Introduction
Reducing shipping and receiving errors is essential for any business aiming to maintain high standards and efficiency.
Mistakes in these areas can lead to delayed orders, lost products, and unsatisfied customers, directly affecting the company’s reputation.
Customers expect accurate deliveries, and even a single error can weaken their trust and loyalty.
Additionally, shipping and receiving mistakes increase operational costs, waste resources, and slow down productivity, impacting overall business performance.
When companies focus on minimizing errors, they streamline operations, improve customer satisfaction, and enhance brand image.
Effective error reduction not only saves money but also ensures that teams work efficiently and deliver consistently.
By adopting proactive strategies, businesses can prevent common mistakes, improve order accuracy, and reduce the likelihood of returns or replacements.
Clear communication and standardized processes play a critical role in error reduction.
Training employees to follow best practices and utilizing technology to automate repetitive tasks can significantly minimize mistakes.
Digital tools, such as barcode scanners and inventory management systems, enhance accuracy by tracking shipments and verifying orders in real time.
Maintaining an organized workspace further aids error prevention.
A clean, well-organized receiving and shipping area allows employees to locate items quickly, process orders accurately, and reduce mistakes.
Regularly auditing and monitoring shipping and receiving activities enables businesses to identify error patterns and implement corrective measures promptly.
In summary, prioritizing error reduction in shipping and receiving is crucial for long-term success.
Reducing mistakes not only protects a company’s reputation but also boosts customer satisfaction and strengthens overall efficiency.
Standardize Procedures
Standardizing procedures is crucial in reducing shipping and receiving errors.
By establishing clear guidelines and protocols for all employees to follow, businesses can streamline their operations and minimize costly mistakes.
Here are some key steps to help standardize procedures and improve accuracy in shipping and receiving processes:
Implement Clear Guidelines
One of the first steps in standardizing procedures is to create clear and detailed guidelines for each step of the shipping and receiving process.
This includes instructions on how to pack items, label packages, and verify shipments.
Transform Your Career Today
Unlock a personalized career strategy that drives real results. Get tailored advice and a roadmap designed just for you.
Start NowBy providing employees with a clear roadmap to follow, businesses can reduce the risk of errors and ensure consistency in operations.
Train Employees
Once procedures are established, it is essential to train all employees on the proper protocols to follow.
This training should include hands-on practice, demonstrations, and written materials to reinforce key steps.
By ensuring that all team members are well-trained, businesses can minimize the likelihood of errors and improve efficiency in shipping and receiving operations.
Consistent Implementation
To prevent errors, it is important for employees to consistently implement the standardized procedures in their daily tasks.
Regular monitoring and supervision can help ensure that all team members adhere to the established guidelines.
By reinforcing the importance of following procedures, businesses can create a culture of accountability and accuracy in shipping and receiving processes.
Regular Audits
Regular audits can help identify any gaps or inconsistencies in the implementation of standardized procedures.
By conducting periodic checks and reviews, businesses can pinpoint areas for improvement and address any issues before they lead to errors.
Audits also provide an opportunity to gather feedback from employees and make necessary adjustments to enhance the efficiency of shipping and receiving operations.
Continuous Improvement
In addition to standardizing procedures, businesses should focus on continuous improvement to further reduce shipping and receiving errors.
This includes staying up-to-date on industry best practices, incorporating feedback from employees and customers, and investing in training and development programs.
By fostering a culture of continuous improvement, businesses can optimize their operations and deliver better outcomes for their customers.
By standardizing procedures, businesses can minimize errors in shipping and receiving processes, improve efficiency, and enhance overall customer satisfaction.
Investing time and resources in establishing clear guidelines, training employees, and implementing consistent practices can help businesses achieve greater accuracy and success in their operations.
Read: Future of Customs Brokerage: Emerging Technologies
Implement Quality Control Measures
Conduct regular quality checks throughout the shipping and receiving process to catch errors early
Quality control measures are essential in reducing shipping and receiving errors.
By implementing these measures, businesses can ensure that products are shipped and received accurately, leading to improved customer satisfaction and increased efficiency.
Regular quality checks should be conducted at various stages of the shipping and receiving process.
This includes checking the accuracy of order details, verifying inventory counts, and inspecting the condition of products.
Transform Your Career Today
Unlock a personalized career strategy that drives real results. Get tailored advice and a roadmap designed just for you.
Start NowBy catching errors early on, businesses can address issues promptly and prevent them from escalating.
Utilize technology such as barcode scanners and tracking systems to streamline operations and reduce mistakes
Technology plays a crucial role in streamlining operations and minimizing mistakes.
