Introduction
Material handling processes play a vital role in various industries.
They encompass the movement, protection, storage, and control of materials.
Efficient material handling directly impacts productivity and cost management.
By optimizing these processes, businesses can streamline operations and enhance workflow.
In manufacturing, effective material handling ensures smooth production flow.
It minimizes delays caused by material shortages or misplacement.
Additionally, organized material handling reduces the risk of damage, ensuring that products remain intact.
This efficiency translates to lower replacement costs and increased customer satisfaction.
In warehousing, material handling systems are crucial for managing inventory.
They help track products accurately and facilitate quick order fulfillment.
This efficiency leads to shorter lead times, allowing companies to respond swiftly to customer demands.
Improved accuracy in inventory management also decreases holding costs, benefiting the bottom line.
Retail industries also rely heavily on effective material handling.
Streamlined processes enhance restocking efficiency, allowing retailers to maintain optimal inventory levels.
This not only improves customer experience but also boosts sales opportunities.
Quick turnaround in material handling enables retailers to adapt to changing market trends effectively.
Furthermore, efficient material handling can contribute to a safer work environment.
Proper training and systems minimize accidents related to heavy lifting and machinery use.
A safe workplace reduces downtime caused by injuries, further enhancing productivity.
In summary, understanding material handling processes is essential across industries.
Transform Your Career Today
Unlock a personalized career strategy that drives real results. Get tailored advice and a roadmap designed just for you.
Start NowEfficient practices improve productivity, reduce costs, and create safer work environments.
Investing in effective material handling systems pays off in the long run, benefiting both companies and their customers.
Embracing these processes leads to sustained growth and competitiveness in today’s fast-paced market.
What is Material Handling?
Material handling and its importance in the manufacturing and distribution process
Material handling refers to the movement, protection, storage, and control of materials throughout the manufacturing and distribution process.
It plays a crucial role in ensuring efficiency and safety in operations.
Effective material handling minimizes waste, reduces costs, and enhances productivity.
The different types of materials that are handled in various industries
Different industries handle various types of materials.
In manufacturing, raw materials like metals, plastics, and chemicals are common.
These materials require careful handling to maintain quality and prevent accidents.
In the construction sector, heavy materials such as steel beams, concrete, and bricks are prevalent.
Workers use cranes, forklifts, and other equipment to manage these items safely.
The food industry deals with perishable materials, such as fruits, vegetables, and dairy products.
Proper handling techniques are essential to maintain freshness and comply with health regulations.
Pharmaceuticals also require strict material handling procedures.
Medications must be stored and transported under specific conditions to ensure efficacy and safety.
In retail, businesses handle consumer goods, from clothing to electronics.
Efficient material handling systems streamline the supply chain, improving customer satisfaction.
Warehousing operations often involve sorting, storing, and retrieving a wide range of products.
Moreover, material handling processes vary depending on the material’s nature and industry requirements.
Some materials, like hazardous substances, require special handling techniques to ensure worker safety and environmental protection.
Transform Your Career Today
Unlock a personalized career strategy that drives real results. Get tailored advice and a roadmap designed just for you.
Start NowUnderstanding material handling processes helps organizations optimize operations.
By implementing best practices, businesses can enhance efficiency, reduce costs, and improve safety.
Effective material handling is vital across industries, impacting overall productivity and success.
Read: Material Handler Jobs: Where to Find Them
Benefits of Efficient Material Handling Processes
The benefits of implementing efficient material handling processes
Implementing efficient material handling processes provides numerous advantages for businesses.
First, it streamlines operations, allowing for faster workflows.
When materials move smoothly, employees spend less time searching for items.
This efficiency boosts productivity and increases overall output.
Moreover, efficient material handling improves safety in the workplace.
Proper handling techniques minimize the risk of accidents and injuries.
Training employees on safe practices fosters a culture of safety.
As a result, businesses experience fewer workplace incidents and reduced liability costs.
How it can streamline operations, improve safety, and reduce downtime
Reducing downtime is another significant benefit of efficient material handling.
When processes are optimized, equipment experiences fewer breakdowns.
Reliable operations lead to consistent production schedules.
This reliability enhances customer satisfaction, as businesses can fulfill orders on time.
Additionally, efficient material handling processes lower operational costs.
Streamlined workflows decrease labor costs and increase resource utilization.
