Introduction
Robotics engineers play a crucial role in the growing field of automation across multiple industries.
As robotics technology advances, the demand for skilled professionals is rising.
However, robotics engineers encounter several challenges that can impact their effectiveness and productivity.
Some common challenges faced by robotics engineers include:
- Complex Design Requirements: Robotics engineers must create systems that are both functional and efficient, which often involves complex problem-solving.
- Rapid Technological Changes: Keeping up with constant technological advancements can be overwhelming and requires continuous learning and adaptation.
- Integration Difficulties: Engineers frequently struggle with integrating robotics systems into existing infrastructure without disrupting operations.
- High Costs and Budget Constraints: Developing innovative robotics solutions can be costly, and budget limitations often restrict creativity and experimentation.
- Skill Shortages: There is a high demand for robotics engineers, but finding professionals with the right skill set can be challenging.
As the significance of robotics grows in various sectors, these challenges emphasize the need for well-trained and adaptable engineers.
Lack of Standardization in Robotics Technology
Various Types Of Robotics Technology Available
Robotics technology encompasses a wide range of systems, including industrial robots, autonomous vehicles, and medical robots.
Each type of robot operates on different hardware and software platforms, making the landscape of robotics incredibly diverse.
Industrial robots often operate using specific programming languages and sensors.
Autonomous vehicles depend on complex AI algorithms and real-time data processing.
This diversity leads to a fragmented industry where various technologies coexist without a unified framework.
How Lack Of Standardization Can Lead To Compatibility Issues
The absence of standardization in robotics technology poses significant challenges, especially regarding compatibility.
Robotics engineers often face difficulties when integrating different systems, as components from various manufacturers may not work seamlessly together.
For example, an engineer working on a robotic assembly line might struggle to connect a robot from one manufacturer with a control system from another.
These compatibility issues can lead to increased development time, higher costs, and potential malfunctions, ultimately hindering innovation.
How This Challenge Affects Robotics Engineers In Their Work
One notable example of the impact of this lack of standardization is in collaborative robots, or cobots, which are designed to work alongside humans.
Engineers often encounter compatibility issues when trying to integrate cobots with existing industrial equipment.
In the field of autonomous vehicles, manufacturers use different sensor systems and communication protocols, complicating unified traffic management efforts.
These challenges underscore the need for industry-wide standards to streamline development and ensure the interoperability of robotics systems.
In general, the lack of standardization in robotics technology creates significant obstacles for engineers, leading to compatibility issues that hinder progress.
Establishing common standards could improve efficiency and foster innovation in the rapidly evolving field of robotics.
Limited Resources for Research and Development
Importance of Research and Development
Research and development (R&D) play a crucial role in advancing robotics technology.
They push the boundaries of robotics by enhancing precision and autonomy.
They also expand robots’ applications across various industries.
R&D efforts lead to innovations that drive technological progress, improve functionality, and address complex challenges.
By continuously exploring new ideas and refining existing technologies, robotics engineers can develop more efficient, reliable, and versatile robotic systems.
This ongoing process keeps the technology at the forefront and meets the evolving needs of industries like manufacturing, healthcare, and logistics.
Financial Constraints Faced by Robotics Engineers
Financial constraints are a significant hurdle for robotics engineers engaged in R&D.
Developing advanced robotics systems requires substantial investment in cutting-edge equipment, high-quality materials, and specialized components.
Additionally, hiring skilled personnel and funding extensive testing and validation processes add to the costs.
Limited budgets can restrict access to these essential resources, slowing down research progress and impacting the ability to explore innovative concepts fully.
Engineers may struggle to pursue ambitious projects or conduct comprehensive experiments. This limitation can lead to missed breakthroughs and advancements.
The Impact Of Limited Resources On Innovation In The Robotics Field
The impact of limited resources on innovation in the robotics field is profound.
When robotics engineers face financial constraints, their ability to experiment with novel ideas and develop new prototypes becomes restricted.
This limitation can lead to a slower pace of technological advancement and reduced competitiveness in the global market.
Without adequate funding, engineers must prioritize short-term goals.
They focus on incremental improvements instead of transformative breakthroughs.
Consequently, the overall rate of progress in robotics technology may be hindered, affecting its potential applications and the development of next-generation systems.
Limited resources impact individual projects and the broader robotics innovation landscape.
They delay groundbreaking technologies and reduce their impact on various sectors.
Read: How to Build a Strong CAD Technician Portfolio
Difficulty in Programming Complex Robotic Systems
The intricacies involved in programming advanced robotic systems
Programming complex robotic systems requires a deep understanding of various programming languages and concepts.
Engineers must be well-versed in languages such as C++, Python, and MATLAB to effectively program robots.
They also need to have a solid grasp of algorithms, data structures, and control systems to ensure that the robots can perform tasks accurately and efficiently.
