Introduction
Brief Overview of Industrial Machinery Mechanics
Industrial machinery mechanics play a crucial role in numerous industries.
They ensure machines run smoothly and efficiently.
Their tasks include repairing, maintaining, and installing complex equipment.
This role is vital in manufacturing, construction, and other sectors reliant on machinery.
Importance of Their Role
- Minimizes Downtime: Quick repairs reduce production interruptions.
- Enhances Safety: Proper maintenance prevents accidents and malfunctions.
- Increases Efficiency: Well-maintained machines operate at peak performance.
Preview of what a Typical Day Looks Like for an Industrial Machinery Mechanic
A typical day for an industrial machinery mechanic involves diverse activities.
They start by reviewing work orders and assessing equipment needs.
They then troubleshoot issues, perform repairs, and conduct routine inspections.
Mechanics often collaborate with other technicians to solve complex problems.
Their day can include replacing parts, adjusting settings, and documenting work performed.
By maintaining machinery, they ensure smooth operations across various industries.
Morning Routine
Early Start to the Day
An industrial machinery mechanic’s day often begins early.
Mechanics usually start their shifts before dawn to address issues promptly.
Arriving early allows them to assess the day’s workload and prioritize tasks.
The early start helps in managing maintenance schedules and minimizing machine downtime.
Morning hours are often quieter, providing a good time for detailed inspections and repairs.
Early shifts are crucial for staying on top of urgent maintenance needs.
Reviewing Work Orders and Schedules
The next step involves reviewing work orders and schedules.
Mechanics examine the list of tasks assigned for the day.
They check for details on specific machinery and maintenance requirements.
Understanding the work orders helps in planning and organizing the day efficiently.
Mechanics also review any updates or changes in the maintenance schedule.
This review process ensures that they address all tasks and follow proper procedures.
Effective planning helps in managing time and resources efficiently throughout the day.
Gathering Necessary Tools and Equipment
Before starting their tasks, mechanics gather the necessary tools and equipment.
They collect tools like wrenches, screwdrivers, and diagnostic devices.
Mechanics ensure that they have all required parts and safety gear.
Checking the condition of tools and equipment before use is essential.
Proper preparation prevents delays caused by missing or malfunctioning tools.
Gathering everything needed for the day’s work helps in maintaining productivity and efficiency.
This preparation is critical for performing repairs and maintenance tasks smoothly.
A day in the life of an industrial machinery mechanic begins early and involves careful preparation.
Mechanics start by arriving early to address maintenance needs.
They review work orders and schedules to plan their tasks effectively.
Gathering the necessary tools and equipment ensures a smooth workflow throughout the day.
These steps are crucial for maintaining machinery and ensuring efficient operation.
Read: CAD Technician vs. Draftsman: Key Differences
Inspection and Maintenance
Checking Machinery for Any Issues or Malfunctions
A typical day for an industrial machinery mechanic starts with checking machinery for issues or malfunctions.
Mechanics begin by reviewing logs and reports for any recent problems.
They inspect machines visually to detect any obvious signs of wear or damage.
Technicians use diagnostic tools to test machinery functions and identify potential issues.
They listen for unusual noises and observe vibrations that might indicate problems.
This initial check helps prevent unexpected breakdowns and ensures machinery operates smoothly throughout the day.
Performing Routine Maintenance Tasks
A typical day for an industrial machinery mechanic starts with checking machinery for issues or malfunctions.
Mechanics begin by reviewing logs and reports for any recent problems.
They inspect machines visually to detect any obvious signs of wear or damage.
Technicians use diagnostic tools to test machinery functions and identify potential issues.
They listen for unusual noises and observe vibrations that might indicate problems.
This initial check helps prevent unexpected breakdowns and ensures machinery operates smoothly throughout the day.
Making Necessary Repairs and Replacements
When issues arise, mechanics make necessary repairs and replacements to restore machinery to proper working order.
They diagnose the specific problem and determine the best course of action.
