Introduction
Material handling safety is crucial across industries to prevent accidents and protect workers.
Statistics show that a significant number of workplace injuries are caused by improper material handling.
This blog post aims to outline the best practices for ensuring safety in material handling processes.
Conduct a thorough assessment of the workplace to identify potential hazards and risks.
Ensure that the layout and organization of the workspace promote safe material handling practices.
Implement clear signage and markings to indicate designated pathways and storage areas.
Provide comprehensive training on proper material handling techniques to all employees.
Regularly reinforce safety protocols and conduct refresher courses to keep employees informed and vigilant.
Encourage open communication between workers to report any unsafe practices or conditions promptly.
Choose material handling equipment that is well-maintained, suitable for the task, and properly rated.
Regularly inspect and service equipment to ensure optimal functionality and safety compliance.
Consider ergonomic features to minimize strain and reduce the risk of musculoskeletal injuries.
Train employees on proper lifting techniques, including bending at the knees and keeping the back straight.
Encourage the use of mechanical aids such as forklifts, pallet jacks, or conveyors for heavy or awkward loads.
Implement weight restrictions and guidelines for team lifting to prevent injuries from overexertion.
Conduct routine safety audits to assess compliance with material handling protocols and identify areas for improvement.
Review incident reports and near-misses to address underlying causes and prevent future occurrences.
Seek feedback from employees to continuously refine safety practices and ensure a culture of prioritizing safety.
Proper Training for Employees
Importance of providing thorough training on safe material handling practices
Providing thorough training on safe material handling practices is crucial for workplace safety.
Well-trained employees are less likely to suffer injuries.
Transform Your Career Today
Unlock a personalized career strategy that drives real results. Get tailored advice and a roadmap designed just for you.
Start NowStart training new hires as soon as they join your team.
Offer hands-on sessions to teach them the correct techniques for lifting, carrying, and moving materials.
Incorporating training sessions for new hires and regular refresher courses for existing employees
Incorporate regular refresher courses for existing employees to keep their skills sharp.
Safety procedures can change over time, so ongoing training is essential.
Ensure employees understand the importance of proper techniques and the potential consequences of negligence.
The correct techniques for lifting, carrying, and moving materials to prevent injuries
Emphasize the significance of body mechanics in lifting heavy items.
Teach employees to bend their knees and keep their back straight while lifting.
Show them how to carry materials close to their bodies to reduce strain.
Encourage teamwork for moving large or awkward items.
Remind employees to ask for help when necessary.
Use a variety of training methods to cater to different learning styles.
Incorporate demonstrations, visual aids, and interactive sessions to engage employees.
Regularly assess employee understanding through quizzes or hands-on evaluations.
In addition to training, provide employees with the right tools and equipment.
Ensure they have access to dollies, forklifts, and personal protective equipment.
Remind them to use these tools to avoid unnecessary strain or injury.
Finally, create a culture of safety in your workplace.
Encourage employees to speak up about unsafe practices or conditions.
Foster an environment where safety is everyone’s responsibility.
By prioritizing proper training, you significantly reduce the risk of injuries and enhance overall workplace safety.
Transform Your Career Today
Unlock a personalized career strategy that drives real results. Get tailored advice and a roadmap designed just for you.
Start NowRead: Career Path: Becoming a Material Handler
Equipment Maintenance and Inspections
Equipment maintenance and inspections are critical components of ensuring material handling safety in any workplace.
By regularly inspecting and maintaining equipment such as forklifts, pallet jacks, and conveyors, organizations can prevent accidents, injuries, and damage to goods.
Here are some best practices for equipment maintenance and inspections:
Regular Inspection of Equipment
It is essential to conduct routine inspections of all material handling equipment to identify any potential safety hazards.
Make sure to check for wear and tear, loose parts, leaks, and other signs of damage that may compromise the safe operation of the equipment.
Proper Maintenance Schedules
Establishing proper maintenance schedules for equipment is crucial to address any issues or malfunctions promptly.
This includes regular servicing, lubrication, and adjustments to ensure that the equipment is in optimal working condition.
Training Employees on Equipment Maintenance
Provide comprehensive training to employees on how to recognize and report equipment problems.
Encourage employees to report any abnormalities they observe during equipment operation so that repairs can be carried out promptly to prevent further damage or accidents.
By implementing these best practices for equipment maintenance and inspections, organizations can create a safer work environment and reduce the risk of accidents or injuries associated with material handling operations.
