Introduction
Explanation of Materials Engineering
Materials engineering is a field that focuses on the development, testing, and improvement of materials used in various applications.
It involves understanding the properties, behaviors, and processing techniques of different materials.
This discipline integrates principles from physics, chemistry, and engineering to create materials that meet specific performance requirements.
Materials engineers work on everything from metals and ceramics to polymers and composites, aiming to enhance their properties and functionality.
Importance of Software Tools for Materials Engineers
Software tools are vital for materials engineers as they provide essential support in analyzing and simulating material performance.
These tools allow engineers to model complex materials and predict their behavior under various conditions, which is crucial for designing reliable and efficient materials.
Advanced software tools help optimize material properties, reduce development time, and minimize errors.
They also facilitate more accurate and informed decision-making by providing detailed insights into material performance.
In today‘s fast-paced technological landscape, leveraging sophisticated software tools is key to staying competitive and driving innovation in materials engineering.
Abaqus
Description of Abaqus Software
Abaqus is an advanced software suite designed for finite element analysis (FEA) and computational fluid dynamics (CFD).
It provides engineers with robust tools for simulating and analyzing the behavior of materials under various conditions.
Abaqus is renowned for its ability to model complex interactions and materials, making it a critical tool for engineers in many fields, including materials engineering.
The software is widely used to assess how materials will perform in real-world applications, helping engineers design more effective and reliable products.
Features and Capabilities for Materials Engineers
Abaqus offers a comprehensive range of features tailored to the needs of materials engineers.
It excels in nonlinear analysis, allowing engineers to model materials that exhibit complex, nonlinear behaviors under different loading conditions.
The software supports dynamic simulations, which are crucial for understanding how materials respond to time-varying forces and movements.
Additionally, Abaqus provides detailed thermal analysis capabilities, enabling engineers to study the effects of temperature changes on material performance.
One of Abaqus’s strengths is its extensive library of material models, which includes options for metals, polymers, composites, and other advanced materials.
This variety allows engineers to accurately simulate a wide range of materials and their interactions.
Abaqus also supports fluid-structure interaction (FSI), which is essential for analyzing scenarios where fluids and solids interact, such as in aerospace and automotive applications.
The software integrates with other tools and data sources, enhancing its flexibility and making it easier for engineers to incorporate external data into their simulations.
Benefits of Using Abaqus for Simulations and Analysis in Materials Engineering
Using Abaqus provides significant benefits for materials engineers, enhancing both the accuracy and efficiency of simulations.
One of the primary advantages is its ability to deliver precise modeling of complex materials.
This precision leads to more accurate predictions of material behavior under various conditions, which is crucial for designing reliable components and systems.
Engineers can test materials virtually, reducing the need for costly physical prototypes and experiments.
Abaqus‘s advanced algorithms and solvers contribute to faster and more efficient simulations.
This efficiency allows engineers to conduct more comprehensive analyses in less time, accelerating the development process.
The software‘s detailed results and visualizations support informed decision-making, helping engineers identify potential issues and optimize material performance before physical testing.
The user-friendly interface and extensive documentation make Abaqus accessible to both new and experienced users.
Engineers can quickly learn to use the software and apply it effectively to their projects.
Additionally, Abaqus‘s capability to handle large-scale simulations and complex interactions is invaluable for studying intricate systems, such as those found in aerospace, automotive, and civil engineering applications.
Overall, Abaqus enhances the materials engineering process by providing powerful simulation tools, improving accuracy, and accelerating development.
Its robust features and capabilities make it an essential tool for engineers seeking to push the boundaries of material performance and innovation.
Read: Decoding the Ethics & Responsibilities of US Civil Engineers
ANSYS
Overview of ANSYS Software
ANSYS is a comprehensive software suite renowned for its advanced engineering simulation capabilities.
It provides robust solutions for structural, thermal, and fluid dynamics simulations, making it indispensable for engineers across various industries.
