Introduction
When it comes to robotics engineering, having the right tools and software is crucial for success.
These tools and software are essential for designing, programming, and testing robotic systems efficiently.
Robotics engineers use various tools and software to streamline their work processes.
They bring ideas to life and ensure robotic systems run smoothly.
With the rapid advancements in technology, the demand for robotics engineers who are proficient in using these tools and software is increasing.
Having the right tools and software allows robotics engineers to design and develop cutting-edge robotic systems with precision and accuracy.
These tools help in simulating robotic movements, testing algorithms, and debugging code effectively, saving time and resources in the long run.
The right software lets robotics engineers program robots to perform complex tasks.
It also enables them to interact with their environment and adapt autonomously to changing conditions.
It also helps in visualizing and analyzing data collected from sensors to improve the performance of robotic systems.
In review, having access to essential tools and software is paramount for robotics engineers to stay ahead in a highly competitive field.
These tools not only enhance productivity but also facilitate innovation and creativity in robotics engineering, driving the industry forward.
CAD Software
The Importance Of Cad Software In Designing And Modeling Robot Parts
Utilizing CAD software is crucial for robotics engineers when it comes to designing and modeling various robot parts.
It allows engineers to create detailed and accurate 3D models that are essential for the fabrication process.
Popular CAD Software Options
- Autodesk AutoCAD: Widely used in the industry for its versatility and user-friendly interface.
- SolidWorks: Known for its robust tools for creating complex mechanical designs.
- Fusion 360: Offers a cloud-based platform for collaboration and design iteration.
- CATIA: Ideal for designing high-performance mechanical systems and aerospace components.
Key Features to Look for in CAD Software
- Parametric Modeling: Allows for easy modification of design parameters.
- Assembly Design: Enables the creation of assemblies with multiple parts.
- Simulation Tools: Provides functionalities for structural and motion analysis.
- Compatibility with CAM Software: Facilitates seamless transition from design to manufacturing.
- Rendering Capabilities: Helps visualize the final product with realistic textures and materials.
In general, selecting the right CAD software is pivotal for robotics engineers to streamline their design process and bring innovative robot concepts to life.
Read: Future of CAD Technician Jobs in Engineering
Simulation Tools in Robotics Engineering
Role of Simulation Tools in Testing and Refining Robot Designs
Simulation tools are indispensable in robotics engineering.
They offer a virtual environment to test and refine robot designs before physical prototyping.
These tools allow engineers to simulate real-world conditions and predict how a robot will perform in various scenarios.
By using simulation tools, engineers can explore different design configurations, assess robot movements, and evaluate interactions without needing physical models.
This approach helps identify potential issues early in the design process, leading to more efficient and cost-effective development.
Simulation tools enable engineers to test various aspects of robot functionality, including kinematics, dynamics, and control algorithms.
They provide valuable insights into how different components of a robot will interact and perform under different conditions.
This virtual testing can reveal design flaws or inefficiencies that might not be apparent in initial design phases.
By addressing these issues early, engineers can avoid costly mistakes and reduce the risk of failures during physical testing.
Furthermore, simulation tools facilitate iterative design processes.
Engineers can quickly modify and test design parameters, leading to faster optimization.
This iterative approach helps refine robot designs to meet specific performance criteria and operational requirements.
It also allows for comprehensive testing of robots in complex and dynamic environments, which is crucial for developing robust and reliable systems.
Examples Of Simulation Tools Commonly Used By Robotics Engineers
Several simulation tools are popular among robotics engineers for their capabilities and versatility.
Here are some commonly used tools:
Gazebo
Gazebo is an open-source simulation tool known for its high-fidelity simulation environment.
It provides realistic physics, sensor data, and complex environments, making it ideal for testing robots in diverse scenarios.
Gazebo supports various robot models and environments, allowing for detailed and accurate simulations.
V-REP (CoppeliaSim)
V-REP, now known as CoppeliaSim, is renowned for its versatility and extensive features.
It supports the simulation of various robot types and interactions, including mobile robots, manipulators, and multi-robot systems.
V-REP integrates with multiple programming languages, making it a flexible choice for different applications.
Webots
Webots is a user-friendly simulation tool commonly used in educational settings.
It supports the simulation of mobile robots and offers various environment configurations.
Webots provides an intuitive interface for creating and testing robot designs, making it accessible for both beginners and experienced engineers.
