Introduction
A material handler plays a vital role in warehouses and manufacturing settings.
They are responsible for moving, storing, and managing materials.
Their work directly influences productivity and operational efficiency.
Efficiency is crucial for material handlers.
It affects how quickly products move through the supply chain.
When material handlers work efficiently, they reduce delays and ensure smooth operations.
This efficiency improves inventory management and helps meet customer demands.
In a busy warehouse, material handlers handle various tasks.
They load and unload trucks, organize inventory, and prepare items for shipping.
By streamlining these processes, handlers can minimize errors and maximize output.
Improving efficiency also reduces labor costs.
When material handlers complete tasks faster, fewer hours are required to achieve the same results.
This cost savings can enhance a company’s bottom line.
Additionally, efficient material handling promotes safety.
A well-organized workspace reduces the risk of accidents.
When handlers know where materials are located, they can work with greater confidence.
Technology plays a significant role in improving efficiency.
Implementing warehouse management systems can optimize routing and inventory tracking.
This technology allows material handlers to locate items quickly and reduce unnecessary movement.
Regular training and development also enhance efficiency.
Transform Your Career Today
Unlock a personalized career strategy that drives real results. Get tailored advice and a roadmap designed just for you.
Start NowProviding material handlers with updated skills ensures they remain effective.
Training programs can cover topics such as proper lifting techniques and equipment operation.
In summary, the role of a material handler is crucial in any warehouse or manufacturing environment.
Their efficiency impacts overall operations, productivity, and safety.
By focusing on training and leveraging technology, organizations can significantly enhance their material handling processes.
Organize Work Area
As a material handler, maximizing efficiency is crucial to ensuring productivity and meeting deadlines.
One effective way to improve efficiency is by organizing your work area effectively.
Clear Clutter
Start by decluttering your work area.
Remove any unnecessary items or materials that are not related to your current tasks.
This will create more space and make it easier to access the materials you need.
Regular Cleaning
Establish a routine for cleaning your work area.
This includes sweeping the floors, wiping down surfaces, and organizing tools and equipment.
A clean workspace not only improves efficiency but also creates a more pleasant working environment.
Utilize Storage Solutions
Invest in storage containers, shelves, and cabinets to keep materials organized and easily accessible.
Utilize color-coded bins or labels to categorize different types of materials, making it quicker to find what you need.
Implement a Labeling System
Label shelves, bins, and storage containers with clear and easy-to-read labels.
Use a consistent naming convention for products and materials to avoid confusion and reduce search time.
This simple step can save a significant amount of time in the long run.
Arrange Materials Strategically
Position frequently used materials and tools within arm’s reach to minimize movement and streamline tasks.
Keep less frequently used items in designated storage areas to prevent clutter and maintain an efficient workflow.
Transform Your Career Today
Unlock a personalized career strategy that drives real results. Get tailored advice and a roadmap designed just for you.
Start NowCreate Work Zones
Assign specific areas for different tasks or types of materials.
This helps in reducing confusion and allows for a more structured workflow.
For example, designate one area for incoming materials, another for outgoing shipments, and so on.
By implementing these strategies for organizing your work area, you can significantly improve efficiency as a material handler and optimize your productivity levels.
Remember, a well-organized workspace is the foundation for success in any handling operation.
Read: Material Handler Job Outlook and Growth
Streamline Processes
Analyze current workflow and identify areas for improvement
To improve efficiency as a material handler, start by analyzing your current workflow.
Review each step involved in handling materials.
Identify areas that cause delays or confusion.
Speak with team members to gather insights on potential improvements.
Implement lean principles to reduce unnecessary steps and eliminate bottlenecks
Next, implement lean principles to streamline operations.
Focus on reducing unnecessary steps that do not add value.
Examine your processes and remove redundant actions.
This helps in minimizing waste and maximizing productivity.
Identify bottlenecks within your workflow.
Look for points where materials slow down or stack up.
Address these issues quickly to keep operations flowing smoothly.
