Introduction
Industrial machinery maintenance is essential for ensuring smooth operations and preventing costly breakdowns.
Proper maintenance reduces downtime, keeping production lines running efficiently and without interruption.
Routine checks and timely repairs prevent small issues from escalating into major problems that could lead to expensive repairs or replacements.
Significance of Following Best Practices for Maintenance to Maximize the Lifespan and Efficiency of Equipment
By following best practices for maintenance, you can maximize the lifespan of your equipment, ensuring it continues to perform at its best for years to come.
Maintenance best practices also enhance overall efficiency, reducing energy consumption and operational costs.
Investing in regular maintenance leads to long-term savings by avoiding high costs associated with unexpected breakdowns and downtime.
Following a structured maintenance routine supports safety standards, protecting both workers and machinery.
Prioritizing maintenance helps create a safer work environment and ensures compliance with industry regulations.
In fact, industrial machinery maintenance is not just about keeping machines running; it‘s about ensuring consistent productivity, reducing costs, and maintaining a safe and efficient operation.
Regular Inspection and Monitoring
Schedule Routine Inspections
Regular inspections are crucial for maintaining industrial machinery in optimal condition.
Schedule routine inspections to identify any signs of wear or damage.
Inspections help in detecting potential issues before they lead to major problems.
Establish a detailed inspection checklist to cover all critical components of the machinery.
Ensure that inspections are performed consistently according to the manufacturer‘s recommendations.
Train maintenance personnel to recognize early signs of equipment failure.
Regularly review inspection reports to identify recurring issues or patterns.
Address any issues found during inspections promptly to avoid costly repairs.
Document all inspection activities and findings for future reference and compliance purposes.
Scheduled inspections help maintain machinery reliability and extend equipment lifespan.
Implementing a robust inspection routine reduces the risk of unexpected breakdowns and operational disruptions.
Use Monitoring Systems
Monitoring systems play a vital role in proactive machinery maintenance.
Install advanced monitoring systems to track equipment performance continuously.
These systems collect real-time data on machinery operations, providing valuable insights.
Utilize sensors and data analytics to detect abnormalities early on.
Set up alerts for unusual performance metrics that may indicate potential problems.
Regularly review performance data to identify trends and patterns.
Analyzing data helps in predicting when maintenance should be performed, reducing downtime.
Monitoring systems enable maintenance teams to address issues before they escalate.
Integrate monitoring systems with your maintenance management software for streamlined operations.
Ensure that monitoring systems are calibrated and maintained properly for accurate readings.
Using these systems enhances maintenance efficiency and helps prevent unexpected equipment failures.
Combine Inspections and Monitoring
Combining routine inspections with advanced monitoring systems creates a comprehensive maintenance strategy.
Use inspections to visually assess equipment condition and identify visible issues.
Employ monitoring systems to detect underlying problems and track performance trends.
Both approaches complement each other, ensuring a thorough maintenance process.
Inspections can validate findings from monitoring systems, and vice versa.
For example, if monitoring systems detect an anomaly, an inspection can confirm the issue’s cause.
Regularly update inspection protocols based on data insights from monitoring systems.
This combined approach ensures early detection and timely resolution of issues.
Integrating these practices helps maintain machinery in peak condition and supports overall operational efficiency.
Train and Educate Personnel
Effective maintenance also relies on well-trained personnel.
Provide ongoing training for your team on best practices for inspections and monitoring.
Ensure that they understand how to use monitoring systems effectively.
Educate staff on recognizing signs of wear and potential issues during inspections.
Regularly update training materials to include new technologies and methods.
Well-informed personnel can perform more accurate inspections and better utilize monitoring systems.
Promote a culture of continuous learning and improvement within your maintenance team.
Training enhances the team’s ability to prevent equipment failures and address issues promptly.
Invest in your team‘s skills to maximize the benefits of your maintenance practices.
Implementing best practices for industrial machinery maintenance involves scheduling routine inspections and utilizing monitoring systems.
Regular inspections help identify signs of wear and potential issues early.
Monitoring systems track equipment performance, detecting abnormalities before they cause major problems.
Combining these practices ensures comprehensive maintenance coverage.
