Introduction
Industrial machinery mechanics play a vital role in various industries by ensuring equipment operates efficiently.
They maintain, repair, and troubleshoot machinery to prevent disruptions.
Without their expertise, many industries would face significant operational challenges and downtime.
Tools are essential for industrial machinery mechanics to perform their duties effectively.
Each tool serves a specific purpose, enabling mechanics to complete tasks accurately and efficiently.
For instance, wrenches and sockets are crucial for tightening and loosening bolts.
Screwdrivers and pliers assist in assembling and disassembling machinery components.
Multimeters help diagnose electrical issues, ensuring proper functionality of electrical systems.
Mechanics rely on diagnostic tools to identify problems quickly.
These tools include vibration analyzers and thermal imaging cameras, which detect issues before they escalate.
Calibration tools ensure that machinery operates within required specifications, improving performance and longevity.
A well-equipped toolkit enhances a mechanic’s ability to address various challenges encountered daily.
Precision tools enable accurate repairs, while general-purpose tools support routine maintenance tasks.
Having the right tools not only improves efficiency but also reduces the risk of damage to machinery.
Overall, the importance of tools in the daily work of industrial machinery mechanics cannot be overstated.
Basic hand tools
Essential Hand Tools for Industrial Machinery Mechanics
Industrial machinery mechanics rely on a variety of hand tools to perform their tasks efficiently.
Each tool serves a specific purpose and is essential for different types of repairs and maintenance.
Wrenches are fundamental for turning bolts and nuts.
Mechanics use adjustable wrenches for versatile applications and socket wrenches for tight spaces.
Pliers come in various types, including needle-nose for precision work and slip-joint for gripping.
Screwdrivers are crucial for inserting and removing screws.
Mechanics should have a set with different sizes and types, such as flathead and Phillips.
Hammers are used for striking and shaping parts.
Mechanics use ball-peen hammers for metalworking and rubber mallets for non-marring tasks.
Sockets and ratchets are vital for quickly loosening and tightening fasteners.
They provide leverage and efficiency, especially in confined spaces.
Allen wrenches or hex keys are necessary for bolts with hexagonal sockets.
Torque wrenches ensure that fasteners are tightened to the correct specifications, preventing damage and ensuring safety.
Importance of High-Quality Hand Tools
Using high-quality hand tools is essential for both efficiency and safety.
Durable tools perform better and last longer, reducing the need for frequent replacements.
High-quality tools also enhance precision, which is critical for effective machinery repair and maintenance.
Poor-quality tools can lead to stripped bolts, damaged components, and unsafe working conditions.
Investing in well-made tools can also improve overall productivity.
Reliable tools minimize downtime and increase the speed of repairs.
For example, a high-quality wrench or screwdriver will grip more securely and require less force, making tasks easier and faster.
Additionally, high-quality tools often come with better ergonomic designs, reducing the risk of strain and injury.
Tips for Maintaining and Organizing Hand Tools
Proper maintenance and organization of hand tools are crucial for a well-functioning workshop.
Start by regularly cleaning tools after use to remove dirt and debris.
This prevents rust and keeps tools in good working condition.
Apply lubrication to moving parts to ensure smooth operation and longevity.
Organize tools systematically in a designated workspace.
Use toolboxes, pegboards, or drawer organizers to keep everything in its place.
Labeling tool areas can help quickly locate the necessary tools and reduce time spent searching.
Regularly inspect tools for damage or wear and replace them as needed to maintain safety and effectiveness.
Store tools properly when not in use.
Keep them in a dry, clean environment to prevent corrosion and damage.
Ensure that all tools are returned to their proper storage locations after use to maintain organization and readiness for the next task.
Read: Top CAD Software for Aspiring CAD Technicians
Power Tools
Overview of Common Power Tools for Industrial Machinery Mechanics
Industrial machinery mechanics rely on a variety of power tools to perform their tasks efficiently.
Understanding these tools and their proper use is essential for effective maintenance and repair.