Barcode scanners can be used to scan products and verify their details, reducing the risk of human error.
Tracking systems allow businesses to monitor the movement of goods in real-time, enabling them to identify potential issues and take corrective action.
By leveraging technology, businesses can automate repetitive tasks, increase accuracy, and improve overall efficiency in the shipping and receiving process.
This not only reduces errors but also saves time and resources, ultimately benefiting the bottom line.
In fact, implementing quality control measures such as conducting regular checks and utilizing technology is paramount in reducing shipping and receiving errors.
By investing in these measures, businesses can enhance their operations, minimize mistakes, and ensure a seamless shipping and receiving process.
Read: Customs Broker Salary: What to Expect in This Career
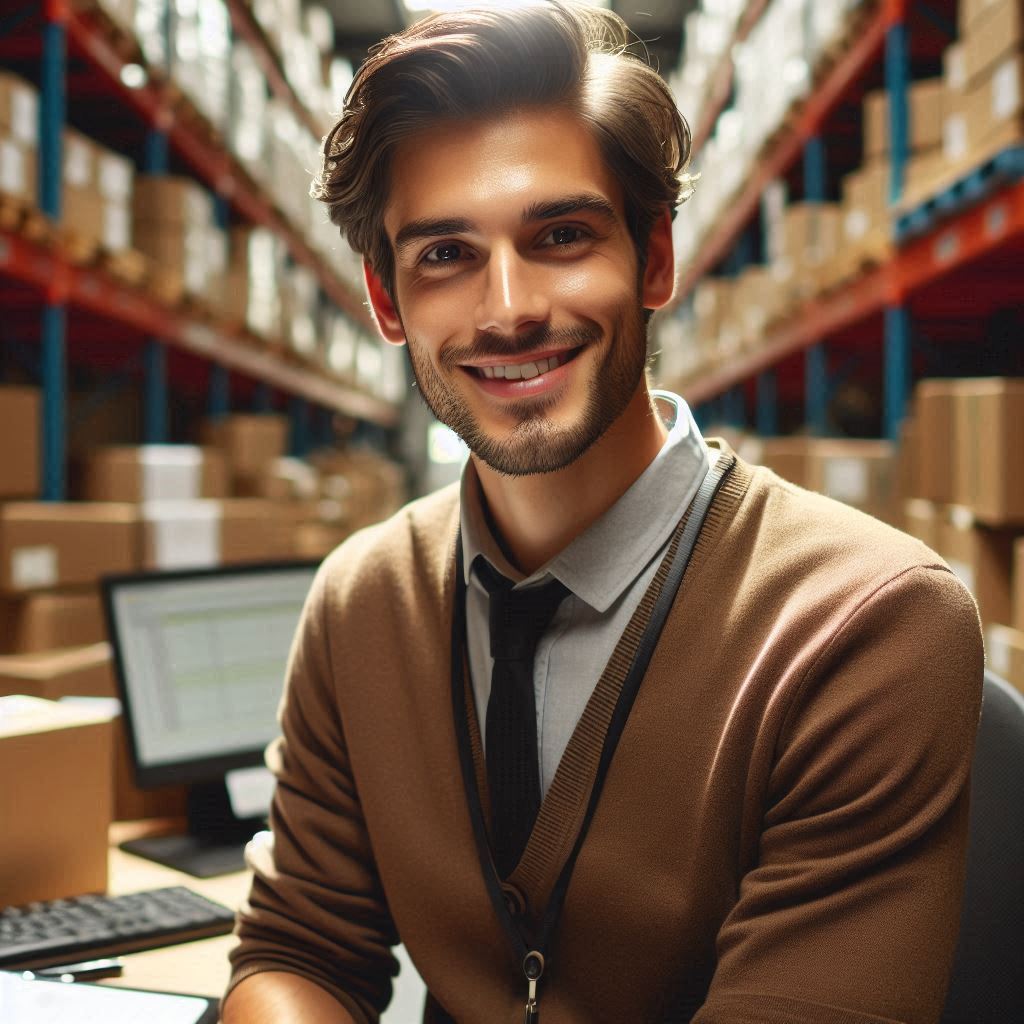
Invest in Training
Provide ongoing training for employees involved in shipping and receiving to improve skills and knowledge
Investing in training for employees involved in shipping and receiving is crucial to reducing errors in this critical process.
By continuously improving the skills and knowledge of your staff, you can ensure that they are equipped to handle their responsibilities effectively and efficiently.
Ongoing training allows employees to stay up-to-date with the latest techniques and technologies in shipping and receiving.