ANSYS allows users to create detailed models of complex systems, simulate their behavior, and analyze their performance under different conditions.
The software‘s versatility and precision enable engineers to optimize designs, reduce physical testing, and accelerate product development.
Its integration of multiple simulation tools into a unified platform enhances workflow efficiency and accuracy.
Application of ANSYS in Materials Engineering
In materials engineering, ANSYS plays a pivotal role in understanding and optimizing material performance.
The software‘s simulation capabilities help engineers predict how materials will behave under various stresses, temperatures, and environmental factors.
This predictive power is crucial for designing materials that will perform reliably in real-world applications, such as in aerospace components, automotive parts, and construction materials.
By leveraging ANSYS, materials engineers can conduct virtual testing to identify potential issues and make necessary adjustments before physical prototypes are produced.
This approach not only saves time but also reduces costs associated with material testing and design modifications.
ANSYS‘s ability to simulate different scenarios helps engineers make informed decisions about material selection and ensure that designs meet safety and performance standards.
Specific Tools and Modules for Materials Analysis and Testing
ANSYS offers a suite of specialized tools and modules tailored for materials analysis and testing, each designed to address specific aspects of material performance.
The ANSYS Mechanical module is essential for detailed structural analysis, providing insights into stress, strain, and deformation.
It enables engineers to evaluate how materials withstand loads and identify potential failure points.
The ANSYS Fluent module focuses on fluid dynamics, which is crucial for studying how fluids interact with materials.
This module helps engineers analyze how materials perform in fluid environments, such as in cooling systems or aerodynamics.
The ANSYS Workbench platform integrates various simulation tools, creating a cohesive environment for performing complex analyses.
It streamlines workflows, allowing engineers to manage multiple simulations and interpret results efficiently.
For composite materials, the ANSYS Composite PrepPost tool is specifically designed to evaluate the behavior of composite structures under different loading conditions.
This module helps engineers understand how composites perform and how to optimize their use in various applications.
The ANSYS Structural Dynamics module assesses how materials respond to dynamic loads and vibrations, providing insights into material behavior under real-world conditions.
This module is particularly useful for evaluating the impact of dynamic forces on material integrity and performance.
Together, these tools and modules ensure comprehensive analysis and testing of materials, enabling engineers to develop more reliable, efficient, and innovative engineering solutions.
Read: From Intern to Lead: Climbing the Software Ladder in the US
MATLAB
Introduction to MATLAB Software
MATLAB is a powerful computing environment widely used for numerical analysis, visualization, and algorithm development.
Developed by MathWorks, MATLAB offers a versatile platform for handling complex mathematical problems.
Its interactive interface and extensive libraries make it ideal for a range of engineering applications.
MATLAB supports matrix operations, data analysis, and graphical plotting, making it a popular choice among engineers and researchers.
Use of MATLAB in Materials Research and Development
In materials research and development, MATLAB proves invaluable for modeling and simulation tasks.
Engineers use MATLAB to analyze material properties, simulate behaviors, and optimize processes.
Its ability to handle large datasets and perform complex calculations accelerates research and development efforts.
MATLAB allows engineers to develop custom algorithms and functions tailored to specific needs, enabling detailed analysis of material performance under various conditions.
It also integrates with other software tools and hardware systems, facilitating a seamless workflow from data collection to analysis and visualization.
Examples of MATLAB Applications for Materials Engineers
One application of MATLAB in materials engineering is finite element analysis (FEA).
Engineers use MATLAB to develop and implement FEA models, predicting how materials will behave under different stresses.
Simulating various loading conditions helps optimize material design and performance before physical testing.
Another example is analyzing microstructure images.
MATLAB‘s image processing toolbox allows engineers to analyze and quantify features in microscopy images, providing insights into microstructural properties like grain size and phase distribution.
MATLAB also supports data-driven approaches to material science.
Engineers perform statistical analysis and machine learning on experimental data to identify patterns and correlations, leading to new insights and innovations.