Drills
Drills are versatile tools used for creating holes and driving screws.
They come in various types, including corded and cordless.
Mechanics use drills to handle tasks ranging from assembling machinery to making precise adjustments.
Grinders
Grinders are essential for cutting, grinding, and polishing metal parts.
Angle grinders, in particular, are useful for removing excess material and sharpening tools.
They provide powerful performance for heavy-duty tasks.
Impact Wrenches
Impact wrenches deliver high torque to loosen or tighten bolts quickly.
These tools are crucial for tasks requiring substantial force, such as assembling or disassembling large machinery components.
They save time and effort compared to manual wrenches.
Saws
Saws, such as reciprocating saws and circular saws, are used for cutting metal and other materials.
They offer precision and speed, making them indispensable for modifying machinery components.
Air Compressors
Air compressors power pneumatic tools like impact wrenches and grinders.
They provide a reliable source of compressed air for various tasks, ensuring consistent tool performance.
Advantages of Power Tools for Heavy-Duty Tasks
Power tools offer several advantages for heavy-duty tasks.
They significantly increase efficiency and reduce manual effort, allowing mechanics to complete tasks faster.
The high torque and power of tools like impact wrenches enable mechanics to handle stubborn bolts and heavy components with ease.
Power tools also improve precision and consistency in tasks such as drilling and cutting, which enhances overall quality and safety.
By reducing the physical strain on mechanics, power tools contribute to a safer and more comfortable work environment.
Safety Precautions and Proper Usage Guidelines
Using power tools safely is crucial to prevent accidents and ensure effective operation.
Always read the manufacturer’s instructions before using any tool.
Wear appropriate personal protective equipment (PPE), including safety glasses, gloves, and hearing protection.
Ensure that tools are properly maintained and inspected before each use to avoid malfunctions.
Keep work areas clean and free of hazards to prevent slips and falls.
Never bypass safety guards or use damaged tools, as these can lead to serious injuries.
Always disconnect power sources when changing accessories or performing maintenance on the tools.
Proper training on the use and maintenance of power tools is essential.
Mechanics should be familiar with each tool’s operating procedures and safety features.
Regular training and adherence to safety guidelines help in maintaining a safe work environment and extending the life of the tools.
Read: How to Become a CAD Technician: Step-by-Step Guide
Diagnostic tools
Diagnostic Tools for Troubleshooting Machinery Issues
Industrial machinery mechanics rely on various diagnostic tools to troubleshoot machinery issues effectively.
Multimeters are essential for measuring electrical properties like voltage, current, and resistance.
Mechanics use multimeters to test circuits and identify electrical faults.
Thermal imagers help detect overheating components by capturing temperature variations.
These devices are crucial for spotting potential failures before they become critical.
Vibration analyzers assess machinery vibrations to identify imbalances, misalignments, or worn bearings.
By analyzing vibration patterns, mechanics can pinpoint mechanical issues and prevent costly downtime.
Each of these tools plays a vital role in diagnosing and addressing problems in complex machinery systems.
Importance of Accurate Diagnostic Tools
Accurate diagnostic tools are crucial for identifying problems quickly and precisely.
Using the right tools allows mechanics to detect issues early, reducing the risk of equipment failure.
For example, a multimeter provides exact readings that help diagnose electrical faults accurately.
Thermal imagers reveal hidden problems like overheating components, which might not be visible otherwise.
Vibration analyzers offer detailed insights into mechanical health, preventing potential breakdowns.
Accurate diagnostics lead to timely repairs, improving machinery reliability and extending equipment lifespan.
Reliable tools ensure that mechanics can address issues effectively, minimizing downtime and maintaining smooth operations.
Training and Certification Requirements
To use diagnostic tools effectively, mechanics need proper training and certification.
Training programs focus on the correct use of tools, interpretation of data, and troubleshooting techniques.
For instance, courses on multimeter usage cover safety procedures, measurement techniques, and common issues.
