Introduction
Preventive maintenance involves regularly scheduled inspections and repairs to prevent equipment failures.
It aims to identify and fix issues before they escalate into major problems.
In the industry, preventive maintenance is crucial for several reasons:
- Reduces Downtime: By preventing unexpected breakdowns, companies can maintain continuous production, minimizing costly downtime.
- Extends Equipment Life: Regular maintenance keeps machinery in optimal condition, prolonging its lifespan and reducing the need for replacements.
- Enhances Safety: Well-maintained equipment operates more safely, reducing the risk of accidents and injuries.
- Improves Efficiency: Properly functioning machines use less energy and resources, contributing to overall operational efficiency.
Preventive maintenance also provides cost savings by reducing the need for emergency repairs and replacements.
It allows companies to plan for maintenance during non-peak hours, minimizing disruption to production.
In the long run, preventive maintenance helps maintain the integrity and reliability of industrial equipment, ensuring smooth and efficient operations.
For these reasons, it is a vital component of any industrial maintenance strategy.
Cost-Saving Benefits of Preventive Maintenance
In the industrial sector, implementing preventive maintenance programs can lead to significant cost savings in the long run.
By regularly inspecting and servicing equipment and machinery, potential issues can be identified and addressed before they escalate into costly repairs.
Identifying and addressing issues early
- Regular maintenance helps in identifying small issues before they turn into major problems.
- Addressing issues early can prevent equipment breakdowns and production delays.
- This proactive approach reduces the need for expensive emergency repairs.
- Regular maintenance also extends the lifespan of equipment, reducing the frequency of replacements.
For example, a manufacturing plant that conducts regular inspections on its machinery can detect worn-out parts before they fail, thus avoiding costly downtime and production losses.
By replacing these parts proactively, the plant can maintain optimal operations and avoid more expensive repairs in the future.
Examples of industries saving money through preventive maintenance
- The aviation industry conducts routine checks on aircraft to ensure safety and efficiency.
- Oil and gas companies regularly maintain drilling equipment to prevent costly breakdowns.
- Hospitals invest in preventive maintenance for medical equipment to ensure patient safety.
- Railway companies implement maintenance schedules to keep trains running smoothly.
These industries have seen significant cost savings by implementing preventive maintenance programs.
By investing in regular inspections and servicing, they have managed to avoid unexpected breakdowns, reduce repair costs, and prolong the lifespan of their equipment.
In summary, preventive maintenance plays a crucial role in the industrial sector by not only ensuring the smooth operation of equipment but also by helping companies save money in the long term.
By addressing issues early and maintaining equipment properly, businesses can avoid costly repairs and production losses, ultimately improving their bottom line.
Read: Online Courses for Surveying and Mapping Technicians
Increased Equipment Longevity
How regular maintenance can extend the lifespan of industrial equipment
Regular maintenance is crucial for extending the lifespan of industrial equipment.
By performing routine checks, mechanics identify potential issues before they become significant problems.
This proactive approach ensures that machines continue to operate at their best, avoiding unnecessary strain and wear.
Preventive maintenance involves a series of actions that help equipment function optimally:
- Lubricating moving parts to reduce friction and prevent excessive wear.
- Cleaning components to avoid the buildup of dust, grime, or debris that can cause overheating or corrosion.
- Inspecting electrical systems for signs of wear, loose connections, or damaged wires that could lead to malfunctions.
- Replacing worn-out parts before they fail, preventing unexpected breakdowns.
The impact of preventive maintenance on reducing the need for frequent replacements
These tasks may seem minor but have a massive impact over time
When each component of a machine is maintained properly, the overall equipment works more efficiently and lasts longer.
Instead of reacting to problems, companies can take charge of their machinery’s health.
Preventive maintenance also significantly reduces the need for frequent replacements.
Transform Your Career Today
Unlock a personalized career strategy that drives real results. Get tailored advice and a roadmap designed just for you.
Start NowEquipment that undergoes regular checks is less likely to suffer from catastrophic failures.
Fewer breakdowns mean less wear on parts and less strain on the entire system, resulting in extended lifespans.
Furthermore, industrial machines that are well-maintained have lower operating costs.
