IntroductionÂ
Material handling techniques involve the movement, protection, storage, and control of materials within a facility.Â
Proper material handling techniques are essential in industries to ensure efficiency, safety, and productivity.Â
Manual material handling involves physically moving materials without the use of machinery or equipment.Â
Workers lift, carry, push, or pull items using proper lifting techniques to prevent injuries.Â
Automated material handling utilizes machines and robots to move, sort, or store materials.Â
This technique increases efficiency, reduces labor costs, and minimizes human error.Â
Conveyor systems are used to transport materials from one location to another within a facility.Â
They come in various types such as belt, chain, roller, and overhead conveyors.Â
Pallet racking is a storage system that organizes and stores materials on pallets.Â
It maximizes warehouse space, improves inventory management, and allows easy access to goods.Â
Forklifts are used to lift, move, and stack materials within a warehouse or facility.Â
They are essential for heavy or bulky items that cannot be handled manually.Â
Choosing the right material handling technique is crucial for the success of any industry.Â
Implementing efficient methods can lead to improved operational processes and increased competitiveness.
Manual Material Handling Techniques
Manual material handling refers to the process of moving goods using physical effort instead of machinery.
It involves tasks like lifting, carrying, pushing, and pulling items to different locations within a warehouse or worksite.
Definition of Manual Material Handling
Manual material handling is the process of moving items by using physical force, such as lifting or carrying, rather than mechanical aids like forklifts or conveyors.
Examples of Manual Material Handling Techniques
- Lifting: Involves raising an object from one location to another, typically done by bending the knees and using leg muscles instead of the back.
- Carrying: Moving an object while holding it in the hands or on the shoulders, distributing the weight evenly to avoid strain.
- Pushing: Using force to move an item away from the body, usually with the arms and upper body strength.
- Pulling: Moving an object towards the body by exerting force in the opposite direction, often using arm and back muscles.
Importance of Proper Body Mechanics in Manual Material Handling
Proper body mechanics are essential when performing manual material handling tasks to prevent injuries and strain on the body.
By using correct lifting techniques and posture, workers can reduce the risk of musculoskeletal disorders and related injuries.
Some key principles of proper body mechanics in manual material handling include:
Transform Your Career Today
Unlock a personalized career strategy that drives real results. Get tailored advice and a roadmap designed just for you.
Start Now- Bend at the knees, not the waist, when lifting heavy objects to avoid straining the back.
- Keep the load close to the body to reduce the amount of force exerted on muscles.
- Use the legs to lift, pushing through the heels and engaging leg muscles instead of relying on the back.
- Avoid twisting the body while carrying or lifting objects, as this can lead to strains and sprains.
- Take frequent breaks and avoid overexertion when performing manual material handling tasks.
Employers should provide training on proper lifting techniques and body mechanics to workers who engage in manual material handling activities to ensure their health and safety.
By following best practices and guidelines, workers can reduce the risk of workplace injuries and improve efficiency in handling materials.
Read: Importance of Data Analysis for Logistics Coordinators
Automated Material Handling Techniques
Definition of automated material handling
Automated material handling refers to the use of technology to move and manage materials.
This approach enhances efficiency and reduces labor costs.
By minimizing human intervention, automation streamlines operations and increases productivity.
How automation improves efficiency and reduces labor costs
Automation significantly improves efficiency by speeding up processes.
Automated systems handle repetitive tasks, allowing human workers to focus on higher-value activities.
This shift results in faster order fulfillment and improved inventory management.
Consequently, companies experience shorter lead times and enhanced customer satisfaction.
Examples of automated material handling equipment like conveyors, robotics, and automated storage systems
Automated material handling equipment plays a crucial role in these improvements.
Conveyors transport materials smoothly throughout facilities.
They reduce manual labor and increase speed in moving products from one location to another.
Robotics further enhance material handling by performing tasks like picking, packing, and sorting.
These machines work around the clock, ensuring consistent output and reducing errors.
Automated storage systems optimize space and improve accessibility.