Properly trained personnel further enhance the effectiveness of these strategies.
By following these best practices, you can maintain machinery in optimal condition, reduce downtime, and improve overall operational efficiency.
Implement Preventive Maintenance Programs
Develop a Comprehensive Maintenance Schedule
Developing a comprehensive maintenance schedule is essential for effective industrial machinery upkeep.
Start by consulting the manufacturer‘s recommendations for maintenance intervals and procedures.
These guidelines provide specific instructions tailored to each machine, ensuring optimal performance.
Combine this information with industry standards to create a robust maintenance plan.
Regularly review and update the schedule to reflect any changes in machine usage or operational conditions.
An effective schedule should include daily, weekly, monthly, and annual maintenance tasks.
Document all maintenance activities and track them to ensure that no tasks are overlooked.
Implementing a well-structured schedule minimizes unexpected breakdowns and extends the lifespan of machinery.
Perform Preventive Tasks
Performing preventive tasks is crucial in avoiding costly repairs and downtime.
Start with regular lubrication of moving parts to reduce friction and wear.
Check and replace filters to maintain air and fluid quality, which prevents contamination.
Regular calibration of machinery ensures that equipment operates within specified parameters, enhancing accuracy and efficiency.
Inspect belts, hoses, and connections for signs of wear and replace them as needed.
Tighten bolts and fittings to prevent leaks and malfunctions.
Conduct routine cleaning to remove debris and prevent buildup that can cause mechanical issues.
By performing these preventive tasks, you address potential problems before they escalate into significant breakdowns.
Benefits of Preventive Maintenance
Implementing a preventive maintenance program offers numerous benefits for industrial machinery.
Regular maintenance helps identify and address issues early, reducing the risk of unexpected failures.
This proactive approach minimizes downtime, which can significantly impact production schedules and costs.
Efficiently maintained equipment operates more smoothly, leading to higher productivity and better quality output.
Preventive maintenance also helps in extending the lifespan of machinery, delaying the need for costly replacements.
Furthermore, it ensures that equipment remains compliant with safety and regulatory standards.
By investing in preventive maintenance, you enhance the overall reliability and performance of your machinery.
A comprehensive maintenance schedule based on manufacturer recommendations and industry standards is essential for effective machinery upkeep.
Performing preventive tasks such as lubrication, filter changes, and calibration prevents breakdowns and extends equipment lifespan.
Regular maintenance minimizes unexpected failures, reduces downtime, and ensures machinery operates efficiently.
By adhering to a well-structured maintenance plan and executing preventive tasks, you ensure the longevity and reliability of your industrial machinery.
Implementing these best practices not only enhances equipment performance but also contributes to smoother operations and cost savings.
Investing in preventive maintenance is a strategic approach that benefits both the machinery and the overall production process.
Train Personnel
Provide Training for Maintenance Staff on Proper Machinery Maintenance Techniques and Safety Procedures
Training maintenance staff thoroughly is essential for maintaining high equipment standards and ensuring safety.
Begin by offering comprehensive training programs that cover the fundamental principles of machinery maintenance.
Include both theoretical knowledge and practical, hands-on sessions to reinforce learning.
Train staff on proper techniques for routine maintenance tasks, such as lubrication, cleaning, and adjustments, to prevent common issues.
Safety is a top priority in machinery maintenance.
Incorporate detailed safety procedures into training programs to minimize risks and protect employees.
Cover the correct use of personal protective equipment (PPE), safe handling of tools, and emergency procedures.
Regularly update training materials to reflect changes in safety regulations and technology advancements.
Conduct periodic refresher courses to keep maintenance staff updated on best practices and emerging technologies.
Encourage staff to engage in continuous learning through workshops, seminars, and industry conferences.
This ongoing education ensures they stay current with new techniques and equipment developments, contributing to improved maintenance outcomes.
Ensure Employees Are Familiar with Equipment Manuals and Understand Troubleshooting Steps
Equipment manuals are crucial resources for effective machinery maintenance.
Ensure that all maintenance staff have access to up-to-date manuals for each piece of equipment they service.