Use visual management tools to monitor progress and highlight areas needing attention.
Encourage open communication among your team members.
Foster a culture where employees feel comfortable sharing suggestions for improvement.
Transform Your Career Today
Unlock a personalized career strategy that drives real results. Get tailored advice and a roadmap designed just for you.
Start NowRegularly hold meetings to discuss challenges and brainstorm solutions together.
Utilize technology to enhance efficiency. Invest in equipment that automates repetitive tasks.
Implement software solutions that track inventory and streamline order processing. This not only saves time but also reduces human error.
Train employees on new processes and technology.
Ensure they understand the importance of following updated procedures.
Provide ongoing support and resources to help them adapt.
Finally, continuously monitor and evaluate your streamlined processes.
Set performance metrics to measure efficiency gains.
Review these metrics regularly and adjust strategies as needed.
By committing to continuous improvement, you can maintain high levels of efficiency in material handling.
Read: Effective Communication for Material Handlers
Utilize Technology to Improve Efficiency as a Material Handler
Invest in inventory management software to track materials and streamline ordering processes
Investing in technology can significantly enhance efficiency in material handling.
Start by implementing inventory management software.
This software helps track materials, manage stock levels, and streamline ordering processes.
With real-time data, you can make informed decisions about inventory needs.
Use barcode scanners or RFID technology for faster and more accurate inventory control
Next, consider using barcode scanners.
These devices simplify the tracking process and reduce manual entry errors.
Scanning barcodes allows for quick identification of products, which speeds up the handling process.
Additionally, barcode scanners integrate easily with inventory management software, creating a seamless workflow.
For even greater efficiency, explore RFID technology.
Transform Your Career Today
Unlock a personalized career strategy that drives real results. Get tailored advice and a roadmap designed just for you.
Start NowRFID systems use radio waves to automatically identify and track materials.
This technology enables faster and more accurate inventory control.
With RFID, you can quickly locate items without manual scanning, saving time during operations.
Incorporating technology also improves communication among team members.
Utilize cloud-based platforms to share inventory data in real-time.
This way, all staff can access up-to-date information, reducing misunderstandings and errors.
Improved communication fosters collaboration and enhances overall efficiency.
Furthermore, train your staff on the new technology.
