Introduction
Inadequate Training Programs for Industrial Machinery Mechanics
Inadequate training programs are a significant challenge for industrial machinery mechanics.
Insufficient training can leave mechanics unprepared for complex machinery.
Without proper training, understanding advanced equipment becomes difficult.
Mechanics may struggle with troubleshooting and repairing modern machines.
Inadequate training can also impact safety, as mechanics might not follow proper procedures.
Importance of Continuous Education and Skill Development
Continuous education is crucial for staying updated with industry standards and new technologies.
Regular skill development ensures mechanics are proficient in handling evolving equipment.
Mechanics must engage in ongoing learning to keep pace with advancements in machinery.
Investing in education helps maintain high standards of job performance and safety.
Potential Consequences of Insufficient Training on Job Performance and Safety
The lack of adequate training can lead to poor job performance and increased risk of accidents.
Insufficient training can cause mechanical failures and safety hazards.
Mechanics may struggle to troubleshoot effectively, leading to prolonged downtimes.
Proper training is essential for optimal job performance and workplace safety.
Addressing training gaps is vital for the success and safety of industrial machinery mechanics.
Lack of Proper Training
Inadequate Training Programs for Industrial Machinery Mechanics
One significant challenge for industrial machinery mechanics is inadequate training programs.
Many programs may not fully prepare mechanics for real-world scenarios.
They might lack hands-on training or focus too heavily on theoretical concepts.
Inadequate training can leave mechanics unprepared for the complex machinery they encounter on the job.
Without proper training, mechanics may struggle to perform maintenance and repairs efficiently.
Some programs might not keep pace with advancements in technology, leading to outdated skills.
Inadequate training can result in gaps in knowledge and skills, impacting job performance.
Mechanics might also face difficulties in diagnosing and fixing machinery issues.
As machinery becomes more advanced, the need for specialized training increases.
Mechanics who do not receive updated training may find themselves at a disadvantage.
This challenge emphasizes the need for comprehensive and up-to-date training programs in the industry.
Importance of Continuous Education and Skill Development
Continuous education and skill development are crucial for overcoming the challenge of inadequate training.
The field of industrial machinery is constantly evolving with new technologies and techniques.
Mechanics must stay informed about these changes to remain effective.
Ongoing education helps mechanics keep their skills current and relevant.
It also allows them to adapt to new machinery and repair methods.
Workshops, courses, and certifications offer opportunities to learn about the latest advancements.
Mechanics can benefit from attending industry conferences and training seminars.
These events provide exposure to emerging technologies and best practices.
Continuous learning helps mechanics troubleshoot and resolve complex issues more effectively.
It ensures that they can perform their duties with a high level of expertise.
Staying updated with current knowledge also contributes to career growth and advancement.
Potential Consequences of Insufficient Training on Job Performance and Safety
Insufficient training can have severe consequences for job performance and safety.
Mechanics with inadequate training may struggle to diagnose and repair machinery accurately.
This can lead to increased downtime and costly repairs.
Poorly performed repairs can also result in machinery malfunctions, affecting production efficiency.
Inadequate training may compromise safety, leading to hazardous working conditions.
Mechanics who are not properly trained may overlook safety protocols, increasing the risk of accidents.
This can endanger not only the mechanic but also other workers in the environment.
Insufficient training can also result in the misuse of equipment, leading to further safety hazards.
The overall performance of machinery may decline, impacting the quality of output.
Consequently, the company may face financial losses and reputational damage.
Proper training is essential for ensuring that mechanics can perform their roles effectively and safely.
In the end, Inadequate training programs present significant challenges for industrial machinery mechanics, affecting job performance and safety.
Continuous education and skill development are crucial to address these challenges.
Mechanics need to stay current with advancements in technology and repair techniques.
By investing in ongoing training, mechanics can improve their job performance and maintain a high level of safety.
Addressing the gaps in training helps ensure that mechanics are well-prepared to handle complex machinery and perform their duties effectively.