Read: The Role of Material Handlers in Inventory Control
Clear Communication and Signage
Implementing clear signage throughout the workplace to indicate designated areas for material storage and handling
Effective communication is essential in ensuring material handling safety in the workplace.
Clear signage should be strategically placed throughout the facility to indicate designated areas for material storage and handling.
This helps employees easily navigate the workspace and understand where certain materials should be stored or handled.
Using visual cues and labels to clearly identify hazardous materials and proper handling procedures
Visual cues and labels play a crucial role in identifying hazardous materials and providing guidance on proper handling procedures.
By utilizing clear and concise signage, employees can quickly recognize potential risks and take appropriate safety measures to prevent accidents or injuries.
Encouraging open communication among employees to report any safety concerns or violations promptly
Encouraging open communication among employees is also vital for maintaining a safe work environment.
Team members should feel empowered to report any safety concerns or violations they observe promptly.
This proactive approach to communication helps address issues before they escalate and ensures that safety protocols are consistently followed.
Transform Your Career Today
Unlock a personalized career strategy that drives real results. Get tailored advice and a roadmap designed just for you.
Start NowRegular safety meetings and training sessions can further reinforce the importance of clear communication and adherence to signage.
By discussing safety procedures and highlighting the significance of following proper handling guidelines, employees are more likely to prioritize safety in their daily tasks.
Basically, clear communication and signage are key components of effective material handling safety practices.
By implementing visible cues, labels, and encouraging open communication, workplaces can foster a culture of safety and minimize the risk of accidents or injuries related to material handling.
Read: Typical Day in the Life of a Material Handler
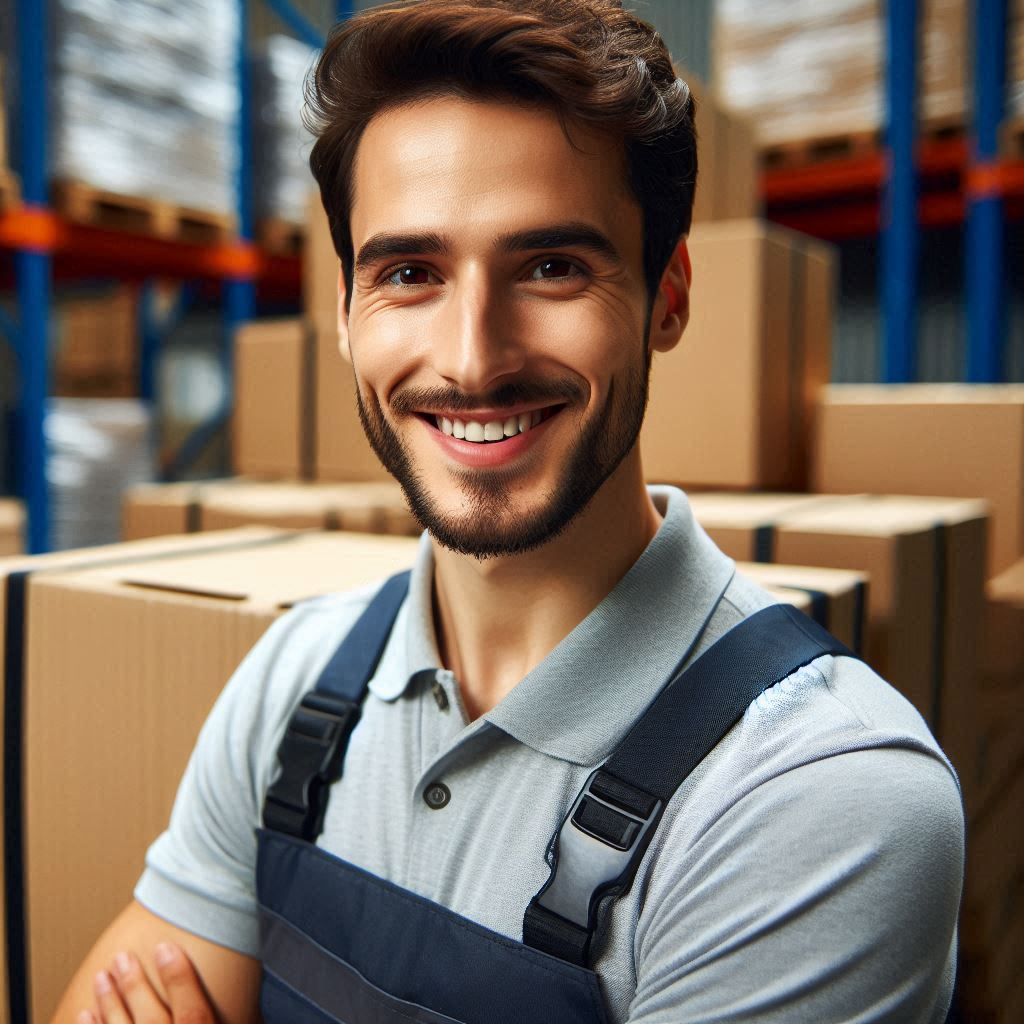
Ergonomic Considerations
When it comes to material handling safety, ergonomic considerations play a crucial role in ensuring the well-being of employees and reducing the risk of injuries.