These systems organize inventory more efficiently, allowing for quick retrieval.
They utilize advanced technology to track inventory levels and locations, minimizing the risk of stockouts or overstocking.
Implementing automated material handling techniques offers significant benefits.
Companies can achieve higher throughput and lower operational costs.
Transform Your Career Today
Unlock a personalized career strategy that drives real results. Get tailored advice and a roadmap designed just for you.
Start NowAutomation also enhances safety by reducing the risk of workplace injuries associated with manual lifting and transporting.
In summary, automated material handling techniques revolutionize the way businesses manage materials.
By leveraging equipment like conveyors, robotics, and automated storage systems, organizations can boost efficiency and reduce labor costs.
Embracing automation positions companies for success in today’s fast-paced market.
Read: Key Skills Needed for Material Handlers in Transport
Ergonomic Material Handling Techniques
Definition of ergonomic material handling
Ergonomic material handling focuses on designing tasks and equipment that fit the human body’s capabilities and limitations.
Importance of ergonomics in material handling to prevent musculoskeletal disorders
Ergonomics plays a crucial role in preventing musculoskeletal disorders, such as strains and injuries, by reducing physical stress on workers’ bodies.
Examples of ergonomic material handling equipment like adjustable height workstations and ergonomic tools
- Adjustable Height Workstations: These workstations allow employees to customize the height of their workspace, reducing the risk of strain.
- Ergonomic Tools: Tools with ergonomic designs reduce the strain on the hands, wrists, and arms, making tasks easier and safer.
Implementing ergonomic material handling techniques not only improves worker safety and health but also enhances productivity and efficiency in the workplace.
Read: Logistics Coordinator: Strategies for Career Growth
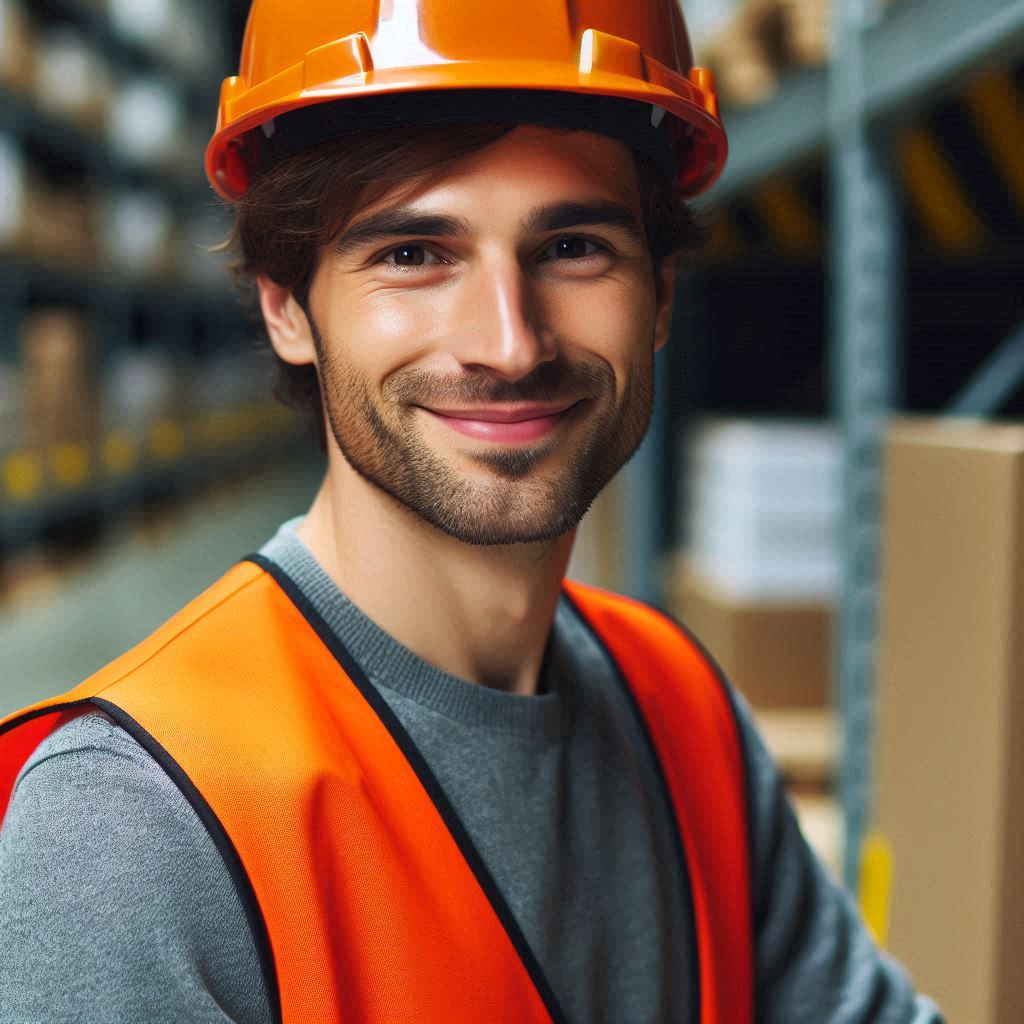
Just-In-Time (JIT) Material Handling Techniques
Just-In-Time (JIT) material handling is a strategy that focuses on having the right materials at the right place and time.
This technique is crucial for efficient production processes and supply chain management.
JIT Material Handling
JIT material handling revolves around minimizing inventory levels to reduce costs associated with storage and handling.
It involves precise planning and coordination with suppliers to ensure timely delivery of materials.
By implementing JIT material handling, companies can streamline their operations and eliminate waste in the form of excess inventory.
This approach allows businesses to respond quickly to changes in customer demand and market trends.
Benefits of JIT Material Handling in Reducing Inventory and CostsÂ
