Introduction
Nanotechnology involves manipulating materials at the nanoscale, typically between 1 and 100 nanometers.
This innovative field plays a vital role in various sectors, including medicine, electronics, energy, and environmental science.
By designing and creating nanomaterials, nanotechnologists enable advancements that enhance product performance and efficiency.
These materials exhibit unique properties, allowing for innovations that can significantly improve existing technologies and create new applications.
Nanotechnologists focus on developing materials with enhanced characteristics, such as increased strength, improved conductivity, and enhanced reactivity.
For instance, in medicine, they work on targeted drug delivery systems that release medication precisely where needed, minimizing side effects.
In electronics, nanotechnology leads to smaller and faster devices with greater energy efficiency.
Additionally, in energy, nanomaterials can improve solar cell performance and create more efficient batteries.
However, the unique properties of nanomaterials can also pose safety risks.
Their small size and large surface area can lead to different behaviors and interactions compared to bulk materials.
As a result, they may present potential hazards to human health and the environment.
Therefore, adherence to safety practices in the nanotechnology industry is crucial.
Importance of Safety in Nanotechnology
The Potential Risks Associated with Working with Nanoparticles
Nanoparticles, while beneficial for various applications, pose potential risks to human health and the environment.
Their small size allows them to easily penetrate biological membranes, leading to unintended exposure.
Research shows that certain nanoparticles can cause respiratory and cardiovascular issues when inhaled.
Additionally, some nanoparticles may have toxic effects on cells and tissues.
These risks necessitate careful handling and awareness of the materials used in nanotechnology.
The unique properties of nanoparticles can also lead to unexpected interactions with biological systems.
For instance, engineered nanoparticles may trigger inflammatory responses in living organisms.
Understanding these potential risks is crucial for ensuring worker safety and minimizing health hazards.
Importance of Protecting Both Workers and the Environment from Exposure
Protecting workers from exposure to nanoparticles is essential in nanotechnology workplaces.
Organizations must implement comprehensive safety protocols to minimize the risk of inhalation or skin contact.
Personal protective equipment (PPE) plays a vital role in safeguarding workers from potential exposure.
This includes gloves, masks, and protective clothing designed to prevent nanoparticle penetration.
In addition to protecting workers, safeguarding the environment is equally important.
Nanoparticles can enter ecosystems through improper disposal or accidental release.
They may accumulate in soil and water, posing risks to wildlife and human health.
Therefore, proper waste management and disposal practices are critical in nanotechnology settings.
Employers must prioritize training programs to educate workers about potential risks associated with nanoparticles.
Workers should understand the importance of following safety protocols and using PPE consistently.
Regular training ensures that employees stay informed about the latest safety practices and research findings.
The Need for Strict Safety Measures to Prevent Accidents and Health Hazards
Implementing strict safety measures is vital for preventing accidents and health hazards in nanotechnology laboratories.
Organizations should establish comprehensive safety guidelines that address specific risks associated with nanoparticle handling.
These guidelines must include procedures for safe storage, transportation, and disposal of nanomaterials.
Ventilation systems in laboratories should be equipped to filter out nanoparticles effectively.
Fume hoods and dust containment systems can help reduce exposure during experiments.
Organizations should regularly inspect and maintain these systems to ensure optimal performance.
Additionally, conducting risk assessments before starting new projects is essential.
Assessing potential hazards associated with specific nanoparticles allows organizations to develop targeted safety measures.
This proactive approach helps prevent accidents and promotes a culture of safety within the workplace.
Regular monitoring of nanoparticle exposure levels is also necessary.
Employers should implement air quality assessments to ensure that nanoparticle concentrations remain below acceptable limits.
Monitoring helps identify potential issues early and enables timely interventions to protect worker health.
Personal Protective Equipment (PPE)
Essential PPE Required for Nanotechnologists
Nanotechnologists must wear specific PPE to protect themselves from exposure to nanoparticles.