It also contributes to a safer work environment and better overall performance.
Complex and Advanced Machinery
Increasing Complexity of Industrial Machinery
Industrial machinery continues to evolve, becoming increasingly complex.
Modern machines integrate advanced technologies such as automation and robotics.
This complexity poses significant challenges for industrial machinery mechanics.
Mechanics must adapt to rapidly changing technology and sophisticated equipment.
As machines incorporate more electronic components and software, understanding their operation becomes crucial.
Traditional mechanical skills alone are often insufficient.
Mechanics need to stay current with new technologies and innovations.
This demands continuous learning and skill development to effectively maintain and repair advanced machinery.
Challenges in Troubleshooting and Repairing Advanced Machinery
Troubleshooting and repairing advanced machinery present unique challenges.
Modern equipment often features intricate electronic systems and complex software.
Diagnosing issues requires not only mechanical skills but also a deep understanding of electronics and programming.
Mechanics must use specialized diagnostic tools and software to identify problems accurately.
Repairs may involve complex procedures and require precise calibration.
Additionally, downtime can be costly, so efficient problem-solving is essential.
Mechanics face pressure to quickly diagnose and fix issues to minimize production interruptions.
The complexity of advanced machinery can make troubleshooting a time-consuming and challenging task.
Need for Specialized Knowledge and Skills
The need for specialized knowledge and skills is growing as industrial machinery advances.
Mechanics must acquire expertise in various areas, including electronics, computer systems, and automation technology.
Specialized training programs and certifications are often necessary to stay proficient.
Mechanics need to understand the interaction between mechanical components and digital systems.
Familiarity with industry-specific machinery and software is crucial.
Employers seek mechanics with a combination of mechanical and technical skills.
Continuous education and hands-on experience are essential for mastering modern equipment.
The ability to work on advanced machinery requires a commitment to ongoing learning and skill enhancement.
Overall, Industrial machinery mechanics face several challenges due to the increasing complexity of machinery, troubleshooting difficulties, and the need for specialized knowledge.
As machines become more advanced, mechanics must adapt to new technologies and sophisticated systems.
Troubleshooting modern equipment involves understanding both mechanical and electronic components, requiring specialized tools and skills.
Mechanics need to stay current with technological advancements through continuous education and training.
The growing complexity of industrial machinery emphasizes the importance of specialized knowledge and hands-on experience.
By addressing these challenges, mechanics ensure they remain effective in maintaining and repairing cutting-edge equipment.
Safety Hazards
Exposure to hazardous materials and environments
Industrial machinery mechanics face several challenges in their line of work.
Among these, the risk of accidents and injuries is significant.
Ensuring safety while working with complex machinery requires strict adherence to protocols and regulations.
Risk of Accidents and Injuries While Working on Machinery
Industrial machinery mechanics often work in environments where the risk of accidents is high.
They handle heavy equipment, operate complex machines, and perform tasks that can lead to injuries.
Common hazards include moving parts, electrical components, and high temperatures.
Mechanics may experience cuts, bruises, or more severe injuries if proper precautions are not taken.
Working with machinery also involves dealing with high noise levels and potential exposure to harmful substances.
These conditions increase the risk of hearing loss and respiratory issues.
Additionally, mechanics often work in confined spaces or awkward positions, which can lead to musculoskeletal injuries.
Another challenge is the potential for accidents related to machine malfunctions or failures.
These incidents can occur suddenly and pose significant risks to mechanics and other workers.
Immediate and accurate response is crucial to prevent further harm and ensure safe operation.
Importance of Following Safety Protocols and Regulations
Following safety protocols and regulations is essential for minimizing the risk of accidents and injuries.
Industrial machinery mechanics must adhere to established safety guidelines to protect themselves and their colleagues.
This includes wearing appropriate personal protective equipment (PPE) such as gloves, safety glasses, and ear protection.