- Reduction of carrying costs: With JIT material handling, companies can minimize the expenses related to storing, managing, and financing excess inventory.
- Improved cash flow: By reducing inventory levels, businesses can free up capital that would have been tied up in excess materials.
- Enhanced efficiency: JIT material handling helps in optimizing production processes, leading to reduced lead times and higher productivity.Â
- Lower risk of obsolescence: Through JIT, companies can avoid the risk of holding obsolete or expired inventory, thus reducing potential losses.
Examples of JIT Material Handling Techniques
There are several techniques that companies can use to implement JIT material handling effectively.
Some common examples include:Â
- Kanban Systems: Kanban is a visual scheduling system that helps in regulating the flow of materials by signaling when to replenish or move supplies.
- Cross-Docking: This technique involves unloading materials from incoming trucks directly onto outbound vehicles without storing them in the warehouse.Â
- Vendor-Managed Inventory (VMI): With VMI, suppliers manage the inventory levels at the customer’s facility, ensuring a seamless supply of materials.
- Continuous Replenishment: This approach involves replenishing materials in small quantities frequently to maintain optimal inventory levels.
Overall, JIT material handling enables companies to operate more efficiently, reduce costs, and improve customer satisfaction by delivering products when needed.
By embracing JIT principles, businesses can stay competitive in today’s dynamic market environment.
Read: Logistics Coordinator: Remote Work Opportunities
Transform Your Career Today
Unlock a personalized career strategy that drives real results. Get tailored advice and a roadmap designed just for you.
Start NowLean Material Handling Techniques
Lean material handling refers to the implementation of lean principles in the handling and movement of materials within a facility.
It aims to streamline processes, reduce waste, and enhance overall efficiency.
Definition of Lean Material Handling
Lean material handling involves using lean manufacturing principles to optimize material flow and eliminate non-value-added activities.
It emphasizes continuous improvement and waste reduction throughout the material handling process.
Importance of Lean Principles
Integrating lean principles in material handling helps in improving productivity, reducing lead times, enhancing product quality, and increasing customer satisfaction.
By eliminating waste and inefficiencies, companies can achieve cost savings and operational excellence.
Optimizing Material Flow
One of the key objectives of lean material handling is to optimize material flow by ensuring that materials are efficiently transported, stored, and processed throughout the facility.
