Introduction
Getting your fashion designs manufactured is a crucial step in transforming your creative ideas into tangible products.
This process involves finding the right manufacturer who can bring your designs to life with precision and quality.
Selecting a manufacturer requires careful consideration of their capabilities, reputation, and alignment with your design vision.
A reliable manufacturer ensures that your designs are produced accurately and to a high standard, impacting the overall success of your collection.
Choosing the right manufacturer also helps avoid costly mistakes and delays.
It guarantees that your designs will meet industry standards and customer expectations.
Moreover, a good manufacturer can assist in optimizing your production process, improving efficiency, and reducing waste.
The benefits of having your designs manufactured include increased market reach and professional presentation.
Quality production enhances your brand’s reputation and attracts potential buyers.
Effective manufacturing turns your creative concepts into successful, sellable products.
It establishes your presence in the fashion industry and drives business growth.
Researching potential manufacturers
The Importance of Thorough Research
Researching potential manufacturers is a critical step in turning your fashion designs into reality.
Thorough research ensures that you choose a manufacturer who meets your needs.
A well-chosen manufacturer can help you achieve high-quality production and align with your brand values.
Where to Look for Manufacturers
Start by attending trade shows.
Fashion industry trade shows are excellent for meeting manufacturers in person.
These events provide a platform to see samples and discuss capabilities.
You can gather valuable information on production processes and establish direct contacts with potential partners.
Online directories also offer a wealth of information.
Websites like Maker’s Row and ThomasNet list numerous manufacturers, each with detailed profiles.
You can filter by location, specialization, and production capacity to find suitable candidates.
Explore these directories to compare different manufacturers and find those that align with your needs.
Referrals from industry peers can also be incredibly useful.
Reach out to other designers and brands for recommendations.
Their firsthand experiences can provide insights into the reliability and quality of manufacturers they have worked with.
Personal referrals often lead to discovering trustworthy partners who may not be widely advertised.
Aligning with Brand Values and Budget
When researching manufacturers, assess their alignment with your brand values.
Choose a manufacturer who understands and supports your design philosophy.
This alignment ensures that your vision and quality standards are maintained throughout production.
A manufacturer who shares your commitment to sustainability or ethical practices can enhance your brand’s credibility and appeal.
Budget considerations are also crucial.
Evaluate manufacturers based on their cost structures and payment terms.
Request detailed quotes and compare them to ensure they fit within your financial plans.
Remember, the cheapest option may not always be the best in terms of quality.
Balance cost with the value offered to ensure you get a good return on your investment.
Production Capabilities and Quality Control
Additionally, consider the manufacturer’s production capabilities and capacity.
Ensure they can handle your order volume and meet your deadlines.
A manufacturer’s ability to scale up or down as needed is important for managing your production needs effectively.
Verify their track record with similar projects to ensure they can deliver on their promises.
Finally, review the manufacturer’s quality control processes.
High standards in quality control prevent costly mistakes and defects.
Ask about their inspection procedures and request samples before committing to a large order.
This step helps confirm that their production aligns with your quality expectations.
Thorough research into potential manufacturers helps ensure you partner with the right one.
Choosing a manufacturer who aligns with your brand values and budget is essential for successful production.
This careful selection process sets the foundation for turning your fashion designs into successful, market-ready products.
Read: Top Skills Needed for Art Educators and Instructors
Communicating your design specifications
The Importance of Clear Communication
Clear communication with manufacturers is essential for successful production and ensuring that your fashion designs are realized as intended.
Misunderstandings or ambiguity in instructions can lead to production errors, delays, and increased costs.
Effective communication helps prevent these issues by ensuring that your design vision is accurately translated into the final product.
It also fosters a strong working relationship with your manufacturer, making it easier to address any concerns that arise during the production process.
Being precise and thorough in your instructions minimizes the risk of mistakes and ensures that the finished product meets your quality standards.
Key Components to Include in Design Specifications
When preparing design specifications, include detailed information about the materials you want to use.
Specify the types of fabrics, trims, and finishes required for your design.
For example, if you want a specific type of fabric like silk or denim, state this clearly.