Additionally, MATLAB‘s optimization toolbox helps fine-tune material properties and processing parameters.
Engineers use it to design materials with desired properties by adjusting variables and constraints in the model.
Overall, MATLAB‘s comprehensive suite of tools and its adaptability make it an essential resource for materials engineers.
Its capabilities in simulation, analysis, and optimization drive advancements in material science and engineering, enhancing research and development efforts.
Read: The Role of NCARB in US Architecture Licensing.
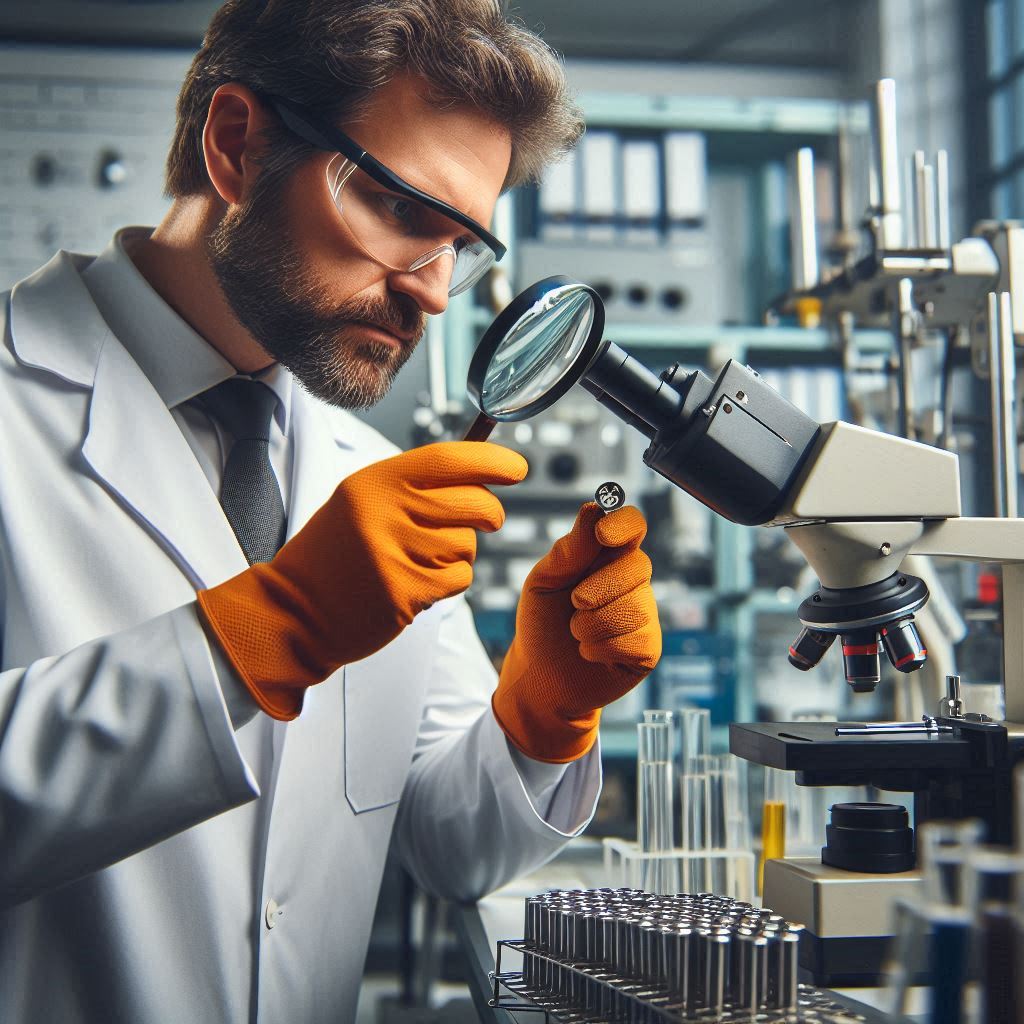
COMSOL Multiphysics
Description of COMSOL Multiphysics Software
COMSOL Multiphysics is a versatile simulation software used in materials engineering and other fields.