MATLAB/Simulink
MATLAB/Simulink is widely used for simulating robot dynamics, control systems, and sensor data.
It integrates with other software tools and provides a comprehensive environment for developing and testing algorithms.
MATLAB/Simulink is particularly useful for algorithm development and control system design.
RoboDK
RoboDK specializes in offline programming and simulation for industrial robots.
It offers a wide range of robots and workpieces for simulation, making it suitable for tasks such as path planning, collision detection, and programming.
RoboDK helps optimize robot operations and improve productivity in industrial settings.
Benefits of Using Simulation Tools
Simulation tools offer numerous benefits throughout the robotics development process:
- Cost Savings: Simulation tools cut down on the need for physical prototypes, saving significant costs.
- Time Efficiency: Engineers can quickly iterate on designs and test various scenarios without waiting for physical prototypes.
- Enhanced Accuracy: Simulation tools provide precise data on robot performance, enabling engineers to fine-tune designs and improve accuracy.
- Risk Reduction: Engineers can reduce the risk of costly errors by identifying potential problems in a simulated environment before physical testing and deployment.
- Design Optimization: Engineers can experiment with different design configurations and operating conditions to find the most effective solutions.
- Improved Collaboration: Simulation tools support collaboration among team members by providing a shared platform for design testing and evaluation.
In short, simulation tools are essential for modern robotics engineering.
They offer a virtual environment for testing and refining designs, leading to cost savings, time efficiency, and improved accuracy.
Tools like Gazebo, V-REP, Webots, MATLAB/Simulink, and RoboDK provide valuable capabilities for optimizing robot designs and reducing risks.
Simulation tools provide crucial benefits, making them essential for robotics development.
Engineers use these tools to create more effective and reliable robotic systems.
Read: How to Build a Strong CAD Technician Portfolio
Programming Languages
Essential Programming Languages for Robotics Engineering
Robotics engineers rely on various programming languages to design, build, and control robots.
Mastery of these languages is crucial for success in the field.
Here are some essential programming languages for robotics:
- C++: Known for its efficiency and performance, C++ is widely used in robotics for real-time systems and hardware interactions.
- Python: Python‘s simplicity and extensive libraries make it ideal for scripting, rapid prototyping, and data analysis in robotics.
- ROS (Robot Operating System): While not a language per se, ROS uses languages like C++ and Python for managing robot software development.
- MATLAB: MATLAB is essential for algorithm development, simulation, and data visualization in robotics projects.
- Java: Java is used in some robotics applications due to its portability and robust libraries for network and UI development.
Importance of Proficiency in Programming Languages
Proficiency in programming languages is critical for robotics engineers.
Here‘s why:
- Efficient Problem Solving: Mastery of programming languages allows engineers to write efficient code, optimizing robot performance.
- Real-Time Control: Languages like C++ enable precise control over hardware, crucial for real-time robotics applications.
- Algorithm Development: Python and MATLAB are invaluable for developing complex algorithms that drive robotic behaviors and decision-making.
- Integration and Communication: Knowledge of programming languages facilitates integration with various systems and communication protocols.
- Rapid Prototyping: Python‘s ease of use allows for quick testing and iteration, speeding up the development process.
Resources for Learning and Mastering Programming Languages
Several resources can help robotics engineers learn and master these essential programming languages:
- Online Courses: Websites like Coursera, edX, and Udacity offer specialized courses in C++, Python, ROS, and MATLAB.
- Books: Books such as ‘Programming Robots with ROS‘ and ‘MATLAB for Engineers‘ provide in-depth knowledge and practical examples.
- Tutorials and Documentation: The official documentation and online tutorials for C++, Python, and ROS offer valuable insights and code samples.
- Forums and Communities: Engaging in forums like Stack Overflow or robotics-specific communities provides support and practical advice from experienced engineers.
- University Programs: Many universities offer courses and degrees focused on robotics, providing structured learning and hands-on experience.
By leveraging these languages and resources, robotics engineers can effectively design, program, and control advanced robotic systems.
Mastery of these tools is essential for tackling complex challenges and advancing the field of robotics languages essential for robotics engineering.
Read: Top Companies Hiring CAD Technicians in the USA
Development Platforms
The Role Of Development Platforms In Programming And Controlling Robots
Development platforms play a crucial role in programming and controlling robots.
These platforms provide a software framework that simplifies the process of building and operating robots.
Transform Your Career Today
Unlock a personalized career strategy that drives real results. Get tailored advice and a roadmap designed just for you.
