Introduction
Quality Control Inspectors and Quality Assurance professionals play crucial roles in ensuring the quality of products and services.
They are responsible for maintaining standards, identifying defects, and implementing corrective actions to improve overall quality.
In various industries such as manufacturing, healthcare, and technology, quality control and assurance are paramount to success.
Quality control inspectors focus on examining products or services to detect defects and deviations from specifications.
On the other hand, quality assurance professionals are involved in developing and implementing quality standards and processes.
Both roles are essential in maintaining customer satisfaction, compliance with regulations, and overall business success.
Having a strong quality control and assurance program in place can enhance a company’s reputation and competitiveness in the market.
By actively monitoring and evaluating processes, these professionals help prevent issues before they impact the end-user.
In essence, quality control inspectors and quality assurance professionals play complementary roles in ensuring high-quality products and services.
Their attention to detail, adherence to standards, and commitment to improvement are vital for the success of any organization.
Role of a Quality Control Inspector
Responsibilities of inspecting products, materials, and processes to ensure they meet quality standards
Quality Control Inspectors play a crucial role in ensuring that products meet the required quality standards.
They are responsible for inspecting products, materials, and processes to ensure they meet the specified criteria.
Let’s delve into the specifics of their role and responsibilities.
As a Quality Control Inspector, one of the primary responsibilities is to inspect products, materials.
And processes to ensure they meet quality standards set by the company or regulatory bodies.
This involves checking for any defects, deviations, or non-conformities that may affect the quality of the final product.
Conducting thorough inspections and tests to identify defects or deviations from specifications
Conducting thorough inspections and tests is a crucial aspect of a Quality Control Inspector’s role.
They must follow established procedures and protocols to ensure that all aspects of the product or process are evaluated effectively.
This includes visual inspections, measurements, and testing to confirm compliance with specifications.
When defects or deviations are identified during inspections, Quality Control Inspectors must report their findings promptly.
This includes documenting the issue, its severity, and any potential impact on the product’s quality.
Additionally, they are responsible for recommending corrective actions to address the root cause of the problem and prevent recurrence in the future.
Furthermore, Quality Control Inspectors play a proactive role in improving quality within the organization.
By identifying trends or recurring issues in the inspection process, they can suggest process improvements, training programs.
Or quality control measures to enhance overall quality performance.
Reporting findings and recommending corrective actions to improve quality
Overall, Quality Control Inspectors play a critical role in ensuring that products meet quality standards through meticulous inspections, reporting of findings, and continuous improvement efforts.
Their attention to detail, technical knowledge, and commitment to quality assurance are essential for maintaining high standards of product quality.
Generally, the role of a Quality Control Inspector is vital in the manufacturing and production industry.
By fulfilling their responsibilities effectively, they contribute to the overall quality of products and processes.
Ultimately providing customers with products that meet their expectations and regulatory requirements.
Qualifications and skills required for a Quality Control Inspector
Quality control inspectors play a crucial role in ensuring that products meet specific quality standards and regulations before they reach consumers.
To excel in this role, individuals need to possess a combination of qualifications and skills that enable them to effectively evaluate and assess product quality.
Below are some of the key qualifications and skills required for a quality control inspector
Education and Training Background
One of the primary qualifications for a quality control inspector is having a solid education and training background in quality control or a related field.
This could include a degree in quality assurance, industrial engineering, manufacturing technology, or a similar discipline.
Having the necessary educational foundation equips inspectors with the knowledge and understanding of quality control principles and practices.
Attention to Detail and Ability to Follow Instructions
Attention to detail is a critical skill for quality control inspectors, as they are responsible for thoroughly examining products and identifying any defects or discrepancies.
Inspectors must have a keen eye for detail and be able to spot even the smallest imperfections that could affect product quality.
Additionally, inspectors must be adept at following instructions and protocols to ensure consistent and accurate evaluation of products.
Strong Analytical and Problem-Solving Skills
Quality control inspectors need to possess strong analytical and problem-solving skills to effectively evaluate product quality and identify issues that may impact performance or safety.
Inspectors must be able to analyze data, interpret quality control metrics, and make informed decisions on product acceptability.
Additionally, inspectors must be skilled at identifying root causes of quality issues and implementing corrective actions to prevent future defects.
Overall, quality control inspectors play a vital role in upholding product quality standards and ensuring that consumers receive safe and reliable products.