With the rapid advancements in logistics and supply chain management, it is essential for staff to be well-informed and prepared to adapt to changes in the industry.
Educate staff on best practices and potential errors to watch out for in their daily tasks
Educating your staff on best practices can help prevent common errors that may occur during the shipping and receiving process.
By highlighting potential errors and providing guidance on how to avoid them, you can minimize the risk of costly mistakes that could impact your business operations.
Training should cover a range of topics, including proper handling of products, accurate labeling and packaging, and efficient inventory management.
By ensuring that your staff are well-trained in these areas, you can reduce the likelihood of errors that may lead to delays or inaccuracies in shipments.
Additionally, training can help employees recognize warning signs of potential errors before they escalate into larger issues.
By empowering your staff to identify and address problems early on, you can prevent costly mistakes that could impact customer satisfaction and your bottom line.
Overall, investing in training for employees involved in shipping and receiving is a proactive approach to reducing errors in your supply chain operations.
Transform Your Career Today
Unlock a personalized career strategy that drives real results. Get tailored advice and a roadmap designed just for you.
Start NowBy providing your staff with the tools and knowledge they need to succeed, you can improve efficiency, accuracy, and overall performance in this critical area of your business.
Read: Streamlining the Shipping and Receiving Process
Utilize Checklists
Develop checklists for each step of the shipping and receiving process to ensure nothing is missed
Utilizing checklists can greatly reduce shipping and receiving errors by promoting accuracy and consistency.
Develop clear checklists covering each step of the shipping and receiving process.
Include essential tasks, such as verifying order details, checking product conditions, and ensuring correct quantities.
Make sure each checklist is concise and easy to follow, focusing on key actions.
Encourage employees to use these checklists as a tool for verification and accuracy
Encourage employees to view checklists as valuable tools for maintaining accuracy.
Train staff to check off items as they complete each step, confirming nothing is overlooked.
Make checklists a standard part of the workflow to create consistency across teams.
Reinforce the importance of using checklists for all employees, regardless of experience level.
Regularly review and update checklists to reflect changes in procedures or products.
Gather feedback from employees to ensure checklists remain relevant and useful.
Set expectations that following checklists is non-negotiable for every shipment or receipt.
Provide easy access to checklists, whether through printed copies or digital tools, so they’re always available.
Supervisors should monitor compliance, encouraging employees to complete checklists for every task.
Highlight the impact of checklists on reducing errors and improving efficiency.
When employees understand the benefits, they’re more likely to use checklists consistently.
Regularly recognize and reward employees who demonstrate checklist compliance and accuracy in their work.
Incorporate checklists into quality control audits, and make adjustments as needed based on findings.
With consistent use, checklists will become second nature, helping teams catch potential errors before they become costly issues.
Transform Your Career Today
Unlock a personalized career strategy that drives real results. Get tailored advice and a roadmap designed just for you.
Start NowRead: Shipping and Receiving Compliance Standards
Improve Communication
Improving communication is crucial in reducing shipping and receiving errors. When there is a lack of clear communication, mistakes are bound to happen which can result in delays, lost or damaged shipments, and dissatisfied customers.
Here are some ways to enhance communication to ensure a smooth process:
Foster open communication between departments involved in shipping and receiving to prevent misunderstandings
Establish regular meetings or check-ins between the shipping and receiving departments to discuss ongoing orders, issues, and any changes in processes.
Encourage team members to share any concerns or suggestions they may have to improve the workflow.
Utilize communication tools such as email, messaging apps, or project management software to keep everyone informed and aligned.
Encourage employees to ask questions and seek clarification when needed to avoid errors
Create a culture where employees feel comfortable asking for clarification on tasks, instructions, or expectations.
Provide training on how to effectively communicate and ask questions to avoid misunderstandings.
Emphasize the importance of clear communication in preventing errors and ensuring that shipments are accurate and timely.
By improving communication within the shipping and receiving departments, you can minimize errors, streamline processes, and enhance overall efficiency.
Remember, clear and open communication is the key to a successful shipping and receiving operation.
Analyze Past Errors
Review past shipping and receiving errors to identify common trends and root causes
Analyzing past errors is a crucial step in reducing shipping and receiving errors.
By reviewing past mistakes, you can gain valuable insights into the common trends and root causes that contribute to these errors.
This information can then be used to implement preventative measures and address any recurring issues proactively.
When analyzing past errors, it is important to look for patterns or trends that may indicate underlying issues within your shipping and receiving processes.
By identifying these common trends, you can focus your efforts on implementing targeted solutions that will help prevent similar errors from occurring in the future.