Start NowPopular development platforms
Popular development platforms used in the field of robotics include:
- ROS (Robot Operating System): ROS is one of the most widely used development platforms in robotics. It provides a set of tools and libraries for building complex robot applications.
- Arduino: Arduino is a popular open-source platform used for building simple to complex robotic projects. It is known for its ease of use and versatility.
- RobotC: RobotC is a programming language specifically designed for programming robots. It is commonly used with VEX and LEGO robotics kits.
- LabVIEW: LabVIEW is a visual programming language commonly used for controlling robots in research and industrial settings. It offers a user-friendly interface for designing robot control systems.
The features and capabilities of different development platforms
Features and capabilities of different development platforms:
- ROS: ROS supports C++, Python, and Java programming languages. It offers libraries for motion planning, perception, and navigation tasks.
- Arduino: Arduino supports various sensors and actuators, making it ideal for diverse robotic applications.
- RobotC: RobotC offers a simple yet powerful programming environment for beginners and advanced users alike.
- LabVIEW: LabVIEW’s graphical programming interface makes it easy to design and debug robot control algorithms.
The specific requirements of the robotics project determine the choice of development platform.
Consider the robot’s complexity, the required control level, and the user’s programming experience.
Each platform has its strengths and weaknesses, so it is important to carefully evaluate them based on the project’s needs.
Read: Best Online Courses for CAD Technician Training
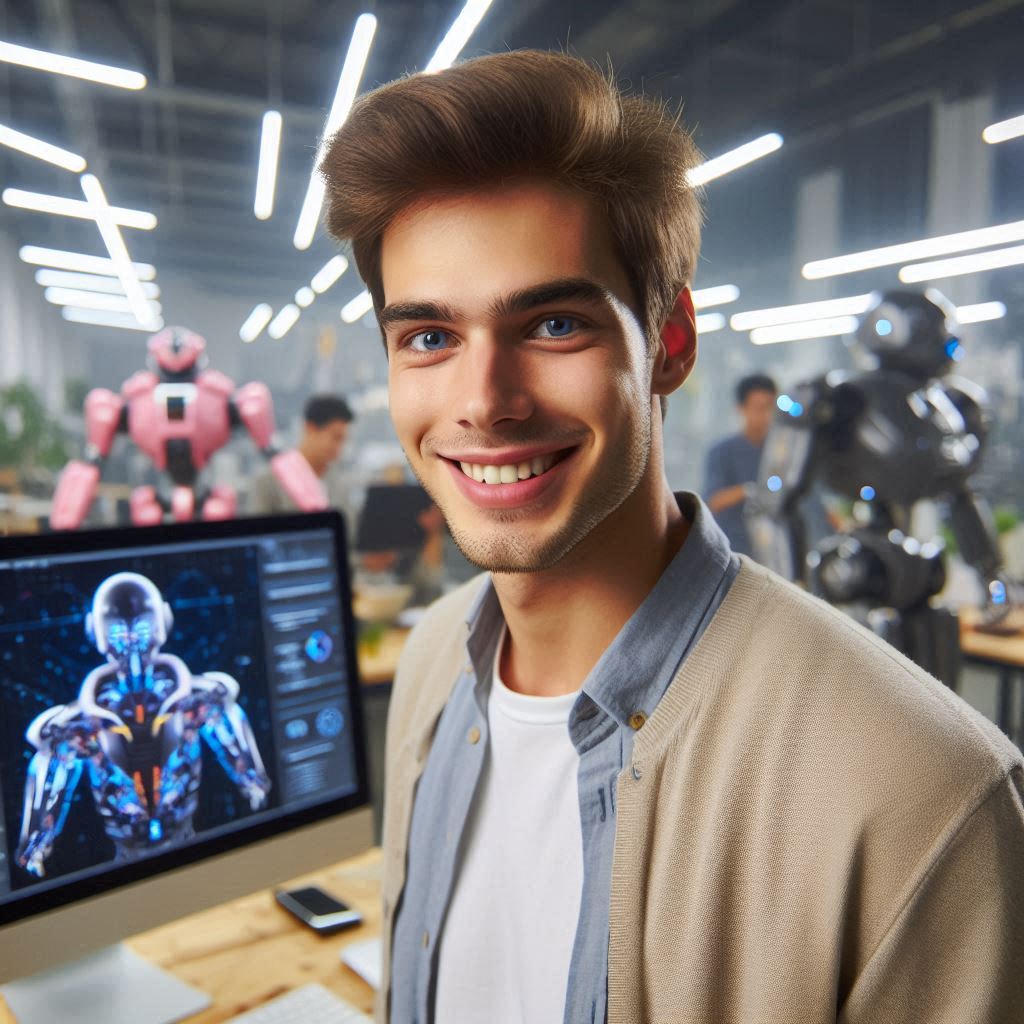
Hardware Tools
When it comes to building and assembling robots, having the right hardware tools is crucial for a successful construction process.