Technicians disassemble machines to access and repair or replace faulty parts.
They may repair or replace components such as motors, gears, or hydraulic systems.
After completing repairs, mechanics reassemble the machinery and test it to ensure it functions correctly.
They document the repairs and update maintenance records to track the machinery’s condition.
Effective repairs and replacements help prevent future issues and ensure reliable machinery operation.
A day in the life of an industrial machinery mechanic involves several key activities.
Checking machinery for malfunctions, performing routine maintenance, and making necessary repairs are essential tasks.
These activities ensure that machinery operates efficiently and reliably.
By regularly inspecting, maintaining, and repairing equipment, mechanics play a crucial role in keeping industrial operations running smoothly.
Read: CAD Technician Certification: What You Need to Know
Troubleshooting
Diagnosing Problems with Machinery
Mechanics start their day by assessing and diagnosing machinery issues.
Their tasks include:
Transform Your Career Today
Unlock a personalized career strategy that drives real results. Get tailored advice and a roadmap designed just for you.
Start Now- Visual Inspection: Check for visible signs of damage, wear, or misalignment.
- Listen for Unusual Noises: Identify any abnormal sounds such as grinding, squealing, or knocking.
- Check for Vibrations: Feel for excessive vibrations or movement that could indicate a problem.
- Monitor Temperature: Measure temperatures to detect overheating or abnormal temperature fluctuations.
- Check for Leaks: Look for fluid leaks around seals, joints, and hoses.
- Review Operating Conditions: Verify that the machinery is operating under the correct conditions, such as load and speed.
- Inspect Lubrication Levels: Ensure proper lubrication levels and check for contamination in lubricants.
- Test Electrical Systems: Check for issues with wiring, connections, and electrical components.
- Analyze Performance Data: Review historical and real-time performance data to spot anomalies.
- Run Diagnostic Software: Use diagnostic software tools to detect issues and error codes.
- Check Sensors and Gauges: Verify that all sensors and gauges are functioning correctly.
- Perform Load Testing: Conduct tests to determine if the machine can handle its designed load.
- Check Alignment and Balance: Inspect the alignment and balance of rotating parts and components.
- Inspect Bearings and Moving Parts: Look for wear, noise, or heat in bearings and other moving parts.
- Review Maintenance Records: Check past maintenance records for recurring issues or patterns.
Accurate diagnosis is crucial for determining the correct repair or maintenance actions needed.
Using Specialized Tools and Equipment to Identify Issues
Once a problem is identified, mechanics use specialized tools and equipment to further investigate.
Key tools include:
- Diagnostic Software: Mechanics use software to run detailed diagnostics on machinery.
This software provides insights into electronic systems and component performance. - Vibration Analyzers: These tools measure vibrations to identify imbalances or misalignments. They help diagnose issues with rotating equipment.
- Thermal Cameras: Mechanics use thermal imaging to detect hot spots and overheating components.
This helps in finding issues that are not visible to the naked eye. - Multimeters and Gauges: They measure electrical signals and pressure levels.
These measurements help diagnose issues related to electrical and hydraulic systems.
Specialized tools are essential for precise and efficient problem identification.
Collaborating with Team Members to Come Up with Solutions
Collaboration is key to solving complex machinery issues.
Mechanics frequently work with team members to develop effective solutions:
- Brainstorming Sessions
- Mind Mapping
- Round Robin Discussions
- SWOT Analysis
- Workshops and Collaborative Work Sessions
- Design Thinking Workshops
- Group Problem-Solving Techniques (e.g., Six Thinking Hats)
- Feedback and Iteration Cycles
- Idea Voting and Prioritization
- Collaborative Whiteboarding Tools
- Pair Programming or Pair Work
- Fishbowl Conversations
- Breakout Group Discussions
- Consensus Building Exercises
- Scenario Planning and Role Playing
Team collaboration enhances problem-solving and ensures that machinery repairs are completed effectively and safely.