Regular training on safety procedures is also vital.
Mechanics should be familiar with emergency protocols, proper machine handling techniques, and first aid procedures.
Ongoing education helps mechanics stay updated on best practices and new safety regulations.
Additionally, proper maintenance and inspection of machinery are critical.
Mechanics must ensure that machines are in good working condition and identify any potential issues before they lead to accidents.
Performing routine checks and addressing maintenance needs promptly can prevent many hazards.
Implementing safety measures in the workplace, such as clear signage, safety barriers, and well-maintained equipment, further reduces the risk of accidents.
A safety-first culture encourages all employees to prioritize safety and report hazards or unsafe conditions.
Mechanics should also participate in safety audits and inspections.
These assessments help identify potential risks and ensure compliance with safety standards.
Addressing issues identified during audits can improve overall workplace safety and prevent accidents.
In essence, Industrial machinery mechanics face significant challenges, particularly regarding the risk of accidents and injuries.
Following safety protocols and regulations is crucial to mitigating these risks.
By adhering to safety guidelines, participating in ongoing training, and maintaining a safety-conscious work environment, mechanics can protect themselves and their colleagues from harm.
Prioritizing safety ensures a safer and more efficient workplace for everyone involved.
Read: CAD Technician Job Market: Trends and Insights
Tight Schedules and Deadlines
Pressure to Complete Repairs and Maintenance Tasks Quickly
Industrial machinery mechanics often face significant pressure to complete repairs and maintenance tasks swiftly.
This pressure stems from the need to minimize equipment downtime and maintain production schedules.
Delays in repairs can lead to costly production halts and reduced efficiency.
Mechanics must diagnose and address issues promptly to prevent extended downtime.
The challenge is to balance speed with thoroughness, ensuring repairs are effective and lasting.
Quick fixes may not always address underlying issues, leading to repeated problems.
Mechanics must work under tight deadlines while maintaining high-quality work standards.
This constant pressure can be stressful and demanding, impacting job satisfaction and performance.
Effective communication with supervisors and team members about realistic timelines is crucial.
By setting clear expectations and prioritizing tasks, mechanics can better manage this pressure and improve their workflow.
Balancing Efficiency with Precision in Repairs
Balancing efficiency with precision is a critical challenge for industrial machinery mechanics.
Mechanics need to complete repairs quickly while ensuring accuracy and thoroughness.
Efficiency involves performing tasks in a timely manner to keep machinery operational.
Precision ensures that repairs are done correctly to avoid recurring issues.
Striking this balance is crucial for long-term machinery performance and reliability.
Rushing repairs can lead to mistakes, which may result in more significant problems or safety hazards.
Mechanics must carefully assess each situation to determine the appropriate repair methods and techniques.
They need to use their expertise to make informed decisions that prioritize both speed and quality.
Developing a systematic approach to repairs can help maintain this balance.
Training and experience play a significant role in achieving efficiency without sacrificing precision.
Strategies for Managing Time Effectively and Meeting Deadlines
Effective time management is essential for industrial machinery mechanics to meet deadlines and handle multiple tasks.
Start by creating a detailed plan for each repair or maintenance task.
Prioritize tasks based on urgency and importance to ensure critical issues are addressed first.
Use checklists to track progress and ensure all necessary steps are completed.
Break larger tasks into smaller, manageable steps to avoid feeling overwhelmed.
Allocate specific time blocks for each task and stick to these deadlines as closely as possible.
Avoid distractions and stay focused on the task at hand to maximize productivity.
Communicate with your team to coordinate efforts and share workload effectively.
Regularly review and adjust your strategies to improve efficiency and meet deadlines.
Utilizing time management tools and software can also help streamline tasks and track progress.
Continuous improvement and adaptability are key to managing time effectively in a demanding work environment.
Industrial machinery mechanics face several challenges, including pressure to complete tasks quickly, balancing efficiency with precision, and managing time effectively.
