Introduction
The Importance of Troubleshooting Skills for Industrial Machinery Mechanics
Troubleshooting skills are crucial for industrial machinery mechanics, serving as the backbone of effective maintenance and repair.
These skills ensure that mechanics can quickly identify and resolve issues, which is vital for maintaining the efficiency and productivity of industrial operations.
Proficiency in troubleshooting minimizes downtime, reduces repair costs, and helps prevent minor problems from escalating into major issues.
By mastering these skills, mechanics contribute significantly to the overall reliability and performance of machinery, which directly impacts the success of industrial processes.
The Complexity of Industrial Machinery and the Necessity of Being Able to Troubleshoot Issues Quickly and Effectively
Industrial machinery is increasingly complex, incorporating advanced technologies and intricate systems.
This complexity demands that mechanics possess a high level of troubleshooting skill to address problems swiftly and effectively.
Rapid and accurate diagnostics are essential to minimize disruptions and maintain operational flow.
As machinery technology evolves, the need for proficient troubleshooting becomes even more critical.
Mechanics must be prepared to handle sophisticated systems and respond to emerging challenges with agility and expertise to ensure continuous and efficient operation.
Understanding the Machinery
The Different Types of Industrial Machinery That Mechanics May Work On
Industrial machinery includes a variety of equipment, each with specific functions and components.
Mechanics may work on pumps, conveyors, motors, and presses.
Each machine type presents unique challenges and requires specialized knowledge.
Pumps are essential for transferring fluids.
Mechanics need to understand the distinctions between centrifugal and positive displacement pumps.
Issues such as cavitation or seal leaks require an in-depth grasp of pump operations.
Conveyors are critical for material handling across industries.
Mechanics should be familiar with belt conveyors, roller conveyors, and chain conveyors.
Troubleshooting problems like misalignment or belt slippage demands knowledge of conveyor systems.
Motors drive almost all machinery.
Mechanics must differentiate between AC and DC motors and their control systems.
Diagnosing electrical issues, such as short circuits or burned-out windings, requires detailed motor knowledge.
Presses, used for shaping or cutting, come in mechanical and hydraulic types.
Mechanics need expertise in both.
Hydraulic presses involve understanding fluid dynamics, while mechanical presses require knowledge of gears and levers.
The Need for a Deep Understanding of How Each Machine Operates in Order to Effectively Troubleshoot Problems
A deep understanding of machinery is crucial for effective troubleshooting.
Each type of equipment operates based on different principles and components.
Mechanics must thoroughly understand these principles to diagnose issues accurately.
Studying manuals and schematics is essential for gaining this knowledge.
Mechanics should be familiar with common issues and their symptoms for each machine type.
Regular training and hands-on practice are vital for developing a comprehensive understanding.
Without detailed knowledge, troubleshooting becomes a matter of guesswork.
An informed mechanic can systematically approach problems, identifying the root cause rather than merely addressing symptoms.
Understanding machinery also supports preventive maintenance.
Mechanics can predict and address potential issues before they cause significant downtime.
This proactive strategy helps reduce operational costs and ensures smoother machine operation.
Basically, a mechanic‘s deep understanding of pumps, conveyors, motors, and presses is essential.
This knowledge not only aids in troubleshooting but also in preventing future problems.
Mastery of machinery details equips mechanics to handle issues swiftly and efficiently.
Read: CAD Technician vs. Draftsman: Key Differences
Developing Problem-Solving Techniques
The Importance of Developing a Systematic Approach to Troubleshooting
A systematic approach to troubleshooting is crucial for solving mechanical problems efficiently.
This method ensures that mechanics address issues in a logical sequence, minimizing the risk of overlooking critical details.
Starting with a clear understanding of the machine‘s normal operation is fundamental.
Mechanics should gather information on the specific symptoms and issues reported.
This initial step helps in forming a hypothesis about potential causes.
Next, mechanics need to check for obvious problems before diving into more complex diagnostics.
Simple issues, such as loose connections or visible wear, are often the cause.
Addressing these first can save time and effort.
Once simple issues are ruled out, mechanics should use diagnostic tools to examine more intricate components.
Systematic testing and measurement help in pinpointing the exact fault.
Following a structured process reduces errors and increases troubleshooting efficiency.
Documentation of each step taken during troubleshooting is also essential.
This practice not only helps in the current repair but also aids in refining the problem-solving approach for future issues.