They consume less energy and require fewer repairs.
This efficiency not only reduces expenses but also minimizes downtime, allowing companies to maximize productivity.
Preventive maintenance also provides a better return on investment.
The initial cost of implementing a regular maintenance schedule is far lower than the expense of frequent replacements.
Companies save money by avoiding the high costs of purchasing new equipment and dealing with the associated logistics.
To summarize, regular maintenance plays a vital role in increasing equipment longevity and reducing the need for replacements.
Companies that prioritize preventive maintenance see a direct impact on their bottom line, benefiting from longer-lasting equipment, reduced costs, and greater operational efficiency.
Taking care of machinery today prevents costly replacements tomorrow, making preventive maintenance a smart business strategy.
Read: Surveying and Mapping Technician: Job Satisfaction
Improved Efficiency and Productivity
How well-maintained equipment operates more efficiently
In any industry, the efficiency of equipment is crucial to operational success.
Well-maintained equipment consistently operates at its peak performance.
Preventive maintenance ensures that machinery runs smoothly, minimizing disruptions caused by unexpected failures.
When equipment is regularly inspected and serviced, it maintains its optimal condition, which translates to better performance.
Well-maintained machines are less likely to experience performance issues that could hinder productivity.
For instance, a regularly cleaned and lubricated engine will run more efficiently than one that has not been serviced.
This efficiency leads to reduced energy consumption, as machines operate without unnecessary strain or friction.
Consequently, operational costs decrease, and output quality improves.
By keeping equipment in top shape, industries can avoid the inefficiencies associated with breakdowns and repairs.
Equipment that is prone to frequent malfunctions will inevitably slow down production processes.
On the other hand, well-maintained machinery consistently delivers high performance, ensuring that production goals are met more effectively.
This efficiency contributes to an overall smoother workflow and better product quality.
The role of preventive maintenance in reducing downtime and increasing overall productivity in the industry
Preventive maintenance plays a pivotal role in minimizing downtime, a critical factor in maintaining high productivity levels.
Downtime can be costly, resulting in halted production lines and missed deadlines.
Regular maintenance helps to identify potential issues before they lead to major failures.
By scheduling routine inspections and servicing, industries can address minor problems before they escalate.
This proactive approach prevents unexpected equipment failures that could disrupt operations.
For example, replacing worn-out parts during scheduled maintenance can prevent a sudden breakdown.
As a result, production processes remain uninterrupted, and downtime is significantly reduced.
Increased overall productivity is another major benefit of preventive maintenance.
When equipment is in good working condition, it operates efficiently, producing more output in less time.
This increased efficiency leads to faster production cycles and higher output volumes.
As a result, industries can meet higher demand without the need for additional resources.
Additionally, preventive maintenance extends the lifespan of equipment.
Longer-lasting machinery reduces the need for frequent replacements, which can be expensive.
With well-maintained equipment, industries can avoid the disruptions associated with purchasing and installing new machines.
This stability supports sustained productivity and operational efficiency.
Overall, preventive maintenance is essential for reducing downtime and boosting productivity.
By ensuring that equipment is consistently in optimal condition, industries can maintain smooth operations and achieve higher levels of efficiency.
This approach not only saves costs but also enhances the overall effectiveness of production processes.