Use this data to implement preventative measures and address any recurring issues proactively
Reviewing past errors can also help you identify any root causes that may be contributing to the mistakes.
Whether it’s a lack of training, poor communication, or inefficient processes, understanding the underlying reasons for errors is key to implementing effective solutions.
One way to analyze past errors is to create a spreadsheet or database to track and categorize each mistake.
By documenting the type of error, its frequency, and any relevant details, you can start to see patterns emerge that will help you pinpoint areas for improvement.
Transform Your Career Today
Unlock a personalized career strategy that drives real results. Get tailored advice and a roadmap designed just for you.
Start NowOnce you have compiled data on past errors, take the time to analyze this information thoroughly.
Look for common themes or recurring issues that are causing errors in your shipping and receiving operations.
This analysis will help you prioritize which areas need immediate attention and which ones can be addressed more long-term.
Based on your analysis, create a list of preventative measures that can help reduce the likelihood of future errors.
This may include implementing additional training for staff, improving communication protocols, or updating your shipping and receiving processes to make them more efficient and error-proof.
In addition to implementing preventative measures, it is important to address any recurring issues proactively.
This may involve conducting regular audits of your shipping and receiving processes, seeking feedback from staff members, or making adjustments to your systems to prevent similar errors from happening in the future.
By analyzing past errors and taking proactive measures to address them, you can significantly reduce the number of shipping and receiving errors in your operations.
This proactive approach will not only help you improve efficiency and accuracy but also enhance customer satisfaction and loyalty.
Set Clear Expectations
Clearly communicate performance expectations and error tolerance levels to employees
Clearly defined expectations reduce shipping and receiving errors significantly.
Start by outlining specific performance goals and error tolerance limits for all employees.
Make these guidelines easily accessible, ensuring every team member understands their responsibilities.
When employees know the standards, they perform tasks more accurately, reducing mistakes.
Regularly discuss these expectations in team meetings and training sessions to reinforce them.
Encourage employees to ask questions, fostering a culture of transparency and accountability.
Accountability measures hold employees responsible for errors, motivating them to focus on quality.
Establish accountability measures for errors and provide feedback for improvement
Establish a process to track performance and identify any error patterns.
If mistakes occur, review them with employees to understand the cause.
Offer constructive feedback, helping employees learn from errors and improve their skills.
Positive feedback on successful performance reinforces their commitment to accuracy.
Transform Your Career Today
Unlock a personalized career strategy that drives real results. Get tailored advice and a roadmap designed just for you.
Start NowConsider implementing an incentive program to reward consistent accuracy and accountability.
Recognition for meeting or exceeding standards motivates employees to maintain quality.
By setting clear expectations and accountability, you establish a strong foundation for reducing shipping and receiving error.
Regularly Review and Revise Procedures
Continuously monitor and evaluate shipping and receiving procedures for effectiveness
Regularly reviewing and revising shipping and receiving procedures helps reduce errors and improve efficiency.
Continuously monitor all aspects of these processes to identify potential issues.
Evaluate the effectiveness of current practices and determine if they meet accuracy standards.
When errors are found, analyze them thoroughly to understand their root causes.
Use this information to make necessary adjustments that prevent similar mistakes in the future.
Adapt procedures to align with changing business requirements and industry standards.
Stay updated on the latest tools and technologies that improve accuracy in shipping and receiving.
Implement any new methods that could enhance efficiency and accuracy.
Communicate changes clearly to the entire team to ensure everyone follows updated procedures.
Make necessary adjustments and updates to prevent errors and adapt to changing business needs
Training employees regularly on revised procedures is crucial to maintaining high performance and minimizing errors.
Encourage team members to provide feedback on the effectiveness of these changes. Use their insights to further refine and improve processes.
Schedule routine checks to ensure all procedures are being followed correctly.
Document each review to track improvements and maintain consistent performance.
This ongoing evaluation not only reduces errors but also boosts productivity in the long term.
Conclusion
Reducing shipping and receiving errors is crucial for efficient operations and customer satisfaction.
Key points discussed include implementing barcode scanners, using proper labeling, conducting regular audits, and providing employee training.
It is essential to adopt these strategies to improve accuracy, save costs, and maintain a positive reputation in the market.
Transform Your Career Today
Unlock a personalized career strategy that drives real results. Get tailored advice and a roadmap designed just for you.
Start NowBy taking proactive measures to minimize errors, businesses can enhance productivity, streamline processes, and increase customer loyalty.
A focus on reducing shipping and receiving errors is a worthwhile investment that can lead to long-term success and growth.