Businesses can allocate resources more effectively, leading to improved profitability.
Furthermore, implementing advanced technologies, such as automation, enhances material handling efficiency.
Transform Your Career Today
Unlock a personalized career strategy that drives real results. Get tailored advice and a roadmap designed just for you.
Start NowAutomated systems reduce human error and speed up processes.
Businesses that adopt these technologies gain a competitive edge in the market.
Lastly, efficient material handling contributes to better inventory management.
Accurate tracking of materials ensures that stock levels remain optimal.
This prevents overstocking and stockouts, reducing excess inventory costs.
The benefits of efficient material handling processes are substantial.
Streamlining operations, improving safety, and reducing downtime all contribute to business success.
Companies that prioritize efficient material handling position themselves for growth and enhanced performance.
Investing in these processes is crucial for achieving operational excellence.
Read: Material Handler Job Satisfaction Factors
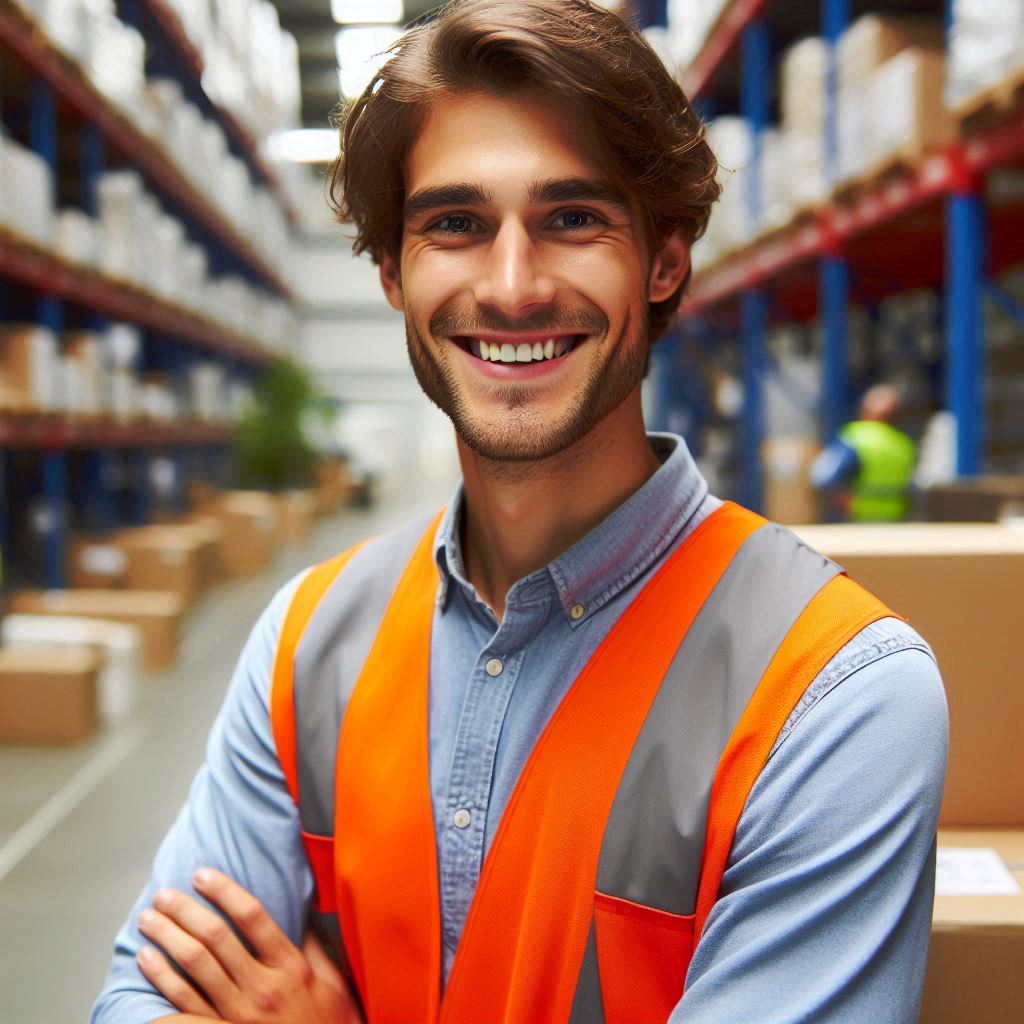
Common Material Handling Equipment
Material handling equipment plays a crucial role in various industries.
