Introduction:
A Quality Control Inspector plays a crucial role in ensuring product compliance in various industries.
They are responsible for inspecting, testing, and evaluating products to ensure they meet quality standards.
Quality control is essential in manufacturing and production industries to maintain consistency, meet customer expectations, and comply with regulations.
It helps prevent defects, reduce waste, and improve overall product quality.
The purpose of this blog post is to delve into the role of a Quality Control Inspector, the importance of quality control in manufacturing, and the impact they have on ensuring product compliance.
Role of a Quality Control Inspector
The role of a Quality Control Inspector is crucial in ensuring that products meet certain standards before reaching the customer.
They play a key part in upholding quality and compliance within a company.
Responsibilities of a Quality Control Inspector
- Inspecting products to ensure they meet quality standards set by the company.
- Conducting tests and analysis on samples to check for defects or flaws.
- Documenting and reporting any issues found during the inspection process.
- Collaborating with production teams to address and resolve quality concerns.
- Implementing and adhering to quality control procedures and protocols.
Importance of their role in ensuring product compliance and customer satisfaction
Quality Control Inspectors are the gatekeepers of quality in a company.
Their role is critical in ensuring that products not only meet industry standards but also satisfy customer expectations.
Here are some reasons why their role is vital:
- Product Integrity: By carefully inspecting products, Quality Control Inspectors help maintain the integrity and reputation of the brand.
- Compliance with Regulations: They ensure that products comply with all relevant laws and regulations, preventing any legal issues for the company.
- Customer Trust: Inspecting products for quality builds trust with customers, leading to increased satisfaction and loyalty.
- Cost Savings: Identifying defects early in the production process can save the company from costly recalls or returns.
- Continuous Improvement: By providing feedback on product quality, inspectors contribute to the continuous improvement of processes and products.
Skills Required to be a Successful Quality Control Inspector
Attention to detail is one of the most crucial skills that a quality control inspector must possess.
This involves being able to carefully examine and identify even the smallest defects in a product to ensure compliance with quality standards.
Strong communication skills are essential for a quality control inspector to relay information clearly and concisely to colleagues, supervisors, and other team members.
This includes being able to provide feedback, report findings, and collaborate with others to improve processes.
Additionally, quality control inspectors need to be able to analyze data collected from inspections, tests, and audits to make informed decisions about the quality of a product.
This involves interpreting data, identifying trends, and using critical thinking skills to determine the best course of action to ensure compliance.
In addition to these key skills, successful quality control inspectors often possess a combination of technical knowledge, problem-solving abilities, and a strong work ethic.
By honing these skills and continually seeking opportunities for growth and development, quality control inspectors can make a significant impact in ensuring product compliance and maintaining high standards of quality in their organization.
Explore Further: Veterinary Collaborations in Dairy Science
Transform Your Career Today
Unlock a personalized career strategy that drives real results. Get tailored advice and a roadmap designed just for you.
Start NowQuality Control Inspection Process
Quality control inspection is a crucial process in ensuring product compliance.
It involves various steps to guarantee that products meet the required quality standards.
Steps Involved in Inspecting Products for Compliance
- Receive the product for inspection.
- Review the specifications and quality standards.
- Inspect the product visually for any defects.
- Conduct measurements using appropriate tools.
- Check the functionality of the product.
- Compare the results with the set standards.
- Document the inspection results for reference.
Quality control inspectors utilize a variety of tools and equipment to measure quality standards accurately.
These tools help ensure that products are manufactured according to specifications and meet quality requirements.
Use of Tools and Equipment to Measure Quality Standards
- Calipers: Used to measure dimensions precisely.
- Micrometers: Ensures accurate measurements of small parts.
- Gauges: Used to verify tolerances and dimensions.
- CMM (Coordinate Measuring Machine): Provides precise measurement data for complex parts.
- Spectrophotometer: Measures color consistency in products.
- X-ray machines: Used for internal inspection of products.
- Thermal imaging cameras: Detects temperature variations in products.