By incorporating ergonomic principles into the design of workstations and material handling processes, employers can create a safer and more comfortable working environment for their employees.
Designing workstations and material handling processes with ergonomic principles to reduce strain and injuries
One key aspect of ergonomic design is the need to reduce strain and injuries that can result from repetitive or heavy lifting tasks.
By carefully planning and organizing workstations in a way that minimizes unnecessary movements and strain on the body, employers can help prevent injuries such as strains, sprains, and musculoskeletal disorders.
Providing adjustable equipment and tools to accommodate employees of various heights and body types
Providing adjustable equipment and tools is another important aspect of ergonomic considerations in material handling safety.
Employees come in all shapes and sizes, and it is essential to have equipment that can be easily adjusted to accommodate individuals of varying heights and body types.
This not only promotes a more comfortable working environment but also reduces the risk of injuries caused by using tools that are not properly suited to an employee’s physical characteristics.
Encouraging proper posture and technique during material handling tasks to prevent musculoskeletal injuries
In addition to providing adjustable equipment, employers should also focus on educating employees about the importance of proper posture and technique during material handling tasks.
Encouraging employees to maintain good posture and use correct lifting techniques can help prevent injuries such as back strains and sprains.
Providing training on proper lifting techniques and reinforcing the importance of following ergonomic guidelines can go a long way in reducing the risk of musculoskeletal injuries in the workplace.
Overall, incorporating ergonomic considerations into material handling processes is essential for promoting the safety and well-being of employees.
By designing workstations with ergonomic principles in mind, providing adjustable equipment, and promoting proper posture and technique, employers can create a safer and more comfortable work environment that reduces the risk of injuries and improves employee morale and productivity.
Read: What Does a Material Handler Do in Logistics?
Emergency Preparedness
Establishing emergency protocols for accidents and injuries related to material handling incidents
In any workplace, accidents and injuries can happen unexpectedly, especially in environments where material handling is a crucial part of daily operations.
It is essential to be prepared for emergencies and have protocols in place to address them promptly and effectively.
Transform Your Career Today
Unlock a personalized career strategy that drives real results. Get tailored advice and a roadmap designed just for you.
Start NowConducting regular drills to practice emergency response procedures and evacuation routes
One of the best practices for ensuring safety in material handling operations is to establish clear emergency protocols.
These protocols should outline the steps to be taken in the event of an accident or injury related to material handling incidents.
Having a set procedure in place can help mitigate risks and minimize the impact of emergencies.
Providing proper first aid kits and training employees on basic first aid techniques for immediate assistance
Regular drills and exercises can be extremely beneficial in preparing employees for emergencies.
By conducting drills, employees can practice emergency response procedures and familiarize themselves with evacuation routes.
This hands-on experience can significantly improve their ability to react quickly and effectively during a real emergency.
Another crucial aspect of emergency preparedness is ensuring that first aid resources are readily available on-site.
Providing proper first aid kits equipped with essential supplies is essential.
Additionally, training employees on basic first aid techniques can empower them to provide immediate assistance to those in need.
This training can make a significant difference in the outcome of an emergency situation.
By prioritizing emergency preparedness and incorporating these best practices into your material handling safety program, you can create a safer work environment for everyone involved.
Remember, being proactive and prepared is key to preventing accidents and minimizing the impact of emergencies in the workplace.
Implementing a Safety Culture
Fostering a culture of safety awareness and accountability among all employees
Creating a safety culture is essential for effective material handling.
Begin by fostering safety awareness among all employees.
Ensure everyone understands their role in maintaining a safe work environment.
Encourage open communication about safety concerns and practices.