Read: Essential Skills for CAD Technicians
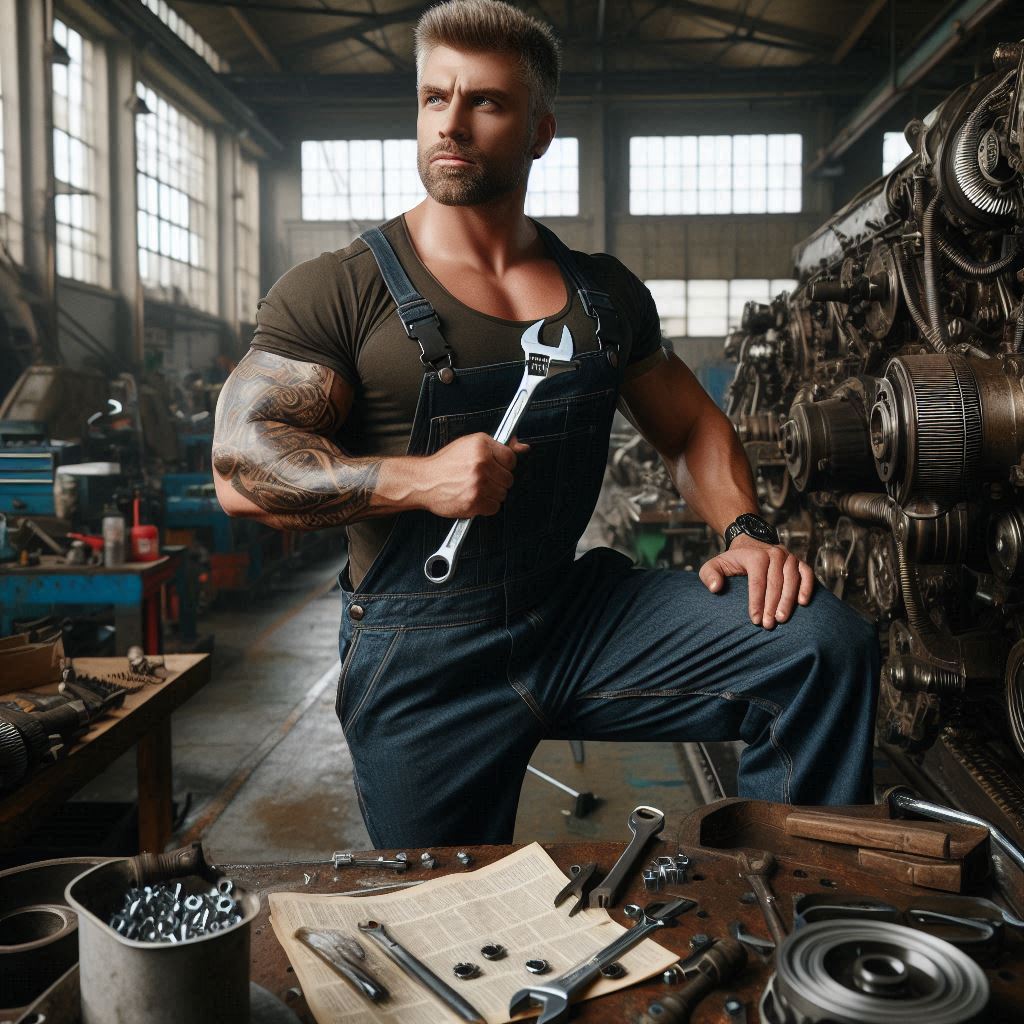
Repairs and Adjustments
Fixing Mechanical, Electrical, and Hydraulic Systems
A typical day for an industrial machinery mechanic involves fixing various systems.
They address mechanical, electrical, and hydraulic issues.
Mechanics begin by diagnosing problems in machinery.
They use tools and techniques specific to each system.
For mechanical issues, they repair or replace faulty gears, belts, and bearings.
Electrical repairs involve troubleshooting wiring, circuits, and control panels.
Hydraulic system repairs include fixing leaks and ensuring proper fluid levels.