Effective training ensures that everyone understands how to use the software and devices.
This minimizes mistakes and increases confidence among team members.
Regular training sessions can help keep skills sharp and up to date.
Lastly, continuously evaluate and adapt your technological solutions.
Monitor the effectiveness of your chosen tools and make adjustments as needed.
Stay informed about emerging technologies that could further enhance your efficiency.
By embracing technology, you can significantly improve your material handling processes and achieve better results.
Read: Physical Requirements for Material Handlers
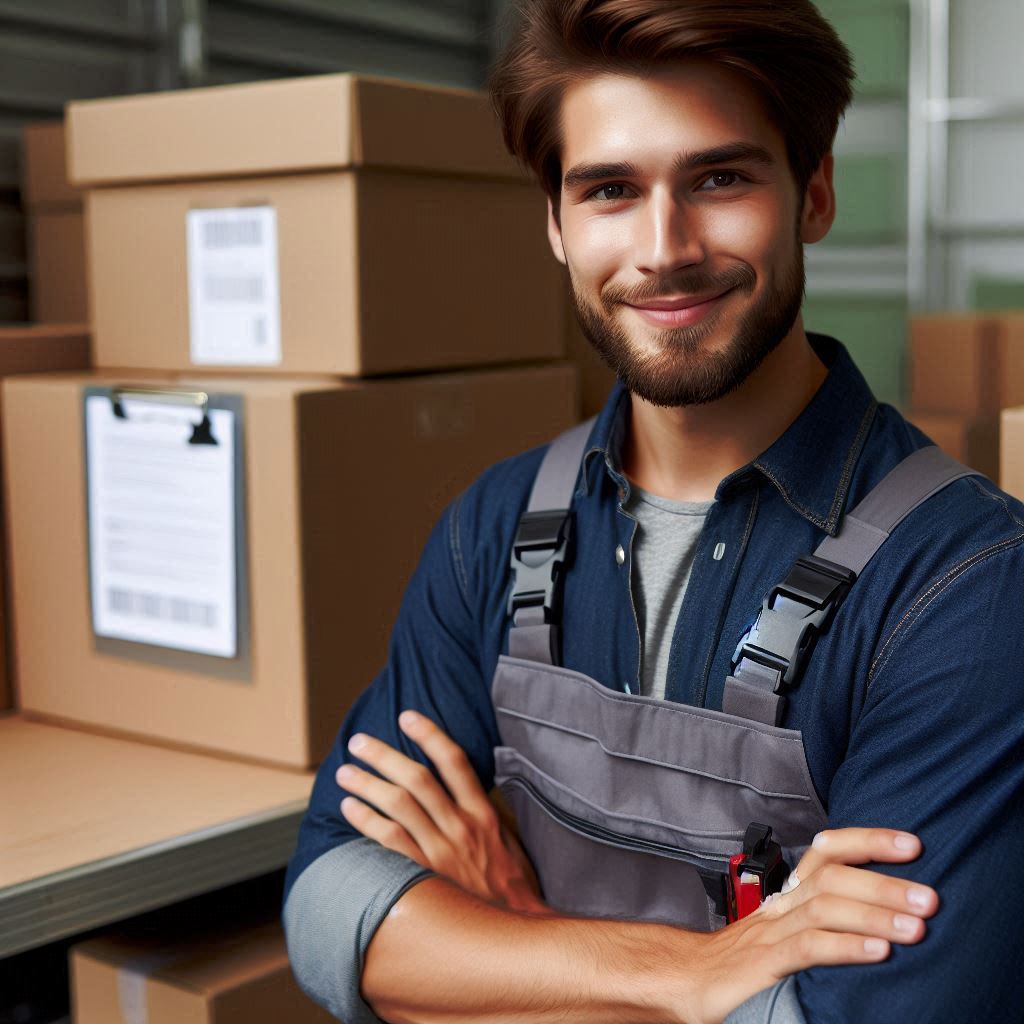
Prioritize Safety
Ensuring safety in the workplace is crucial for material handlers to perform their duties efficiently.
By prioritizing safety, organizations can not only protect their employees but also improve productivity and reduce costly incidents.
Proper Training
One of the key ways to enhance safety as a material handler is by providing adequate training to employees on proper lifting techniques.
Improper lifting can lead to serious musculoskeletal injuries, which can result in downtime and decreased efficiency.
Transform Your Career Today
Unlock a personalized career strategy that drives real results. Get tailored advice and a roadmap designed just for you.
Start NowOrganizations should invest in training programs that educate employees on the correct way to lift heavy objects, emphasizing the importance of using their legs instead of their back to avoid strain.
By teaching employees how to lift and handle materials safely, companies can reduce the risk of injuries and improve overall efficiency.
Following Safety Protocols
In addition to proper training, it is essential for material handlers to follow safety protocols and guidelines at all times.
This includes wearing appropriate personal protective equipment, such as gloves and safety shoes, to prevent injuries.
Furthermore, material handlers should be well-versed in the protocols for operating equipment, such as forklifts and conveyor belts, to prevent accidents in the workplace.
By adhering to safety guidelines, employees can minimize risks and ensure a safe working environment for themselves and their colleagues.
Overall, prioritizing safety in the workplace is not only beneficial for the well-being of employees but also crucial for improving efficiency as a material handler.
By training employees on proper lifting techniques and ensuring all safety protocols are followed, organizations can create a safer work environment that fosters productivity and minimizes disruptions.
Read: Steps to Becoming a Certified Material Handler
Cross-train Employees
Provide training opportunities for employees to learn different aspects of the material handling process
Cross-training employees in a material handling environment is crucial for improving efficiency.