Manuals provide detailed instructions on equipment operation, maintenance schedules, and troubleshooting steps, which are essential for efficient repair and upkeep.
Training employees to read and understand these manuals is vital.
Teach staff how to locate and interpret relevant sections, such as maintenance procedures and troubleshooting guides.
Encourage them to familiarize themselves with the specific requirements and common issues associated with each piece of equipment.
Develop clear troubleshooting protocols that staff can follow when diagnosing and resolving equipment problems.
These protocols should be based on the information provided in the manuals and tailored to the specific machinery in use.
Regularly review and update troubleshooting procedures to incorporate feedback and lessons learned from past maintenance experiences.
Integrate Best Practices into Daily Operations
Incorporate these best practices into daily maintenance routines to achieve consistent results.
Develop a structured maintenance schedule that includes routine inspections, preventive measures, and corrective actions.
Use checklists and digital tools to track maintenance activities and ensure adherence to established procedures.
Promote a culture of accountability and continuous improvement among maintenance staff.
Encourage open communication and feedback regarding maintenance practices and equipment performance.
Regularly review maintenance processes and outcomes to identify areas for improvement and implement necessary changes.
Generally, implementing best practices for industrial machinery maintenance involves providing thorough training for maintenance staff and ensuring they are familiar with equipment manuals.
By focusing on proper maintenance techniques, safety procedures, and effective troubleshooting, you can enhance machinery performance and longevity.
Ongoing education and adherence to best practices will contribute to a safer, more efficient, and productive work environment.
Read: Radiologic Technologist: Work Environment Insights
Maintain Cleanliness
Keeping Machinery and Surrounding Areas Clean
Maintaining cleanliness in machinery and surrounding areas is crucial for optimal performance.
Dirt, debris, and contaminants can severely affect machinery efficiency.
Regular cleaning prevents these elements from accumulating and causing damage.
Ensure that work areas around machinery are free of clutter and spills.
Use appropriate cleaning materials and techniques to avoid damaging sensitive components.
Schedule routine cleaning tasks to keep equipment in peak condition.
This includes wiping down surfaces and removing any buildup that could impair function.
Keep floor areas clean to prevent debris from being tracked onto machinery.
Effective housekeeping practices contribute significantly to machinery longevity and reliability.
By maintaining a clean environment, you reduce the risk of unexpected breakdowns and prolong the life of your equipment.
Cleanliness also promotes a safer work environment by minimizing hazards related to spills and contamination.
Regular Cleaning and Inspection of Components
Regular cleaning and inspection of machinery components are essential for preventing performance issues.
Focus on components like filters, cooling systems, and electrical connections.
Clean filters regularly to ensure they function properly and do not obstruct airflow.
Dirty filters can cause overheating and decreased efficiency.
Inspect cooling systems to ensure they are free of debris and blockages.
Proper cooling is vital to prevent machinery from overheating and sustaining damage.
Check electrical connections for signs of wear, corrosion, or loose connections.
Clean connections and terminals to maintain proper electrical flow and prevent malfunctions.
Implement a routine maintenance schedule that includes these cleaning and inspection tasks.
Regularly reviewing component conditions allows for early detection of potential issues.
Addressing minor problems before they escalate reduces the risk of major repairs and downtime.
Comprehensive cleaning and inspection routines are key to maintaining machinery performance and reliability.
Best Practices for Effective Maintenance
Adopt best practices for effective industrial machinery maintenance to enhance performance and durability.
Start with a preventive maintenance plan that includes regular cleaning and inspections.
Document maintenance activities to track component conditions and identify trends.
Use manufacturer guidelines to ensure that cleaning methods and intervals are appropriate for each type of machinery.
Train maintenance personnel in proper cleaning techniques and safety procedures.
Employ specialized tools and equipment designed for cleaning and inspecting machinery components.
Incorporate condition monitoring technologies to detect early signs of wear or potential failures.
Regularly review and update maintenance practices based on equipment performance and feedback.
Encourage a culture of proactive maintenance within your team to address issues before they become significant problems.
By following these best practices, you maintain machinery in optimal condition and enhance overall operational efficiency.
In review, maintaining a clean environment around machinery and performing regular component cleaning are crucial for optimal performance.