Read: CAD Technician vs. Draftsman: Key Differences
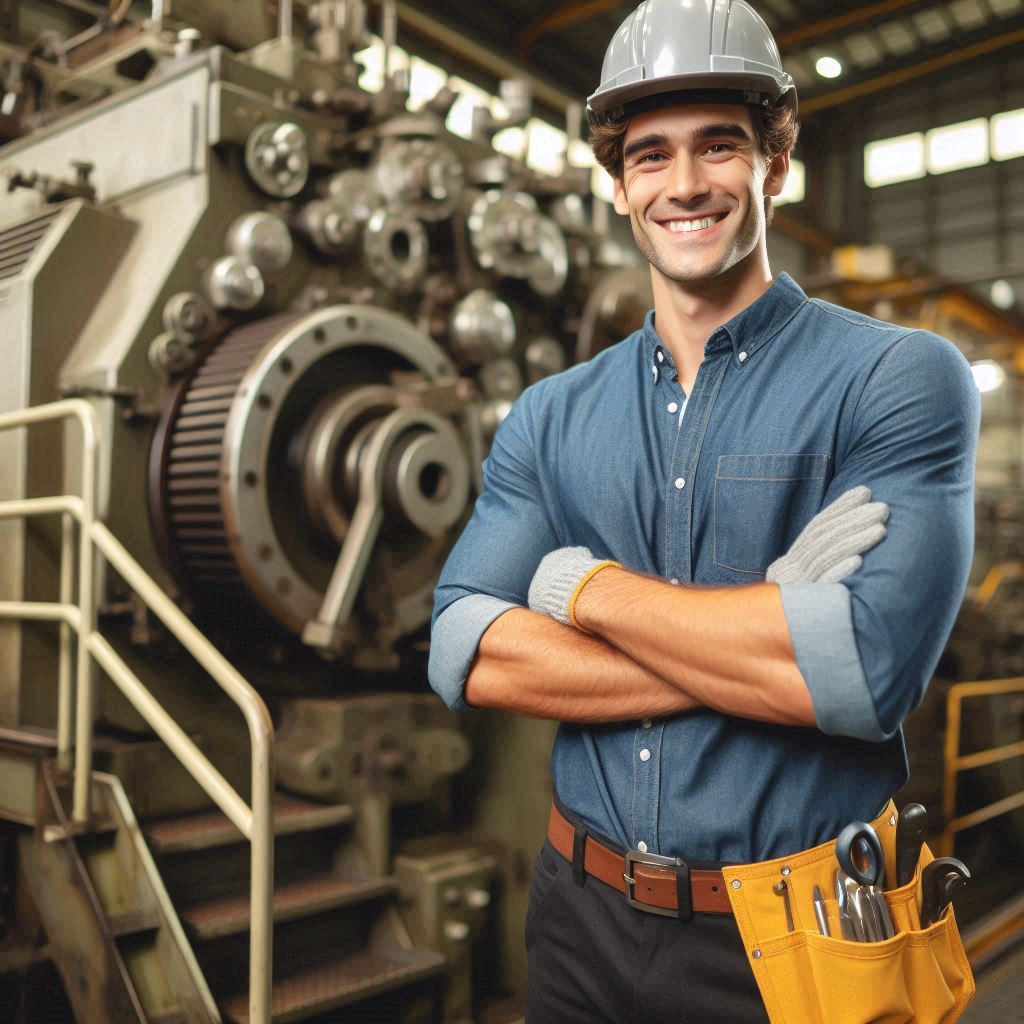
Enhanced Safety Measures
Preventive maintenance can help identify safety hazards before they escalate
Preventive maintenance plays a crucial role in enhancing safety measures within industrial settings.
By proactively identifying potential safety hazards and addressing them before they escalate, organizations can create a secure work environment for their employees.
Here, we delve into the importance of maintaining a safe working environment through regular equipment inspections and maintenance.
One of the primary benefits of preventive maintenance is its ability to identify safety hazards before they cause harm.
By conducting routine inspections and addressing any issues promptly, organizations can prevent accidents and injuries from occurring in the workplace.
This proactive approach not only safeguards employees but also protects the company from potential liabilities associated with workplace accidents.
Regular equipment inspections allow maintenance teams to detect wear and tear, faulty components, or other issues that could compromise safety.
By assessing the condition of machinery and ensuring that it meets safety standards, organizations can minimize the risk of equipment malfunctions leading to accidents.
Additionally, preventive maintenance helps extend the lifespan of equipment, reducing the likelihood of sudden breakdowns that could pose safety risks.
Creating a culture of safety within the workplace is essential for fostering a positive and productive environment.
Regular maintenance demonstrates a commitment to prioritizing employee safety, which can boost morale and job satisfaction.
Employees are more likely to feel valued and supported when they see that their well-being is a top priority for the organization.
This, in turn, can lead to improved performance, reduced absenteeism, and higher employee retention rates.
Maintenance ensures safe working conditions by inspecting equipment regularly
Moreover, maintaining a safe working environment through preventive maintenance can also enhance operational efficiency.