Essential items include lab coats, gloves, and respirators. Each piece of equipment plays a vital role in minimizing exposure and maintaining safety.
Lab Coats
A lab coat provides a barrier between the skin and hazardous materials.
It protects against spills and contamination.
Nanotechnologists should wear lab coats made from tightly woven fabric.
This fabric helps prevent nanoparticles from penetrating through to the skin.
Gloves
Gloves are crucial for protecting hands from direct contact with nanoparticles.
Nitrile gloves are often preferred because they resist punctures and chemical exposure.
Nanotechnologists should change gloves regularly to maintain protection.
Wearing gloves also prevents contamination of samples and equipment.
Respirators
Respirators guard against inhalation of airborne nanoparticles.
They filter out harmful particles, ensuring that nanotechnologists breathe clean air.
It is essential to select the right type of respirator, such as N95 or P100, depending on the level of exposure risk.
Proper fit testing is crucial to ensure maximum protection.
Function of Each Piece of Equipment in Preventing Exposure to Nanoparticles
Each piece of PPE serves a specific function in preventing exposure to nanoparticles.
Lab coats shield skin and clothing from spills and dust, reducing the risk of contamination.
Gloves create a physical barrier against harmful substances, minimizing the chances of dermal exposure.
Respirators protect the respiratory system by filtering out harmful particles from the air.
Together, these items create a comprehensive safety approach for nanotechnologists.
Tips on Proper Handling, Maintenance, and Disposal of PPE
Proper handling and maintenance of PPE are vital for effective protection.
Here are some essential tips
- Inspect PPE Regularly: Always check for signs of damage or wear before use.
Replace any damaged or worn-out PPE immediately. - Clean and Maintain Equipment: Clean lab coats and gloves according to manufacturer instructions.
Proper maintenance extends the life of the equipment and ensures safety. - Proper Storage: Store PPE in a clean, dry area away from contaminants.
This practice helps maintain the integrity of the equipment. - Dispose of PPE Properly: Follow institutional guidelines for disposing of contaminated PPE.
Place used gloves and lab coats in designated waste bins to prevent cross-contamination. - Training and Awareness: Ensure that all personnel receive proper training on using PPE. Regular training updates help maintain safety standards and awareness.
In general, nanotechnologists must prioritize safety practices by using essential PPE. Lab coats, gloves, and respirators protect against exposure to nanoparticles.
Proper handling, maintenance, and disposal of PPE are crucial for ensuring a safe working environment.
By adhering to these practices, nanotechnologists can minimize risks and enhance their safety while working with nanoscale materials.
Read: Top Skills Needed for a Successful Geology Career
Engineering Controls
Describe Engineering Controls Used in Nanotechnology Labs
Safety is a top priority in nanotechnology labs.
Engineers design effective engineering controls to protect workers from hazardous materials.
Fume hoods are essential for managing airborne contaminants.
These ventilated enclosures capture harmful fumes and particles, preventing exposure to researchers.
Properly functioning fume hoods ensure that researchers work safely with nanoparticles.
Ventilation systems also play a critical role in nanotechnology labs.
These systems circulate clean air and filter out hazardous particles.
They reduce the risk of inhaling harmful nanoparticles, ensuring a safe working environment.
Well-designed ventilation systems help maintain optimal air quality in lab settings.
Another important engineering control is the use of negative pressure rooms.
These rooms prevent the escape of nanoparticles into the surrounding environment.
Researchers can safely conduct experiments without risking contamination outside the lab.
Engineering controls like these create a safer workspace for all lab personnel.
How These Controls Help Contain Nanoparticles and Reduce Exposure Risks
Engineering controls are vital in containing nanoparticles and minimizing exposure risks.
Fume hoods effectively trap airborne nanoparticles, preventing them from dispersing in the lab.
This containment protects researchers from inhaling harmful substances.
Proper ventilation systems dilute airborne contaminants and remove them from the work area.
These systems maintain a clean air environment, reducing overall exposure to nanoparticles.