Cleanliness prevents dirt and debris from impacting machinery function.
Regularly inspecting and cleaning components like filters, cooling systems, and electrical connections further ensures efficient operation.
Implementing these practices as part of a comprehensive maintenance plan enhances equipment longevity and reduces downtime.
By adhering to best practices and focusing on cleanliness, you create a more reliable and efficient work environment.
Read: Continuing Education for Radiologic Technologists
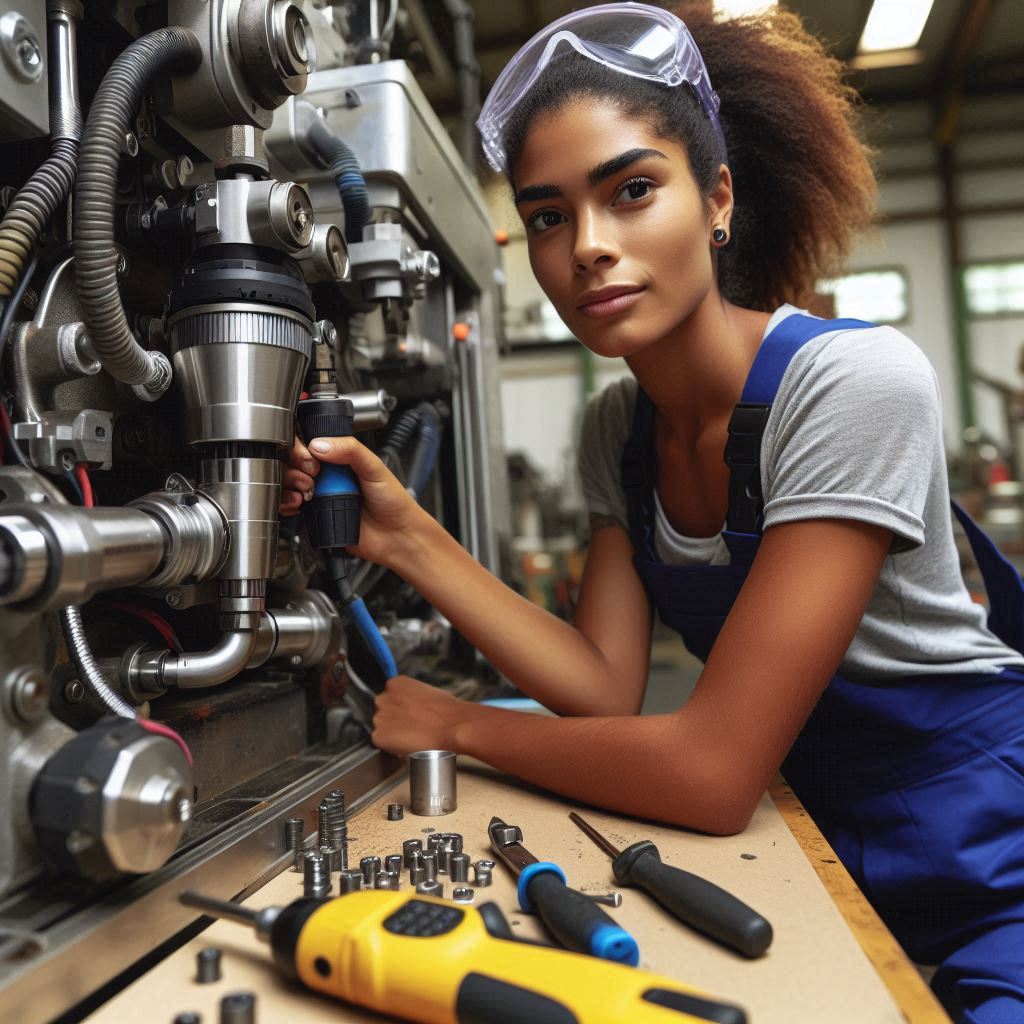
Regular Calibration and Alignment
Periodic Calibration of Equipment
Periodic calibration of equipment is essential for ensuring accuracy and reliability in industrial operations.
Regular calibration checks help maintain precise measurements and operational standards.
