Introduction
Furniture design plays a vital role in defining the aesthetic and functionality of any interior space.
Well-designed furniture enhances both the look and the usability of a room.
It seamlessly blends form and function, creating an environment that is not only visually pleasing but also practical.
In today‘s world, furniture design is more than just selecting pieces that match a space.
Designers carefully consider aspects such as ergonomics, sustainability, and user needs to create furniture that serves multiple purposes.
The right furniture can transform an ordinary room into a stylish, efficient space tailored to its occupants.
The furniture design process is a structured journey that begins with understanding the client‘s needs.
It involves more than just creativity; it requires thoughtful planning, research, and technical skills.
Each step in the process contributes to the final product, ensuring that the design not only looks good but also functions well in its intended space.
From concept development to material selection, every decision impacts the overall success of the design.
Research and Inspiration
The furniture design process begins with research and inspiration.
This phase sets the foundation for creativity and innovation.
Designers gather ideas from diverse sources.
Nature offers organic shapes and colors.
Observing natural elements can spark unique design concepts.
Collecting Inspiration from Various Sources
Architecture also provides valuable inspiration.
Architectural styles inform furniture design through form and function.
Designers analyze buildings and spaces to understand proportions.
They explore how furniture can enhance both aesthetics and usability.
Elements like lines, textures, and materials found in architecture can influence design decisions.
Other design styles are essential sources of inspiration.
Designers study furniture styles from various eras, such as mid-century modern or Art Deco.
Each style has distinct characteristics and aesthetics.
By understanding these elements, designers can create pieces that resonate with different audiences.
Blending styles can lead to innovative results, merging classic elegance with contemporary flair.
Researching Current Trends and Consumer Preferences
Researching current trends is crucial in the furniture industry.
Designers keep an eye on market shifts and consumer preferences.
They examine popular materials, colors, and functionalities.
Staying updated helps designers create relevant and appealing products.
Industry reports, trend forecasts, and design publications serve as essential resources.
Social media platforms also play a significant role.
Designers follow influencers and brands to observe emerging trends.
Instagram and Pinterest showcase vibrant design communities.
These platforms provide immediate access to fresh ideas and innovative designs.
Designers can engage with followers to understand their preferences.
Conducting surveys and interviews offers direct insights.
Designers can learn about consumer needs and desires.
Understanding what customers want helps create functional and desirable furniture.
This knowledge shapes the design process, ensuring relevance in a competitive market.
Designers also explore sustainable practices during research.
Eco-friendly materials and production methods are increasingly popular.
Incorporating sustainability attracts environmentally conscious consumers.
Researching eco-friendly alternatives can lead to innovative designs that prioritize both style and responsibility.
Gathering inspiration involves documenting ideas visually.
Designers create mood boards to organize their thoughts.
These boards compile images, materials, and color palettes.
They serve as visual guides throughout the design process.
Designers can refer back to these boards for clarity and direction.
Ultimately, research and inspiration fuel creativity in furniture design.
They inform decision-making and help establish a clear vision.
By tapping into various sources, designers cultivate a rich palette of ideas.
This groundwork enhances the entire design process, leading to innovative and compelling furniture pieces that resonate with users.
Sketching and Concept Development
In the furniture design process, sketching and concept development play a vital role.
This phase transforms ideas and inspirations into tangible forms.
Designers start by brainstorming concepts based on research and inspirations gathered earlier.
These concepts often emerge from various sources, such as nature, architecture, or personal experiences.
Translating Ideas and Inspirations into Rough Sketches and Drawings
Once ideas surface, designers begin translating them into rough sketches.
These initial drawings capture the essence of each concept.
Designers use pencil and paper or digital tools to create these sketches.
At this stage, creativity flows freely without constraints.
The focus remains on visualizing concepts rather than perfecting details.
Sketches serve as a foundation for further development.
Designers select the most promising ideas to refine and expand.
They consider factors like functionality, aesthetics, and user experience.
Each sketch evolves as designers experiment with different shapes, materials, and configurations.
This iterative process encourages exploration and innovation.
