Introduction
Quality control engineering is crucial in the tech industry.
It ensures that products meet high standards of reliability and performance.
As technology evolves rapidly, the role of quality control becomes increasingly complex and vital.
Quality control engineers develop and implement processes to detect defects early.
They use advanced tools and techniques to ensure products function as intended.
The importance of quality control in tech cannot be overstated.
It directly impacts product reliability and customer satisfaction.
High-quality products foster trust and loyalty among users.
Companies that consistently deliver reliable products gain a competitive edge.
They build strong reputations and reduce costs associated with returns and repairs.
Quality control engineers employ various strategies to maintain high standards.
They design rigorous testing protocols to assess product performance under different conditions.
Automation and machine learning are becoming integral to these processes.
These technologies allow for more precise and efficient testing.
The future of quality control engineering in tech will likely see increased integration of artificial intelligence.
AI can predict potential issues before they arise.
It helps in optimizing testing processes and improving accuracy.
This shift towards automation and data-driven decision-making will enhance product quality and reduce time-to-market.
Automation and Artificial Intelligence
How Automation and AI Are Reshaping Quality Control Processes
Automation and artificial intelligence (AI) are dramatically reshaping quality control processes in the tech industry.
These technologies streamline tasks, enhance accuracy, and boost efficiency.
By integrating automation, companies can perform repetitive quality control tasks more quickly and consistently.
AI-driven systems enable real-time monitoring of production lines, alerting operators to potential issues before they escalate.
This proactive approach helps maintain high standards and prevent costly recalls.
Automation also enhances data collection and analysis.
Robots generate detailed reports on production quality, providing valuable insights into trends and potential issues.
This data-driven approach supports continuous improvement and informed decision-making.
The integration of AI in quality control extends to predictive maintenance.
AI systems predict when equipment is likely to fail, allowing for timely maintenance and reducing unexpected breakdowns.
Use of Robotics and Machine Learning Algorithms for Defect Detection and Analysis
Robotics plays a crucial role in modern quality control.
Automated systems handle inspections, testing, and measurements with precision.
They reduce human error and increase throughput, allowing for more frequent and detailed inspections.
Robots equipped with advanced sensors and cameras inspect products with high accuracy.
They detect defects that might be missed by human inspectors, ensuring only high-quality products reach consumers.
Machine learning algorithms further transform quality control.
These algorithms analyze vast amounts of data to identify patterns and anomalies.
They continuously learn from new data, improving their ability to detect defects over time.
In defect detection, automation and AI excel.
Machine learning algorithms analyze defect data to understand root causes, refining manufacturing processes and improving product design.
The integration of AI in quality control enhances both defect detection and analysis.
The insights gained from AI-driven systems lead to fewer defects and better overall product quality.
Companies adopting these technologies benefit from reduced labor costs and increased productivity.
Automation and AI streamline operations, freeing up human resources for more complex tasks, allowing for a focus on innovation and strategic planning.
In summary, automation and AI are revolutionizing quality control engineering.
They offer significant improvements in accuracy, efficiency, and data analysis.
Embracing these technologies helps companies stay competitive and maintain high-quality standards in the tech industry.
Data Analytics
Leveraging Big Data and Analytics to Improve Quality Control Practices
In the realm of quality control engineering, data analytics is transforming practices.
Leveraging big data has become essential for enhancing quality control processes.
By analyzing vast datasets, engineers gain deeper insights into product performance and manufacturing efficiency.
Big data tools enable real-time monitoring of production lines.
This capability allows for immediate detection of anomalies and deviations from quality standards.
Engineers utilize advanced analytics to identify patterns that were previously invisible.
These patterns help in understanding the root causes of defects and inefficiencies.
Data analytics also improves the accuracy of quality control tests.
Traditional methods often rely on sampling, which might miss defects.
Advanced analytics can analyze 100% of production data, ensuring comprehensive quality assessment.
This approach increases the reliability of quality control and reduces the chances of defective products reaching consumers.
Integrating big data into quality control systems involves using various tools and technologies.
Machine learning algorithms, for example, can automate the detection of quality issues.
These algorithms learn from historical data and improve over time, becoming more effective at identifying defects.
Predictive Analytics for Identifying Potential Defects and Optimizing Production Processes
Predictive analytics plays a crucial role in anticipating potential issues before they arise.
By analyzing historical data, engineers predict which production processes are prone to defects.