It provides a comprehensive platform for modeling and simulating complex physical phenomena.
The software enables engineers to create detailed simulations that integrate multiple physical processes.
With COMSOL, users can address various challenges related to heat transfer, fluid dynamics, and structural mechanics.
The software supports a wide range of applications, making it valuable for analyzing and optimizing materials in different scenarios.
Key Features for Materials Engineering Applications
COMSOL Multiphysics offers several key features beneficial for materials engineering.
Its multiphysics capabilities allow users to combine different physical phenomena into a single model.
This integration helps engineers study interactions between heat, stress, and electromagnetic fields in materials.
The software includes a variety of material libraries, enabling users to select and apply accurate material properties.
COMSOL also supports parametric studies, which help in exploring how changes in design parameters affect performance.
Additionally, it provides advanced visualization tools to interpret simulation results clearly and effectively.
How COMSOL Can Help Materials Engineers with Multi-Physics Simulations
COMSOL Multiphysics excels in multi-physics simulations, which are crucial for materials engineering.
Engineers often deal with complex systems where multiple physical effects interact.
For example, in designing a new composite material, engineers need to consider thermal, mechanical, and chemical properties.
COMSOL allows engineers to model these interactions comprehensively.
By integrating different physical processes, engineers can predict how materials will behave in real-world conditions.
This capability helps in optimizing material performance and ensuring reliability in various applications.
Additionally, COMSOL‘s user-friendly interface simplifies the setup and execution of complex simulations, making it accessible for engineers at all levels.
The software also provides accurate results, which are essential for making informed decisions and improving material designs.
Overall, COMSOL Multiphysics is a powerful tool that supports engineers in developing innovative materials and solving intricate engineering problems.
Read: Comparison: Architecture Styles across American Regions.
OpenSees
Overview of OpenSees Software
OpenSees, which stands for Open System for Earthquake Engineering Simulation, is a robust software framework designed for structural analysis.
Developed by the University of California, Berkeley, it is an open-source platform that provides advanced tools for modeling and simulating complex structures.
OpenSees supports both linear and nonlinear analysis, making it versatile for a wide range of engineering applications.
Its modular design allows users to extend and customize its features according to their specific needs.
This flexibility and the ability to handle large-scale simulations make OpenSees a valuable tool in structural engineering.
Benefits of Using OpenSees for Structural Analysis in Materials Engineering
OpenSees offers several benefits for structural analysis in materials engineering.
Its open-source nature grants access to a broad array of modeling tools and libraries.
Engineers can modify and adapt the software to fit their unique project requirements without the constraints of proprietary systems.
OpenSees excels in nonlinear analysis, allowing detailed evaluation of material behaviors under extreme conditions.
This capability is crucial for assessing how materials perform during seismic events.
Additionally, OpenSees supports advanced finite element modeling, which helps accurately simulate complex structural systems.
These features enable engineers to predict material responses and optimize designs effectively.
Transform Your Career Today
Unlock a personalized career strategy that drives real results. Get tailored advice and a roadmap designed just for you.
Start NowExamples of OpenSees Applications for Materials Engineers
Materials engineers apply OpenSees in various practical applications to enhance structural performance.
For example, engineers use OpenSees to analyze the seismic response of buildings and bridges, simulating earthquake loads to assess structural resilience.
It also helps in evaluating new materials and construction techniques by modeling experimental materials to predict their real-world behavior.
OpenSees is used to study retrofitting techniques for aging infrastructure, allowing engineers to determine their effectiveness in extending the lifespan and safety of structures.
Additionally, it assists in designing resilient structures by analyzing how different materials perform under diverse environmental conditions.
Its comprehensive analysis capabilities make OpenSees an essential tool for materials engineers seeking to improve structural safety and performance.