Refining Initial Concepts Based on Feedback and Feasibility
Feedback from peers, mentors, or clients is crucial during this phase.
Designers present their sketches for critique, gaining fresh perspectives.
Constructive criticism helps identify strengths and weaknesses in the concepts.
This feedback shapes the direction of further development, guiding designers toward better solutions.
After gathering feedback, designers refine their sketches.
They focus on enhancing details while maintaining the original vision.
This step involves rethinking proportions, lines, and features to improve usability and appeal.
Designers also assess the feasibility of each concept during this phase.
Practical considerations, such as materials, production techniques, and cost, influence the design choices.
As sketches evolve, designers create more detailed drawings.
These refined sketches illustrate how the furniture will function in real life.
Designers incorporate dimensions and specifications, ensuring the design is practical.
This detailed approach allows for clearer communication with stakeholders, including manufacturers and clients.
Additionally, designers may create mood boards alongside their sketches.
Mood boards showcase colors, textures, and materials that complement the design.
This visual representation enriches the concept, offering a holistic view of the furniture piece.
It serves as a reference point throughout the design process.
Ultimately, sketching and concept development set the stage for successful furniture design.
This phase encourages creativity, collaboration, and critical thinking.
By translating ideas into visual forms, designers lay a solid foundation for the next steps.
With careful refinement and feedback integration, they enhance their concepts, ensuring they resonate with users and fulfill practical needs.
In general, effective sketching and concept development fuel the furniture design process.
This crucial phase transforms abstract ideas into concrete designs that inspire and innovate.
Read: Top Skills Needed for Art Educators and Instructors
Material Selection
Choosing the right materials is crucial in the furniture design process.
This decision significantly impacts the final product’s aesthetics, functionality, and longevity.
Start by identifying materials that align with your design concept.
Consider how these materials contribute to the overall vision.
Identifying the Appropriate Materials That Align with the Design Concept and Intended Function of the Furniture Piece
Think about the intended function of the furniture piece.
Different functions require different material properties.
For example, a dining table needs durability to withstand daily use.
In contrast, a decorative piece may prioritize aesthetics over durability.
Durability is one of the most critical factors to consider.
High-quality materials ensure the furniture lasts for years.
Look for woods like oak or maple, known for their strength.
Metals like stainless steel offer durability and modern appeal.
Even synthetic materials can provide longevity if chosen wisely.
Considering Factors Such as Durability, Sustainability, and Cost
Sustainability is increasingly important in today‘s design landscape.
Many consumers prefer eco-friendly materials that minimize environmental impact.
Research renewable options like bamboo or reclaimed wood.
These materials often add unique character to designs while supporting sustainability.
Next, evaluate the cost of your selected materials.
Balancing quality and affordability is essential for a successful project.
High-end materials may offer superior aesthetics but can strain your budget.
Always calculate the overall cost of the project, including materials and labor.
Don‘t forget about sourcing materials.
Identify reliable suppliers that offer quality options within your budget.
Building relationships with these suppliers can lead to better pricing and unique material access.
When selecting materials, also think about their textures and colors.
The right texture can enhance the tactile experience of the furniture.
Similarly, color plays a vital role in the design‘s emotional impact.
Choose materials that complement your overall color scheme and design concept.
Consider the maintenance requirements of your selected materials.
Some materials may need regular upkeep, while others are more forgiving.
For example, leather offers luxury but requires care to maintain its appearance.
In contrast, metal finishes might need occasional polishing but can be easier to clean.
Finally, test your material choices with prototypes.
Create small samples to see how they work together.
This practice helps visualize the final piece and identify any potential issues.
Gathering feedback on prototypes can guide your final material selection.
Material selection is a pivotal step in the furniture design process.
By thoughtfully considering durability, sustainability, and cost, you can enhance your design’s success.
Make informed decisions that reflect your design vision and meet client expectations
Read: Collaborating with Other Creative Roles
Prototyping and Testing
Prototyping and testing form a crucial step in the furniture design process.
Designers create a physical prototype to evaluate their concepts.
