Introduction
Overview of the Importance of Safety Tips for Industrial Machinery Mechanics
Safety tips for industrial machinery mechanics are fundamental for maintaining a secure work environment.
Proper safety practices not only protect the workers but also ensure that machinery operates efficiently.
Implementing these guidelines helps prevent accidents and reduces potential hazards, making the workplace safer and more productive.
The Risks Involved in Working with Industrial Machinery
Working with industrial machinery presents several risks, such as equipment malfunctions, exposure to hazardous materials, and the complexity of mechanical systems.
These risks can lead to serious injuries or accidents if not carefully managed.
The nature of the job demands constant awareness and adherence to safety protocols to avoid potential dangers.
The Significance of Following Safety Guidelines to Prevent Accidents and Injuries
Following safety guidelines is essential for preventing accidents and injuries.
Mechanics must use personal protective equipment and follow established procedures to minimize risks.
Regular maintenance of machinery and ongoing safety training are also critical.
By prioritizing safety and continuously improving practices, workers contribute to a safer environment and help prevent workplace incidents.
Understand the Machinery
Familiarize Yourself with the Specific Machinery You Will Be Working On
Before starting any maintenance or repair work, invest time in understanding the specific machinery you will be handling.
Each piece of equipment has its own unique features and operational characteristics.
Familiarity with these details will help you perform tasks more efficiently and safely.
Recognize that different machines require different handling techniques.
Knowing these specifics minimizes the risk of errors and enhances your overall effectiveness.
The Owner’s Manual and Understand the Proper Operation Procedures
A critical step in ensuring safe and effective machinery operation is reading the owner‘s manual.
The manual provides detailed information about the machine‘s functions and how to operate it properly.
It contains guidelines on routine maintenance, operational limits, and safety procedures.
Thoroughly understanding these procedures is vital to prevent accidents and ensure the equipment runs smoothly.
Make sure to follow these instructions precisely to maintain the machine in optimal condition and avoid unnecessary breakdowns.
Potential Hazards and Risks Associated with the Machinery
Identifying potential hazards and risks associated with the machinery is essential for maintaining a safe working environment.
Hazards can include moving parts, high temperatures, or electrical components.
By recognizing these risks, you can take appropriate precautions to protect yourself and others.
Carefully examine the machine for any warning signs or labels that indicate potential dangers.
Additionally, assess the surrounding environment for possible risks, such as clutter or inadequate ventilation.
Addressing these hazards before starting work ensures a safer and more controlled working environment.
Basically, understanding the machinery involves more than just operating it; it requires a deep awareness of its specifics, adherence to the manufacturer‘s guidelines, and a thorough assessment of potential hazards.
By familiarizing yourself with the machine, reading the owner‘s manual, and identifying risks, you lay a solid foundation for safe and effective maintenance and repair work.
Read: Online Courses for Surveying and Mapping Technicians
Wear Appropriate Safety Gear
Always Wear Personal Protective Equipment Such as Gloves, Goggles, and Steel-Toed Boots
Personal protective equipment (PPE) is essential for ensuring your safety while working with industrial machinery.
Always wear gloves to protect your hands from sharp edges, hot surfaces, and moving parts.
Goggles are crucial for shielding your eyes from debris, sparks, or chemicals.
Steel-toed boots provide vital protection for your feet against heavy objects and accidental impacts.
Proper PPE reduces the risk of injury and helps you work more confidently.
Use Ear Protection If Working in Noisy Environments
In noisy environments, ear protection is a must.
Prolonged exposure to high noise levels can lead to hearing loss and other auditory issues.
Earplugs or earmuffs help reduce noise exposure and protect your hearing.
Always check the noise levels of the environment and choose appropriate ear protection to ensure you stay safe.
Investing in quality ear protection is crucial for preserving your long-term hearing health.
Ensure Clothing Is Not Loose or Dangling, Which Can Get Caught in Machinery
Loose or dangling clothing can pose significant hazards when working with machinery.
Such clothing can easily get caught in moving parts, leading to serious injuries.
Wear snug-fitting clothes that won‘t interfere with the machine’s operation.
Avoid wearing jewelry, ties, or long sleeves that could become entangled.