Material Studio
Introduction to Material Studio Software
Material Studio is a comprehensive software suite designed for materials modeling and analysis.
Developed by BIOVIA, it provides a robust platform for simulating and visualizing material properties and behaviors.
The software supports a wide range of materials, including polymers, metals, ceramics, and composites.
Its advanced computational tools facilitate both academic research and industrial applications, accelerating materials development and optimization.
Tools Available for Materials Modeling and Analysis
Material Studio includes a suite of tools tailored for various aspects of materials modeling and analysis.
Users can access modules for molecular dynamics, quantum mechanics, and crystal structure analysis.
The software enables tasks such as molecular modeling, electronic structure calculations, and thermodynamic analysis.
Users can build and manipulate molecular models, predict material properties, and analyze atomic-level interactions.
Additionally, Material Studio offers visualization tools to interpret complex data and results effectively.
How Material Studio Can Aid Materials Engineers in Studying Complex Material Systems
Material Studio is essential for materials engineers studying complex material systems.
Its powerful modeling tools allow engineers to simulate and understand material behavior under different conditions.
The software helps engineers explore properties like strength, conductivity, and stability before physical experiments.
This predictive capability identifies potential issues and optimizes performance early in the design process.
Material Studio also supports analyzing interactions between different materials, crucial for developing composites and multi-phase systems.
By streamlining research and reducing experimentation costs, Material Studio accelerates the development of new materials, enhances decision-making, and drives innovation in materials engineering.
Moldflow Software for Materials Engineers
Description of Moldflow Software
Moldflow is a leading simulation software from Autodesk, tailored for plastic injection molding.
It provides tools for modeling and predicting how molten plastic flows into a mold cavity.
Moldflow’s advanced capabilities include simulating cooling, shrinkage, and warping.
It supports various plastic materials and molding techniques, offering versatility for different applications.
Its intuitive interface allows efficient setup and analysis of complex simulations.
Engineers use Moldflow to visualize potential issues before physical production starts.
Application of Moldflow in Materials Processing and Manufacturing
Moldflow plays a crucial role in materials processing and manufacturing, especially in optimizing plastic injection molding.
It helps engineers design molds and optimize mold filling patterns.
The software identifies potential defects like air traps and weld lines early in the design phase.
By simulating the molding process, Moldflow enables adjustments to parameters such as temperature, pressure, and cooling rates.
This predictive capability assists in designing molds that produce high-quality parts with minimal waste.
It also helps in selecting the most suitable materials for specific applications.
How Moldflow Can Help Materials Engineers Optimize Production Processes
Moldflow helps materials engineers optimize production processes by offering detailed insights into the molding process.
Engineers use simulation results to adjust parameters, improving part quality and consistency.
The software allows for early issue identification and resolution, reducing costly trial and error.
By optimizing mold design and processing conditions, Moldflow minimizes material waste and lowers production costs.
It also accelerates the design process, making it more efficient.
Overall, Moldflow enhances the ability to produce high-quality, cost-effective parts, improving performance and reliability in manufactured products.
Find Out More: Importance of Continuous Learning for Marine Engineers
Conclusion
Recap of the Importance of Software Tools for Materials Engineers
Software tools are crucial for materials engineers, offering precision in analysis and efficiency in design.
They handle complex simulations, improve accuracy, and boost productivity.
Tools like Abaqus, OpenSees, and Material Studio play a significant role in achieving accurate results and advancing research.
By using these tools, engineers can better understand material properties and make informed decisions, which is essential for successful engineering projects.
Encouragement for Materials Engineers to Explore
Materials engineers should actively explore and master these advanced software tools.
Embracing these technologies enhances their ability to tackle intricate problems and optimize material performance.
Investing in learning and utilizing these tools is vital for innovative solutions and successful project outcomes.
Staying current with these tools will lead to more effective research and improved project efficiency.
Engineers are encouraged to integrate these top tools into their workflows to gain a competitive edge and achieve superior results in their work.