The Value of Keeping a Log of Previous Issues and Solutions for Reference
Maintaining a log of previous issues and solutions offers significant benefits.
A well-kept log serves as a valuable reference for diagnosing recurring problems and identifying patterns.
Recording details of each issue, including symptoms, diagnostics, and resolutions, provides insights into common failures.
This historical data helps in predicting and preventing similar problems in the future.
A log also assists in evaluating the effectiveness of different troubleshooting techniques.
Mechanics can review past solutions to determine which methods were successful and which were not.
This review process helps in refining their problem-solving strategies.
Moreover, a log can be a valuable training tool for new mechanics.
It provides real-world examples of issues and resolutions, helping them understand practical troubleshooting approaches.
In short, developing a systematic approach to troubleshooting is vital for effective problem resolution.
Mechanics should follow a logical sequence of steps, from understanding the machine‘s operation to using diagnostic tools.
Keeping a detailed log of past issues and solutions enhances this process, offering valuable insights and improving overall troubleshooting efficiency.
Read: CAD Technician Certification: What You Need to Know
Utilizing Diagnostic Tools
The Various Diagnostic Tools Commonly Used by Industrial Machinery Mechanics
Diagnostic tools are essential for industrial machinery mechanics to accurately identify and resolve issues.
These tools range from basic to advanced, each serving a specific purpose in the troubleshooting process.
- Multimeters: Multimeters measure electrical parameters such as voltage, current, and resistance.
Mechanics use them to test electrical circuits, ensuring components are functioning within their specified ranges.
They are crucial for diagnosing electrical faults and confirming power supply issues. - Oscilloscopes: Oscilloscopes visualize electrical signals over time.
They allow mechanics to analyze waveforms, which helps in diagnosing complex electrical problems.
For instance, oscilloscopes can detect irregularities in motor signals or power supply fluctuations. - Infrared Thermometers: Infrared thermometers measure surface temperatures from a distance.
Mechanics use them to identify overheating components or check temperature variations across machinery.
This tool is especially useful for spotting issues in electrical panels or rotating equipment. - Vibration Analyzers: Vibration analyzers assess the vibration patterns of machinery.
Mechanics use them to detect misalignments, unbalanced components, or wear in rotating parts.
By analyzing vibration data, they can predict potential failures and prevent costly breakdowns. - Ultrasonic Sensors: Ultrasonic sensors detect sound waves above the human hearing range.
Mechanics use these to identify leaks, cracks, or defective components.
For example, ultrasonic sensors can locate air or fluid leaks in pressurized systems. - Pressure Gauges: Pressure gauges measure the pressure within a system.
Mechanics use them to ensure that hydraulic or pneumatic systems are operating at correct pressures.
Abnormal pressure readings can indicate blockages or faulty components. - Alignment Tools: Alignment tools, such as laser alignment systems, ensure machinery components are correctly aligned.
Proper alignment is crucial for preventing excessive wear and improving efficiency.
Mechanics use these tools to align shafts, belts, and other components accurately.
Examples of How These Tools Can Help Pinpoint Issues More Efficiently
Diagnostic tools significantly enhance the efficiency of pinpointing issues in industrial machinery.
For instance, using a multimeter can quickly reveal a faulty electrical connection or a broken wire, which might be the root cause of a machine’s malfunction.
An oscilloscope can help diagnose complex issues by displaying the electrical signal waveform of a motor.
If the waveform is irregular, it can indicate problems such as a failing motor driver or signal interference.
Infrared thermometers allow mechanics to detect overheating components without physical contact.
If a motor or bearing is running hotter than usual, it can signal an internal problem that needs addressing, such as excessive friction or lubrication failure.
Vibration analyzers can identify imbalances or misalignments in rotating equipment.
For example, if a pump shows abnormal vibration patterns, mechanics can use this data to adjust the alignment or replace worn bearings, thus preventing a potential breakdown.
Ultrasonic sensors can locate leaks in a compressed air system by detecting the high-frequency sound of escaping air.
Addressing these leaks promptly can prevent loss of efficiency and reduce operational costs.
Finally, pressure gauges help ensure that hydraulic systems maintain the correct pressure.
If a gauge shows unusually low or high pressure, it can indicate a blockage or a failing pump, allowing mechanics to take corrective action before a major failure occurs.