Ensure that all clothing and accessories are securely fastened to prevent accidents and maintain a safer working environment.
In general, wearing appropriate safety gear is a fundamental practice for industrial machinery mechanics.
Equip yourself with gloves, goggles, and steel-toed boots for protection against physical hazards.
Use ear protection in noisy environments to safeguard your hearing.
Additionally, ensure that your clothing is fitted properly to avoid entanglement with machinery.
By adhering to these safety gear guidelines, you enhance your protection and reduce the risk of workplace injuries.
Read: Surveying and Mapping Technician: Job Satisfaction
Follow Lockout/Tagout Procedures
Before Performing Any Maintenance or Repair Work, Ensure the Machinery Is Properly Shut Off and Tagged Out
Before starting any maintenance or repair work on machinery, always ensure it is properly shut off.
This is a crucial first step in preventing accidental machine startups.
Verify that the equipment is completely powered down and isolated from its energy sources.
Tagging out the machine informs others that it is being serviced.
This procedure helps prevent unintended operation and reduces the risk of accidents.
Use Lockout Devices to Prevent Accidental Startup of Machinery
After shutting off the machinery, use lockout devices to secure it.
Lockout devices physically prevent the machinery from being turned on while maintenance is in progress.
These devices are designed to keep energy sources isolated and ensure that machinery cannot be restarted accidentally.
Always use the appropriate lockout device for the specific equipment and follow manufacturer recommendations.
This practice significantly reduces the risk of accidental injury or equipment damage.
Always Follow Proper Lockout/Tagout Protocols to Avoid Electrical or Mechanical Accidents
Adhere to established lockout/tagout protocols rigorously.
These procedures are designed to provide a systematic approach to de-energizing and securing machinery.
Follow all steps outlined in your company‘s lockout/tagout program.
Ensure that all team members are aware of and understand these protocols.
Proper adherence prevents electrical and mechanical accidents, ensuring a safer work environment.
Regular training and audits can help maintain compliance and reinforce the importance of following these safety measures.
All in all, following lockout/tagout procedures is essential for safe maintenance and repair of machinery.
Always ensure the machine is shut off and tagged out, use lockout devices to prevent accidental startups, and adhere strictly to lockout/tagout protocols.
These practices are crucial for preventing accidents and ensuring a safe working environment.
Read: Importance of Accuracy in Surveying and Mapping
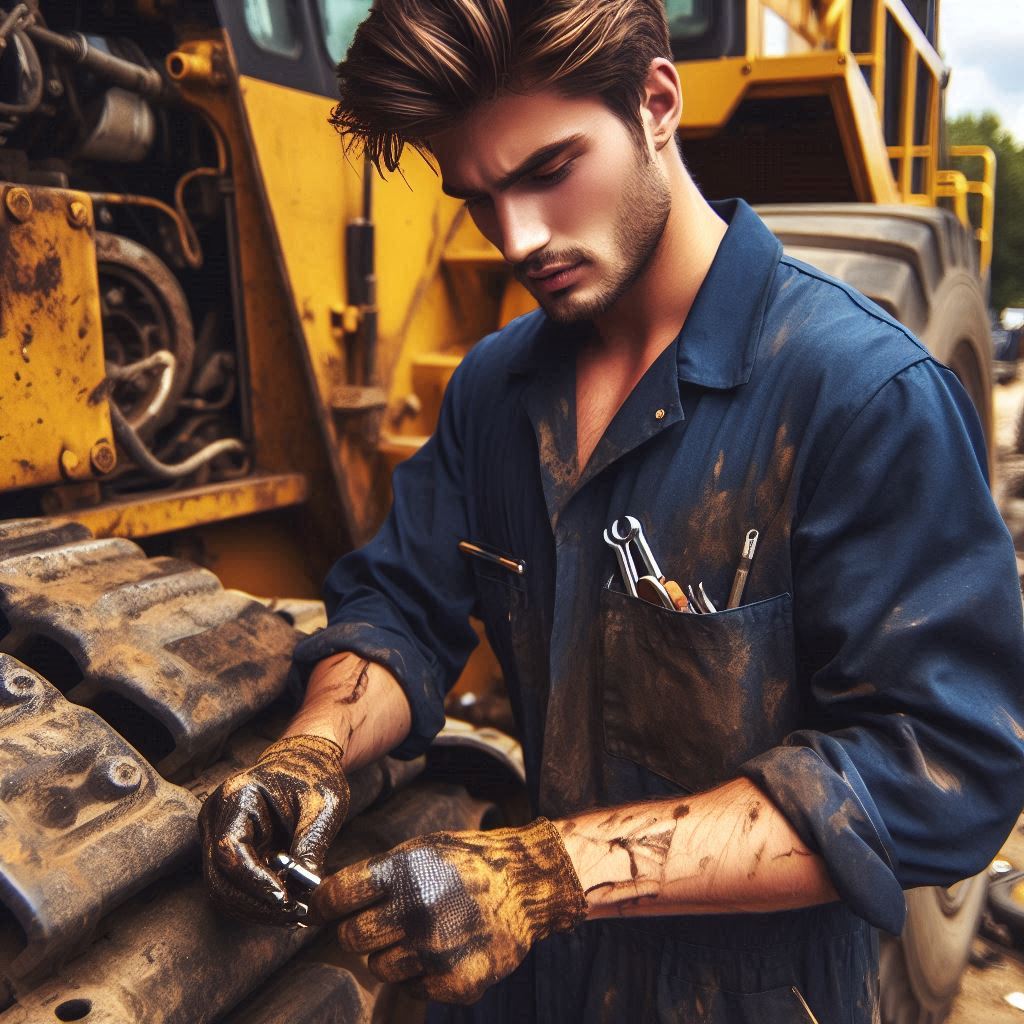
Maintain a Clean Work Environment
Keep Work Areas Clean and Organized to Prevent Slips, Trips, and Falls
A clean and organized work environment is vital for safety and efficiency.