In addition, engineers must consider factors like real-time processing, sensor integration, and motion planning to program advanced robotic systems successfully.
The need for specialized skills in programming
Programming robots goes beyond basic coding skills.
Robotics engineers need to have specialized knowledge in areas such as artificial intelligence, machine learning, and computer vision to develop intelligent robotic systems.
They must be able to analyze complex problems, design algorithms, and implement them effectively in the robotic software.
Moreover, they need to understand the dynamics of robotic systems and be able to optimize algorithms for performance and efficiency.
As robotics technology advances, engineers must continuously update their skills to stay relevant in the field.
Examples of common programming challenges faced by robotics engineers
One common challenge is dealing with the complexity of sensor data processing.
Robots rely on sensors to perceive their environment and make decisions.
Processing large amounts of sensor data in real-time requires sophisticated algorithms and efficient coding practices.
Another challenge is ensuring the safety of autonomous robots.
Engineers need to program robots to make safe and ethical decisions in dynamic environments.
This requires developing robust algorithms that can handle unexpected situations and prevent accidents.
Furthermore, navigation and path planning are crucial aspects of robotics programming.
Engineers must program robots to navigate through complex environments, avoid obstacles, and reach their destinations efficiently.
This involves implementing algorithms for localization, mapping, and path optimization.
In a nutshell, programming complex robotic systems is a challenging task that requires specialized skills, knowledge, and experience.
Robotics engineers must continuously update their skills and adapt to new technologies to overcome the programming challenges they face.
Read: Best Online Courses for CAD Technician Training
Safety Concerns in Robotic Applications
Importance of Safety Protocols in Robotics
Ensuring safety protocols are in place is crucial in robotics to prevent accidents.
Robotic engineers must prioritize safety measures to protect both humans and equipment.
Failing to implement proper safety protocols can lead to catastrophic consequences.
Potential Risks Associated with Robotic Applications
One major risk in robotic applications is physical harm to humans or other living beings.
Transform Your Career Today
Unlock a personalized career strategy that drives real results. Get tailored advice and a roadmap designed just for you.
Start NowAnother risk is damage to property or equipment due to malfunctioning robots.
Cybersecurity threats pose a significant risk to robotic systems and can result in data breaches.
Examples of Safety Incidents in the Robotics Industry
In 2014, a worker was killed by a robotic arm at a Volkswagen plant in Germany.
Tesla faced scrutiny after its autonomous vehicles were involved in accidents, raising safety concerns.
The Fukushima nuclear disaster in 2011 highlighted the dangers of relying too heavily on robotics.
Robotic engineers must learn from past safety incidents to prevent future accidents.
Read: Future of CAD Technician Jobs in Engineering
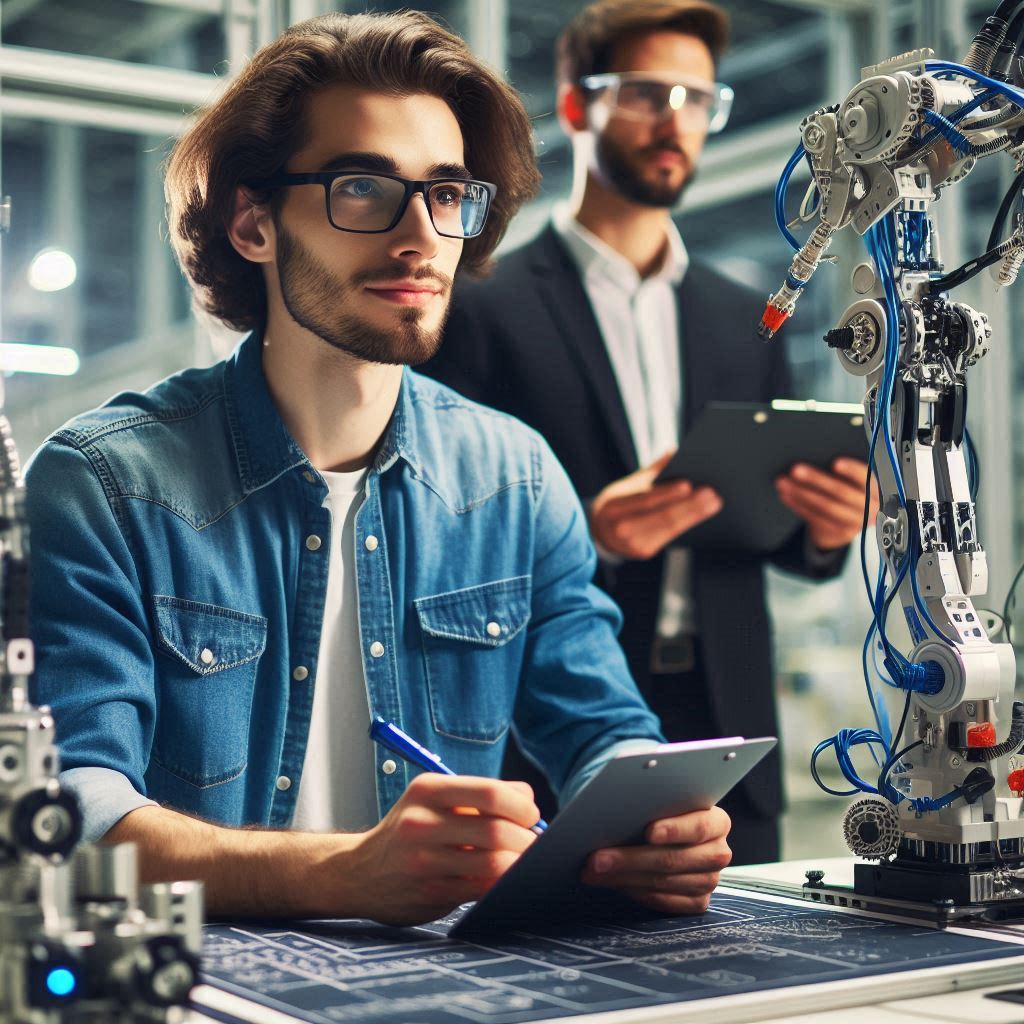
High Cost of Robotic Components
One of the most common challenges faced by robotics engineers is the high cost of robotic components.
This issue can significantly impact the development and progress of robotics projects.
In this section, we will explore the cost factors in designing and building robotic systems.
We will explain how expensive components can hinder projects.
We will also offer tips on cost-saving strategies for robotics engineers.
Cost Factors in Designing and Building Robotic Systems