This foresight allows for timely interventions, reducing the likelihood of defects in finished products.
Optimizing production processes is another benefit of predictive analytics.
Engineers can adjust parameters in real time based on predictive models.
This proactive approach minimizes waste and improves overall product quality.
By implementing these data-driven strategies, companies can enhance their competitive edge in the market.
Predictive analytics supports root cause analysis efficiently.
By leveraging big data, engineers trace defects to their origins faster.
This rapid identification of issues allows for quicker resolutions and process improvements.
Furthermore, big data analytics supports continuous improvement initiatives.
By constantly analyzing production data, engineers identify areas for enhancement.
This ongoing process helps companies adapt to changing market demands and maintain high-quality standards.
Most importantly, data analytics is reshaping the future of quality control engineering.
Leveraging big data and predictive analytics significantly improves quality control practices.
These advancements lead to better defect detection, optimized production processes, and enhanced overall product quality.
As technology continues to evolve, data analytics will remain a cornerstone in achieving excellence in quality control.
Virtual Reality and Augmented Reality
Integration of VR and AR Technologies in Quality Control Inspections
Virtual Reality (VR) and Augmented Reality (AR) are transforming quality control engineering with their advanced capabilities.
Their integration into quality control inspections offers groundbreaking improvements in precision and efficiency.
VR creates immersive digital environments where engineers can interact with 3D models of products.
This simulation allows them to detect potential flaws and issues before actual production begins.
By visualizing products in a virtual space, engineers can identify defects early, thereby reducing errors in the manufacturing process and saving valuable time and resources.
AR, on the other hand, overlays digital information onto the physical world.
During inspections, engineers wearing AR glasses can see real-time data about the product.
This includes crucial metrics such as dimensions, tolerances, and other quality indicators, all superimposed directly on the object being examined.
This integration provides a detailed view that helps in identifying deviations from quality standards more efficiently.
Engineers can quickly spot issues that might not be visible through traditional inspection methods, leading to more accurate assessments and higher-quality outcomes.
The application of VR in quality control extends beyond just inspections.
It also plays a significant role in training and simulation.
Engineers can use VR environments to practice inspection techniques and familiarize themselves with complex components or assemblies.
This virtual training enhances their skills and prepares them for real-world scenarios, ultimately improving their ability to maintain high quality standards.
AR facilitates real-time interaction with the physical product.
This technology allows for dynamic adjustments and immediate feedback during inspections.
Engineers can make instant decisions based on the augmented data, which speeds up the inspection process and enhances overall efficiency.
Enhancing Visualization and Remote Monitoring Capabilities for Better Quality Assurance
The visualization capabilities provided by VR and AR are crucial for enhancing quality control processes.
VR offers an immersive experience that helps engineers understand the full context of how a product will function.
By simulating various conditions and scenarios, VR allows for a thorough analysis of the product’s performance.
This capability is particularly valuable for complex or intricate components, where traditional inspection methods might fall short.
AR enhances remote monitoring by enabling experts to provide guidance from different locations.
Using AR devices, on-site engineers can stream live feeds of the inspection process to remote experts.
These experts can then offer real-time feedback, instructions, and support.
This remote collaboration bridges geographical gaps and ensures that specialized knowledge is accessible whenever needed.
It enhances the inspection process by bringing in expert insights without the need for physical presence.
Both VR and AR technologies contribute to a better understanding of the product’s quality and performance.
By providing detailed visualizations and interactive elements, these technologies help in identifying and addressing issues more effectively.
Engineers can make more informed decisions, leading to improved quality assurance and more reliable products.
As VR and AR continue to advance, their role in quality control engineering will become even more significant.
These technologies promise to make quality assurance processes more efficient, accurate, and adaptable.
The integration of VR and AR into quality control workflows represents a significant leap forward in ensuring high standards and achieving excellence in the tech industry.
Read: Environmental Engineering Software and Tools
Internet of Things (IoT)
Utilizing IoT Devices for Real-Time Monitoring of Machine Performance
The Internet of Things (IoT) is revolutionizing quality control engineering.
IoT devices enable real-time monitoring of machine performance.
These smart devices continuously collect and transmit data.
This data provides engineers with instant insights into machinery operations.
With real-time monitoring, engineers can track performance metrics as they occur.
They observe variables such as temperature, vibration, and pressure.