By providing opportunities for employees to learn various aspects of the material handling process, you can ensure that there are versatile and skilled workers available to handle different tasks when needed.
Cross-trained employees can fill in for each other during peak times or absences to maintain productivity
When employees are cross-trained, they can easily step in to assist their colleagues during peak times or when someone is absent.
This flexibility helps maintain productivity levels and ensures that operations run smoothly even when facing unexpected challenges.
Moreover, cross-training employees can lead to a more motivated workforce. Learning new skills and being able to contribute in different areas can boost employee morale and job satisfaction.
This, in turn, can improve overall performance and efficiency in the workplace.
Additionally, cross-training helps in creating a more cohesive team.
When employees have a better understanding of each other’s roles and responsibilities, they can work together more effectively and communicate better.
This collaborative environment can enhance workflow and streamline processes.
Overall, investing in cross-training employees is a strategic approach to improving efficiency as a material handler.
By developing a versatile and capable workforce, you can adapt to changing demands, maintain productivity, foster employee engagement, and promote teamwork within your organization.
Transform Your Career Today
Unlock a personalized career strategy that drives real results. Get tailored advice and a roadmap designed just for you.
Start NowImplement Just-In-Time (JIT) Inventory
Reduce excess inventory by implementing a just-in-time system that delivers materials as needed
Implementing a Just-In-Time (JIT) inventory system can greatly improve efficiency as a material handler.
This method focuses on reducing excess inventory levels by only ordering materials when they are needed for production.
By implementing JIT inventory, material handlers can streamline their processes and minimize waste.
One of the key benefits of JIT inventory is the reduction of excess inventory.
Instead of stocking up on materials that may not be needed immediately, JIT ensures that materials are delivered just in time for production, eliminating the need for storing large quantities of inventory.
This reduces storage costs and frees up valuable space in the warehouse.
Minimize storage costs and reduce the risk of obsolete inventory by ordering materials only when necessary
Furthermore, JIT inventory helps to reduce the risk of obsolete inventory.
With traditional inventory management systems, there is always a possibility of materials becoming outdated or no longer needed due to changes in production processes.
By ordering materials only when necessary, material handlers can avoid the risk of having obsolete inventory sitting in the warehouse.
Implementing JIT inventory requires close coordination with suppliers to ensure that materials are delivered on time.
Material handlers need to have a robust communication system in place to convey their production needs accurately to suppliers.
This partnership is crucial in ensuring that materials are available just in time for production.
Moreover, JIT inventory can help improve cash flow for the organization.
By reducing excess inventory levels, capital is not tied up in surplus materials, allowing for more investment in other areas of the business.
This can lead to improved financial performance and overall efficiency in operations.
All in all, implementing a JIT inventory system can bring numerous benefits to material handlers.
By reducing excess inventory, minimizing storage costs, and avoiding obsolete inventory, material handlers can streamline their processes and operate more efficiently.
It is essential for material handlers to consider implementing JIT inventory as a way to enhance their operations and stay competitive in today’s fast-paced business environment.
Set Performance Metrics
As a material handler, setting performance metrics is crucial for improving efficiency in your daily operations.
By establishing key performance indicators (KPIs), you can track your progress, identify areas of improvement, and drive productivity.
Transform Your Career Today
Unlock a personalized career strategy that drives real results. Get tailored advice and a roadmap designed just for you.
Start NowHere are some tips on how to effectively set performance metrics to enhance your efficiency as a material handler:
Define Key Performance Indicators (KPIs)
Identify specific metrics that are directly related to the efficiency and productivity of your material handling tasks.
This could include metrics such as order fulfillment time, inventory accuracy, or on-time delivery performance.
By defining KPIs that are relevant to your role, you can measure your performance accurately.
Align Metrics with Organizational Goals
Ensure that the KPIs you set align with the overall goals of your organization.
Consider how your performance impacts the broader objectives of the company and choose metrics that reflect these goals.