By possessing the right qualifications and skills, inspectors can effectively carry out their responsibilities and contribute to the overall success of a company’s quality control efforts.
Read: Sustainable Wastewater Treatment Methods
Role of a Quality Assurance professional
Focus on Developing and Implementing Quality Management Systems
A Quality Assurance (QA) professional plays a crucial role in developing and implementing quality management systems.
They design frameworks that guide organizations in maintaining consistent quality.
These systems establish procedures and standards to ensure products and services meet defined criteria.
QA professionals work to integrate these systems into daily operations.
They collaborate with various departments to tailor quality practices to specific needs.
Effective implementation ensures that all processes align with organizational goals and regulatory requirements.
Ensuring Compliance with Quality Standards and Regulations
Another essential role of QA professionals is ensuring compliance with quality standards and regulations.
They stay informed about relevant industry laws and guidelines.
This knowledge helps them maintain adherence to quality benchmarks across all operations.
QA professionals regularly review and update quality policies to reflect changes in regulations.
They conduct assessments to verify that procedures meet required standards.
Their work ensures that products are safe, functional, and meet customer expectations.
Conducting Audits and Evaluations to Monitor and Improve Processes
QA professionals conduct regular audits and evaluations to monitor and improve processes.
These audits assess whether procedures align with established quality standards.
They identify areas for improvement and address potential issues before they affect the final product.
During evaluations, QA professionals review production methods, testing protocols, and documentation practices.
They use their findings to propose enhancements and collaborate with teams to implement changes.
This proactive approach helps prevent quality issues and enhances overall product reliability.
Additionally, QA professionals develop and deliver training programs to educate employees on quality standards.
Effective training ensures that all team members understand their role in maintaining quality.
QA professionals also manage quality documentation, which supports transparency and accountability.
Overall, QA professionals are essential in upholding high standards of quality.
They ensure that organizations comply with regulations, develop robust quality management systems, and continuously improve processes through regular audits and evaluations.
Their efforts contribute to reliable products and services, fostering customer trust and organizational success.
Read: Environmental Engineers in the Mining Industry
Qualifications and Skills Required for a Quality Assurance Professional
Strong Knowledge of Quality Management Principles and Practices
A successful Quality Assurance (QA) professional must have a deep understanding of quality management principles.
This includes knowledge of standards such as ISO 9001, Six Sigma, and Lean methodologies.
They should grasp quality control, process improvement, and compliance requirements.
Mastery of these principles ensures they can set up and maintain effective quality systems.
This expertise helps QA professionals uphold industry standards and drive organizational quality efforts.
Experience in Implementing Quality Assurance Programs
Practical experience is crucial for QA professionals.
They need hands-on experience in developing and managing quality assurance programs.
This includes designing and executing QA initiatives that enhance product quality and operational efficiency.
Experience often involves conducting audits, analyzing performance data, and implementing corrective actions.
This background helps QA professionals address quality issues effectively and implement solutions that align with organizational goals.
Excellent Communication and Leadership Skills
Communication skills are essential for QA professionals.
They must convey quality standards and expectations clearly to team members.
Effective communication ensures that everyone understands their role in maintaining quality.
QA professionals also need to explain complex quality issues and solutions to stakeholders at various levels.
Strong communication prevents misunderstandings and fosters a quality-focused culture within the organization.
Leadership skills are equally important.
QA professionals often lead teams or workgroups focused on quality improvements.
They must inspire and motivate their team to adhere to quality standards and achieve performance goals.
Strong leadership helps in navigating challenges, resolving conflicts, and driving continuous improvement.
Effective leaders guide their teams in maintaining high-quality standards and implementing successful quality initiatives.
In summary, a Quality Assurance professional should possess a thorough understanding of quality management principles.
Practical experience in implementing QA programs, and excellent communication and leadership skills.
These qualifications and skills are critical for maintaining high-quality standards and driving continuous improvement within an organization.