Immediate data analysis allows for quick decision-making and problem resolution.
This capability enhances the overall efficiency and reliability of production processes.
Implementation of Sensors and Connected Devices for Proactive Quality Control Measures
IoT-enabled sensors are critical for proactive quality control.
Sensors are installed on machinery to monitor various operational parameters.
By providing continuous data, these sensors help engineers identify anomalies before they escalate.
The implementation of connected devices enables proactive quality control measures.
Engineers use data from these devices to anticipate and prevent potential issues.
This predictive approach minimizes downtime and reduces maintenance costs.
Engineers can address problems early, ensuring consistent product quality and reducing the risk of defects.
Connected devices also support advanced analytics and automated alerts.
When sensors detect deviations, they trigger alerts to notify engineers.
This rapid response capability allows for swift intervention, maintaining high production standards and operational efficiency.
The integration of IoT in quality control enhances precision.
Detailed insights into every aspect of the manufacturing process allow for process optimization.
Engineers can fine-tune operations based on accurate, real-time data, improving both product quality and production consistency.
Despite the advantages, IoT in quality control presents challenges.
Security concerns with increased connectivity must be addressed.
Protecting data integrity and safeguarding against cyber threats are essential for effective IoT implementation.
In summary, IoT devices offer significant benefits for quality control engineering.
Real-time monitoring of machine performance and proactive measures through sensors and connected devices lead to more efficient and reliable operations.
As IoT technology advances, its role in shaping the future of quality control engineering will become increasingly vital.
Read: Environmental Engineers in the Mining Industry
Quality Control in Agile Development
Adapting Quality Control Processes to Agile Methodologies
Agile methodologies have transformed the way tech companies develop software.
Adapting quality control processes to fit agile practices is crucial for success.
Traditional quality control methods often clash with the fast-paced nature of agile development.
Therefore, quality control teams must adjust their strategies to maintain high standards.
In agile development, quality control must be integrated into daily workflows.
This requires shifting from end-of-cycle testing to ongoing evaluation.
Agile teams need to implement practices that support continuous improvement and rapid feedback.
Teams should focus on maintaining quality throughout the entire development process rather than just at the end.
Incorporating Continuous Testing and Feedback Loops for Faster Product Iteration
Continuous testing is a key practice in agile development.
This approach involves frequent testing throughout the development cycle, not just at the end.
By integrating testing into daily routines, teams can catch issues early. Early detection of problems reduces the risk of costly fixes later.
Continuous testing helps ensure that each iteration meets quality standards.
Feedback loops are another essential component in agile quality control.
These loops involve regularly gathering feedback from stakeholders and end-users.
Quick feedback allows teams to make necessary adjustments promptly.
This process supports the agile principle of responding to change over following a rigid plan.
With feedback integrated into each development cycle, products evolve based on real user needs.
Automated testing tools play a significant role in agile environments.
They enable rapid and consistent testing across different iterations.
Automation speeds up the testing process and reduces human error.
It also frees up quality control engineers to focus on more complex tasks that require human insight.
Another benefit of agile quality control is the close collaboration between developers and testers.
Optimizing Quality Control in Agile Development
Agile encourages cross-functional teams where quality control is a shared responsibility.
This collaboration fosters a culture of quality from the beginning of the development cycle.
Developers and testers working together can address issues more effectively.
Implementing agile quality control processes involves several steps.
Teams should start by integrating testing into the daily development routine.
Establishing clear protocols for feedback and iteration helps maintain focus.
Automated tools should be chosen based on the specific needs of the project.
Additionally, training team members in agile practices ensures everyone is aligned with the new processes.
Effective quality control in agile development requires flexibility and commitment.
Teams must be willing to adapt and refine their processes as needed.
Embracing these changes leads to more efficient product development cycles.
By continuously improving quality control practices, teams can deliver better products more rapidly.
Basically, adapting quality control processes to agile methodologies is essential for tech companies.
Continuous testing and feedback loops are crucial for faster product iteration.
Embracing automation and fostering collaboration further enhance quality control.
As agile development continues to evolve, so must the strategies for ensuring product quality.
Transform Your Career Today
Unlock a personalized career strategy that drives real results. Get tailored advice and a roadmap designed just for you.