This helps in reducing bottlenecks and delays in the production process.
Minimizing Waste
Lean material handling focuses on minimizing waste in various forms such as excess inventory, unnecessary motion, overproduction, and defects.
By identifying and eliminating waste, companies can operate more efficiently and sustainably.
Examples of Lean Material Handling TechniquesÂ
- Value Stream Mapping: This technique involves mapping out the entire material flow process to identify areas of waste and inefficiency.
By visualizing the value stream, companies can implement improvements to enhance flow and eliminate bottlenecks. - 5S Methodology: 5S is a systematic approach to organizing the workplace by sorting, setting in order, shining, standardizing, and sustaining.
By implementing 5S practices, companies can create a clean and well-organized work environment that promotes efficiency and safety.
All in all, lean material handling techniques play a crucial role in enhancing operational performance and driving continuous improvement within manufacturing and logistics operations.
By embracing lean principles, companies can achieve greater efficiency, cost savings, and customer satisfaction.
Safety Considerations in Material Handling
When it comes to material handling, safety should always be a top priority to protect workers and prevent accidents.
By following key safety guidelines and using proper safety equipment, potential risks can be minimized.
Let’s explore the importance of safety in material handling, key safety guidelines, and examples of safety equipment that should be utilized.
Importance of Safety in Material HandlingÂ
- Preventing Accidents and Injuries: Safety measures help reduce the likelihood of accidents and injuries in the workplace.
- Protecting Workers: Ensuring safety in material handling protects workers from potential harm.
- Promoting a Safe Work Environment: By prioritizing safety, a safe work environment is maintained.
- Compliance with Regulations: Adhering to safety guidelines ensures compliance with regulations and standards.
Key Safety Guidelines for Proper Material Handling TechniquesÂ
- Training: Proper training should be provided to employees on safe material handling practices.
- Use of Mechanical Aids: Utilize equipment like forklifts and conveyors for heavy lifting.Â
- Proper Lifting Techniques: Encourage employees to lift with their legs, not their back.Â
- Clear Communication: Ensure clear communication among workers to prevent mishaps.
- Regular Inspections: Conduct regular inspections of equipment and tools for safety compliance.
Examples of Safety EquipmentÂ
- Personal Protective Equipment (PPE): Items like gloves, helmets, goggles, and steel-toed boots protect workers from hazards.Â
- Safety Signage: Clear and visible signs indicating potential dangers and safety precautions.Â
- Fire Extinguishers: Tools to combat fires that may arise during material handling activities.Â
- First Aid Kits: Essential in providing immediate medical attention in case of injuries.
- Emergency Alarms: Alerts and notifications to evacuate in case of emergencies.
By prioritizing safety in material handling and following these key guidelines, workplaces can ensure the well-being of their employees and mitigate potential risks effectively.
Conclusion
In this blog post, we explored various material handling techniques.
Each technique plays a crucial role in streamlining operations.
We discussed manual handling, which relies on human strength and coordination.
Next, we examined mechanical handling, utilizing equipment like forklifts and conveyors.
Transform Your Career Today
Unlock a personalized career strategy that drives real results. Get tailored advice and a roadmap designed just for you.
Start NowAutomated systems were also highlighted for their efficiency and speed in large-scale operations.
Proper material handling techniques are vital for ensuring workplace safety.
They help prevent accidents and injuries, protecting employees.
Implementing these techniques boosts operational efficiency, reducing time and costs.
Additionally, effective handling minimizes product damage, preserving quality and reducing waste.
Industries that prioritize material handling techniques see enhanced productivity.
Workers can perform tasks more quickly and accurately.
Moreover, proper training in handling techniques equips employees with essential skills.
This knowledge leads to safer work environments and fosters teamwork.
In the end, adopting the right material handling techniques is essential for success.
Organizations should assess their current practices and seek improvements.
By doing so, they can create safer workplaces and optimize operations.
Embracing these techniques benefits both employees and businesses, ultimately driving growth.