Without accurate calibration, machinery can produce faulty results, leading to inefficiencies and potential product defects.
Implement a routine calibration schedule based on manufacturer recommendations and operational demands.
This practice prevents errors and maintains high performance levels.
Checking Alignment of Moving Parts
Additionally, checking the alignment of moving parts is crucial for preventing premature wear and improving efficiency.
Misalignment can cause excessive friction, leading to accelerated wear and tear on machinery components.
Regular alignment checks and adjustments ensure that parts operate smoothly and efficiently.
Misaligned parts can also lead to increased energy consumption and higher operational costs.
Therefore, proper alignment is vital for optimizing machinery performance and extending its lifespan.
Routine Inspections and Maintenance
Routine inspections should include checking belts, gears, and shafts for proper alignment.
Use precision instruments to measure and adjust alignment as needed.
Ensure that all components are properly secured and functioning within specified tolerances.
This proactive approach helps avoid unexpected breakdowns and costly repairs.
Transform Your Career Today
Unlock a personalized career strategy that drives real results. Get tailored advice and a roadmap designed just for you.
Start NowTraining and Continuous Improvement
Training your maintenance team on the importance of these practices is also essential.
Ensure they understand the procedures for calibration and alignment, and provide them with the necessary tools and resources.
Regularly review and update maintenance protocols to incorporate the latest technologies and techniques.
This continuous improvement approach will keep your machinery in optimal condition.
Periodic calibration and proper alignment of moving parts are fundamental to maintaining industrial machinery.
These practices ensure that equipment operates accurately and efficiently, reducing the risk of premature wear and operational disruptions.
By incorporating these best practices into your maintenance routine, you can achieve reliable performance, extend machinery life, and enhance overall productivity.
Prioritize these steps to keep your operations running smoothly and effectively.
6. Use Genuine Parts and Fluids:
– Always use manufacturer-recommended parts and fluids during maintenance and repairs.
– Avoid using counterfeit or substandard components that could compromise equipment performance.
Always Use Manufacturer-Recommended Parts and Fluids During Maintenance and Repairs
Adhering to manufacturer recommendations for parts and fluids ensures optimal equipment performance.
Each machine is designed with specific components in mind.
Using manufacturer-recommended parts guarantees compatibility and reliability.
These parts meet the necessary quality and safety standards.
Similarly, using the prescribed fluids maintains proper lubrication and cooling, which prevents overheating and excessive wear.
Following these guidelines helps extend the lifespan of machinery.
It also minimizes the risk of unexpected breakdowns, which can halt production and incur significant costs.
Avoid Using Counterfeit or Substandard Components That Could Compromise Equipment Performance
Counterfeit or substandard components pose serious risks to machinery.
These components often lack the quality and precision of genuine parts.
Installing them can lead to poor performance, increased wear, and even catastrophic failures.
They may not fit properly or function as intended, leading to potential safety hazards.
The cost of repairs due to faulty components can far exceed the initial savings from using cheaper alternatives.
Substandard components can also void warranties, leaving you responsible for any future issues.
Ensuring that only high-quality, certified parts are used helps maintain the integrity of machinery.
Benefits of Using Genuine Parts and Fluids
Using genuine parts and fluids results in more reliable and efficient machinery operation.
These parts are designed to work seamlessly with your equipment, ensuring optimal performance.
Genuine parts also come with manufacturer support and warranties, which can be valuable if issues arise.
This support often includes technical assistance and coverage for potential defects.
By using recommended parts and fluids, you enhance the overall safety and productivity of your equipment.
Potential Consequences of Using Non-Recommended Parts and Fluids
The consequences of using non-recommended parts and fluids can be severe.
Machinery may experience reduced efficiency, frequent breakdowns, and shorter operational lifespans.
Inconsistent performance can lead to delays in production and higher maintenance costs.
Additionally, non-compliance with manufacturer guidelines can result in safety hazards for operators and other personnel.
It is essential to consider these risks when deciding on parts and fluids for maintenance and repairs.
Best Practices for Ensuring Quality and Compliance
To ensure quality and compliance, always source parts and fluids from reputable suppliers.
Verify that components are genuine and meet the manufacturer‘s specifications.