Essential hardware tools needed for building and assembling robots
- Screwdriver set: Used for tightening screws and bolts during the assembly process.
- Wire cutter/stripper: Essential for cutting and stripping wires to the required length.
- Soldering iron: Used for soldering electronic components onto circuit boards.
- Multimeter: Helps in measuring voltage, current, and resistance in electronic components.
- Electric drill: Needed for drilling holes in various materials for mounting components.
The importance of quality hardware tools in the construction process
High-quality hardware tools are essential for robotics engineers as they ensure precision, reliability, and efficiency in the construction process.
Using inferior tools can lead to inaccurate measurements, poor connections, and overall subpar performance of the robot.
Quality tools also offer durability and longevity, saving time and money in the long run.
Recommendations for reliable hardware tools for robotics engineers
- Brand: Investing in reputable brands such as Bosch, Dewalt, and Stanley ensures quality and reliability.
- Material: Opt for tools made from high-grade materials like stainless steel for longevity.
- Ergonomics: Choose tools with ergonomic designs for comfort and ease of use during long hours of construction.
- Reviews: Research and read reviews from other robotics engineers to get insights on the best hardware tools in the market.
Delve into the Subject: Pros and Cons of Being a Field Service Technician
See Related Content: Key Skills for Aspiring Transportation Engineers
Sensor Technology
The Significance of Sensor Technology in Robotics Engineering
Sensor technology drives robotics engineering, allowing robots to engage with their surroundings, perform tasks independently, and make decisions from real-time data.
Sensors are the ‘eyes and ears‘ of robots, providing the necessary inputs to process information and execute actions.
The integration of advanced sensor technology is crucial for the development of intelligent and adaptable robotic systems.
Types of Sensors Used in Robotics Applications
Robotics engineers utilize a wide range of sensors, each serving specific functions that contribute to the robot‘s overall performance.
Key types of sensors include:
- Proximity Sensors: Detect objects within a certain range without physical contact. Commonly used in obstacle avoidance and object detection.
- Vision Sensors: Enable robots to perceive their environment visually, using cameras and image processing algorithms.
- Tactile Sensors: Mimic the sense of touch, allowing robots to detect pressure, texture, and force. Used in applications like gripping and assembly.
- Ultrasonic Sensors: Use sound waves to measure distance and detect objects. Often employed in navigation and obstacle detection.
- Infrared Sensors: Detect heat signatures and measure distances. Frequently used in environmental monitoring and safety applications.
- Accelerometers and Gyroscopes: Measure acceleration and rotational movement, providing critical data for balancing and stability in mobile robots.
- Temperature Sensors: Monitor temperature changes, ensuring that robots operate within safe parameters, especially in sensitive environments.
- Light Sensors: Detect variations in light intensity, useful for tasks like line following and environmental awareness.
Importance of Understanding Sensor Technology for Robotics Engineers
For robotics engineers, a deep understanding of sensor technology is essential for designing and developing effective robotic systems.
Robots use sensors to perceive and interact with their surroundings.
Sensors are crucial for the functionality and autonomy of robotic applications.
Key reasons for understanding sensor technology include:
- Designing Autonomous Systems: Engineers must choose and integrate the right sensors for robots to operate autonomously.
- Enhancing Robot Efficiency: Proper sensor selection and integration can improve a robot‘s efficiency, accuracy, and reliability in performing tasks.
- Ensuring Safety: Sensors play a crucial role in ensuring the safety of robotic systems, particularly in environments where humans and robots coexist.
- Enabling Adaptability: Advanced sensor technology allows robots to adapt to changing environments, enhancing their versatility in various applications.
- Improving Human-Robot Interaction: Understanding sensor technology helps engineers design robots that can interact more naturally and effectively with humans.
Sensor technology is the backbone of robotics engineering, providing the necessary data for robots to perceive, navigate, and interact with their environment.