By following a systematic process of quality control inspection and using the right tools and equipment, quality control inspectors play a critical role in ensuring that products are compliant with quality standards and specifications.
Learn More: Creating a Sustainable Farm Business Model
Importance of Quality Control Inspection
When it comes to quality control inspection, adherence to regulations and standards is of utmost importance.
This section will discuss the significance of following industry standards and regulations.
We will also cover the consequences of failing to comply with quality standards.
Overview of Industry Standards and Regulations
Industry standards and regulations are put in place to ensure that products meet specific criteria for quality, safety, and performance.
These standards are developed by organizations such as the International Organization for Standardization (ISO), the American National Standards Institute (ANSI), and the American Society for Testing and Materials (ASTM).
Industry-specific regulations may also apply depending on the type of product being manufactured.
These regulations help create consistency in product quality and ensure that products are safe for consumers to use.
Consequences of Not Complying with Quality Standards
Failure to comply with quality standards can have serious consequences for a company.
Some of the potential repercussions include:
- Loss of reputation: When products fail to meet quality standards, it can damage a company’s reputation in the marketplace.
- Legal issues: Non-compliance with regulations can result in fines, lawsuits, and legal penalties.
- Recalls: If products do not meet quality standards, they may need to be recalled, leading to financial losses and negative publicity.
- Loss of customers: Consumers expect products to meet certain quality standards, and failure to do so may result in a loss of customer trust and loyalty.
It is essential for companies to prioritize quality control inspection and ensure compliance with industry standards and regulations to avoid these negative outcomes.
By investing in quality control processes and monitoring product compliance, companies can maintain a competitive edge in the market.
They can build consumer trust and safeguard their reputation.
Uncover the Details: Agricultural Labor Jobs for Veterans: Opportunities and Support
Benefits of Having a Quality Control Inspector
Quality Control Inspectors play a crucial role in ensuring that products meet high standards.
Transform Your Career Today
Unlock a personalized career strategy that drives real results. Get tailored advice and a roadmap designed just for you.
Start NowLet’s delve into the benefits of having a Quality Control Inspector in place.
Reduced Production Costs
By catching defects early in the production process, Quality Control Inspectors help reduce costs associated with rework or scrap materials.
Increased Customer Satisfaction and Loyalty
When products meet quality standards, customers are more likely to be satisfied with their purchases.
This leads to repeat business and brand loyalty.
Prevention of Product Recalls and Reputation Damage
Quality Control Inspectors help prevent the distribution of defective products.
This can save a company from costly recalls and protect its reputation in the market.
Investing in a Quality Control Inspector is a proactive approach to maintaining product quality and ensuring customer satisfaction.
These professionals are trained to identify deviations from specifications and work closely with production teams to address issues promptly.
Having a Quality Control Inspector on staff can lead to significant cost savings in the long run by minimizing rework and waste.
Moreover, these inspectors act as a line of defense against potential quality issues that could harm a company’s reputation.
Through regular inspections and audits, Quality Control Inspectors can detect quality problems early in the production process.
By maintaining consistent quality standards, companies can build a reputation for reliability and trustworthiness among consumers.
Ultimately, the role of a Quality Control Inspector is crucial in upholding product compliance and meeting customer expectations.
Companies that prioritize quality control benefit from improved operational efficiency and long-term business sustainability.
Quality Control Inspectors serve as quality ambassadors.
They ensure that products leaving the production line meet established criteria.
With their attention to detail and commitment to excellence, these professionals play a vital role in maintaining product integrity and customer satisfaction.