Generally, utilizing diagnostic tools like multimeters, oscilloscopes, and infrared thermometers greatly improves the efficiency of troubleshooting.
These tools provide valuable data and insights, enabling mechanics to identify and resolve issues more accurately and quickly.
Read: Day in the Life of a CAD Technician
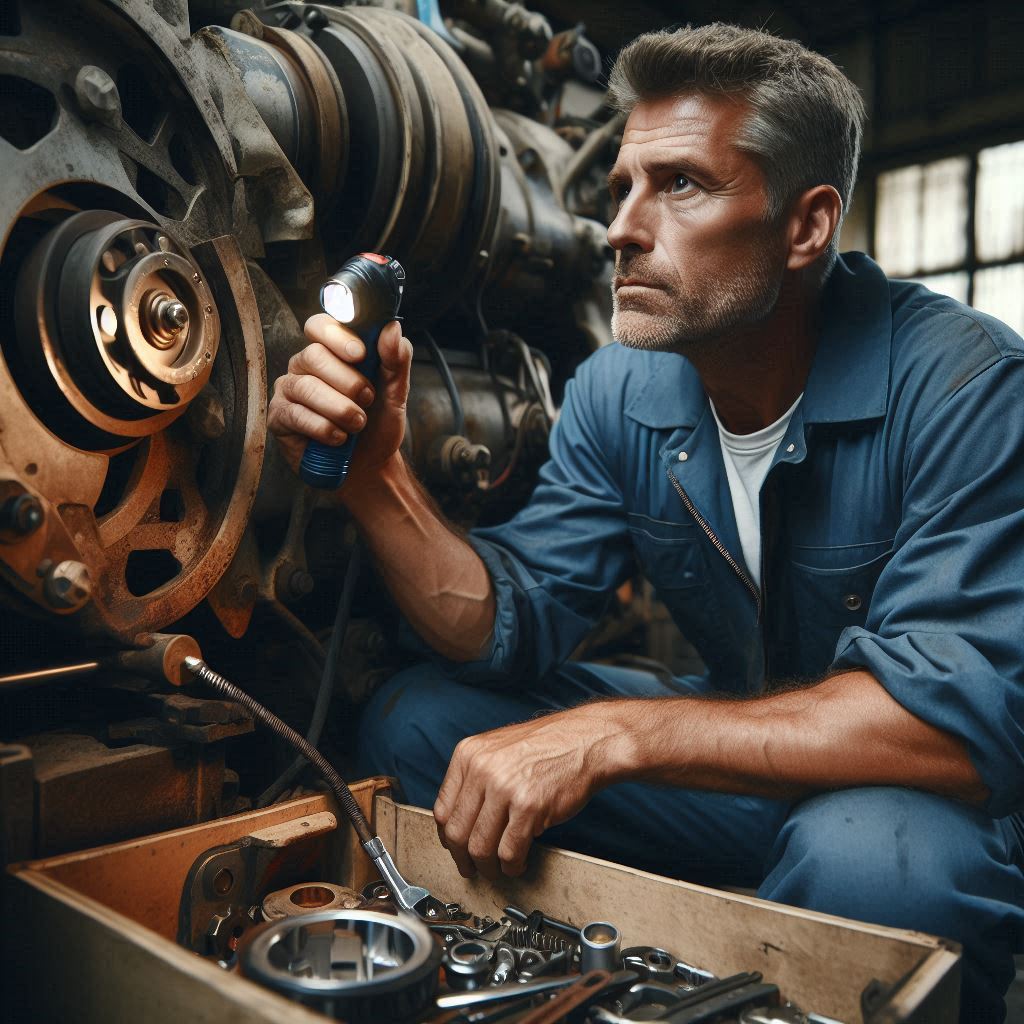
Communication Skills
The Significance of Effective Communication with Colleagues and Supervisors When Troubleshooting Machinery
Effective communication is crucial for successful machinery troubleshooting.
Clear and concise interactions with colleagues and supervisors ensure that everyone involved understands the issues and the steps being taken to resolve them.
Mechanics often work as part of a team, where sharing information about machinery problems and solutions is vital.
Clear communication helps in coordinating efforts, avoiding redundant actions, and leveraging collective expertise.
For instance, explaining the symptoms and suspected causes of a malfunction allows team members to contribute their insights and solutions.
Additionally, communicating with supervisors is essential for aligning troubleshooting efforts with operational priorities.