Addressing these challenges requires a strategic approach and a commitment to quality.
By developing effective time management skills, balancing speed with accuracy, and setting realistic expectations, mechanics can improve their performance and job satisfaction.
Overcoming these challenges will lead to better outcomes in machinery maintenance and repair, contributing to overall operational efficiency.
Read: Quality Control Inspector: Entry-Level Guide
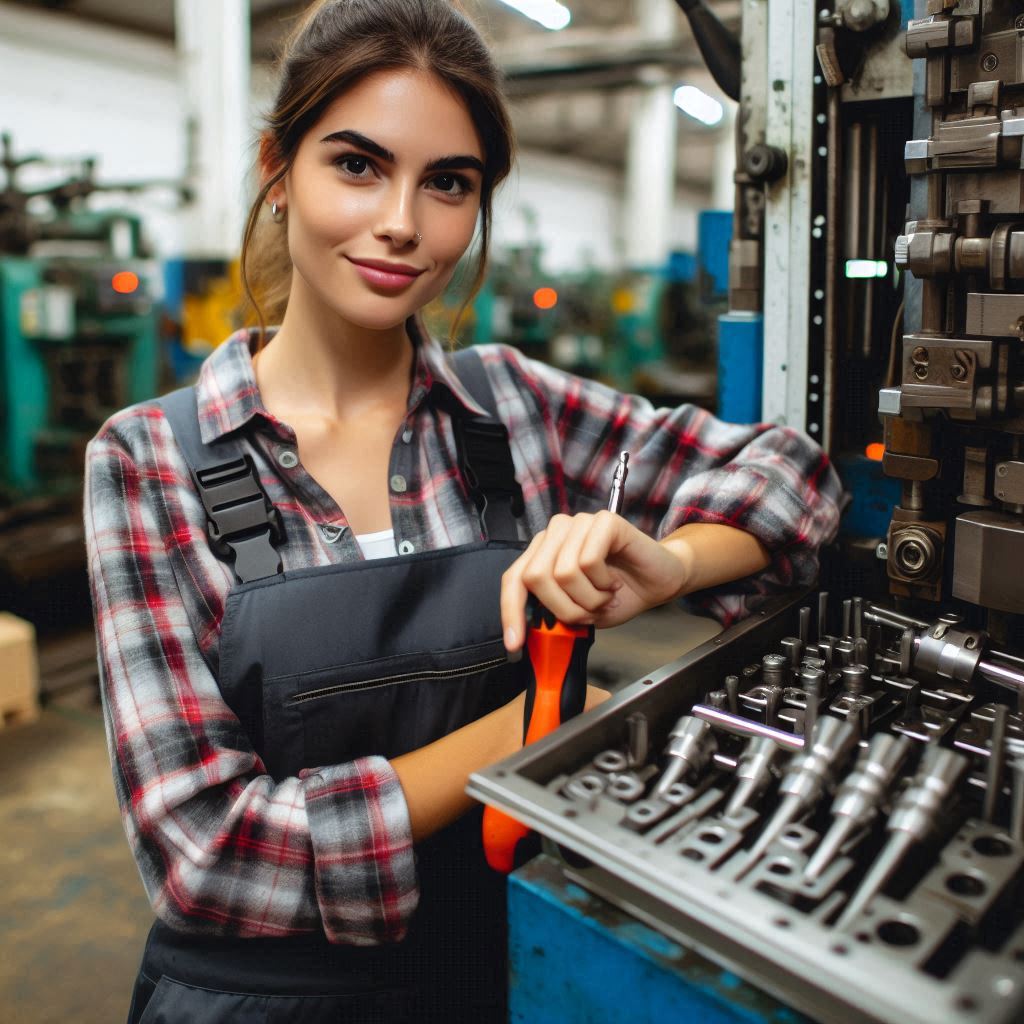
Physical Demands
Requirement for Physical Strength and Stamina to Work on Heavy Machinery
Industrial machinery mechanics face significant physical demands in their daily tasks.