Effective airflow helps prevent the accumulation of hazardous particles in the lab.
Moreover, using personal protective equipment (PPE) in conjunction with engineering controls enhances safety.
While engineering controls provide primary protection, PPE serves as an additional barrier against exposure.
Examples of Best Practices for Implementing and Maintaining Engineering Controls
Implementing and maintaining engineering controls requires adherence to best practices.
Regular inspections of fume hoods and ventilation systems are essential.
Technicians should check for leaks, airflow, and proper functioning.
Routine maintenance ensures that these systems operate effectively and provide necessary protection.
Training staff on proper use and maintenance of engineering controls is crucial.
Researchers should understand how to operate fume hoods and recognize signs of malfunction.
Awareness of safety protocols fosters a culture of safety within the lab.
Additionally, conducting risk assessments helps identify areas needing improvement.
Regular evaluations of lab practices can reveal potential hazards and lead to necessary adjustments.
Labs should establish clear guidelines for handling nanoparticles safely.
Lastly, labs must promote open communication among researchers regarding safety concerns.
Encouraging team members to report issues with engineering controls enhances overall safety.
Sharing best practices and lessons learned can lead to continuous improvement in lab safety.
Read: Preparing for a Botany PhD: Tips and Advice
Hazard Communication
When working with nanomaterials, hazard communication is crucial to ensuring the safety of employees.
Clear labeling and communication of hazards associated with nanomaterials are key components of a successful safety program.
Importance of Clear Labeling
Clear labeling of containers containing nanomaterials is essential to inform employees about potential hazards.
Labels should include information such as the name of the material, hazard warnings, and safe handling instructions.
This helps to minimize the risk of accidental exposure and ensures that employees are aware of the dangers associated with the materials they are working with.
Safety Data Sheets (SDS)
Safety Data Sheets (SDS) provide detailed information about the properties and hazards of nanomaterials.
They include information on safe handling practices, storage requirements, emergency procedures, and disposal guidelines.
SDSs help employees understand the risks associated with the materials they are working with and how to protect themselves from potential harm.
Guidelines for Training Employees
Training employees on hazard communication is essential to ensure that they are aware of the risks associated with nanomaterials and how to handle them safely.
Training should include information on how to read labels, interpret SDSs, and respond to emergencies.
It is important to conduct regular training sessions to reinforce safety protocols and ensure that employees are up to date on the latest information.
Transform Your Career Today
Unlock a personalized career strategy that drives real results. Get tailored advice and a roadmap designed just for you.
Start NowUltimately, hazard communication is a critical component of a successful safety program when working with nanomaterials.
By clearly labeling containers, providing SDSs, and training employees on hazard communication, organizations can create a safe working environment and minimize the risk of accidents or injuries.
Implementing these practices not only protects employees but also ensures compliance with regulations and standards governing the use of nanomaterials.