Supervisors can provide context about the impact of machinery issues on production schedules and resource allocation.
This information helps mechanics prioritize tasks and focus on solutions that align with overall business goals.
Effective communication also fosters a collaborative environment where feedback is welcomed.
Mechanics should be open to discussing their findings and seeking input from more experienced colleagues.
This exchange of ideas can lead to more innovative and efficient troubleshooting methods.
The Importance of Documenting Findings and Communicating Recommendations Clearly
Documenting findings and communicating recommendations clearly is crucial for several reasons.
Proper documentation provides a record of the issues encountered, the steps taken to resolve them, and the outcomes.
This record is invaluable for future reference, helping mechanics understand recurring problems and improve their troubleshooting strategies.
Clear documentation also ensures that others who may work on the same machinery in the future can follow the resolution process.
It includes details such as symptoms, diagnostic results, repairs performed, and any parts replaced.
This comprehensive information supports continuity and reduces the likelihood of repetitive troubleshooting efforts.
When communicating recommendations, clarity is key.
Mechanics should provide precise and actionable recommendations based on their findings.
This involves detailing any repairs needed, parts that should be replaced, or adjustments that should be made.
Clear recommendations help supervisors and team members understand the necessary actions and make informed decisions.
In addition, effective communication of recommendations helps in planning maintenance schedules and budgeting for repairs.
For example, if a mechanic identifies a potential issue that could lead to a major failure, communicating this proactively allows the team to address it before it escalates.
In fact, effective communication with colleagues and supervisors enhances teamwork and ensures that troubleshooting efforts are well-coordinated.
Documenting findings thoroughly and clearly communicating recommendations helps in creating a reliable record of issues and solutions, facilitating future troubleshooting and maintenance tasks.
Read: Top CAD Software for Aspiring CAD Technicians
See Related Content: Day in the Life of a Computer Engineering Student
Safety Considerations
The Need for Following Safety Protocols When Troubleshooting Industrial Machinery
Following safety protocols is paramount when troubleshooting industrial machinery.
Adhering to these protocols helps prevent accidents, injuries, and equipment damage.
Safety protocols are designed to protect both the technician and the machinery, ensuring a safe working environment.
Before starting any troubleshooting work, it’s essential to perform a thorough risk assessment.
Identify potential hazards associated with the machinery, such as moving parts, electrical components, and high-pressure systems.
Understanding these risks allows technicians to take appropriate precautions.
Lockout/tagout procedures are critical for ensuring safety.
Before working on any machinery, ensure that the power source is turned off and securely locked out.
Tag the equipment to indicate that maintenance work is in progress.
This prevents accidental reactivation and reduces the risk of electrical shocks or mechanical injuries.
Personal protective equipment (PPE) is another vital aspect of safety.
Wear appropriate PPE such as safety goggles, gloves, helmets, and ear protection based on the specific risks of the job.
PPE helps protect against flying debris, sharp edges, and loud noise, contributing to overall safety.
Following manufacturer guidelines and safety manuals is crucial.
These documents provide specific instructions and safety recommendations for each piece of equipment.
Familiarizing yourself with these guidelines ensures that troubleshooting is performed correctly and safely.
Tips for Ensuring Personal Safety While Working on Potentially Hazardous Equipment
Ensuring personal safety while working on hazardous equipment involves several key practices:
- Use Proper Tools: Always use the correct tools for the job. Using improper tools can lead to accidents or damage to the equipment.
For example, use insulated tools when working on electrical components to prevent shocks. - Maintain a Clean Work Area: Keep the work area clean and free of obstacles.
A cluttered workspace increases the risk of tripping or accidentally contacting moving parts. Ensure that tools and equipment are organized and readily accessible. - Be Aware of Moving Parts: When working on machinery with moving parts, stay alert and avoid placing your hands or body near these areas.
Use tools or equipment to make adjustments rather than direct contact whenever possible. - Follow Safe Lockout Procedures: Always follow lockout/tagout procedures to ensure that machinery is completely de-energized before starting work.
This step is crucial for preventing accidental machine start-ups and protecting against electrical or mechanical hazards. - Check for Residual Energy: Before beginning work, check for and safely discharge any residual energy, such as hydraulic pressure or electrical charges.
This precaution helps prevent unexpected releases of energy that could cause injury. - Stay Hydrated and Rested: Working while fatigued or dehydrated can impair your judgment and coordination.