This prototype serves as a tangible representation of the final product.
It allows designers to assess structural integrity and overall usability.
Creating a physical prototype of the furniture design to test its structural integrity and usability
Creating a prototype involves various materials.
Designers often choose wood, metal, or plastics based on the final design.
Each material presents unique properties and challenges.
A well-constructed prototype can reveal strengths and weaknesses early in the process.
After completing the prototype, designers must conduct thorough testing.
This testing examines the durability and stability of the piece.
Designers push, pull, and apply weight to assess how it holds up.
They pay attention to joints and connections to ensure they withstand stress.
Gathering Feedback from Potential Users and Making Necessary Adjustments
Usability testing is equally important.
Designers invite potential users to interact with the prototype.
They observe how users engage with the piece.
This feedback provides valuable insights into the design’s functionality.
Are the dimensions comfortable? Is the height appropriate for various tasks?
Gathering user feedback often highlights unforeseen issues.
Users may identify discomfort or difficulty that the designer overlooked.
These insights are vital for refining the design.
Designers should document all feedback meticulously for later reference.
Once designers analyze the feedback, they can make necessary adjustments.
Small changes can significantly improve the overall experience.
For example, adjusting the height or modifying the shape can enhance comfort.
Sometimes, a complete redesign is necessary based on user input.
Prototyping also allows designers to explore aesthetics.
Color, finish, and texture can be tested on the prototype.
This exploration helps in visualizing the final product more clearly.
It allows designers to see how different elements work together.
Testing the prototype also provides an opportunity for team collaboration.
Designers can involve engineers, marketers, and manufacturers in this phase.
Their perspectives can contribute to a more robust design.
Incorporating diverse feedback during this stage fosters innovation.
It leads to solutions that a designer might not have considered alone.
This collaborative effort ensures the final product resonates with its target audience.
Ultimately, prototyping and testing are about refinement.
They transform initial ideas into functional, appealing furniture.
This step is essential for achieving a successful design.
By prioritizing user feedback and iterative adjustments, designers create products that truly meet user needs.
Read: Historic Costume Design Inspirations
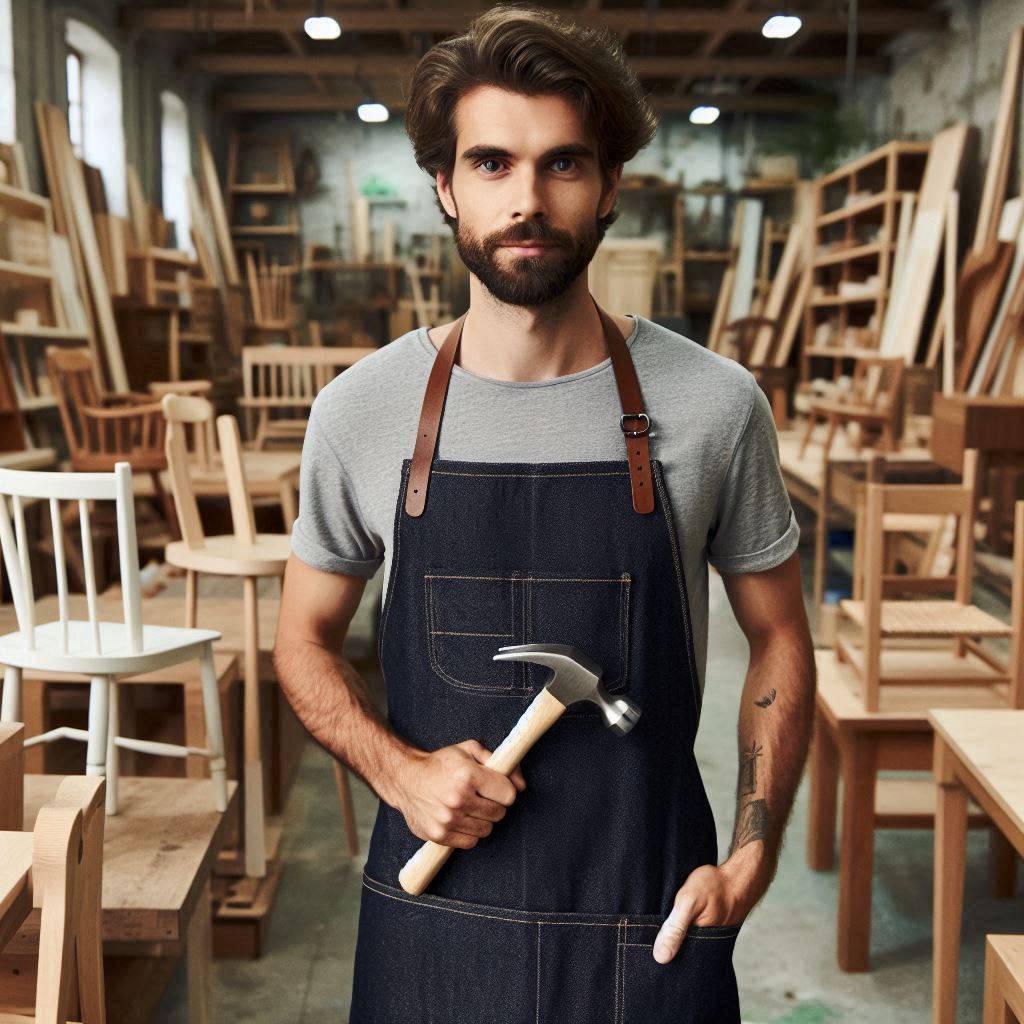
Technical Drawings and Specifications
Creating technical drawings and specifications is a crucial step in the furniture design process.
These documents serve as blueprints for production, ensuring that every detail is clear.