Gain More Insights: Innovative Irrigation Techniques for Specialists
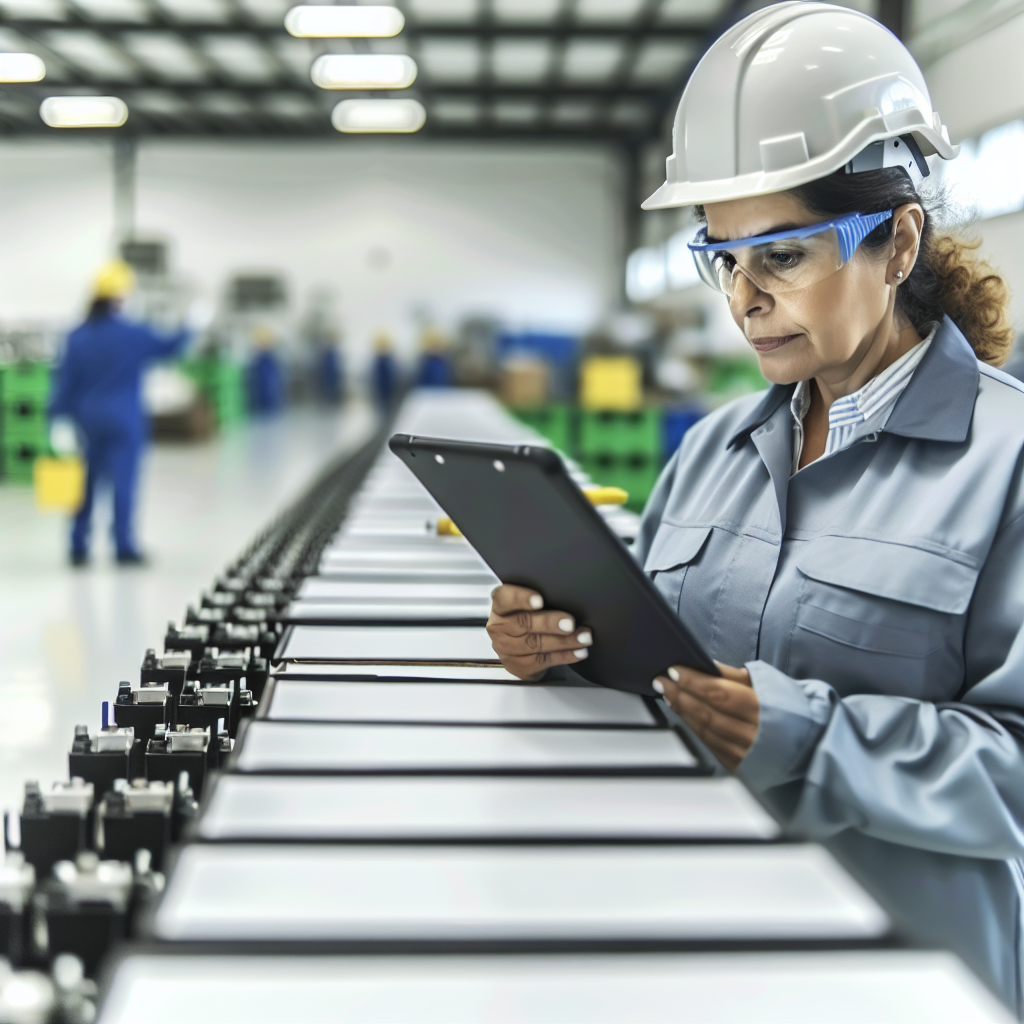
Challenges Faced by Quality Control Inspectors
Quality control inspectors play a vital role in ensuring product compliance with regulations and standards.
However, their job is not without challenges.
Transform Your Career Today
Unlock a personalized career strategy that drives real results. Get tailored advice and a roadmap designed just for you.
Start NowDealing with High Volume Production
- Inspectors often have to work with large quantities of products being produced, making it difficult to thoroughly inspect each item.
- Tight deadlines and pressure to meet production targets can also impact the quality control process.
- High volume production can lead to fatigue and the risk of overlooking defects or non-compliance issues.
Ensuring Consistency in Inspections
- Consistency is key in quality control inspections to ensure that all products meet the same standards.
- Inspectors must follow strict protocols and guidelines to maintain consistency in their evaluations.
- Training and development programs can help inspectors improve their skills and ensure uniformity in inspections.
Handling Non-Compliant Products
- Inspectors often encounter products that do not meet quality standards or regulatory requirements.
- Dealing with non-compliant products requires decision-making skills and the ability to enforce corrective actions.