- Complexity of Components: Robotics systems often require intricate and specialized components.
- R&D Costs: Research and development expenses for new technologies can be high.
- Customization: Customized parts or systems can drive up costs.
- Quality Standards: High-quality components can come with a premium price tag.
- Manufacturing Costs: The cost of manufacturing robotic components can be expensive.
How The High Cost Of Components Can Hinder The Development Of Robotics Projects
- Stalled Progress: High costs can delay or halt the progress of robotics projects.
- Limited Innovation: Engineers may be restricted in their ability to innovate due to budget constraints.
- Reduced Accessibility: High component costs can make robotics projects less accessible to smaller organizations or individuals.
- Increased Development Time: Costly components can prolong the development timeline of projects.
- Budget Constraints: Limited budget may result in compromises on quality or scope of projects.
Tips Cost-Saving Strategies for Robotics Engineers
- Reuse and Recycle: Repurpose existing components or materials to reduce costs.
- Collaboration: Partner with other organizations or individuals to share costs and resources.
- Open-Source Solutions: Utilize open-source hardware and software to minimize expenses.
- DIY Approach: Adopt a do-it-yourself mentality to build components or systems from scratch.
- Bulk Purchasing: Buy components in bulk to take advantage of volume discounts.
In essence, robotics engineers face high costs for components, but strategies exist to mitigate these financial challenges.
Engineers can overcome high component costs by understanding cost factors, recognizing their impact, and implementing cost-saving strategies.
These actions drive continued innovation in robotics.
Read: Top Companies Hiring CAD Technicians in the USA
Limited Access to Training and Education
Robotics engineers often face challenges due to the limited access to specialized training programs in the field.
This lack of dedicated educational resources can hinder their professional growth and development.
The lack of specialized training programs for robotics engineers
One of the significant challenges faced by robotics engineers is the absence of comprehensive training programs that cater specifically to their needs.
Most traditional engineering programs do not offer courses that focus solely on robotics.
This gap in specialized education can make it difficult for robotics engineers to acquire the necessary skills and knowledge required to excel in their field.
As a result, they may struggle to keep up with the latest advancements in robotics technology and industry trends.
The importance of continuous learning in the rapidly evolving robotics field
In a field as dynamic as robotics, continuous learning is essential for staying relevant and competitive.
Robotics engineers need to constantly upgrade their skills and knowledge to adapt to the rapidly evolving landscape of technology.
Robotics engineers risk falling behind their peers and missing out on growth opportunities without ongoing education and training.
Continuous learning enables them to stay abreast of emerging trends and innovations in the field.
Resources for robotics engineers to enhance their skills and knowledge
- Online courses: Platforms like Udemy, Coursera, and edX offer a wide range of online courses specifically tailored to robotics engineers.
- Workshop and seminars: Attending workshops and seminars can provide hands-on experience and networking opportunities for robotics engineers.
- Professional certifications: Obtaining certifications from reputable organizations can help validate the skills and knowledge of robotics engineers.
- Industry conferences: Participating in industry conferences allows robotics engineers to learn about the latest trends and technologies in the field.