When equipment is kept in optimal condition, it performs better and experiences fewer disruptions, resulting in increased productivity and reduced downtime.
By minimizing the occurrence of unplanned breakdowns and repairs, organizations can streamline their operations and meet production targets more consistently.
In a nutshell, the importance of preventive maintenance in enhancing safety measures in the industry cannot be overstated.
By identifying and addressing potential safety hazards through regular equipment inspections and maintenance, organizations can create a secure work environment, protect employees from harm, and optimize operational efficiency.
Prioritizing safety through preventive maintenance not only benefits employees and the company but also contributes to overall success and sustainability in the long run.
Read: Essential Skills for CAD Technicians
Compliance with Regulations
Adhering to Preventive Maintenance Schedules
Preventive maintenance plays a crucial role in ensuring compliance with industry regulations.
Many industries, such as manufacturing and healthcare, are governed by strict regulations aimed at ensuring safety, reliability, and environmental protection.
By adhering to preventive maintenance schedules, companies can demonstrate their commitment to these standards.
Regular maintenance helps ensure that equipment and systems operate within the prescribed limits set by regulatory bodies.
This proactive approach minimizes the risk of equipment failure, which could otherwise lead to unsafe working conditions or environmental hazards.
In addition, routine inspections and maintenance activities often serve as documentation that proves compliance during regulatory audits.
Therefore, following a well-structured preventive maintenance plan not only supports operational efficiency but also reinforces a company’s adherence to essential regulations.
Consequences of Failing to Meet Maintenance Requirements
Failing to meet maintenance requirements set by regulatory bodies can have severe consequences for a business.
Regulatory agencies impose maintenance standards to safeguard public health, safety, and environmental quality.
Non-compliance can result in hefty fines and legal penalties, which can significantly impact a company‘s financial stability.
In severe cases, regulatory bodies may issue cease-and-desist orders, halting operations until compliance is achieved.
This disruption can lead to loss of revenue, damage to the company‘s reputation, and potential legal battles.
Additionally, equipment failures due to inadequate maintenance can result in accidents or environmental spills, further exacerbating the situation.
Such incidents can cause harm to employees, damage to the environment, and lead to increased scrutiny from regulators.
Therefore, it is imperative for companies to adhere to maintenance requirements to avoid these adverse consequences and ensure smooth, uninterrupted operations.
Transform Your Career Today
Unlock a personalized career strategy that drives real results. Get tailored advice and a roadmap designed just for you.
Start NowExplore Further: Future of Robotics: Predictions from Industry Experts
Minimizing Disruptions to Production
The impact of equipment breakdowns on production schedules
Equipment breakdowns can severely disrupt production schedules.
Unexpected failures halt operations, leading to costly downtime.
Each minute of unplanned downtime impacts productivity and delays product delivery.
Businesses face financial losses due to halted machinery and idle labor.
Equipment failures also strain resources as maintenance teams scramble to fix issues.
The ripple effect extends to supply chains, affecting customer satisfaction and market competitiveness.
Frequent breakdowns disrupt workflows, reduce efficiency, and can damage a company’s reputation.
Consequently, addressing these breakdowns promptly becomes essential to maintaining steady operations.
How preventive maintenance helps minimize disruptions and keeps the production process running smoothly
Preventive maintenance is key to minimizing disruptions.
By regularly servicing equipment, companies can identify potential issues before they cause failures.
Scheduled inspections and maintenance tasks help prevent unexpected breakdowns, ensuring that machinery operates efficiently.
This approach allows for timely repairs, reducing the likelihood of unplanned downtimes.
Moreover, preventive maintenance extends the lifespan of equipment, which helps in avoiding sudden malfunctions.
Routine checks and part replacements keep production running smoothly, avoiding costly interruptions.
Overall, preventive maintenance maintains steady workflows and enhances operational reliability.
Implementing a preventive maintenance strategy helps sustain productivity and keep operations on track.
Skilled Workforce Development
Implementing preventive maintenance programs in industries can significantly contribute to the development of a skilled workforce.
Here’s how:
Training Opportunities
Regular maintenance of industrial equipment provides ample training opportunities for employees.