Include information on texture, weight, and any special properties the material should have.
Accurate material descriptions are crucial for ensuring that the final product meets your expectations and maintains the quality you desire.
Measurements are another critical component of your design specifications.
Provide precise dimensions for each part of your design, including garment lengths, widths, and sizes.
Clearly define fit requirements, such as whether the design should be tailored or loose-fitting.
Accurate measurements help avoid sizing discrepancies and ensure that the final product fits as intended, which is crucial for customer satisfaction.
Color specifications are also vital.
Clearly state the colors you want for your design, using color codes, swatches, or Pantone numbers.
Providing this level of detail helps avoid confusion and ensures that the colors in the final product match your design vision.
Consistency in color across production runs is important for maintaining brand identity and customer expectations.
Providing Detailed Sketches, Tech Packs, or Samples
Detailed sketches or technical drawings are essential for conveying your design intent to manufacturers.
These visual aids should illustrate all aspects of your design, including construction details, design features, and any special instructions.
Annotations on sketches can clarify complex elements and provide additional guidance.
A comprehensive tech pack is another crucial tool in communicating your design specifications.
A tech pack should include all relevant details, such as material descriptions, measurements, color information, and construction methods.
It serves as a reference document for manufacturers, ensuring they have all the necessary information to produce your design accurately.
Providing physical samples of materials or prototypes, if possible, can further enhance clarity.
Samples offer a tangible reference for manufacturers, helping them understand the texture, weight, and quality of materials you envision.
This step is particularly useful for ensuring that the manufacturer can replicate the desired look and feel of your design.
Effective communication of your design specifications is essential for translating your vision into high-quality products.
Include detailed information on materials, measurements, and colors to prevent misunderstandings and ensure accuracy.
Providing sketches, tech packs, or samples helps manufacturers align with your design intent and deliver results that meet your expectations.
Clear and comprehensive communication is the key to successful manufacturing and achieving the best possible outcome for your fashion designs.
Read: Collaborating with Other Creative Roles
Getting cost estimates and negotiating terms
Requesting Cost Estimates
Requesting cost estimates from manufacturers is a vital step in the production process.
Begin by clearly outlining your design specifications and requirements.
Provide detailed information on materials, sizes, and quantities to get accurate quotes.
Include your desired production timeline and any special requests to ensure manufacturers understand your needs.
Send your request to multiple manufacturers to gather a range of estimates.
This allows you to compare costs and services.
Request a detailed breakdown of the costs, including material, labor, and any additional fees.
Understanding these components helps you assess the overall value of the quote.
Negotiating Key Terms
Negotiating terms is crucial to establishing a favorable working relationship with your manufacturer.
Start with minimum order quantities (MOQs).
Discuss your production needs and negotiate MOQs that align with your budget and sales projections.
Manufacturers may be willing to adjust MOQs based on your long-term potential and order consistency.
Payment terms are another important aspect to negotiate.
Discuss options such as deposits, payment schedules, and net terms.
Ensure the payment terms are manageable for your cash flow and align with your financial planning.
Consider negotiating favorable terms to balance your financial risk and manage your budget effectively.
Lead times also play a critical role in production planning.
Discuss and agree upon lead times for both production and delivery.
Understanding the manufacturer’s timeline helps you plan your product launches and inventory management.
Negotiate shorter lead times if necessary, but be mindful of the impact on cost and quality.
Ensuring Fair Pricing
To ensure you are getting a fair price, compare the estimates and terms from different manufacturers.
Look beyond the base price and evaluate the overall value offered.
Consider factors such as quality, production capabilities, and additional services included in the quote.
A higher price may be justified if it includes superior quality or faster delivery.
Conduct market research to understand industry pricing standards.
This knowledge helps you assess whether the estimates you receive are competitive.
Additionally, check for hidden costs or fees that might not be immediately apparent in the initial quote.
Build a transparent relationship with your manufacturer.
Discuss your budget constraints openly and seek their advice on cost-effective solutions.
A collaborative approach often leads to better negotiation outcomes and fosters a positive working relationship.
Getting cost estimates and negotiating terms are critical steps in securing a successful manufacturing partnership.