Thermal imager training includes understanding thermal patterns and interpreting thermal data.
Vibration analysis training teaches how to recognize vibration signatures and diagnose mechanical problems.
Certification programs often include hands-on experience and assessments to ensure proficiency.
Mechanics may need certifications from industry-recognized organizations or manufacturers to demonstrate their expertise.
Proper training and certification ensure that mechanics can utilize diagnostic tools to their full potential, enhancing their ability to maintain and repair machinery efficiently.
Diagnostic tools like multimeters, thermal imagers, and vibration analyzers are essential for troubleshooting machinery issues.
Accurate tools help mechanics identify problems quickly and precisely, leading to timely repairs and improved equipment reliability.
Effective use of these tools requires specialized training and certification, which ensure that mechanics can perform their tasks with confidence and skill.
Read: Surveying and Mapping Technician Internships: A Guide
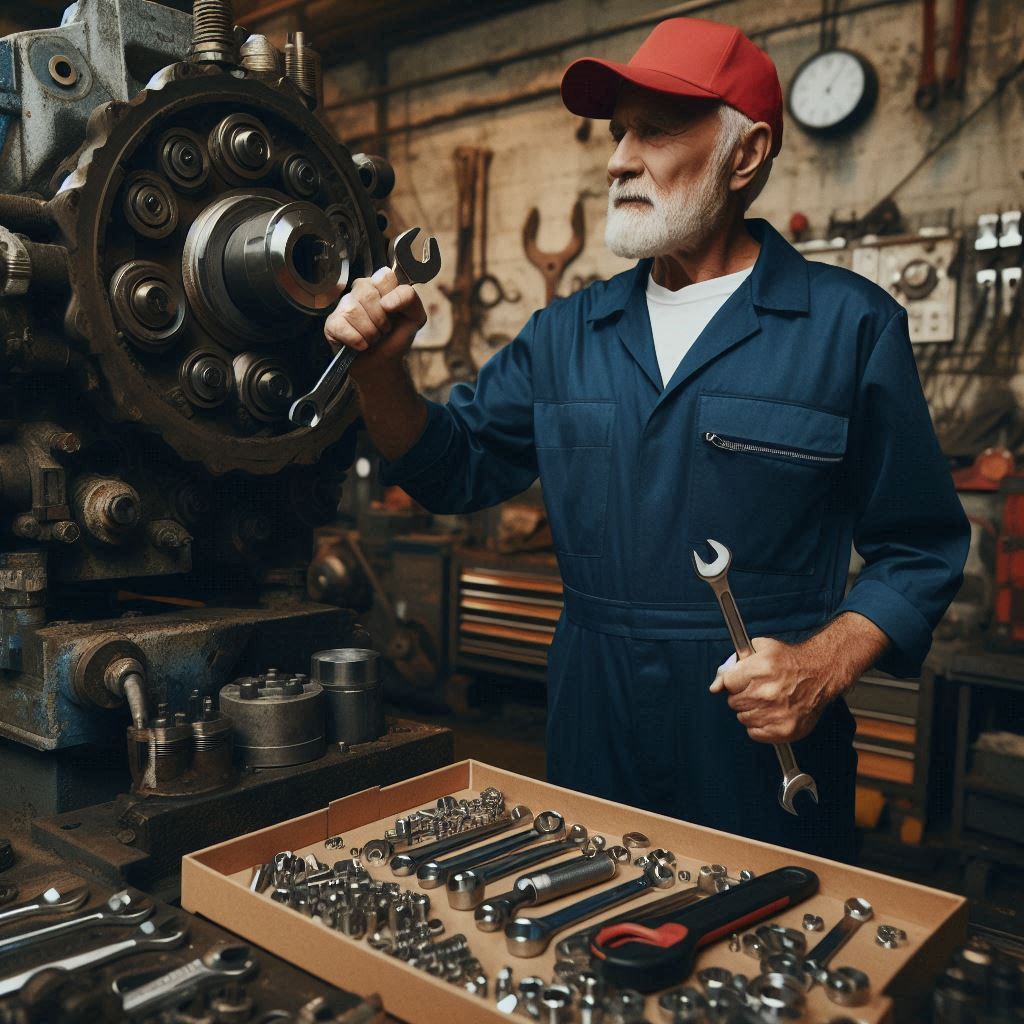
Specialized tools
Industrial machinery mechanics often require specialized tools to perform specific tasks or maintain certain types of machinery.