Read: Women in Botany: Celebrating Pioneers and Leaders
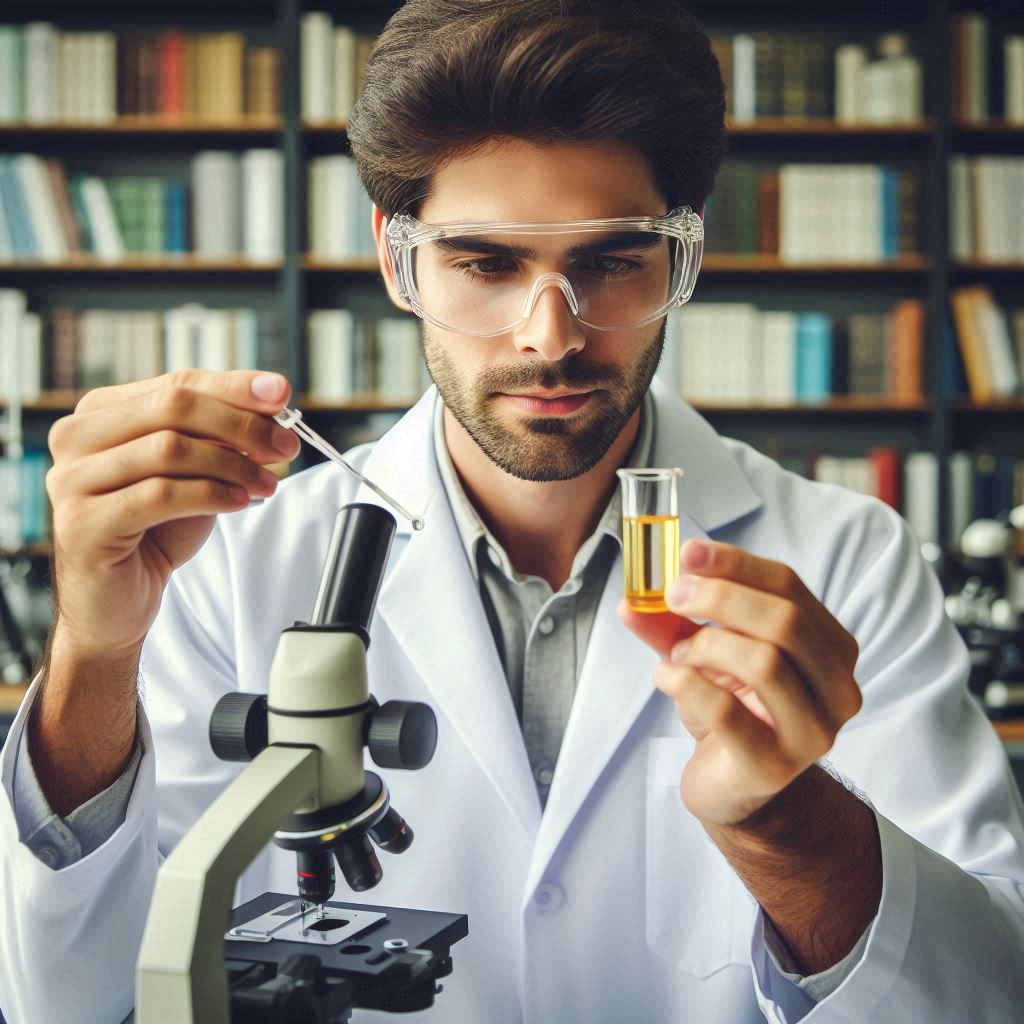
Waste Management
Proper Procedures for Handling and Disposing of Nanowaste
Handling and disposing of nanowaste requires strict adherence to safety practices.
First, always wear appropriate personal protective equipment (PPE).
This includes gloves, goggles, and lab coats to protect against exposure.
Second, use designated containers for collecting nanowaste.
Label these containers clearly to prevent confusion and ensure proper disposal.
Store nanowaste in a secure area, away from incompatible materials.
Avoid mixing different types of nanowaste, as this can create hazardous reactions.
Follow the specific regulations and guidelines set by local and national authorities for disposal.
Many regions require specialized facilities to handle nanowaste due to its unique properties.
When disposing of nanowaste, consider decontamination methods first.
Some nanomaterials can be treated to neutralize their hazardous properties.
After treatment, dispose of the waste according to established protocols.
Always document the disposal process to maintain compliance and accountability.
Risks of Improper Waste Management and Potential Impacts on Health and the Environment
Improper management of nanowaste poses significant risks to health and the environment.
Nanomaterials can be toxic, affecting human health upon exposure.
Inhalation or skin contact may lead to respiratory issues or skin irritation.
Long-term exposure could result in chronic health problems that are not immediately apparent.
Environmentally, nanomaterials can persist in ecosystems, causing harm to wildlife.
These particles can enter the food chain, posing risks to various organisms.
Contaminated water sources may affect drinking water quality and aquatic life.
Additionally, improper disposal can lead to soil contamination, disrupting local ecosystems.
Neglecting proper waste management practices also undermines public trust in nanotechnology.
