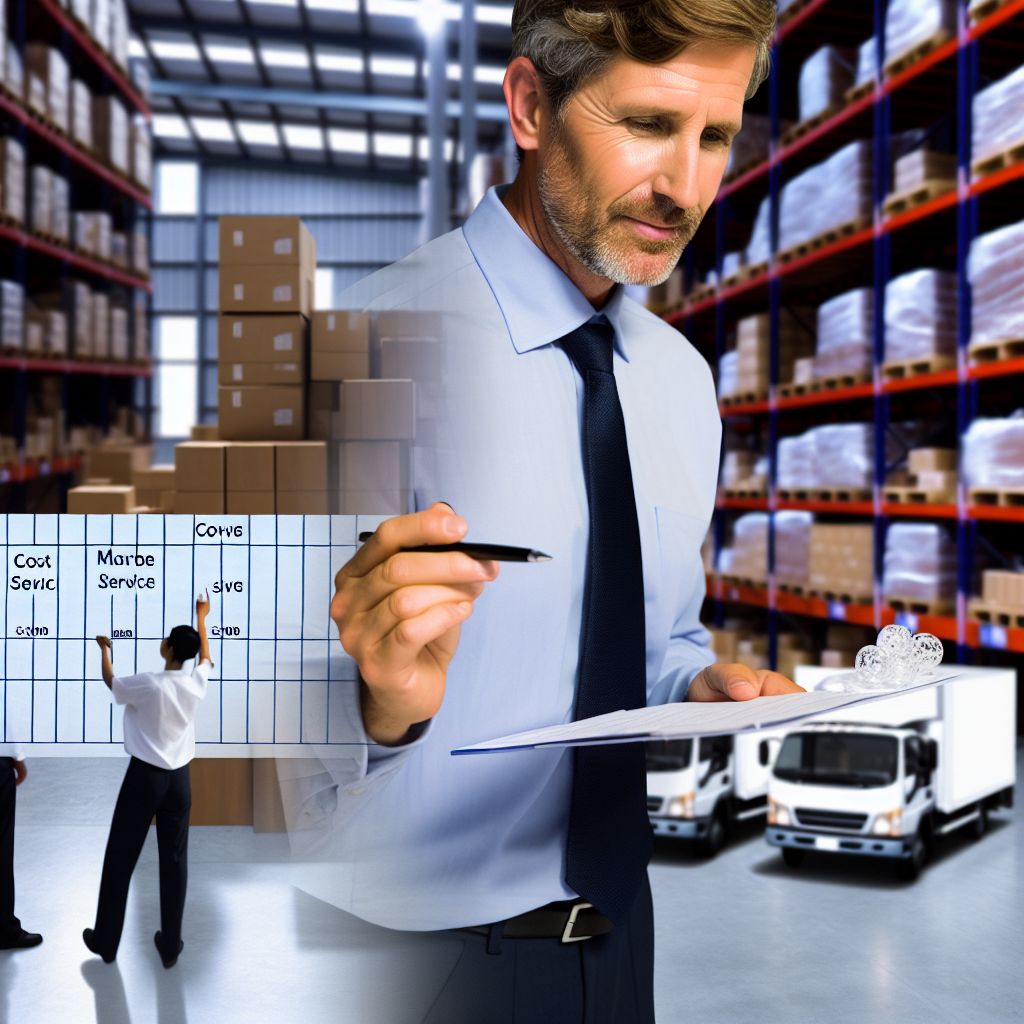
Establishing Vendor Partnerships for Cost Savings
Collaborative relationships with suppliers are essential for cost-effective sourcing.
Working closely with vendors can lead to numerous benefits for warehouse management.
Overview of Collaborative Relationships
Building strong relationships with vendors is crucial for maintaining a competitive edge in the market.
By forging partnerships based on mutual trust and respect, warehouses can create win-win situations that benefit both parties.
Transform Your Career Today
Unlock a personalized career strategy that drives real results. Get tailored advice and a roadmap designed just for you.
Start NowBulk Purchasing
One way to save costs is through bulk purchasing.
Buying in large quantities allows warehouses to take advantage of discounted prices offered by suppliers.