Working with heavy machinery requires substantial physical strength and stamina.
Mechanics often handle large and cumbersome parts, such as motors and gears, which can be physically taxing.
The job involves frequent bending, lifting, and maneuvering of equipment, all of which require a strong and resilient body.
Mechanics need to maintain good physical conditioning to perform these tasks effectively.
Regular exercise and strength training can help build the necessary muscle and endurance for the job.
In addition, mechanics must be prepared for long hours on their feet, often in physically challenging positions.
Potential Strain on the Body from Lifting and Moving Equipment
Lifting and moving heavy equipment can place significant strain on a mechanic‘s body.
Repeated lifting of heavy parts, such as pumps or compressors, can lead to musculoskeletal issues.
Mechanics may experience back pain, shoulder strain, or joint discomfort from the physical demands of their work.
Proper lifting techniques and the use of mechanical aids, such as hoists or forklifts, can help mitigate some of this strain.
However, even with these aids, the physical demands of the job remain substantial.
Mechanics must be vigilant about their physical health and take steps to prevent injury.
Importance of Proper Ergonomics and Avoiding Injuries
Proper ergonomics play a crucial role in preventing injuries and ensuring long-term health for industrial machinery mechanics.
Mechanics should use ergonomic tools and equipment designed to reduce strain on the body.
Adjustable workstations, ergonomic hand tools, and proper seating can all contribute to a more comfortable and less physically taxing work environment.
Mechanics should also practice good body mechanics, such as keeping their back straight while lifting and using their legs rather than their back.
Regular breaks and stretching exercises can help alleviate muscle tension and reduce the risk of repetitive strain injuries.
In addition, employers should provide adequate training on ergonomics and safety practices.
Mechanics should be encouraged to report any discomfort or potential hazards they encounter.
Addressing ergonomic issues proactively can help prevent long-term health problems and improve overall job satisfaction.
Using proper safety gear, such as gloves and supportive footwear, is also essential in protecting against injuries.
The role of an industrial machinery mechanic involves considerable physical demands, including strength, stamina, and the ability to handle heavy equipment.
The strain from lifting and moving machinery can lead to musculoskeletal issues, making proper ergonomics and injury prevention crucial.
By prioritizing physical conditioning, using ergonomic tools, and adhering to safety practices, mechanics can reduce their risk of injury and maintain their health.
Understanding and addressing these challenges can lead to a safer and more sustainable career in industrial machinery maintenance.
Transform Your Career Today
Unlock a personalized career strategy that drives real results. Get tailored advice and a roadmap designed just for you.
Start NowRead: Interview Tips for Aspiring Radiologic Technologists
Communication Challenges
Collaboration with Other Team Members and Supervisors
Industrial machinery mechanics often face challenges in collaborating with team members and supervisors.
Effective teamwork is crucial for resolving complex equipment issues.
Mechanics must work closely with other technicians, engineers, and managers to ensure smooth operations.
This collaboration helps in sharing knowledge and solving problems efficiently.
Teamwork is essential when dealing with large-scale repairs or maintenance tasks that require multiple hands.
Supervisors play a key role in guiding and supporting the mechanics.
Open communication with supervisors helps in understanding priorities and receiving timely assistance.
Mechanics must also be adaptable and willing to coordinate with different departments.
Effective collaboration leads to faster problem resolution and improved equipment performance.
Effective Communication to Troubleshoot and Address Equipment Issues
It is vital for troubleshooting and addressing equipment issues.
Mechanics must clearly describe problems to colleagues and supervisors.
Providing accurate information about symptoms helps in diagnosing issues more quickly.
Effective communication also involves listening to feedback and suggestions from others.
Discussing potential solutions with team members can lead to better outcomes.
Mechanics should document all issues and repairs thoroughly.
Clear documentation aids in future troubleshooting and maintenance.