Through hands-on experience in maintaining and servicing machinery, workers can enhance their technical skills and knowledge.
This practical training enables them to troubleshoot issues effectively and perform repairs efficiently.
Skill Development
Engaging in preventive maintenance tasks exposes workers to a variety of tools and techniques used in the industry.
This exposure helps them develop a diverse set of skills that are essential for equipment maintenance.
From understanding machinery schematics to performing diagnostic tests, employees can expand their skill set through continuous maintenance work.
Problem-Solving Abilities
Regular maintenance activities involve identifying and resolving equipment issues before they escalate into major problems.
This process hones employees’ problem-solving abilities as they learn to diagnose issues, develop solutions, and implement corrective measures.
Over time, workers become adept at analyzing complex problems and finding practical solutions, thereby enhancing their problem-solving skills.
Team Collaboration
Implementing preventive maintenance programs encourages teamwork among employees.
Working together to schedule maintenance tasks, allocate resources, and execute maintenance activities fosters collaboration and communication within the workforce.
This collaborative environment promotes information sharing, collective problem-solving, and mutual support among team members, leading to a cohesive and efficient workforce.
Increased Efficiency
Regular maintenance of industrial equipment improves operational efficiencies and reduces downtime.
When employees are involved in maintaining equipment, they gain a deeper understanding of machinery functionality and performance.
This knowledge enables them to optimize equipment operation, identify potential efficiency improvements, and implement preventive measures to enhance productivity.
As a result, employees become more efficient in managing equipment and handling maintenance tasks, contributing to overall operational efficiency.
Career Advancement
Engaging in preventive maintenance activities equips employees with valuable skills and expertise that can lead to career advancement opportunities.
As workers develop proficiency in equipment maintenance, they become eligible for specialized roles in maintenance, repair, or even leadership positions within the organization.
This career growth not only rewards employees for their dedication to maintenance work but also motivates them to continuously enhance their skills and expand their knowledge in the field.
In review, implementing preventive maintenance programs in industries not only ensures the longevity and efficiency of equipment but also plays a crucial role in workforce development.
By providing training opportunities, fostering skill development, enhancing problem-solving abilities, promoting team collaboration, improving efficiency,
and offering career advancement prospects, preventive maintenance programs contribute to building a skilled and competent workforce capable of meeting the challenges of the industry.
Uncover the Details: Petroleum Engineer vs. Petroleum Geologist
Conclusion
In the industrial sector, preventive maintenance plays a crucial role in ensuring smooth operations.
By conducting regular inspections and servicing of equipment, companies can avoid unexpected breakdowns and costly repairs.
Proactive maintenance schedules help in detecting potential issues before they escalate into major problems.
This not only reduces downtime but also increases productivity and efficiency in the long run.
Timely replacement of worn-out parts and lubrication of machinery can enhance their lifespan and performance.
This proactive approach ultimately leads to significant cost savings for the company.
Moreover, preventive maintenance improves workplace safety by identifying and rectifying hazardous conditions.
This ensures a secure working environment for employees and minimizes the risk of accidents.
Routine maintenance also contributes to energy conservation and environmental sustainability.
Well-maintained equipment operates more efficiently, consuming less energy and reducing carbon emissions.
In closing, preventive maintenance is a cornerstone of sustainable growth and efficiency in the industry.
By prioritizing proactive maintenance strategies, companies can optimize their operations, reduce costs, ensure safety, and contribute to environmental protection.
Embracing preventive maintenance as a core principle is essential for long-term success and competitiveness in today’s rapidly evolving industrial landscape.
[E-Books for Sale]
The Big Book of 500 High-Paying Jobs in America: Unlock Your Earning Potential
$19.99 • 500 High-Paying Jobs • 330 pages
Explore 500 high-paying jobs in America and learn how to boost your career, earn more, and achieve success!
See All 500 High-Paying Jobs of this E-Book
1001 Professions Without a Degree: High-Paying American Jobs You Can Start Now
$19.99 • 1001 Professions Without a Degree • 174 pages
Discover 1001 high-paying jobs without a degree! Unlock career tips, skills, and success strategies for just $19.99!