This can lead to significant savings over time and help to reduce overall procurement costs.
Vendor-Managed Inventory (VMI)
Vendor-managed inventory is another strategy that can streamline warehouse operations and reduce costs.
With VMI, suppliers are responsible for monitoring and replenishing inventory levels at the warehouse.
This helps to minimize stockouts, improve efficiency, and lower carrying costs for the warehouse.
Just-in-Time (JIT) Delivery
Just-in-time delivery is a method of inventory management that aims to reduce excess inventory and cut down on storage costs.
By receiving goods only when they are needed, warehouses can optimize their space utilization and minimize holding costs.
Importance of Strategic Vendor Partnerships
Strategic vendor partnerships play a significant role in reducing procurement costs and improving overall warehouse efficiency.
By working closely with suppliers, warehouses can access valuable insights, negotiate better terms, and address supply chain challenges proactively.
Establishing vendor partnerships for cost savings is a critical aspect of warehouse management.
By leveraging collaborative relationships, implementing strategies like bulk purchasing, VMI, and JIT delivery, and prioritizing strategic partnerships, warehouses can optimize their procurement processes, reduce costs, and enhance service levels.
Implementing Performance Metrics for Cost-Effective Operations
Introduction to key performance indicators (KPIs) for cost measurement in warehouse management.
- Discussion on metrics such as order accuracy, on-time delivery, and inventory turnover.
- Importance of tracking performance metrics to identify cost-saving opportunities.
Key Performance Indicators (KPIs)
Key Performance Indicators (KPIs) are essential tools in measuring the performance of warehouse operations.
They provide valuable insights into the efficiency and effectiveness of processes, helping managers make data-driven decisions for cost-saving strategies.
Order Accuracy
Order accuracy is a critical metric to evaluate the precision of order fulfillment processes in warehouses.
By tracking the percentage of orders shipped correctly, organizations can minimize the costs associated with returns and re-shipping, ultimately enhancing customer satisfaction.
On-Time Delivery
On-time delivery measures the ability of a warehouse to fulfill customer orders within the specified timeframe.
Ensuring timely deliveries not only improves customer loyalty but also reduces expedited shipping costs and penalties for late shipments, enhancing overall operational efficiency.
Inventory Turnover
Inventory turnover is a key metric that reflects the pace at which inventory is sold and replaced within a given period.
Transform Your Career Today
Unlock a personalized career strategy that drives real results. Get tailored advice and a roadmap designed just for you.
Start NowBy analyzing inventory turnover ratios, organizations can optimize stock levels, minimize carrying costs, and prevent overstock or stockouts, leading to improved cost management.
Importance of Tracking Performance Metrics
Tracking performance metrics is crucial for identifying inefficiencies and cost-saving opportunities in warehouse management.
By continuously monitoring KPIs, organizations can pinpoint areas for improvement, streamline processes, and optimize resource allocation to drive down operational costs.
Identifying Cost-Saving Opportunities
Performance metrics enable managers to identify bottlenecks, redundancies, and inefficiencies that contribute to high operational costs.
By leveraging data-driven insights, organizations can implement targeted strategies to reduce expenses, enhance productivity, and increase profitability.
Implementing performance metrics such as order accuracy, on-time delivery, and inventory turnover is essential for achieving cost-effective warehouse operations.
By tracking KPIs and analyzing data, organizations can optimize processes, minimize expenses, and drive sustainable growth in the competitive logistics industry.
Balancing Cost and Service in Warehouse Management
Balancing cost and service in warehouse management is crucial for business success.
By optimizing costs while maintaining high service levels, companies can stay competitive and profitable.
We discussed key points such as the impact of warehouse management on overall costs.
We highlighted the importance of efficient operations and the need for strategic decision-making.
Finding the right balance between cost and service is essential for driving growth and customer satisfaction.
Businesses must prioritize cost optimization strategies without compromising on service quality.
We urge businesses to evaluate their warehouse management practices.
Focus on achieving a harmonious balance between cost efficiency and service excellence.
By doing so, companies can enhance their bottom line and gain a competitive edge in the market.