Regular updates to team members and supervisors keep everyone informed about the status of repairs.
This ensures that everyone is on the same page and that resources are allocated efficiently.
Addressing equipment issues promptly and accurately depends on strong communication skills.
Importance of Clear and Concise Communication Skills
Clear and concise communication skills are crucial for industrial machinery mechanics.
These skills help in conveying technical information effectively.
Mechanics must be able to explain complex issues in simple terms.
This ensures that all team members understand the problem and solution.
Concise communication prevents misunderstandings and reduces the risk of errors.
It also helps in coordinating efforts and managing resources efficiently.
Strong communication skills enhance teamwork and collaboration.
They enable mechanics to provide clear instructions and receive useful feedback.
Clear communication is also important when interacting with non-technical staff or customers.
It ensures that everyone involved understands the equipment’s status and any required actions.
Strategies for Improving Communication and Collaboration
Improving communication and collaboration involves several strategies.
First, practice active listening to fully understand others’ perspectives and concerns.
Ask clarifying questions when needed to ensure accurate understanding.
Second, use clear and straightforward language when discussing technical issues.
Avoid jargon that might confuse non-technical team members.
Third, maintain open lines of communication with all team members and supervisors.
Regular meetings and updates can help keep everyone informed.
Finally, invest in communication training or workshops if available.
These can enhance both verbal and written communication skills.
Implementing these strategies can improve teamwork, increase efficiency, and lead to better problem-solving outcomes.
Ultimately, collaboration and effective communication are critical for industrial machinery mechanics.
Working closely with team members and supervisors enhances problem-solving and equipment maintenance.
Clear and concise communication skills are essential for troubleshooting and addressing issues effectively.
By focusing on improving these skills, mechanics can overcome common challenges and contribute to a more efficient and successful work environment.
Read: Future of CAD Technician Jobs in Engineering
Financial Constraints
Limited Budget for Necessary Repairs and Maintenance
Industrial machinery mechanics often face the challenge of working with limited budgets for repairs and maintenance.
Budget constraints can limit the ability to perform necessary repairs, potentially leading to more significant issues down the line.
With restricted funds, prioritizing which repairs to address first becomes crucial.
Mechanics must find ways to make the most of available resources while ensuring machinery remains operational.
Balancing Cost-Effective Solutions with Quality Repairs
Balancing cost-effective solutions with quality repairs is a critical challenge.
Mechanics need to ensure that repairs are both affordable and effective.
Using lower-cost parts or temporary fixes might seem like a quick solution, but they can lead to recurring problems.
On the other hand, opting for higher-quality repairs might strain the budget but can prevent frequent breakdowns and more expensive repairs in the future.
Finding the right balance involves evaluating the long-term impact of repair decisions.
Mechanics should consider the cost-benefit ratio of each repair option.
Investing in quality repairs can often save money in the long run by reducing downtime and extending the lifespan of the machinery.
However, it is also essential to identify areas where cost-effective solutions can be applied without compromising safety or performance.
Strategies for Prioritizing Maintenance Tasks to Fit Within Budget Constraints
To fit within budget constraints, mechanics must develop effective strategies for prioritizing maintenance tasks.
Start by conducting a thorough assessment of all machinery to identify critical issues.
Focus on repairs that will prevent major failures and minimize downtime.
Prioritize tasks based on their impact on overall operations and the potential cost of inaction.
Implementing a preventive maintenance program can also help manage costs.
Regularly scheduled maintenance can prevent unexpected breakdowns and reduce the need for emergency repairs.
By addressing potential issues before they become severe, mechanics can avoid more significant expenses and keep operations running smoothly.
Additionally, maintaining a detailed log of maintenance activities and repairs can provide valuable insights.
This log helps track the performance and reliability of machinery, guiding future maintenance decisions.
It also allows mechanics to analyze patterns and identify which repairs offer the best value for the budget.
Leveraging relationships with suppliers and vendors can also be beneficial.