This empowers employees to take ownership of their safety responsibilities.
Recognizing and rewarding individuals and teams who demonstrate commitment to safe material handling practices
Recognize and reward individuals and teams committed to safe material handling practices.
Implement a recognition program that highlights safe behavior.
Celebrate milestones, such as incident-free weeks, to motivate all staff.
Transform Your Career Today
Unlock a personalized career strategy that drives real results. Get tailored advice and a roadmap designed just for you.
Start NowThis recognition not only boosts morale but reinforces the importance of safety.
Holding regular safety meetings to discuss incidents, near misses, and ways to improve safety measures
Conduct regular safety meetings to address incidents and near misses.
Use these meetings to analyze what went wrong and identify areas for improvement.
Involve employees in discussions about safety challenges they face.
Their insights can lead to practical solutions that enhance safety measures.
Ensure that safety meetings are interactive and engaging.
Encourage team members to share experiences and suggestions for improvement.
Create a safe space for discussions, where employees feel valued and heard.
This collaborative approach fosters a sense of community focused on safety.
Provide ongoing training on safe material handling practices.
Use real-life scenarios to illustrate the importance of safety.
This hands-on training helps employees recognize potential hazards and respond effectively.
Regularly review and update safety protocols based on feedback and incidents.
Adapt to changing circumstances to keep safety practices relevant.
A proactive approach to safety ensures all employees remain vigilant and informed.
By prioritizing safety culture, organizations can significantly reduce accidents and injuries.
A strong commitment to safety cultivates a work environment where everyone thrives.
This not only protects employees but enhances overall productivity and efficiency.
Continuous Improvement and Feedback
Encouraging employees to provide feedback on current material handling processes and suggest improvements
Encouraging employees to provide feedback on current material handling processes and suggest improvements can lead to valuable insights.
By creating a culture of continuous improvement and feedback, organizations can proactively address safety issues and prevent accidents.
Transform Your Career Today
Unlock a personalized career strategy that drives real results. Get tailored advice and a roadmap designed just for you.
Start NowEmployees should feel empowered to speak up about any concerns they may have regarding material handling safety.
Conducting regular safety audits and inspections to identify potential hazards and areas for improvement
Regular safety audits and inspections should be conducted to assess the current state of safety practices in the workplace.
These audits can help identify potential hazards and areas for improvement, allowing organizations to take corrective actions promptly.
Implementing a system for reporting and addressing safety concerns in a timely manner
Having a system in place for reporting and addressing safety concerns is critical.
Employees should be able to report any safety issues they encounter, and management should address these concerns in a timely manner to prevent accidents and injuries.
Feedback from employees should be taken seriously, and suggestions for improvement should be carefully considered.
Implementing changes based on this feedback can lead to a safer work environment and improved material handling practices.
Overall, continuous improvement and feedback are key components of a successful material handling safety program.
By prioritizing these practices, organizations can create a culture of safety and prevent accidents in the workplace.
Learn More: Top Skills and Qualities of a Successful Train Conductor
Conclusion
Best practices for material handling safety are vital for every workplace.
Workers should receive comprehensive training on safe handling techniques.
Proper lifting techniques, such as bending at the knees, reduce the risk of back injuries.
Always use appropriate equipment, like forklifts or pallet jacks, to move heavy items.
Employers must encourage a culture of safety.
This involves regularly inspecting equipment and maintaining a clean workspace.
Clear pathways free from obstructions ensure safe movement throughout the facility.
Implementing signage and visual aids reminds employees of safe practices.
Utilizing personal protective equipment (PPE) is essential.
Gloves, steel-toed boots, and safety goggles provide additional protection against potential hazards.
Transform Your Career Today
Unlock a personalized career strategy that drives real results. Get tailored advice and a roadmap designed just for you.
Start NowEmployees should know when and how to use PPE correctly.
Regular safety audits and assessments help identify risks.
Conducting these audits fosters a proactive approach to safety.
Engaging workers in discussions about safety can uncover valuable insights and improvements.
Injuries from improper material handling can significantly affect productivity.
Prioritizing safety in all material handling processes prevents accidents and injuries.
A safe work environment boosts employee morale and retention.
By embracing these best practices, organizations create a culture of safety.
Ultimately, focusing on material handling safety benefits everyone in the workplace.
A commitment to safety leads to a more productive and efficient operation.
Always remember, safety is everyone‘s responsibility, and it should be a top priority.