Each task requires precision and technical expertise to restore equipment functionality.
Adjusting Components for Proper Functionality
Adjusting components to ensure proper functionality is a key part of the job.
Mechanics calibrate and fine-tune machinery to meet performance standards.
They adjust gears, valves, and other components to correct misalignments.
Proper adjustments enhance machine efficiency and prevent wear.
Mechanics follow technical manuals and specifications for each adjustment.
They ensure that all components operate in harmony.
Accurate adjustments are essential for optimal machine performance and longevity.
Testing Machinery to Verify Repairs and Adjustments
After repairs and adjustments, testing machinery is crucial.
Mechanics run tests to verify that all issues have been resolved.
They observe the machine’s operation under normal and extreme conditions.
Testing ensures that repairs are effective and that components function correctly.
Mechanics check for any remaining issues or irregularities.
They document test results and make additional adjustments if necessary.
Comprehensive testing confirms that machinery operates reliably and meets safety standards.
Daily Workflow and Responsibilities
The daily workflow for an industrial machinery mechanic involves a mix of troubleshooting, repairing, and adjusting equipment.
Mechanics start by reviewing maintenance logs and identifying equipment issues.
They then proceed with detailed inspections and repairs.
Adjustments are made based on performance data and technical specifications.
Testing follows to ensure that repairs and adjustments have restored functionality.
Throughout the day, mechanics prioritize safety and efficiency.
They also maintain detailed records of their work and communicate with team members about ongoing issues.
Read: Day in the Life of a CAD Technician
Safety protocols
A day in the life of an industrial machinery mechanic involves a strict adherence to safety guidelines and protocols.
Prioritizing safety is crucial in ensuring a secure work environment and effective machinery maintenance.
Following Safety Guidelines and Protocols
Industrial machinery mechanics start their day by reviewing safety guidelines and protocols.
They ensure they are updated on the latest safety procedures.
Following these guidelines helps prevent accidents and injuries.
Mechanics adhere to protocols for machinery inspection, repair, and operation.
Regular safety briefings and training sessions reinforce the importance of these procedures.
Using Personal Protective Equipment
Personal protective equipment (PPE) is essential for mechanics working on machinery.
They wear safety glasses, gloves, and ear protection as standard practice.
PPE protects them from potential hazards, such as flying debris and loud noises.
Mechanics also use helmets and steel-toed boots when required.
Proper use of PPE is critical for personal safety and compliance with workplace regulations.
Ensuring a Safe Work Environment
Mechanics are responsible for maintaining a safe work environment for themselves and their colleagues.
They ensure work areas are clean and free of hazards.
Regularly inspecting machinery for potential safety issues is part of their routine.
Mechanics also adhere to lockout/tagout procedures to prevent accidental machine startups during maintenance.
They report any unsafe conditions or equipment malfunctions promptly.
Implementing Safe Work Practices
Safe work practices are integral to a mechanic’s daily tasks.
Mechanics use tools and machinery according to manufacturer guidelines and safety standards.
They follow proper procedures for lifting heavy objects and handling hazardous materials.
Adhering to these practices reduces the risk of injury and ensures efficient and effective machinery repairs.
Conducting Regular Safety Checks
Regular safety checks are part of a mechanic’s routine.
Mechanics inspect machinery before and after use to identify any safety concerns.
They perform routine maintenance on safety equipment, such as emergency stop buttons and fire extinguishers.
These checks help ensure that safety systems are functioning correctly and ready for use in emergencies.
Continuous education helps mechanics remain aware of new safety regulations and technologies.
Documentation and Reporting
As an industrial machinery mechanic, documentation and reporting are crucial aspects of the job.
It involves keeping detailed records of work done on each machine, reporting any significant findings or issues to supervisors, and updating maintenance logs while tracking inventory of spare parts.
Transform Your Career Today
Unlock a personalized career strategy that drives real results. Get tailored advice and a roadmap designed just for you.