These tools are designed to meet the unique needs of specific industries or machinery types.
Let’s delve into an overview of specialized tools, examples of commonly used ones, and suggestions for acquiring these tools.
Overview of specialized tools
Overview of Specialized Tools for Industrial Machinery Mechanics
Transform Your Career Today
Unlock a personalized career strategy that drives real results. Get tailored advice and a roadmap designed just for you.
Start NowIndustrial machinery mechanics use a range of specialized tools designed for specific industries or types of machinery.
These tools help perform precise tasks and ensure machinery operates efficiently.
Specialized tools address unique needs in various machinery types, from heavy-duty equipment to intricate components.
Using the right tool for the job is crucial for maintaining machinery and preventing damage.
Understanding which tools are best suited for specific applications enhances both efficiency and safety.
Mechanics must be knowledgeable about these tools to perform their jobs effectively.
Examples of Specialized Tools
Several specialized tools are essential for industrial machinery maintenance:
- Torque Wrenches: These tools ensure that bolts and nuts are tightened to the manufacturer’s specifications.
Accurate torque application prevents over-tightening and equipment damage. - Bearing Pullers: Bearing pullers are used to remove bearings from shafts or housings without damaging surrounding components.
- Alignment Tools: Proper alignment tools, such as laser alignment systems, help align shafts and other components accurately.
- Calipers and Micrometers: These tools measure component dimensions with high precision, ensuring parts meet exact specifications and fit correctly.
- Vibration Analyzers: These tools diagnose issues by measuring vibrations in machinery.
They help detect imbalances, misalignments, and other problems that could lead to failure. - Hydraulic Jacks: Hydraulic jacks are used to lift heavy machinery safely, providing access for maintenance and repairs.
Each of these tools plays a critical role in maintaining machinery performance and reliability.
Proper use of specialized tools can prevent costly downtime and extend the life of equipment.
Acquiring Specialized Tools Through Training and Experience
Mechanics can acquire the skills needed to use specialized tools through various training programs and on-the-job experience.
Many vocational schools and community colleges offer courses in industrial machinery maintenance that include training on these tools.
These programs provide hands-on experience and knowledge of tool operation, maintenance techniques, and safety procedures.
On-the-job training is also valuable for gaining practical experience.
Working alongside experienced mechanics allows newcomers to learn the nuances of using specialized tools in real-world scenarios.
Employers often provide training sessions or workshops to keep mechanics updated on new tools and technologies.
Additionally, certifications in machinery maintenance or specific tools can enhance a mechanic’s expertise and job prospects.
Pursuing certification programs that focus on specialized tools demonstrates commitment and proficiency in the field.
Specialized tools are essential for effective industrial machinery maintenance.
Tools like torque wrenches, bearing pullers, and alignment tools help ensure machinery operates efficiently and safely.
Mechanics can gain proficiency in using these tools through formal training programs and hands-on experience, which is crucial for career development and effective machinery maintenance.
Read: Impact of Drones on Surveying and Mapping
Tool Maintenance and Calibration
Importance of Regularly Maintaining and Calibrating Tools
Maintaining and calibrating tools is crucial for ensuring their accuracy and longevity.
Regular maintenance prevents tool malfunctions and inaccuracies.
Calibration ensures that tools provide precise measurements, which is vital for machinery repair and maintenance.
Without proper calibration, tools can produce unreliable readings, leading to incorrect adjustments and potential equipment damage.