Clearly request detailed estimates, negotiate key terms such as MOQs, payment terms, and lead times, and ensure fair pricing through comparison and market research.
By following these guidelines, you can establish a solid foundation for manufacturing your fashion designs effectively and within your budget.
Read: Historic Costume Design Inspirations
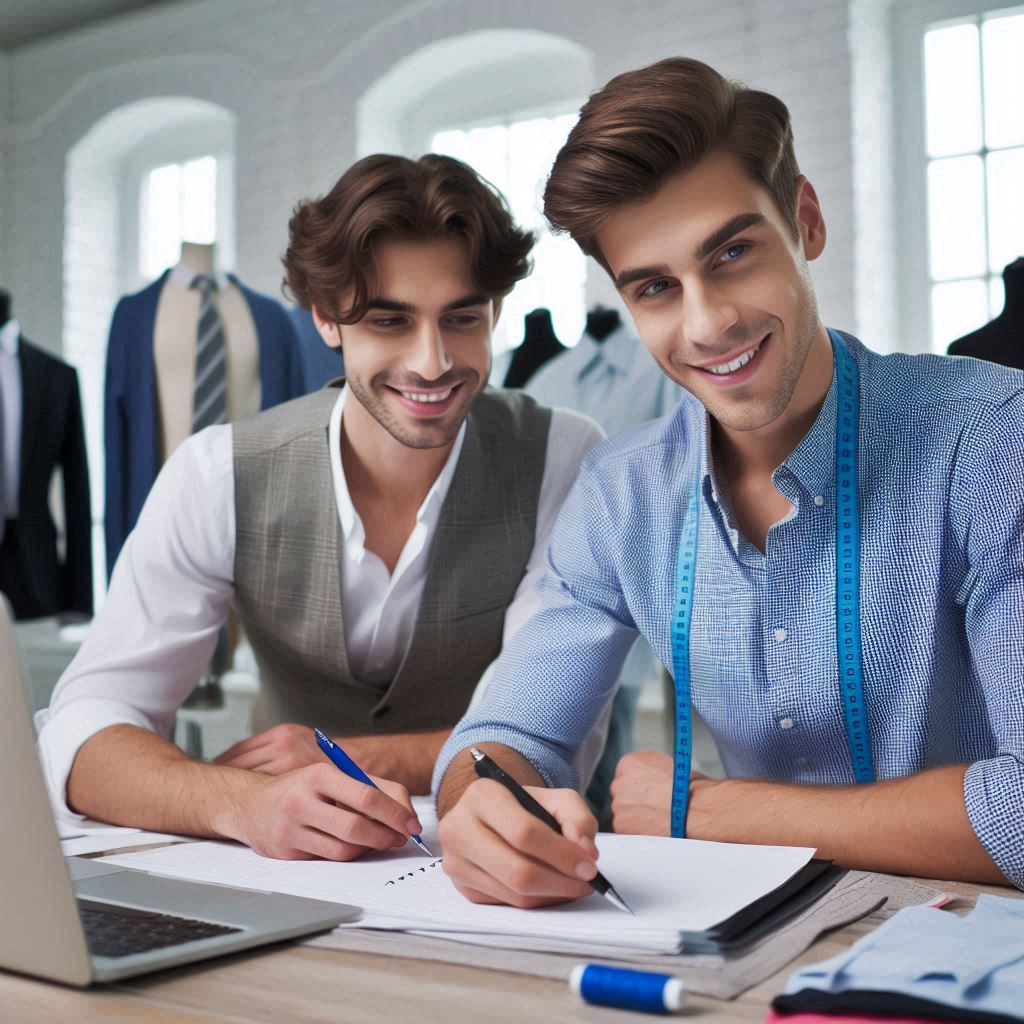
Inspecting samples and prototypes
The Importance of Inspecting Samples and Prototypes
Inspecting samples and prototypes before production begins is crucial.
This step ensures that the final product aligns with your vision and quality standards.
By evaluating samples early, you can identify potential issues and make necessary adjustments before committing to a full production run.