Start NowRead: Tips for Writing Environmental Engineering Reports
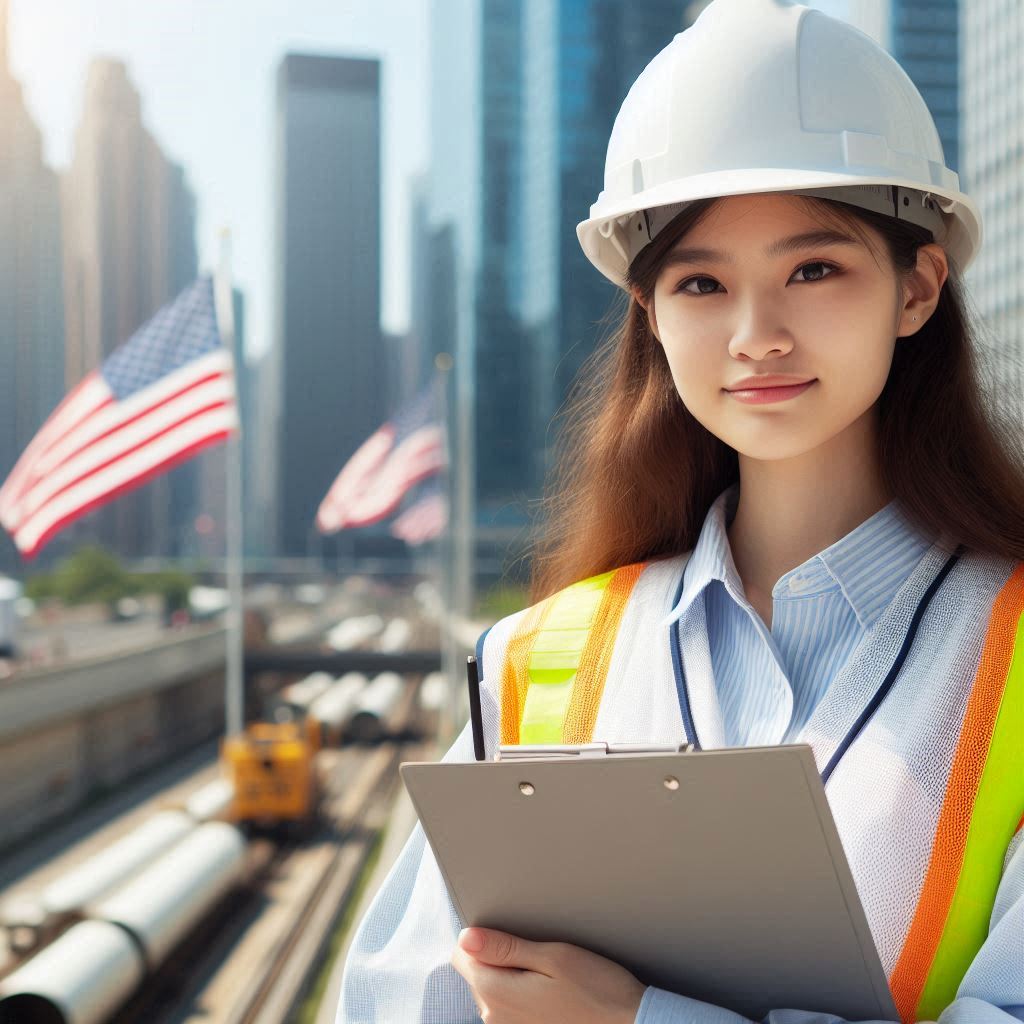
Cybersecurity in Quality Control
Addressing Security Concerns in Quality Control Systems
In the realm of quality control, cybersecurity has become a critical concern.
As technology evolves, quality control systems increasingly rely on digital tools and data.
This advancement introduces significant cybersecurity risks that must be addressed to ensure system integrity.
Quality control systems handle sensitive data, including product specifications, test results, and production metrics.
Unauthorized access to this data can severely impact product quality and lead to intellectual property theft.
Therefore, securing these systems is paramount.
Robust security measures are essential for protecting data integrity and preventing tampering.
Encryption plays a crucial role in safeguarding data during both transmission and storage.
Encrypted data is harder for unauthorized users to access and manipulate.
Access control measures are also critical.
Restricting access to authorized personnel only reduces the risk of internal breaches.
Implementing strong authentication methods, such as multi-factor authentication, enhances access security.
Regular software updates and patch management are vital for addressing vulnerabilities.
Outdated software can be exploited by cyber attackers to gain unauthorized access.