Keep detailed records of all maintenance activities, including parts used and service dates.
Regularly review and update your maintenance procedures to align with manufacturer recommendations.
Train maintenance staff to recognize and avoid counterfeit or substandard components.
Implementing these practices helps maintain high standards for equipment performance and safety.
In the end, using manufacturer-recommended parts and fluids is crucial for maintaining the performance and safety of industrial machinery.
Avoiding counterfeit or substandard components is equally important to prevent costly repairs and potential safety hazards.
By adhering to these best practices, you ensure that your equipment remains reliable, efficient, and safe throughout its operational life.
Read: CAD Technician vs. Draftsman: Key Differences
Discover More: Best Certifications for Aspiring Cybersecurity Analysts
Document Maintenance Activities
Keep Detailed Records of All Maintenance Activities
Effective industrial machinery maintenance relies heavily on thorough documentation and tracking.
Start by documenting every maintenance task performed, including the date, specific tasks, and any issues identified.
This information provides a clear history of each machine’s upkeep and helps in pinpointing recurring problems.
Accurate record-keeping supports preventive maintenance strategies.
By reviewing past maintenance activities, you can identify patterns or frequent issues, which can guide future maintenance plans.
For instance, if a machine consistently requires specific repairs, you might adjust your maintenance schedule to address these needs proactively.
Detailed records also aid in understanding the machinery’s performance and predicting when certain components might need replacement.
Use Maintenance Software or Logs
Use maintenance software or logs to streamline this process.
Software tools can automate many aspects of record-keeping, reducing human error and improving efficiency.
Choose a maintenance management system that fits your operational needs.
These systems often come with features such as automated reminders for upcoming maintenance tasks and digital logs that are easily accessible.
Maintenance software provides a centralized platform for tracking equipment history.
This centralization makes it easier to review maintenance records and make informed decisions about machinery care.
Additionally, software can generate reports and analytics that help assess the effectiveness of your maintenance strategies.
Regularly reviewing these reports ensures you stay informed about the machinery’s condition and any emerging trends.
Schedule Future Maintenance Tasks
Scheduling future maintenance tasks is simplified with maintenance software.
Set up alerts for upcoming tasks based on the equipment’s usage or manufacturer recommendations.
Automated scheduling helps prevent missed maintenance activities and reduces the risk of unplanned downtime.
By ensuring that maintenance tasks are completed on time, you can avoid unexpected failures and extend the lifespan of your equipment.
Logs and software also facilitate compliance with industry regulations and standards.
Detailed records demonstrate adherence to required maintenance schedules and practices.
This is essential for passing audits and maintaining safety standards.
Ensure that your records are accurate and up-to-date to meet regulatory requirements and avoid potential penalties.
Facilitate Communication Among Team Members
Effective communication among team members is supported by maintaining detailed records.
Share insights from maintenance logs with relevant personnel to keep everyone informed about equipment status and issues.
This shared knowledge improves coordination and ensures that all team members are aware of ongoing maintenance activities.
Ultimately, keeping detailed records and using maintenance software are best practices for industrial machinery maintenance.
These practices not only enhance the efficiency of your maintenance program but also contribute to the overall reliability and performance of your machinery.
Invest in good record-keeping practices and maintenance tracking tools to ensure that your equipment remains in optimal condition and continues to support your operational goals effectively.
Read: Best Online Courses for CAD Technician Training
Explore Further: Balancing Work and Life as a Geotechnical Engineer
Monitor and Measure Performance
Track Key Performance Indicators (KPIs)
Effective maintenance of industrial machinery hinges on tracking key performance indicators (KPIs).
Downtime, energy consumption, and maintenance costs are crucial metrics.
Downtime refers to periods when equipment is non-operational.
Monitoring this helps in identifying issues causing interruptions.
Energy consumption measures the power used by machinery.
Efficient use of energy can significantly cut costs and enhance performance.
Maintenance costs include expenses for repairs, parts, and labor.
Keeping these costs in check improves the overall financial health of operations.
Use Data Analytics to Identify Trends
Using data analytics plays a vital role in maintenance optimization.
By analyzing KPIs, you can identify trends and patterns.