This equipment streamlines the movement, protection, and storage of goods.
Several types of equipment are commonly used to enhance efficiency and safety in material handling processes.
The different types of material handling equipment commonly used in industries
Forklifts are widely used for lifting and transporting heavy loads.
They excel in warehouses and construction sites.
These vehicles come in various types, including electric and propane models, catering to different needs.
Forklifts can handle pallets and bulk materials, making them essential in material handling.
Conveyors provide a continuous flow of materials.
They efficiently move products between different locations within a facility.
Various conveyor types exist, such as belt, roller, and overhead systems.
Transform Your Career Today
Unlock a personalized career strategy that drives real results. Get tailored advice and a roadmap designed just for you.
Start NowEach type serves unique functions, allowing for seamless product transportation.
Pallet jacks are essential for moving pallets and heavy items short distances.
Operators can easily maneuver these devices in tight spaces.
Manual and electric pallet jacks are available, accommodating various load capacities and user preferences.
Cranes are crucial for lifting heavy loads to significant heights.
They are commonly used in construction and manufacturing sectors.
Different types of cranes, such as overhead and mobile cranes, offer versatility in lifting operations.
These machines enhance safety and efficiency when handling large materials.
Other equipment, such as stackers and hoists, also play important roles in material handling.
Each type of equipment is designed to meet specific operational needs.
Understanding these options helps businesses choose the right tools for their material handling processes.
Examples such as forklifts, conveyors, pallet jacks, and cranes
Investing in appropriate material handling equipment boosts productivity and enhances workplace safety.
Companies should evaluate their specific needs to select the best equipment.
This decision will ultimately lead to smoother operations and reduced labor costs.
Read: Material Handler Resume: Tips and Examples
Factors to Consider in Material Handling
When designing a material handling system, there are several key factors that need to be taken into consideration to ensure efficiency and safety.
Below are some important factors to consider:
Space ConstraintsÂ
- One of the most critical factors to consider is the available space for material handling activities.
- The layout of the facility and the storage area should be optimized to minimize travel distance and maximize storage capacity.
- Efficient space utilization can help reduce material handling costs and improve productivity.
Material CharacteristicsÂ
- Understanding the characteristics of the materials being handled is essential in designing an effective material handling system.
- The weight, size, shape, and fragility of the materials will dictate the type of equipment and handling methods required.
- Special handling requirements such as temperature sensitivity or hazardous properties must also be taken into account.
Safety RegulationsÂ
- Compliance with safety regulations is a crucial consideration in material handling system design.
- Adherence to OSHA regulations and industry standards is necessary to protect workers and prevent accidents.
- Proper training of employees on safe handling practices and the use of appropriate safety equipment is essential.
By carefully considering these factors, businesses can design material handling systems that are efficient, cost-effective, and safe.
It is important to conduct a thorough assessment of the specific requirements of the operation to tailor the material handling system to meet those needs effectively.
Read: Material Handler’s Role in Logistics Strategy
Transform Your Career Today
Unlock a personalized career strategy that drives real results. Get tailored advice and a roadmap designed just for you.
Start NowBest Practices for Material Handling Processes
When it comes to optimizing material handling processes, there are several tips and best practices that businesses can implement to improve efficiency and productivity.
Organizing the Workspace
- Designate specific areas for different types of materials to promote easy access and retrieval.
- Implement a labeling system to ensure items are clearly identified and located quickly.
- Regularly declutter and organize the workspace to prevent bottlenecks and improve flow.
- Utilize storage solutions such as shelves, bins, and racks to maximize space and efficiency.
Training Employees
- Provide comprehensive training on safe material handling practices to prevent injuries and accidents.
- Ensure employees are familiar with equipment operation and maintenance for optimal use.
- Offer continuous training and refresher courses to keep employees updated on best practices.
- Encourage open communication and feedback to address any issues or concerns promptly.
Utilizing Technology
- Implement material handling systems such as conveyors, robots, and automation to streamline processes.
- Utilize inventory management software to track and manage stock levels effectively.
- Integrate barcode scanners and RFID technology for accurate and efficient tracking of materials.
- Explore new technologies such as drones and autonomous vehicles for advanced material handling solutions.