Keeping work areas clean significantly reduces the risk of slips, trips, and falls‘common and often severe workplace accidents.
Regularly inspect and clean floors and work surfaces to eliminate any spills, oil, or other slippery substances.
Ensure that walkways and working spaces are kept clear of debris and obstructions.
This not only helps in maintaining safety but also boosts overall productivity by providing a clear and unobstructed workspace.
Implement a routine cleaning schedule to address any potential hazards before they become serious issues.
Encourage all team members to participate in maintaining cleanliness.
Regularly removing waste materials and cleaning spills promptly can prevent accidents and create a more pleasant and efficient working environment.
Consider using non-slip mats in areas prone to spills or where the floor is inherently slippery.
Remove Any Clutter or Debris That Could Obstruct Machinery or Cause Accidents
Clutter and debris around machinery can pose significant hazards, leading to accidents or equipment damage.
Ensure that all work areas are free from unnecessary items that could obstruct machinery or create tripping hazards.
Regularly check for and remove any items that could potentially interfere with machine operations or cause accidents.
Create designated areas for tools, materials, and waste to prevent clutter from accumulating in work zones.
Ensure that all team members are aware of these designated areas and adhere to them.
Keeping tools and materials organized not only improves safety but also enhances efficiency by ensuring that everything is in its proper place and easy to locate.
Additionally, routinely inspect machinery and surrounding areas for any signs of wear or damage that could be exacerbated by clutter.
Address any issues promptly to prevent further complications.
Regular inspections and maintenance of the work area can prevent potential accidents and ensure that the workspace remains safe and functional.
Properly Store Tools and Equipment When Not in Use
Proper storage of tools and equipment is a key aspect of maintaining a safe and organized work environment.
Always return tools and equipment to their designated storage locations when they are not in use.
This practice prevents accidents caused by misplaced or scattered tools and helps in reducing clutter around work areas.
Establish clear guidelines for tool storage and ensure that all team members are trained to follow them.
Use tool storage solutions such as cabinets, racks, and shelves to keep tools organized and readily accessible.
Clearly label storage areas to make it easy for everyone to find and return tools.
Implement regular checks to ensure that all tools and equipment are stored properly and in good condition.
Damaged or malfunctioning tools should be reported and repaired or replaced as needed.
Proper storage not only keeps the work environment safer but also extends the lifespan of tools and equipment by preventing damage and wear.