If communities perceive that researchers ignore safety protocols, they may oppose nanotechnology developments.
Therefore, responsible waste management is crucial for safeguarding both public health and environmental integrity.
Recycling or Treating Nanomaterial Waste to Minimize Environmental Impact
Minimizing the environmental impact of nanowaste requires effective recycling and treatment strategies.
First, evaluate the feasibility of recycling nanomaterials before disposal.
Some nanomaterials, like carbon nanotubes, can be recycled and repurposed for other applications.
Collaborate with specialized recycling facilities that handle nanomaterials safely.
Second, consider treatment methods to neutralize the harmful properties of nanowaste.
Techniques such as thermal treatment can decompose certain nanomaterials, rendering them less hazardous.
Chemical treatments can also modify nanomaterials to reduce their toxicity.
Implementing closed-loop systems in research facilities can help minimize waste generation.
These systems enable the reuse of materials, reducing the amount of nanowaste produced.
Regularly train staff on the latest safety practices and disposal techniques to ensure compliance.
In essence, proper handling and disposal of nanowaste are vital for maintaining safety in nanotechnology.
Understanding the risks associated with improper waste management can guide better practices.
By adopting recycling and treatment strategies, we can minimize the environmental impact of nanomaterials while promoting responsible research.
Read: How Climate Change Is Impacting Plant Research
Delve into the Subject: Job Market Trends for Nuclear Scientists
See Related Content: Marine Biology Research Methods Explained
Emergency Response
Protocols for Responding to Accidents or Spills Involving Nanomaterials
Responding to accidents or spills involving nanomaterials requires strict protocols.
First, assess the situation to determine the extent of the spill.
Ensure that all personnel are safe and evacuate the area if necessary.
Inform your supervisor immediately about the incident.
They will coordinate the response and inform emergency services if needed.
Next, refer to the Material Safety Data Sheet (MSDS) for the specific nanomaterial involved.
The MSDS contains crucial information about hazards, handling procedures, and first aid measures.
Follow the recommendations outlined in the MSDS for containment and cleanup.
Use appropriate personal protective equipment (PPE) during the cleanup process to minimize exposure.
After the cleanup, document the incident thoroughly.
Record the details of the spill, including time, location, and response actions taken.
This documentation helps identify trends and improve safety protocols in the future.
Steps to Take in Case of Exposure or Contamination
In case of exposure to nanomaterials, prompt action is essential.
If skin contact occurs, immediately rinse the affected area with plenty of water for at least 15 minutes.
Remove contaminated clothing to prevent further exposure.
If inhalation occurs, move to fresh air and seek medical attention if symptoms persist.
For eye exposure, rinse the eyes gently with water or saline solution for at least 15 minutes.
Avoid rubbing the eyes, as this can worsen the situation.
Always report any exposure incidents to your supervisor for further evaluation and guidance.
In cases of ingestion, do not induce vomiting unless instructed by a medical professional.
Seek immediate medical attention to assess the situation and provide appropriate treatment.
Prompt response is crucial for minimizing health risks associated with nanomaterial exposure.
Importance of Emergency Drills and Training for All Personnel
Regular emergency drills and training are vital for ensuring a safe work environment.
These drills prepare personnel for responding effectively to accidents or exposure incidents.
They help reinforce safety protocols and build confidence among team members.
Training sessions should cover proper handling procedures for nanomaterials, including storage, disposal, and emergency response.
Employees must understand the risks associated with the specific nanomaterials they work with.
This knowledge empowers them to take appropriate precautions and act decisively in emergencies.
Moreover, emergency drills help identify areas for improvement in safety practices.
After each drill, conduct a debriefing session to discuss what went well and what needs improvement.
Continuous training and practice enhance the team‘s readiness to handle unexpected situations.
Essentially, following essential safety practices is crucial for nanotechnologists.
Proper protocols for responding to accidents, steps for exposure management, and regular training contribute to a safer work environment.