Data analytics helps predict potential failures before they occur.
This predictive approach allows for timely interventions, reducing unexpected downtimes.
Analyzing historical data provides insights into machinery performance over time.
It helps pinpoint recurring issues and areas needing improvement.
Optimize Maintenance Schedules
Optimizing maintenance schedules is another benefit of data analytics.
Traditional maintenance schedules often rely on time-based intervals.
Data-driven schedules are based on actual machinery condition and performance data.
This ensures maintenance activities are performed only when necessary, reducing unnecessary work.
Effective scheduling also minimizes equipment downtime and extends machinery life.
Improve Overall Equipment Effectiveness (OEE)
Improving overall equipment effectiveness (OEE) is a key goal.
OEE measures how well equipment performs relative to its full potential.
It takes into account availability, performance efficiency, and quality.
High OEE indicates optimal machinery performance, while low OEE signals room for improvement.
By tracking KPIs and using data analytics, you can enhance OEE.
Regularly review KPI data to assess performance and adjust maintenance strategies accordingly.
Benchmark Performance Against Industry Standards
Data analytics also helps in benchmarking performance against industry standards.
Comparing your machinery‘s performance to that of similar equipment provides context.
It highlights areas where your operations excel or lag behind.
Benchmarking fosters continuous improvement and drives competitiveness.
Setting performance targets based on these benchmarks can guide maintenance efforts.
Transform Your Career Today
Unlock a personalized career strategy that drives real results. Get tailored advice and a roadmap designed just for you.
Start NowIntegrate Data Analytics Tools
Integrating data analytics tools into maintenance practices offers a competitive advantage.
Advanced software can provide real-time monitoring and analysis.
These tools generate actionable insights that can be used to refine maintenance strategies.
Real-time data allows for immediate response to emerging issues, reducing the likelihood of costly breakdowns.
Regularly Review and Update Practices
Regularly review and update your data analytics practices.
As technology evolves, so do analytical tools and methods.
Staying current with these advancements ensures that your maintenance strategies remain effective and relevant.
Investing in the right tools and training for your team can lead to substantial improvements in machinery maintenance.
In conclusion, tracking KPIs and utilizing data analytics are essential for effective industrial machinery maintenance.
By focusing on downtime, energy consumption, and maintenance costs, and leveraging data for optimization, you can enhance equipment performance.
Regularly analyze trends and adjust maintenance schedules to improve overall equipment effectiveness.
This proactive approach will lead to greater operational efficiency and reduced costs.
You Might Also Like: Field Service Technician Remote Troubleshooting
You Might Also Like: Importance of Safety in the Mining Engineering Field
Conclusion
Following best practices for industrial machinery maintenance is crucial to ensure optimal performance and reliability.
Proactive maintenance significantly reduces the risk of unexpected breakdowns, which can lead to costly downtime.
Regular inspections and servicing allow you to identify and address potential issues before they escalate into major problems.
This approach not only prevents interruptions but also enhances productivity, as well-maintained machinery operates more efficiently and consistently.
In addition to boosting productivity, proactive maintenance plays a vital role in reducing energy consumption and operational costs.
Equipment that is properly maintained requires less energy to function, contributing to lower utility bills and a more sustainable operation.
Moreover, consistent maintenance efforts extend the lifespan of your machinery, delaying the need for expensive replacements and capital investments.
By adhering to these best practices, you also improve workplace safety, as well-maintained equipment is less likely to malfunction or cause accidents.
In the long run, following best practices for industrial machinery maintenance saves money, improves efficiency, and ensures the longevity of your equipment.
[E-Books for Sale]
The Big Book of 500 High-Paying Jobs in America: Unlock Your Earning Potential
$19.99 • 500 High-Paying Jobs • 330 pages
Explore 500 high-paying jobs in America and learn how to boost your career, earn more, and achieve success!
See All 500 High-Paying Jobs of this E-Book
1001 Professions Without a Degree: High-Paying American Jobs You Can Start Now
$19.99 • 1001 Professions Without a Degree • 174 pages
Discover 1001 high-paying jobs without a degree! Unlock career tips, skills, and success strategies for just $19.99!