By exploring various sensor types and their uses, robotics engineers can design smarter, more adaptable, and efficient robots.
This drives innovation and progress in the field.
To develop cutting-edge solutions, robotics engineers must leverage sensor technology effectively.
Mastering this technology is crucial in today‘s rapidly evolving landscape.
Delve into the Subject: Chemical Engineering Project Management Skills
Communication Protocols in Robotics
Communication protocols are essential for enabling robots to interact with other devices, systems, and components.
They define the rules and formats for data exchange, ensuring reliable and efficient communication between robotic systems and external entities.
Proper communication is crucial for the coordination, control, and functionality of robots in various applications.
Role of Communication Protocols
Communication protocols serve several key functions in robotics systems:
- Data Exchange: Protocols facilitate the transmission of data between robots and other devices, such as sensors, actuators, and controllers.
- Coordination: They enable robots to synchronize their actions with other robots or systems, essential for collaborative tasks and multi-robot systems.
- Control: Protocols allow operators to remotely control and monitor robots, providing commands and receiving status updates.
- Integration: They ensure robots integrate seamlessly with existing systems. They support interoperability across various technologies.
- Error Handling: Protocols include mechanisms for detecting and correcting errors in data transmission, ensuring reliable communication.
Common Communication Protocols Used in Robotics
Several communication protocols are widely used in robotics systems, each suited for different types of data exchange and control needs.
Common protocols include:
- Ethernet/IP: A standard for industrial network communication that supports real-time data exchange and is widely used in automation and robotics.
- CAN (Controller Area Network): A robust protocol designed for high-speed communication between microcontrollers and devices in automotive and industrial applications.
- RS-232/RS-485: Serial communication protocols used for point-to-point or multi-point communication, suitable for various control and monitoring tasks.
- Modbus: A protocol for serial communication used in industrial environments for connecting and communicating with equipment and sensors.
- Bluetooth: A wireless communication protocol for short-range data exchange, commonly used for mobile robots and wearable devices.
- Wi-Fi: Provides wireless communication over longer distances, allowing robots to connect to networked systems and the internet.
- Zigbee: A low-power, wireless protocol designed for short-range communication in sensor networks and IoT applications.
- MQTT (Message Queuing Telemetry Transport): A lightweight messaging protocol for efficient data exchange in IoT and remote systems.
Importance of Selecting the Right Communication Protocol
Selecting the appropriate communication protocol is critical for the success of robotics projects.
The right choice impacts several aspects of the system:
- Performance: The protocol must support the required data transfer rates and real-time performance necessary for the robot’s tasks.
- Compatibility: It should be compatible with the existing systems, devices, and infrastructure to ensure seamless integration.
- Reliability: The protocol must offer reliable data transmission and error handling to prevent communication failures and ensure consistent performance.
- Scalability: The chosen protocol should accommodate future expansions or upgrades, allowing the system to grow and adapt to new requirements.
- Cost: Different protocols have varying costs associated with implementation and maintenance. Choosing a protocol that balances performance and cost is essential for project success.
Communication protocols play a vital role in robotics, enabling efficient and reliable interaction between robots and other devices.
By selecting and understanding the right protocols, robotics engineers ensure effective data exchange, coordination, and control.
This drives the success of their projects.
Choosing the right communication protocol boosts the performance, reliability, and scalability of robotic systems.
This choice enhances their effectiveness and integration in different environments.
Conclusion
Having the right tools and software is crucial for robotics engineers to effectively design, develop, and test their projects.
From simulation software like ROS to hardware tools like soldering irons and multimeters, each tool plays a vital role in the success of a robotics project.
By investing in essential tools and software, robotics engineers can streamline their workflow, improve efficiency, and ultimately produce higher quality robots.
These tools not only enhance the productivity of engineers but also enable them to push the boundaries of robotics technology.
Essentially, the importance of choosing the right tools and software cannot be overstated in the field of robotics engineering.
As technology continues to advance, it becomes increasingly important for engineers to stay updated with the latest tools and software to remain competitive in the industry.
Therefore, I encourage all readers who are interested in robotics to explore the wide range of tools and software available in the market today.
By investing in the right tools, engineers can take their robotics projects to new heights and contribute to the exciting advancements in this ever-evolving field.
Transform Your Career Today
Unlock a personalized career strategy that drives real results. Get tailored advice and a roadmap designed just for you.
Start Now