By prioritizing safety, nanotechnologists can minimize risks and ensure the well-being of everyone involved in nanotechnology research.
Gain More Insights: Grant Writing Tips for Aspiring Botanical Researchers
Regulatory Compliance
Regulations and Guidelines Set by Government Agencies
The Occupational Safety and Health Administration (OSHA) provides regulations that focus on worker safety.
OSHA requires that employers conduct risk assessments related to nanomaterials.
These assessments help identify potential hazards and implement appropriate control measures.
OSHA guidelines also include proper labeling of nanomaterials and maintaining Safety Data Sheets (SDS) for all chemicals used in the lab.
The Environmental Protection Agency (EPA) also plays a significant role in regulating nanotechnology.
The EPA requires manufacturers to report any new nanomaterials under the Toxic Substances Control Act (TSCA).
This regulation helps ensure that nanomaterials are evaluated for safety before they are introduced into the market.
The EPA conducts risk assessments to evaluate the environmental impact of nanomaterials and their potential effects on human health.
Compliance with these regulations is essential for promoting safety in nanotechnology research and development.
Adhering to established guidelines protects workers and the environment from potential hazards.
Consequences of Non-Compliance and Potential Legal Implications
Non-compliance with safety regulations can lead to serious consequences.
Failing to adhere to OSHA and EPA guidelines may result in workplace accidents and injuries.
Such incidents can jeopardize the health of employees and create liability issues for employers.
In addition to health risks, non-compliance can lead to significant legal implications.
Government agencies can impose hefty fines for violations.
Companies found in violation of safety regulations may face penalties ranging from thousands to millions of dollars.
These fines can severely impact a company‘s financial stability and reputation.
Moreover, legal action from employees or affected parties may occur due to negligence.
Companies may face lawsuits if they fail to provide a safe working environment.
Such legal actions can result in costly settlements and long-lasting reputational damage.
Resources for Staying Informed About Updates and Changes in Regulations
Staying informed about safety regulations is crucial for nanotechnologists.
Several resources can help professionals keep up-to-date with changes in regulations and guidelines.
The OSHA and EPA websites provide comprehensive information about regulations, compliance requirements, and safety practices.
Industry organizations such as the Nanotechnology Industry Association (NIA) offer resources and training related to nanotechnology safety.
These organizations often provide webinars, newsletters, and workshops that cover the latest developments in regulations.
Additionally, academic institutions and research organizations may publish guidelines and best practices for nanotechnology safety.
Subscribing to relevant journals can also help nanotechnologists stay informed about emerging safety issues and solutions.
Understanding and adhering to safety regulations in nanotechnology is essential.
Following guidelines set by agencies like OSHA and EPA protects workers and the environment.
Staying informed about updates and changes in regulations helps ensure compliance and promotes a culture of safety in the field.
By prioritizing safety, nanotechnologists can continue to innovate while safeguarding public health and well-being.
Conclusion
Safety practices are crucial for nanotechnologists working with materials at the nanoscale.
These practices ensure the well-being of researchers and protect the environment from potential hazards.
The unique properties of nanomaterials often pose unknown risks, making it essential to implement effective safety measures.
Proper handling, storage, and disposal of nanomaterials minimize exposure and reduce accidents.
Continuous learning and improvement in safety protocols are vital for nanotechnologists.
Staying updated on the latest research and industry standards helps mitigate risks associated with new materials and techniques.
Attending workshops and safety training can provide valuable insights into best practices for working safely with nanotechnology.
Additionally, companies must prioritize safety training and resources for their employees.
By investing in safety equipment and creating comprehensive training programs, organizations foster a culture of safety in the workplace.
This commitment not only protects workers but also enhances productivity and morale.
The responsibility for safety extends beyond individual researchers.
Companies, regulators, and the scientific community must collaborate to create a safe working environment.
This collaboration involves sharing knowledge and resources to develop comprehensive safety guidelines and regulations.
Engaging in open dialogue about safety concerns promotes transparency and accountability within the industry.