This will help you focus on areas that are most critical to the success of the business.
Regularly Review and Analyze Metrics
Consistently monitor your performance metrics to track your progress and identify trends over time.
Regular reviews will allow you to spot any deviations from the desired outcomes and take corrective action promptly.
Analyzing your metrics will also help you understand the factors that contribute to efficiency or inefficiency in your operations.
Identify Areas for Improvement
Use your performance metrics to identify areas where you can make improvements in your material handling processes.
Look for patterns or trends that indicate bottlenecks or inefficiencies and brainstorm potential solutions.
By pinpointing areas for improvement, you can focus your efforts on making meaningful changes that enhance your efficiency.
Set Goals for Progress
Based on your performance metrics and areas for improvement, set clear goals for progress.
Establish specific, measurable targets that you aim to achieve within a defined timeframe.
Setting goals will not only motivate you to improve but also provide a roadmap for your ongoing development as a material handler.
In a nutshell, setting performance metrics is a fundamental step in improving efficiency as a material handler.
By establishing KPIs, aligning them with organizational goals, regularly reviewing and analyzing metrics, identifying areas for improvement, and setting goals for progress, you can enhance your performance and contribute to the overall success of your organization.
Embrace the power of performance metrics to drive continuous improvement in your material handling role.
Seek Feedback
Encourage open communication with employees to gather feedback on current processes
Gathering feedback from your employees is a crucial step in improving efficiency as a material handler.
Transform Your Career Today
Unlock a personalized career strategy that drives real results. Get tailored advice and a roadmap designed just for you.
Start NowYour team members are on the front lines of the operation, and they often have valuable insights into how processes can be optimized.
By fostering a culture of open communication and actively seeking feedback, you can make informed decisions to enhance efficiency in your daily tasks.
Use employee suggestions to make continuous improvements and foster a culture of efficiency in the workplace
One of the best ways to gather feedback is to hold regular meetings with your team where they can openly express their thoughts and suggestions.
Encourage them to share their experiences, challenges, and ideas for improvement.
By creating a safe space for communication, you can gain valuable insights into areas that need adjustment.
In addition to team meetings, you can also implement anonymous suggestion boxes or digital platforms where employees can submit their feedback confidentially.
This allows team members to share their thoughts without fear of reprisal, resulting in more honest and constructive feedback.
Make sure to review these suggestions regularly and act on actionable feedback promptly.
When receiving feedback, it’s essential to approach it with an open mind and a willingness to make changes.
Even if the suggestions challenge your current processes or require additional resources, consider their potential impact on efficiency in the long run.
By demonstrating that you value your employees’ input and are committed to making improvements, you can foster a culture of continuous improvement in the workplace.
Employee feedback can lead to innovative solutions and process improvements that you may not have considered on your own.
By leveraging the diverse perspectives and experiences within your team, you can identify inefficiencies and implement targeted solutions to streamline operations.
Moreover, involving employees in the decision-making process can increase their engagement and motivation, resulting in a more efficient and productive workforce.
Essentially, seeking feedback from your employees is a powerful tool for improving efficiency as a material handler.
By encouraging open communication, listening to their suggestions, and acting on feedback, you can drive continuous improvements and cultivate a culture of efficiency in the workplace.
Remember, your team members are valuable resources who can help you optimize processes and achieve operational excellence.
Conclusion
Efficiency as a material handler is crucial for warehouse operations. One key point is optimizing workflows.
Implementing technology like inventory management systems can streamline tasks and reduce errors.
Training and cross-training employees enhance overall efficiency and productivity in handling materials.
Transform Your Career Today
Unlock a personalized career strategy that drives real results. Get tailored advice and a roadmap designed just for you.
Start NowRegularly evaluating processes and seeking feedback will help identify areas for improvement.
In the end, improving efficiency as a material handler involves optimizing workflows, utilizing technology, and training employees.
Continuous efforts to enhance efficiency are essential for success in warehouse operations.