Read: Public Health and Environmental Engineering
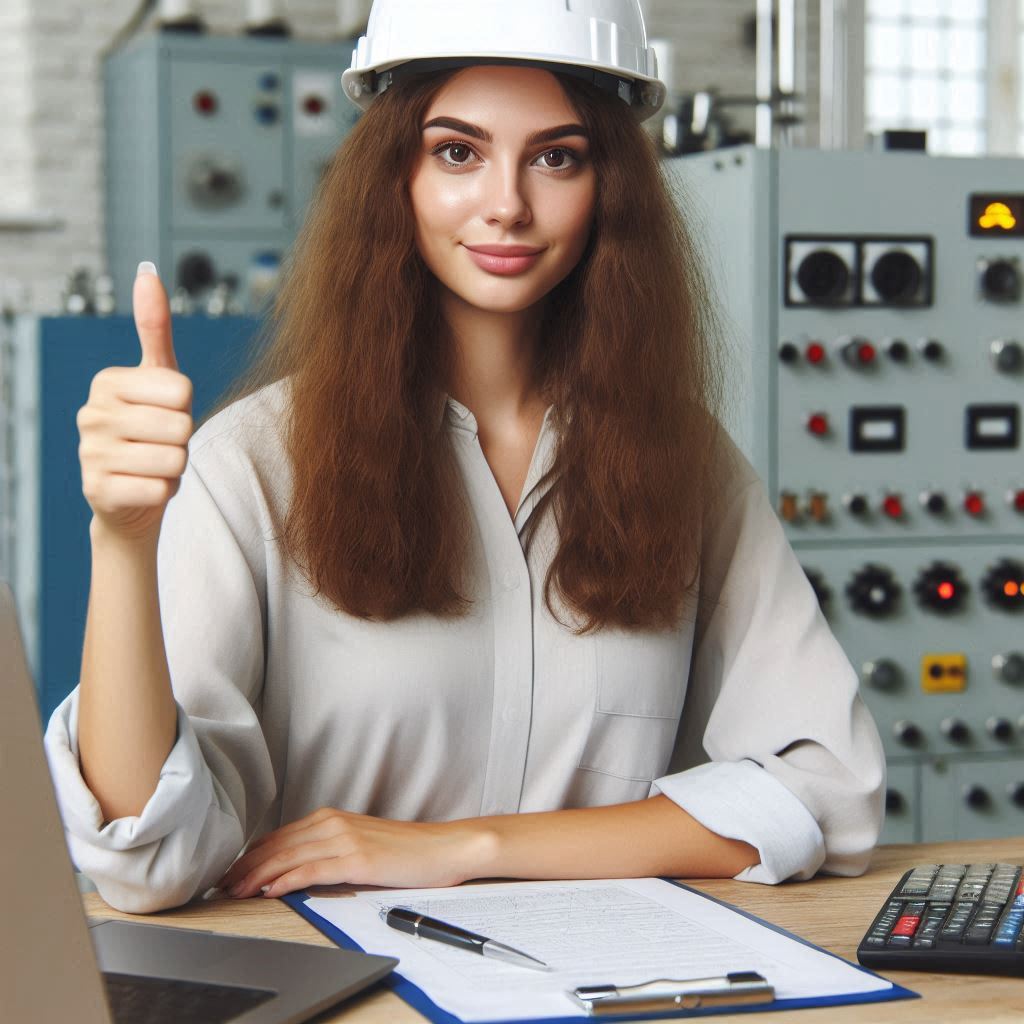
Uncover the Details: Robotics Engineering and Artificial Intelligence Synergy
Key differences between Quality Control Inspector and Quality Assurance professional
- Focus: Quality Control Inspector focuses on inspecting products and materials, while Quality Assurance professional focuses on developing and implementing quality management systems.
- Responsibilities: Quality Control Inspector identifies defects and deviations, while Quality Assurance professional monitors processes and ensures compliance with standards.
Quality control and quality assurance are two essential components in ensuring the quality of products and services.
While they both play crucial roles in maintaining quality standards, there are key differences between a Quality Control Inspector and a Quality Assurance professional.
Focus of Quality Control Inspector
A Quality Control Inspector is primarily responsible for inspecting products and materials to ensure they meet specific quality criteria.
They are tasked with identifying defects, deviations, and non-conformities in the products through meticulous inspection and testing processes.
Transform Your Career Today
Unlock a personalized career strategy that drives real results. Get tailored advice and a roadmap designed just for you.
Start NowFocus of Quality Assurance Professional
On the other hand, a Quality Assurance professional focuses on the development and implementation of quality management systems.
They are responsible for establishing processes, procedures, and standards to ensure consistency and quality throughout the entire production or service delivery process.
Responsibilities of Quality Control Inspector
The key responsibilities of a Quality Control Inspector include conducting visual inspections.
Performing tests, analyzing data, documenting findings, and recommending corrective actions to address any quality issues identified during the inspection process.