Routine maintenance also extends the lifespan of your tools.
Well-maintained tools function better and require fewer repairs.
Regular checks can identify minor issues before they become major problems.
Proper care reduces the risk of unexpected breakdowns, saving time and money in the long run.
Tips for Cleaning, Lubricating, and Storing Tools
Proper cleaning is essential for maintaining tool performance.
After each use, remove debris and residue from tools.
Use a clean cloth or brush to wipe away dust and dirt.
For stubborn grime, apply a mild cleaner, ensuring it is safe for the tool’s material.
Lubrication helps keep moving parts functioning smoothly.
Apply lubricant according to the manufacturer’s recommendations.
Use the right type of lubricant to avoid damaging the tool.
Over-lubrication can attract dirt, while under-lubrication can lead to premature wear.
Storing tools correctly is equally important.
Keep tools in a clean, dry place to prevent rust and corrosion.
Use toolboxes or storage cabinets to protect tools from physical damage.
Hang or place tools in an organized manner to avoid accidental drops and impacts.
Benefits of Investing in Tool Maintenance Programs
Investing in a tool maintenance program offers several benefits.
First, it ensures that tools are regularly inspected and calibrated.
This regular attention keeps tools in top working condition, which improves the quality of work.
A maintenance program can reduce overall repair costs.
By addressing minor issues early, you prevent costly breakdowns and replacements.
Regular maintenance helps avoid downtime, allowing for uninterrupted work processes.
Furthermore, a well-implemented maintenance program enhances tool reliability and safety.
Tools that are regularly checked and serviced are less likely to malfunction during use, reducing the risk of accidents.
Additionally, investing in a maintenance program demonstrates a commitment to quality and professionalism.
It reflects positively on your work ethic and can enhance your reputation in the industry.
Maintaining and calibrating tools is essential for accuracy and longevity.
Regular cleaning, lubricating, and proper storage play key roles in tool care.
Investing in a tool maintenance program provides long-term benefits, including reduced repair costs, increased reliability, and enhanced safety.
By following these practices, you ensure your tools remain in excellent condition, supporting efficient and effective industrial machinery maintenance.
Emerging technologies in tool development
Exploration of New Technologies
New technologies are revolutionizing the toolkit of industrial machinery mechanics.
Smart tools, connected tools, and digital tool management systems are leading this change.
Smart tools come with embedded sensors that provide real-time data on performance and usage.
These tools can alert mechanics to potential issues before they become critical.
Connected tools use wireless technology to transmit data, allowing remote monitoring and diagnostics.
Digital tool management systems help in tracking tool inventory and usage, reducing downtime due to misplaced or malfunctioning tools.
Embracing these advanced tools can significantly enhance maintenance and repair processes.
Advantages of Using Cutting-Edge Tools
Cutting-edge tools offer numerous advantages for increased efficiency and productivity.
Smart and connected tools provide precise data, improving the accuracy of diagnostics and repairs.
Real-time monitoring helps in quickly identifying and addressing issues, reducing downtime.
Digital tool management systems streamline inventory control, ensuring that tools are readily available when needed.
These systems also help in scheduling maintenance, avoiding unnecessary delays.
The use of advanced tools leads to faster and more effective problem-solving, increasing overall productivity.
Moreover, improved accuracy and efficiency contribute to higher quality work and enhanced safety in the workplace.
Challenges and Opportunities in Adapting to New Tool Technologies
Adapting to new tool technologies presents both challenges and opportunities for industrial machinery mechanics.
One challenge is the need for continuous training to stay updated with evolving technologies.
Mechanics must learn how to effectively use and troubleshoot smart and connected tools.
Integrating these new tools into existing workflows may require adjustments and additional planning.
On the other hand, these technologies offer significant opportunities for career growth and skill development.
Mastering new tools can open doors to advanced job roles and higher compensation.
Embracing technological advancements can also lead to greater job satisfaction through more efficient and innovative work processes.