By incorporating these best practices into material handling processes, businesses can enhance their operations, reduce costs, and increase overall efficiency.
Challenges in Material Handling
The common challenges faced in material handling processes
Material handling processes face several common challenges that can disrupt efficiency.
Equipment failure often leads to delays and increased costs.
Regular maintenance is essential to prevent unexpected breakdowns.
Without proper maintenance, organizations risk costly downtime.
Another significant challenge is the lack of training for employees.
When workers are not adequately trained, they may struggle to use equipment safely and effectively.
This can result in accidents and damage to materials.
Providing thorough training programs helps employees understand best practices and safety protocols.
Inefficient layout of storage areas also presents challenges.
A poorly designed layout can cause unnecessary delays in retrieving materials.
Workers may waste time navigating through cluttered or disorganized spaces.
Conducting regular assessments of the layout can help identify areas for improvement.
Issues such as equipment failure, lack of training, and inefficient layout
Additionally, communication issues can hinder material handling processes.
When team members do not communicate effectively, they may misplace items or overlook important tasks.
Implementing clear communication channels fosters collaboration and reduces errors.
Supply chain disruptions can further complicate material handling.
Unexpected delays in receiving materials can lead to inventory shortages.
Companies must develop contingency plans to manage these disruptions effectively.
Transform Your Career Today
Unlock a personalized career strategy that drives real results. Get tailored advice and a roadmap designed just for you.
Start NowMoreover, safety concerns are prevalent in material handling.
Workers are often exposed to heavy lifting, which increases the risk of injuries.
Organizations must prioritize safety training and ergonomics to protect employees.
All in all, addressing these challenges is crucial for efficient material handling.
Organizations can enhance productivity by investing in equipment maintenance, training, layout optimization, communication, and safety.
Proactively managing these challenges ensures smoother material handling processes, ultimately leading to better operational outcomes.
Case Studies
Real-life examples of companies that have successfully implemented efficient material handling processes
Many companies have successfully implemented efficient material handling processes, achieving significant improvements.
One notable example is Toyota.
Toyota adopted a just-in-time (JIT) inventory system to minimize waste and streamline production.
This approach increased productivity by reducing inventory holding costs and enhancing cash flow.
Amazon is another great case study.
The company utilizes advanced robotics in its fulfillment centers.
These robots transport items quickly, reducing the time employees spend moving materials.
As a result, Amazon has improved order fulfillment speed and accuracy, leading to increased customer satisfaction.
The results they achieved in terms of productivity, cost savings, and employee safety
In the automotive industry, Ford has revamped its material handling processes by using automated guided vehicles (AGVs).
These AGVs transport parts to assembly lines efficiently, minimizing downtime.
Ford reported a 25% increase in production efficiency and significant cost savings due to reduced labor requirements.
Walmart also exemplifies effective material handling.
The retail giant employs a centralized distribution model, allowing for streamlined inventory management.
This model reduces transportation costs and ensures products reach stores more quickly.
Transform Your Career Today
Unlock a personalized career strategy that drives real results. Get tailored advice and a roadmap designed just for you.
Start NowWalmart has achieved substantial savings and enhanced overall supply chain efficiency.
Moreover, Coca-Cola implemented a comprehensive training program for employees involved in material handling.
This initiative emphasized safe lifting techniques and proper equipment usage.
As a result, Coca-Cola experienced a marked decrease in workplace injuries, enhancing employee safety and morale.
These real-life examples demonstrate that implementing efficient material handling processes yields remarkable benefits.
Companies achieve increased productivity, substantial cost savings, and improved employee safety.
Organizations can enhance their operations by learning from these successful case studies.
ConclusionÂ
Material handling processes play a crucial role in the efficiency and cost-effectiveness of operations.
By understanding the key elements such as proper storage, efficient transportation, and streamlined workflows, businesses can ensure smoother operations.Â
It is imperative for readers to prioritize efficient material handling processes in their own operations to improve productivity, reduce waste, and ultimately save costs.
Embracing technology and automation can also help in optimizing these processes for better results.Â
By focusing on continuous improvement and investing in training for employees, organizations can achieve better outcomes in terms of safety, quality, and overall operational performance.
Effective material handling processes are the backbone of successful businesses and can make a significant impact on the bottom line.