- Mentorship programs: Joining mentorship programs can provide guidance and support for robotics engineers looking to enhance their skills and knowledge.
By taking advantage of these resources, robotics engineers can overcome the challenges posed by limited access to training and education in the field.
Continuous learning and professional development are crucial for their success in the rapidly evolving world of robotics.
Ethical Considerations in Robotics Development
Robotics technology has brought about a myriad of ethical implications that require careful consideration in society.
Robotics engineers must address ethical considerations to maximize benefits and minimize potential harm in advancing technology.
The ethical implications of robotics technology in society
- Privacy concerns: Robotics technology, such as drones and surveillance robots, raise concerns about invasion of privacy and data security.
- Autonomous decision making: Autonomous robots that can make decisions independently raise questions about accountability and moral reasoning.
- Job displacement: The automation of tasks through robotics technology can lead to job loss and economic inequality.
- Weaponization of robots: The development of military robots raises ethical concerns about the use of autonomous weapons and warfare.
The importance of considering ethical principles in robotics design
Integrating ethical principles into robotics design is essential to ensure that robots are developed and utilized in a responsible and ethical manner.
By prioritizing ethical considerations, robotics engineers can contribute to the development of technology that benefits society as a whole.
Examples of ethical dilemmas faced by robotics engineers
- Programming biases: The algorithms used to program robots can reflect the biases of the designers, leading to discriminatory outcomes.
- Data security: As robots collect and process sensitive data, there are ethical concerns about data privacy and protection.
- Decision-making algorithms: The algorithms that govern autonomous robots raise questions about how decisions are made and who is responsible for the outcomes.
- Impact on society: Robotics technology can profoundly reshape society, raising ethical questions about its impact on individuals and communities.
Generally, the ethical considerations in robotics development play a critical role in shaping the future of technology and society.
Robotics engineers must address ethical implications and dilemmas to ensure a more ethical use of robotics technology.
See Related Content: Environmental Engineering and Urban Planning
Delve into the Subject: Certifications for Biomedical Equipment Technicians
Integration Challenges in Multi-Robot Systems
Integrating multiple robots to work together presents complex challenges that require careful planning and execution.
These challenges include coordinating robots seamlessly, communicating effectively, synchronizing operations, and maintaining system stability and efficiency.
Transform Your Career Today
Unlock a personalized career strategy that drives real results. Get tailored advice and a roadmap designed just for you.
Start NowComplexities in Multi-Robot Integration
When integrating multiple robots, engineers face the complexity of managing different systems, each with unique capabilities and limitations.
Ensuring that these robots can communicate effectively and operate without interference is crucial.
Robots must be synchronized to perform tasks in tandem without causing delays or conflicts.
Additionally, engineers must consider the computational resources required for real-time processing and decision-making in a multi-robot environment.
Coordination and Communication Challenges
Coordination is a significant challenge in multi-robot systems.
Robots must work together to achieve common goals without duplicating efforts or causing collisions.
Effective communication is essential to ensure that robots share information, update their positions, and adapt to changes in the environment.
Engineers must develop robust communication protocols that prevent data loss and ensure all robots stay informed.
Overcoming Integration Challenges
To overcome these integration challenges, robotics engineers can adopt several strategies.
First, they should standardize communication protocols across all robots, ensuring compatibility and reducing the risk of miscommunication.
Second, engineers can implement advanced algorithms for task allocation and scheduling, which help distribute tasks efficiently among robots.
Lastly, thorough testing and simulation are vital.
Engineers should test multi-robot systems in controlled environments to identify potential issues before deploying them in real-world scenarios.
By addressing these complexities, engineers can enhance the performance and reliability of multi-robot systems, leading to more efficient and effective operations.
Discover More: Common Challenges Faced by Mining Engineers Today
Learn More: Ethical Considerations in Environmental Engineering
Conclusion
Robotics engineers encounter a multitude of challenges in their work, from designing and programming robots to ensuring their safety and efficiency.
It is essential to address these challenges to advance the field of robotics and unlock its full potential in various industries.
Collaboration and dialogue among robotics engineers are crucial to overcoming these common challenges and pushing the boundaries of robotics technology.
One of the key challenges faced by robotics engineers is the complexity of designing and programming robots.
Another challenge is ensuring the safety of robots, especially as they interact with humans in various environments.
Issues related to power sources and energy efficiency also pose significant challenges for robotics engineers.
Additionally, robotics engineers often struggle with integrating different software and hardware components to create functional robots.
Designing robots that can adapt to unpredictable and dynamic environments is a common challenge in the field.
Moreover, robotics engineers face challenges related to optimizing the performance of robots while minimizing costs.
Ensuring the reliability and durability of robots over time is another critical challenge faced by robotics engineers.