Keeping software current ensures that known security issues are resolved promptly.
Monitoring and auditing systems for suspicious activity are essential for early detection of potential threats.
Automated monitoring tools can alert administrators to unusual behavior, enabling a swift response to potential security incidents.
Importance of Data Protection and Secure Communication in Maintaining Quality Standards
Secure communication protocols are crucial for protecting data integrity in quality control systems.
They ensure that data exchanges between quality control systems and networked components remain confidential and unaltered.
Secure communication channels help prevent data breaches and unauthorized modifications.
Data protection is vital for maintaining quality standards.
With sensitive data involved in quality control, ensuring its security helps preserve the accuracy and reliability of quality assessments.
Effective data protection strategies mitigate risks associated with data breaches and unauthorized access.
Data backup and recovery plans are essential for maintaining system resilience.
In the event of a cyberattack or data loss, a comprehensive backup strategy ensures that quality control data can be restored quickly.
Regular testing of backup systems confirms their effectiveness.
Training and awareness programs for staff are also important.
Educating employees about cybersecurity best practices helps them recognize potential threats and avoid risky behaviors.
Well-informed staff are less likely to fall victim to phishing attacks or other social engineering tactics.
In summary, addressing cybersecurity in quality control systems is crucial for maintaining product quality and protecting sensitive data.
Implementing strong security measures, secure communication protocols, and effective data protection strategies ensures that quality standards are upheld.
By prioritizing cybersecurity, organizations can safeguard their quality control systems against potential threats.
Read: Sustainable Wastewater Treatment Methods
Explore Further: Top Skills Needed for Automotive Engineers Today
Skills and Training for Quality Control Engineers
Importance of Continuous Learning and Skill Development in Quality Control Engineering
In quality control engineering, continuous learning and skill development are essential for staying relevant.
Technology and methodologies evolve rapidly, presenting new challenges.
Engineers must keep their skills up-to-date to address these challenges effectively.
Ongoing education ensures engineers remain proficient in the latest techniques and tools.
This proactive approach helps engineers tackle advanced quality control issues and apply the best practices in their work.
Training Programs and Certifications for Staying Updated with Industry Trends and Technologies
Training programs offer structured learning opportunities crucial for skill enhancement.
These programs cover advanced statistical methods, new quality control technologies, and industry best practices.
Participating in such programs helps engineers stay current with technological advancements and regulatory changes.
Certifications also play a significant role in maintaining expertise.
Many professional organizations offer certifications that validate an engineer‘s skills and knowledge.
These certifications often involve rigorous exams and practical demonstrations of proficiency in quality control areas.
They act as benchmarks for competence and commitment to the field.
Specialized training in emerging technologies is increasingly important.
Areas such as artificial intelligence, machine learning, and data analytics are becoming integral to quality control.
Training in these fields provides valuable insights and tools for enhancing quality management processes.
Attending industry conferences and workshops can further benefit engineers.
These events offer opportunities to learn from experts and network with peers.
Engineers gain insights into the latest trends and share experiences, fostering a deeper understanding of industry advancements and challenges.
On-the-job training complements formal education.
Practical experience allows engineers to apply theoretical knowledge to real-world scenarios.
This hands-on approach develops problem-solving skills and helps engineers adapt to new technologies.
It also enhances their ability to respond effectively to quality issues.
In summary, continuous learning and skill development are crucial in quality control engineering.
Engaging in training programs, obtaining certifications, and staying updated with industry trends are essential for career advancement.
Embracing these opportunities ensures engineers can meet evolving quality standards and contribute effectively to their organizations.
Conclusion
As we look ahead to the future of quality control engineering in tech, several key points stand out.
The integration of artificial intelligence and machine learning will revolutionize quality assurance processes, making them more efficient and effective.
Additionally, the importance of data analytics and continuous monitoring cannot be overstated.
These tools will enable companies to identify issues early on and proactively address them, ultimately improving product quality and customer satisfaction.
Furthermore, the emphasis on automation and DevOps practices will streamline testing procedures and shorten the time to market for new products and updates.
This agility is crucial in a fast-paced industry where innovation is key to staying ahead of the competition.
Overall, the future of quality control engineering in tech will be shaped by innovation and adaptability.
Companies that embrace new technologies and methodologies will be best positioned to drive quality assurance processes forward and deliver exceptional products to their customers.