Start NowKeeping Detailed Records
One of the key responsibilities of an industrial machinery mechanic is keeping detailed records of all work done on each machine.
This includes information such as the date of maintenance, parts replaced, repairs made, and any other relevant details.
By maintaining accurate records, mechanics can track the history of a machine and identify any recurring issues that may need special attention.
For example, if a machine keeps breaking down at a particular interval, the mechanic can refer back to the maintenance records to determine the cause and develop a proactive solution.
These records also come in handy during safety inspections or audits, as they provide a clear overview of the maintenance history of each machine.
Reporting Significant Findings
Another important aspect of the documentation process is reporting any significant findings or issues to supervisors.
This could include identifying potential safety hazards, recommending essential repairs or upgrades, or flagging any irregularities in machine performance.
By promptly reporting these issues, mechanics can prevent more extensive damage or downtime in the future.
Supervisors rely on these reports to make informed decisions about maintenance schedules, budget allocations, and overall equipment efficiency.
Effective communication is key in this process, as mechanics must clearly articulate the problems observed, the potential solutions, and any associated risks or implications.
Updating Maintenance Logs
In addition to keeping detailed records and reporting findings, industrial machinery mechanics are responsible for updating maintenance logs and tracking inventory of spare parts.
Maintenance logs provide a comprehensive overview of all scheduled and unscheduled maintenance activities, helping to optimize equipment performance and extend its lifespan.
By regularly updating these logs, mechanics can identify patterns of wear and tear, plan preventative maintenance tasks, and ensure that all necessary repairs are completed in a timely manner.
Proper inventory management of spare parts is equally essential, as it helps mechanics to quickly locate and replace faulty components, minimizing downtime and maximizing productivity.
Overall, effective documentation and reporting practices are essential for industrial machinery mechanics to ensure the smooth operation of equipment, maintain a safe working environment, and enhance overall equipment performance.
By staying organized, proactive, and communicative, mechanics can play a vital role in optimizing the efficiency and reliability of industrial machinery systems.
Training and Professional Development
A day in the life of an industrial machinery mechanic involves more than just hands-on repairs.
It includes continuous learning and career development.
This section explores how participating in training courses, staying updated on industry trends, and seeking certification can enhance a mechanic’s skills and career prospects.
Participating in Training Courses to Enhance Skills and Knowledge
Industrial machinery mechanics frequently participate in training courses to improve their skills.
These courses offer advanced techniques and new methodologies for handling machinery.
Mechanics may attend workshops, online courses, or in-person seminars.
Training helps mechanics stay proficient in operating and repairing complex machinery.
It provides opportunities to learn about the latest tools and equipment.
Mechanics gain knowledge about troubleshooting new issues and implementing updated procedures.
Additionally, training courses often cover safety protocols and regulatory requirements.
Mechanics can learn about best practices for maintaining safe working conditions.
Continuous education ensures that they can handle evolving technology and meet industry standards effectively.
Staying Updated on Latest Industry Trends and Technologies
Staying current with industry trends and technologies is vital for industrial machinery mechanics.
The machinery and equipment used in the field constantly evolve.
Mechanics must keep abreast of new developments to remain effective.
Mechanics can follow industry publications, blogs, and forums to stay informed.
Networking with other professionals also provides insights into emerging technologies.
Attending industry conferences and expos offers firsthand experience with the latest innovations.
Being aware of trends helps mechanics adapt to new equipment and techniques.
It ensures that they can apply modern solutions to existing problems and improve efficiency.
Staying updated also positions mechanics as knowledgeable professionals in their field.
Seeking Certification and Licensure Opportunities for Career Advancement
Certification and licensure are crucial for career advancement in industrial machinery mechanics.
Achieving certifications demonstrates expertise and commitment to the profession.
Various certifications are available, including those from industry-recognized organizations.
Obtaining certification often requires passing exams and meeting specific experience requirements.
It validates a mechanic’s skills and knowledge to employers and clients.
Certifications can lead to better job opportunities and higher earning potential.