This proactive approach helps prevent costly mistakes and ensures the final product meets your expectations.
Evaluating the Quality of Samples
To evaluate the quality of samples, start by examining the material and craftsmanship.
Check the fabric’s texture, weight, and durability to ensure it matches your design specifications.
Inspect stitching, seams, and finishes for consistency and quality.
Look for any defects or irregularities that could affect the final product’s appearance or functionality.
Assess the sample’s fit and overall construction to determine if it meets your design requirements.
Provide detailed feedback to the manufacturer based on your evaluation.
Communicate any necessary adjustments clearly and ensure they understand your quality expectations.
Request revised samples if needed to confirm that changes have been implemented correctly.
This iterative process helps refine the product and ensures it aligns with your design vision.
Transform Your Career Today
Unlock a personalized career strategy that drives real results. Get tailored advice and a roadmap designed just for you.
Start NowEnsuring the Final Product Matches Your Vision
Ensuring the final product matches your vision is essential for maintaining your design integrity.
Compare the approved samples to your original design concept to verify accuracy.
Check if the colors, patterns, and details align with your initial sketches and specifications.
Evaluate how well the sample reflects your brand’s style and identity.
Address any discrepancies between the sample and your vision promptly.
Work closely with the manufacturer to resolve any issues and make necessary adjustments.
This collaborative approach helps ensure that the final product is true to your design and meets your quality standards.
Inspecting samples and prototypes before production is a critical step in fashion design.
It allows you to assess quality, make necessary adjustments, and ensure that the final product aligns with your vision.
By thoroughly evaluating samples and collaborating with your manufacturer, you can achieve a high-quality end product that accurately reflects your design intentions.
Read: Breaking Down Iconic Movie Costumes
Managing production timelines and quality control
Advice on how to effectively manage production timelines with manufacturers
When working with manufacturers, it is crucial to set clear timelines for production to ensure timely delivery of your fashion designs.
Communicate your expectations clearly to the manufacturer.
Confirm they can meet your deadlines before starting the production process.
Here are some tips on how to manage production timelines effectively:
Establish a detailed timeline
Create a timeline that outlines key milestones in the production process, including design approval, fabric sourcing, sample development, and final production.
Share this timeline with your manufacturer to ensure that everyone is on the same page.
Communicate regularly
Stay in touch with your manufacturer throughout the production process to track progress and address any delays or issues that may arise.
Regular communication can help you stay on top of the timeline and make adjustments as needed.
Build buffer time
Allow for extra time in your production timeline to account for unexpected delays or challenges.
Building buffer time into your schedule can help you avoid major setbacks and ensure that your fashion designs are delivered on time.
Importance of setting clear expectations for quality control during production
Quality control is essential in the manufacturing process to ensure that your fashion designs meet your standards and brand reputation.
By setting clear expectations for quality control with your manufacturer, you can minimize the risk of defects or errors in your products.
Here are some key factors to consider when setting expectations for quality control:
Define quality standards
Clearly outline your quality standards and expectations for the finished product, including materials, construction, and finish.
Provide samples or visual references to help your manufacturer understand your vision and requirements.
Conduct inspections
Implement a quality control process that includes regular inspections of samples and production runs to identify any issues or defects early on.
Communicate feedback to your manufacturer and work together to address any quality concerns.
Establish communication channels
Ensure that you have open lines of communication with your manufacturer for discussing quality control issues and making necessary improvements.
Regular feedback and collaboration can help you maintain high-quality standards in your fashion designs.
Tips on how to address any issues that may arise during the manufacturing process
Despite careful planning and communication, issues may still arise during the manufacturing process.
It is important to be prepared to address these challenges effectively to ensure that your fashion designs are produced to your satisfaction.
Here are some tips on how to handle issues that may arise during manufacturing:
Identify the root cause
Take the time to investigate the issue and determine the underlying cause before taking any corrective actions.
Understanding the root cause can help you prevent similar issues in the future.
Collaborate with your manufacturer
Work closely with your manufacturer to address the issue and come up with a solution together.
Open communication and cooperation can lead to more efficient problem-solving and improve the outcome of your fashion designs.