Read: Networking Tips for Surveying and Mapping Professionals
Communicate with Coworkers
Always Communicate Your Movements and Actions with Other Mechanics and Operators
Effective communication with coworkers is essential for maintaining safety in industrial settings.
Always inform other mechanics and operators of your movements and actions.
Let them know when you are starting or stopping a task, especially if it involves machinery.
Clear communication helps everyone stay aware of ongoing activities and potential hazards.
This practice prevents accidental interference and ensures that everyone is on the same page regarding work operations.
In a busy environment, where multiple people may be working on different tasks, coordination is key.
Regularly update your team on the status of your work and any changes in your plans.
This proactive approach minimizes the risk of accidents and improves overall efficiency by keeping everyone informed and prepared.
Transform Your Career Today
Unlock a personalized career strategy that drives real results. Get tailored advice and a roadmap designed just for you.
Start NowUse Hand Signals or Verbal Cues to Ensure Everyone Is Aware of Potential Dangers
When working in noisy or busy environments, use hand signals or verbal cues to communicate effectively.
Hand signals can be a quick and clear way to convey messages without needing to shout over machinery noise.
Establish standard hand signals with your team for common instructions or alerts.
In situations where verbal communication is possible, use clear and concise language to relay important information.
Announce any actions that could impact others, such as starting or stopping machinery.
Make sure that everyone understands the signals and cues being used to avoid confusion.
Regularly review and practice these communication methods to ensure that they are effective.
Encourage feedback from your coworkers to refine and improve communication practices.
Effective use of signals and verbal cues enhances safety and ensures that everyone is aware of potential dangers.
Establish Clear Communication Channels to Avoid Misunderstandings or Accidents
Establishing clear communication channels is vital for preventing misunderstandings and accidents.
Define and agree upon methods of communication within your team, whether through regular meetings, radio communication, or other tools.
Ensure that all team members are familiar with and understand these channels.
Create a communication plan that outlines how information should be shared and who should be informed about specific issues.
Designate a point of contact for any questions or concerns related to safety or operations.
This structured approach helps in quickly addressing any issues that arise and ensures that everyone knows how to effectively communicate within the team.
Implement regular training sessions to reinforce communication protocols and address any potential gaps.
Encourage open dialogue and feedback to continually improve communication practices.
By fostering a culture of clear and effective communication, you enhance overall safety and operational efficiency.
Ultimately, effective communication with coworkers is crucial for maintaining a safe and efficient work environment.
Always inform others of your movements and actions, use hand signals or verbal cues to convey potential dangers, and establish clear communication channels to avoid misunderstandings.
These practices help ensure that everyone is aware of and prepared for any potential risks, contributing to a safer and more coordinated workplace.
Read: Recent Trends in Surveying and Mapping Technologies
Uncover the Details: How to Become a Surveying and Mapping Technician
Attend Safety Training Sessions
Participate in Regular Safety Training Sessions to Stay Updated on Best Practices
Regular attendance at safety training sessions is crucial for staying informed about best practices in industrial safety.
These sessions provide updated knowledge and techniques essential for maintaining a safe working environment.
By participating consistently, you ensure that you are familiar with the latest safety standards and procedures.
Safety training often includes information on new equipment, updated regulations, and changes in industry practices.
Staying current with these updates helps you adapt to new safety protocols and maintain a high level of workplace safety.
Regular training also reinforces your understanding of safety practices, making them second nature in your daily work.
Learn About New Safety Protocols and Guidelines in the Industry
Safety training sessions are an opportunity to learn about new safety protocols and industry guidelines.
The industrial safety landscape is continually evolving, with new regulations and best practices emerging regularly.
Training sessions keep you informed about these changes and help you understand their implications for your work.
Understanding new safety protocols ensures that you comply with current regulations and implement the best safety measures.
This knowledge helps in preventing accidents and maintaining a safe working environment.
Embrace the opportunity to learn and apply new guidelines to enhance both personal and team safety.
Ask Questions and Seek Clarification on Any Safety Concerns During Training Sessions
During safety training sessions, actively ask questions and seek clarification on any concerns you may have.
Engaging with the trainer and seeking further explanation helps ensure that you fully understand the safety protocols being discussed.