Overall, while adapting to new tool technologies requires effort and learning, the benefits in terms of efficiency and career advancement make it a worthwhile endeavor.
Tool Safety Practices
Importance of Following Safety Protocols and Using Personal Protective Equipment
Following safety protocols and using personal protective equipment (PPE) are critical when working with tools.
Safety protocols ensure that mechanics handle tools correctly and avoid accidents.
PPE, such as gloves, goggles, and helmets, protects against injuries.
Proper use of PPE minimizes the risk of harm from flying debris, sharp edges, and heavy equipment.
Mechanics should always wear the appropriate gear for each task to maintain safety standards.
Adhering to safety guidelines not only protects individuals but also promotes a safer work environment overall.
Training on Proper Tool Handling Techniques
Training on proper tool handling techniques is essential for preventing accidents.
Mechanics should receive instruction on the correct use of each tool.
Understanding how to operate tools safely reduces the risk of injury.
Training programs should cover proper handling, storage, and maintenance of tools.
Mechanics need to learn the right techniques to ensure efficiency and safety.
Regular training updates help mechanics stay informed about new safety practices and tool advancements.
Effective training programs enhance safety awareness and tool management skills.
Preventing Accidents through Proper Tool Use
Proper tool use is crucial in preventing accidents.
Mechanics must use tools for their intended purposes only.
Using a wrench as a hammer or a screwdriver as a chisel can lead to serious injuries.
Always inspect tools before use to ensure they are in good condition.
Damaged or worn tools should be replaced immediately to avoid accidents.
Following manufacturer instructions and safety guidelines helps in using tools correctly.
Proper maintenance and care of tools further reduce the risk of accidents.
Examples of Common Injuries and Accidents
Improper tool use can lead to a variety of injuries.
Cuts and lacerations are common when using sharp tools without gloves.
Eye injuries can occur if protective goggles are not worn during tasks involving flying debris.
Repetitive strain injuries result from improper handling techniques or overuse of tools.
Heavy equipment accidents can happen if tools are used incorrectly or not maintained properly.
These injuries can lead to significant downtime and medical costs, emphasizing the need for strict adherence to safety protocols.
Ensuring a Safe Work Environment
Creating a safe work environment involves consistently following safety protocols and using PPE.
Encourage a culture of safety by promoting regular training and adherence to guidelines.
Regularly inspect and maintain tools to ensure they are safe for use.
Provide adequate PPE and ensure that all team members understand its importance.
By prioritizing safety and proper tool handling, mechanics can prevent accidents and injuries.
A commitment to safety enhances productivity and contributes to a healthier, more efficient workplace.
Following safety protocols, using PPE, and receiving proper training on tool handling are vital for preventing accidents.
Mechanics should always adhere to these practices to ensure a safe work environment and minimize the risk of injury.
Conclusion
Industrial machinery mechanics rely on a variety of essential tools to perform their tasks efficiently.
Wrenches, including adjustable and socket types, are crucial for tightening and loosening bolts and nuts.
Screwdrivers, both flathead and Phillips, are needed for assembling and disassembling machinery components.
Pliers and cutters are necessary for gripping, twisting, and cutting wires and other materials.
Multimeters play a key role in diagnosing electrical issues by measuring voltage, current, and resistance.
Lubrication tools, such as grease guns and oil cans, help maintain smooth operation and prevent wear.
Calibration tools ensure machinery operates within specified parameters, improving accuracy and performance.
Using the right tools for each job is vital for maintaining machinery and ensuring operational efficiency.
Proper tool selection prevents damage to machinery and reduces the risk of errors.
High-quality tools contribute to faster, more accurate repairs and longer-lasting equipment.
The role of tools in industrial machinery mechanics continues to evolve.
Advances in technology introduce digital tools and smart devices that enhance diagnostic capabilities.
Automation and computerized tools streamline maintenance processes, improving precision and efficiency.
Staying current with these developments helps mechanics remain competitive and effective in their roles.