Consider alternative solutions
Be flexible and explore various solutions to resolve the issue.
Adjust production processes, source new materials, or modify designs.
Stay proactive in finding solutions that align with your vision and quality standards.
Shipping and receiving your manufactured designs
When it comes to getting your fashion designs manufactured, one crucial aspect to consider is shipping and receiving the finished products.
This process can make or break your business, so it’s essential to handle it with care and attention to detail.
Transform Your Career Today
Unlock a personalized career strategy that drives real results. Get tailored advice and a roadmap designed just for you.
Start NowGuide on how to arrange shipping for your manufactured designs
Once your designs are manufactured, the next step is to arrange for them to be shipped to your location or distribution center.
The first thing you need to do is find a reliable shipping company that specializes in transporting fashion items.
It’s important to provide the shipping company with accurate information about the size and weight of your packages to ensure they are properly handled during transit.
You should also inquire about insurance options to protect your goods in case of any mishaps.
Ensure that you have all the necessary documentation and labels ready for the shipment, including customs forms if shipping internationally.
Double-checking everything before sending out your products will help prevent delays or issues during transit.
Importance of tracking shipments and ensuring they arrive on time
Tracking your shipments is crucial to know the exact location of your products and ensure they are delivered on time.
Many shipping companies offer online tracking services that allow you to monitor the progress of your packages in real-time.
By tracking your shipments, you can also anticipate any potential delays and take immediate action to resolve them.
This proactive approach can help you maintain a good relationship with your customers and avoid any negative feedback due to late deliveries.
Timely delivery is essential in the fashion industry, where trends change rapidly, and customers expect quick turnaround times.
Ensuring that your products arrive on schedule will enhance your brand reputation and increase customer satisfaction.
Significance of inspecting the final product upon delivery and addressing any issues promptly
When you receive your manufactured designs, it is crucial to inspect them thoroughly to ensure they meet your quality standards.
Check for any defects, damages, or discrepancies in color, size, or design that may have occurred during shipping.
If you identify any issues with the final product, address them promptly by contacting the manufacturer or shipping company for a resolution.
It’s essential to act quickly to prevent any further damage or inconvenience to your business and customers.
Addressing issues promptly shows your commitment to quality and customer satisfaction.
This approach builds trust and loyalty with your target audience.
It also shows that you take your business seriously and are willing to go the extra mile to rectify any problems that may arise.
Overall, shipping and receiving your manufactured designs require careful planning, organization, and attention to detail.
Follow these guidelines to improve your fashion business’s efficiency.
Track shipments closely and ensure timely delivery.
Inspect products upon arrival to maintain quality.
By actively managing these steps, you streamline the process and set your business up for success.
Conclusion
Provide manufacturers with precise measurements, materials, and construction details for your designs.
Look for manufacturers with experience in your type of clothing and a reputation for quality.
Order samples from potential manufacturers to assess the quality of their workmanship.
Discuss pricing, minimum order quantities, and production timelines with the manufacturer.
Outline all terms and conditions in a written agreement before starting production.
Choosing the right manufacturer is crucial for ensuring the quality and consistency of your fashion designs.
A reputable manufacturer can bring your vision to life and help you establish a strong brand reputation.
By partnering with a trusted manufacturer, you can streamline the production process and deliver high-quality garments to your customers.
If you’re ready to bring your fashion designs to life, now is the time to start the manufacturing process.
By following these key steps and finding the right manufacturer, you can turn your creative vision into a successful fashion business.
Take the first step today and begin the exciting journey of manufacturing your unique designs.
[E-Books for Sale]
The Big Book of 500 High-Paying Jobs in America: Unlock Your Earning Potential
$19.99 • 500 High-Paying Jobs • 330 pages
Explore 500 high-paying jobs in America and learn how to boost your career, earn more, and achieve success!
See All 500 High-Paying Jobs of this E-Book
1001 Professions Without a Degree: High-Paying American Jobs You Can Start Now
$19.99 • 1001 Professions Without a Degree • 174 pages
Discover 1001 high-paying jobs without a degree! Unlock career tips, skills, and success strategies for just $19.99!