If any aspects of the training are unclear, do not hesitate to ask for additional details or examples.
Clarifying your doubts helps prevent misunderstandings and ensures that you are applying safety practices correctly.
Encourage a culture of open communication where safety concerns are addressed promptly and thoroughly.
Additionally, use training sessions as a platform to discuss real-life scenarios or safety challenges you face.
Sharing experiences and learning from others can provide valuable insights and practical solutions to improve safety in your work environment.
In fact, attending safety training sessions is essential for staying updated on best practices and industry guidelines.
Regular participation helps you learn about new protocols and ensures compliance with current safety standards.
Actively asking questions and seeking clarification during training sessions enhances your understanding and application of safety measures.
By prioritizing safety training, you contribute to a safer and more informed workplace.
Take Breaks and Stay Alert
Avoid Working Long Hours Without Breaks, as Fatigue Can Lead to Accidents
Taking regular breaks is essential for maintaining safety and efficiency in the workplace.
Avoid working long hours without intervals, as fatigue can significantly impair your focus and judgment.
Prolonged periods of continuous work can lead to decreased alertness, slower reaction times, and increased risk of accidents.
Schedule regular breaks to rest and recharge, ensuring that you remain sharp and attentive throughout your shift.
Breaks help reduce stress and prevent burnout, allowing you to return to work with renewed energy and focus.
Use these intervals to stretch, hydrate, and relax.
This practice not only enhances your well-being but also contributes to a safer work environment by reducing the likelihood of mistakes caused by fatigue.
Stay Alert and Focused on the Task at Hand While Working with Machinery
Maintaining alertness and focus is crucial when working with machinery.
Stay engaged with the task at hand to ensure that you operate equipment safely and effectively.
Avoid distractions and multitasking, as these can lead to errors and accidents.
Concentrate on the machinery and your immediate surroundings to quickly identify and address any potential issues.
Implement strategies to stay focused, such as setting short-term goals or breaking tasks into manageable steps.
Regularly check your surroundings for any changes or hazards that could impact your work.
Staying vigilant helps you respond promptly to any unexpected situations, enhancing both your safety and operational efficiency.
Report Any Signs of Fatigue or Discomfort to Supervisors Immediately
If you experience signs of fatigue or discomfort, report them to your supervisors immediately.
Open communication about your physical and mental state is essential for addressing potential issues before they lead to accidents.
Informing your supervisor allows them to take appropriate actions, such as adjusting your workload or providing additional support.
Do not ignore feelings of exhaustion or discomfort, as they can indicate that you need a break or medical attention.
Addressing these signs promptly helps prevent accidents and maintains a safe work environment for everyone.
Encourage a culture where employees feel comfortable reporting fatigue and seeking assistance when needed.
In summary, taking breaks and staying alert are vital for maintaining safety and efficiency in the workplace.
Avoid working long hours without breaks to prevent fatigue-related accidents, stay focused on machinery tasks to ensure safe operations, and report any signs of fatigue or discomfort to supervisors immediately.
By prioritizing these practices, you contribute to a safer, more productive work environment.
You Might Also Like: Best Universities for Agricultural Engineering Degrees
Conclusion
The Importance of Safety Tips for Industrial Machinery Mechanics
Safety tips for industrial machinery mechanics are crucial for ensuring a secure working environment.
These guidelines protect both the workers and the machinery, reducing the risk of accidents and improving overall efficiency.
The Role of Following Safety Guidelines in Preventing Accidents and Injuries
Adhering to established safety guidelines is fundamental in preventing workplace accidents and injuries.
Mechanics must use personal protective equipment and follow proper protocols to mitigate risks.
Regular maintenance of machinery is equally important, as it prevents potential malfunctions that could lead to accidents.
Continuous Learning and Improvement in Safety Practices to Create a Safe Work Environment for All Personnel
Encouraging continuous learning and improvement in safety practices is vital.
Regular safety training ensures that all personnel stay updated with the latest safety standards and techniques.
This commitment to ongoing education helps identify and address potential hazards before they cause harm.
By fostering a culture of safety, mechanics contribute to a safer and more efficient work environment, benefiting everyone involved.