Licensure may be required depending on local regulations and industry standards.
It typically involves completing formal education and demonstrating practical experience.
Being licensed enhances credibility and can open doors to advanced positions within the industry.
Interaction with Colleagues and Clients
Industrial machinery mechanics often work in dynamic environments.
Their day includes collaborating with others, communicating effectively, and providing exceptional customer service.
This section explores these aspects of their daily routine.
Collaborating with Other Mechanics and Technicians
Mechanics frequently collaborate with other mechanics and technicians on complex projects.
Working as a team allows for solving intricate issues more efficiently.
Each team member brings unique expertise to address specific problems.
Collaboration involves sharing insights and strategies for repairs and maintenance.
Mechanics often consult each other to troubleshoot and ensure the best solutions.
They coordinate efforts to complete projects on time and within budget.
Joint problem-solving sessions help tackle challenging repairs and upgrades.
Effective teamwork enhances the quality of work and fosters a supportive work environment.
Mechanics rely on each other’s skills and experience to manage complex tasks.
Communicating with Supervisors and Clients
Clear communication with supervisors and clients is crucial for industrial machinery mechanics.
Mechanics provide regular updates on project progress and any challenges encountered.
This transparency helps supervisors make informed decisions and adjust plans as needed.
Mechanics also discuss project timelines and resource requirements with their supervisors.
Effective communication ensures that all parties understand project goals and expectations.
It helps in aligning resources and managing any potential delays.
When dealing with clients, mechanics explain technical issues and solutions clearly.
They address client concerns and provide detailed explanations of the work performed.
Good communication builds trust and ensures that clients are satisfied with the results.
Providing Exceptional Customer Service
Exceptional customer service is a key aspect of a mechanic’s role.
Mechanics strive to deliver high-quality work and exceed client expectations.
They focus on resolving issues efficiently while maintaining a professional demeanor.
Building positive relationships with clients involves listening to their needs and addressing concerns promptly.
Mechanics demonstrate respect and professionalism in all interactions.
Providing clear and accurate information helps clients feel confident in the services provided.
Mechanics also follow up on completed work to ensure client satisfaction.
They may offer additional support or advice to maintain machinery in optimal condition.
This ongoing commitment to service enhances client relationships and encourages repeat business.
Conclusion
An industrial machinery mechanic starts their day by reviewing maintenance schedules and prioritizing tasks.
They inspect machinery to identify any signs of wear or malfunction.
Throughout the day, they perform routine maintenance tasks such as lubrication, adjustments, and part replacements.
Mechanics also troubleshoot and repair any machinery issues that arise, often working under tight deadlines.
They use diagnostic tools to pinpoint problems and implement solutions to minimize downtime.
Mechanics play a crucial role in keeping industrial operations running smoothly.
Their work ensures that machinery operates efficiently and safely, preventing costly production delays.
By addressing issues promptly, they help maintain continuous production flow and high operational standards.
Their efforts directly impact the productivity and profitability of industrial operations.
The work of an industrial machinery mechanic requires dedication and skill.
They often work in challenging environments, handling heavy equipment and working in confined spaces.
Their attention to detail and commitment to quality ensure equipment reliability and safety.
Mechanics work long hours and must be ready to address urgent issues, demonstrating their reliability and expertise.
Industrial machinery mechanics deserve recognition for their hard work and dedication.
Their expertise is vital for maintaining industrial efficiency and preventing disruptions.
[E-Books for Sale]
The Big Book of 500 High-Paying Jobs in America: Unlock Your Earning Potential
$19.99 • 500 High-Paying Jobs • 330 pages
Explore 500 high-paying jobs in America and learn how to boost your career, earn more, and achieve success!
See All 500 High-Paying Jobs of this E-Book
1001 Professions Without a Degree: High-Paying American Jobs You Can Start Now
$19.99 • 1001 Professions Without a Degree • 174 pages
Discover 1001 high-paying jobs without a degree! Unlock career tips, skills, and success strategies for just $19.99!