Negotiate for better pricing on parts and services, and consider bulk purchasing to reduce costs.
Explore options for extended warranties or service agreements that might provide cost savings in the long term.
In summary, navigating budget constraints while ensuring quality repairs and maintenance requires careful planning and strategic decision-making.
By prioritizing critical tasks, balancing cost and quality, and implementing preventive measures, industrial machinery mechanics can effectively manage limited budgets and maintain operational efficiency.
See Related Content: Network Engineer vs. Network Administrator: Key Differences
Technological Advancements
Adoption of New Technologies in Industrial Machinery
The industrial machinery field constantly evolves with new technologies, presenting both opportunities and challenges.
Advancements such as automation, robotics, and smart machinery are becoming more prevalent.
These technologies can enhance efficiency and productivity but also require mechanics to adapt quickly.
Staying current with these innovations is essential for maintaining high performance in machinery.
Challenges in Staying Updated with the Latest Advancements
One major challenge is the rapid pace of technological change.
Mechanics often struggle to keep up with frequent updates and new systems.
Each new technology introduces unique complexities that require additional training and expertise.
Moreover, the cost of new tools and equipment can be a barrier for many professionals.
Limited access to resources or training can further hinder the ability to stay updated.
Importance of Continuous Learning and Training to Keep Up with Technology Trends
Continuous learning is crucial for overcoming these challenges.
Regular training helps mechanics understand and operate new technologies effectively.
Engaging in workshops, courses, and certifications keeps skills sharp and knowledge current.
Additionally, staying informed about industry trends through professional organizations and publications supports ongoing development.
Mechanics who invest in their education can troubleshoot problems more efficiently and maintain high standards of work.
Continuous learning not only improves technical skills but also enhances career prospects.
It enables mechanics to adapt to new technologies and integrate them seamlessly into their work.
In the rapidly changing world of industrial machinery, adapting to new technologies is vital for career growth and job security.
Embracing continuous learning and training ensures that mechanics remain competent and competitive.
Investing in education and staying current with advancements can lead to more job opportunities and a more fulfilling career.
Lastly, while the adoption of new technologies presents challenges, the benefits of staying updated far outweigh the difficulties.
By prioritizing continuous learning and training, industrial machinery mechanics can successfully navigate technological advancements and excel in their field.
Conclusion
Industrial machinery mechanics face several common challenges that can impact their effectiveness and safety.
One significant challenge is inadequate training programs.
Many programs fail to provide the hands-on experience needed for working with complex machinery.
Mechanics who do not receive comprehensive training may struggle with diagnosing and repairing intricate issues.
This can lead to inefficiencies, increased downtime, and costly repairs.
Additionally, outdated training might not cover the latest technologies, which further complicates maintenance and repairs.
Addressing these challenges is crucial for ensuring efficiency and safety in industrial settings.
Continuous education and updated training are essential for mechanics to stay current with new technologies and best practices.
Proper training helps prevent safety hazards and ensures that machinery operates smoothly.
Mechanics need to be equipped with the latest knowledge and skills to perform their jobs effectively.
The hard work and dedication of industrial machinery mechanics deserve recognition.
They play a vital role in maintaining operational efficiency and workplace safety.
Their commitment to overcoming challenges ensures that industrial operations run smoothly and safely.
Recognizing their efforts helps highlight the importance of ongoing support and development in the field.
[E-Books for Sale]
The Big Book of 500 High-Paying Jobs in America: Unlock Your Earning Potential
$19.99 • 500 High-Paying Jobs • 330 pages
Explore 500 high-paying jobs in America and learn how to boost your career, earn more, and achieve success!
See All 500 High-Paying Jobs of this E-Book
1001 Professions Without a Degree: High-Paying American Jobs You Can Start Now
$19.99 • 1001 Professions Without a Degree • 174 pages
Discover 1001 high-paying jobs without a degree! Unlock career tips, skills, and success strategies for just $19.99!