Responsibilities of Quality Assurance Professional
In contrast, a Quality Assurance professional is responsible for monitoring processes, auditing quality systems.
Conducting compliance checks, and continuous improvement initiatives to ensure that products and services meet regulatory requirements and industry standards.
Collaboration between Quality Control and Quality Assurance
While Quality Control Inspectors focus on identifying defects and non-conformities in products, Quality Assurance professionals work to prevent these issues from occurring in the first place.
By collaborating and communicating effectively, both roles can work together to uphold and improve the overall quality of products and services.
Key differences summarized
- Quality Control Inspector focuses on inspecting products and materials, while Quality Assurance professional focuses on developing and implementing quality management systems.
- Quality Control Inspector identifies defects and deviations, while Quality Assurance professional monitors processes and ensures compliance with standards.
Basically, both Quality Control and Quality Assurance professionals are integral parts of the quality management process.
While they have distinct roles and responsibilities, they ultimately work together to ensure that products and services meet the highest quality standards and exceed customer expectations.
It is essential for organizations to recognize the importance of both roles and invest in comprehensive quality control and quality assurance programs to achieve long-term success and sustainability.
Read: Environmental Engineering Software and Tools
Find Out More: Common Challenges for CAD Technicians and Solutions
Discover More: Geotechnical Engineering: Case Studies
Discover More: How to Stay Updated with Computer Engineering Trends
Importance of Quality Control Inspectors and Quality Assurance professionals in maintaining product quality
Quality control inspectors and quality assurance professionals play a crucial role in ensuring that products meet customer expectations and regulatory requirements.
Their job involves meticulous attention to detail and thorough evaluation of products at various stages of production.
Ensuring products meet customer expectations and regulatory requirements
One of the key responsibilities of quality control inspectors and quality assurance professionals is to ensure that products meet the standards set by customers and regulatory bodies.
They meticulously check every aspect of the product to ensure that it meets the specified criteria and is safe for use.
By thoroughly inspecting products, they can identify any potential defects or deviations from the standards, allowing them to take corrective action before the products are released to the market.
This helps in preventing any quality issues that could potentially harm consumers or damage the reputation of the company.
Preventing defects and deviations in production processes
Quality control inspectors and quality assurance professionals are responsible for monitoring production processes to identify any potential issues that could lead to defects in the final product.
By conducting regular inspections and audits, they can identify areas where improvements are needed to prevent defects from occurring.
They work closely with production teams to implement corrective measures and ensure that products meet the desired quality standards.
This proactive approach helps in preventing defects and deviations in production processes, leading to higher quality products that meet customer expectations.
Improving overall quality and efficiency
Quality control inspectors and quality assurance professionals play a vital role in improving the overall quality and efficiency of production processes.
By identifying areas where improvements are needed, they help in streamlining operations and reducing waste.
They work with cross-functional teams to implement quality control measures and provide training to ensure that all employees are aware of the quality standards that need to be met.
This collaborative approach helps in creating a culture of quality within the organization, leading to continuous improvement in product quality and efficiency.
In the end, quality control inspectors and quality assurance professionals are essential in maintaining product quality and ensuring that products meet customer expectations and regulatory requirements.
Their diligent work helps in preventing defects, improving efficiency, and ultimately, delivering high-quality products to consumers.
Conclusion
Quality Control Inspectors and Quality Assurance professionals play distinct yet complementary roles in ensuring product quality.
Quality Control Inspectors focus on evaluating products through inspections and tests.
They detect defects and ensure products meet specific standards.
Their work is crucial for identifying immediate issues and preventing defective products from reaching customers.
Quality Assurance professionals, on the other hand, concentrate on improving processes and systems.
They design and implement procedures to ensure consistent product quality.
Their role involves developing quality management systems and auditing processes to prevent defects from occurring in the first place.
Both roles are essential for maintaining high standards and customer satisfaction.
Quality Control Inspectors provide the final check to catch defects before products are shipped.
Quality Assurance professionals create a framework to ensure products are consistently produced to meet quality standards.
The collaboration between these roles is vital for effective quality management.
Quality Control ensures that the end products are free from defects, while Quality Assurance works on systemic improvements to prevent defects from arising.
Together, they form a robust quality management system that enhances product reliability.
The importance of quality control and assurance cannot be overstated.
Quality Control Inspectors and Quality Assurance professionals safeguard the integrity of products.
Their efforts contribute significantly to customer satisfaction and trust in the brand.