- Communication with production teams and managers is essential to address non-compliance issues effectively.
Technologies and Advancements in Quality Control
Automated systems improve efficiency and accuracy in quality control.
They can handle repetitive tasks with precision and consistency.
Reducing human error and increasing productivity on the production line.
Introduction of Automated Inspection Systems
Data analytics helps in identifying patterns and trends for better decision-making.
Predictive analytics can anticipate defects before they occur.
Improving overall product quality and minimizing risks of non-compliance.
Benefits of Automated Inspection Systems:
- Enhanced Accuracy: Automated systems provide precise measurements and data.
- Increased Productivity: Tasks are completed faster and more efficiently.
- Cost Savings: Reducing manual labor costs and minimizing errors.
- Improved Compliance: Ensuring products meet regulatory standards consistently.
Benefits of Data Analytics for Predictive Quality Control:
- Proactive Approach: Identifying issues before they impact production.
- Real-time Monitoring: Tracking quality metrics continuously for adjustments.
- Decision Support: Providing insights for process improvements and optimizations.
- Sustainable Quality: Ensuring consistent quality levels over time.
Challenges in Implementing Advanced Quality Control Technologies:
- Initial Investment Cost: Automated systems and data analytics tools can be expensive.
- Training and Skills: Employees need to be trained to operate new technologies.
- Integration with Existing Systems: Ensuring compatibility with current processes.
- Data Security: Protecting sensitive information gathered from quality control processes.
Future Trends in Quality Control Technology:
- Internet of Things (IoT) Integration: Connected devices for real-time monitoring and control.
- Artificial Intelligence (AI): Using AI algorithms for data analysis and decision-making.
- Robotics: Automated robots for inspection and quality assurance tasks.
- Blockchain Technology: Ensuring transparency and traceability in quality control processes.
Embracing advanced technologies in quality control is crucial for ensuring product compliance in today’s competitive market.
Automated inspection systems and data analytics provide valuable insights and predictive capabilities that help organizations maintain high-quality standards consistently.
While there are challenges in implementing these technologies, the benefits far outweigh the initial barriers.
Looking towards the future, IoT, AI, robotics, and blockchain are poised to revolutionize quality control practices and drive continuous improvement in product quality and compliance.
Ensuring Product Compliance Through Quality Control
Quality Control Inspectors play a crucial role in ensuring product compliance through rigorous inspections and evaluations.
Importance of Quality Control Inspectors
They are responsible for maintaining the quality and integrity of products, which directly impacts customer satisfaction and brand reputation.
By detecting and rectifying any defects or deviations from standards, Quality Control Inspectors prevent costly recalls and legal issues.
Their meticulous work guarantees that products meet regulatory requirements and industry standards, ensuring consumer safety and satisfaction.
Strategies for Quality Control Excellence
Companies must prioritize quality control inspections to not only comply with regulations but also maintain a competitive edge in the market.
Investing in a robust quality control process can lead to improved product quality, increased customer trust, and overall business success.
By empowering Quality Control Inspectors with the tools and training they need, companies can achieve excellence in product compliance.
It is imperative for businesses to understand the significance of quality control and make it a key focus for long-term success.
Additional Resources
Federal Grain Inspection Service | Agricultural Marketing Service
Part 46 – Quality Assurance | Acquisition.GOV
Transform Your Career Today
Unlock a personalized career strategy that drives real results. Get tailored advice and a roadmap designed just for you.
Start Now[E-Books for Sale]
The Big Book of 500 High-Paying Jobs in America: Unlock Your Earning Potential
$19.99 • 500 High-Paying Jobs • 330 pages
Explore 500 high-paying jobs in America and learn how to boost your career, earn more, and achieve success!
See All 500 High-Paying Jobs of this E-Book
1001 Professions Without a Degree: High-Paying American Jobs You Can Start Now
$19.99 • 1001 Professions Without a Degree • 174 pages
Discover 1001 high-paying jobs without a degree! Unlock career tips, skills, and success strategies for just $19.99!