Ensure you are well-rested and hydrated to maintain alertness and effectiveness while troubleshooting. - Communicate Clearly: Ensure that you communicate clearly with your team and supervisors about the status of the machinery and any potential hazards.
Clear communication helps coordinate safety measures and avoid misunderstandings.
In general, adhering to safety protocols and employing personal safety measures are essential when troubleshooting industrial machinery.
By following risk assessments, lockout/tagout procedures, and using proper PPE, technicians can significantly reduce the risk of accidents and ensure a safer working environment.
Explore Further: Pros and Cons of Being an Automotive Engineer
See Related Content: Educational Requirements for Lab Technicians
Transform Your Career Today
Unlock a personalized career strategy that drives real results. Get tailored advice and a roadmap designed just for you.
Start NowExplore Further: Top Industries Hiring Data Scientists in 2024
Continuous Learning
Encouraging Industrial Machinery Mechanics to Stay Updated on the Latest Technologies and Best Practices in the Field
In the ever-evolving field of industrial machinery, staying updated on the latest technologies and best practices is crucial.
Technology advances rapidly, and new machinery and diagnostic tools frequently emerge.
Mechanics who remain informed about these developments can enhance their troubleshooting skills and efficiency.
Modern machinery often incorporates advanced technologies such as IoT sensors, AI-based diagnostics, and automation systems.
Understanding these innovations allows mechanics to adapt quickly to new equipment and methods.
Staying updated helps in diagnosing issues more accurately and applying the most effective solutions.
Additionally, keeping abreast of industry trends and best practices ensures that mechanics follow the most current safety standards and operational guidelines.
This knowledge helps in implementing improved techniques and avoiding outdated practices that could lead to inefficiencies or safety risks.
Mechanics should regularly read industry publications, follow relevant blogs, and participate in online forums.
Engaging with these resources keeps them informed about new technologies and best practices.
This proactive approach to learning fosters continuous improvement and helps mechanics stay competitive in their field.
Attending Workshops and Training Sessions to Improve Troubleshooting Skills
Attending workshops and training sessions is a valuable way for industrial machinery mechanics to enhance their troubleshooting skills.
These events provide hands-on experience and insights into the latest techniques and technologies.
Workshops often focus on specific aspects of machinery maintenance and troubleshooting.
They offer practical exercises and demonstrations, allowing mechanics to learn new skills and refine existing ones.
For example, a workshop on vibration analysis might teach mechanics how to use advanced tools and interpret data more effectively.
Training sessions led by industry experts offer in-depth knowledge of emerging technologies and best practices.
Mechanics can gain a deeper understanding of new diagnostic tools, advanced machinery, and innovative repair techniques.
This training helps them stay current with industry standards and improve their overall problem-solving capabilities.
Furthermore, these events provide networking opportunities with other professionals in the field.
Sharing experiences and learning from peers can offer new perspectives and solutions to common challenges.
Networking can also open doors to additional resources and support.
In summary, continuous learning is essential for industrial machinery mechanics to keep up with technological advancements and best practices.
Regularly updating knowledge through industry resources and attending workshops and training sessions enhances troubleshooting skills and ensures effective maintenance practices.
Embracing a mindset of ongoing education helps mechanics stay proficient and competitive in their field.
Conclusion
The Key Points Discussed in the Blog Post
Troubleshooting skills are vital for industrial machinery mechanics.
Effective troubleshooting involves accurate diagnosis, swift resolution, and preventive maintenance.
We covered essential methods such as systematic inspection, root cause analysis, and leveraging technology for efficient problem-solving.
Mechanics must remain adept with the latest tools and techniques to address complex issues effectively.
Continuous learning and hands-on practice are crucial for staying current and improving diagnostic accuracy.
The Importance of Troubleshooting Skills for Industrial Machinery Mechanics and the Value of Continuous Improvement in This Area
Troubleshooting skills directly impact operational efficiency and equipment longevity.
By developing these skills, mechanics can minimize downtime, reduce repair costs, and enhance overall productivity.
Regular training and professional development play a significant role in mastering these techniques.
Emphasizing troubleshooting skills fosters a proactive approach to maintenance and repair.
This ongoing commitment to improvement ensures that mechanics can address emerging challenges with confidence and precision.
Investing in these skills not only benefits individual mechanics but also contributes to the broader success of industrial operations.