Designers translate their concepts into precise drawings that communicate ideas effectively.
Developing Detailed Technical Drawings and Specifications for Production
Start with accurate measurements.
Use measuring tools to gather dimensions for each component.
This ensures that everything fits together seamlessly.
Dimensions should include height, width, and depth.
Consider any additional details that affect the overall design, like leg height or drawer depth.
Next, select materials carefully.
Clearly indicate the type of wood, metal, or fabric you plan to use.
Specify the grade and quality to ensure durability and aesthetic appeal.
Mention any unique material properties that might affect production or usability.
Including Dimensions, Materials, Finishes, and Assembly Instructions
Finishes also play a significant role in the final product.
Specify paint colors, stains, or varnishes that will enhance the design.
Provide details on the application process to achieve the desired look.
Include information about drying times and environmental considerations.
These details help ensure consistency in the final appearance.
Assembly instructions are vital for manufacturers.
Clearly outline how each piece fits together.
Include diagrams or images to illustrate the assembly process.
Use numbered steps for clarity, guiding the assembler through each stage.
Make sure to highlight any specific tools required for assembly.
Additionally, include any special instructions that might be necessary.
For example, if a particular technique or adhesive is essential, specify that in the documentation.
Clear instructions minimize errors and ensure a smooth production process.
Quality assurance is another critical aspect.
Mention any testing procedures required to maintain design integrity.
Specify tolerances for manufacturing, so each piece meets your standards.
This helps avoid issues during production and ensures a high-quality final product.
Finally, review all drawings and specifications thoroughly.
Verify that all dimensions, materials, and finishes are accurately represented.
Collaborate with production teams to ensure everyone understands the design intent.
This collaboration fosters communication and reduces the likelihood of misunderstandings.
In addition, detailed technical drawings and specifications form the backbone of successful furniture design.
They communicate vital information to manufacturers and ensure that your vision becomes a reality.
By focusing on dimensions, materials, finishes, and assembly instructions, you lay the groundwork for a smooth production process.
This attention to detail ultimately leads to a high-quality, functional, and aesthetically pleasing piece of furniture.
Transform Your Career Today
Unlock a personalized career strategy that drives real results. Get tailored advice and a roadmap designed just for you.
Start NowRead: Breaking Down Iconic Movie Costumes
Production Planning
Production planning is a crucial step in the furniture design process.
It transforms concepts into tangible products.
Collaborating effectively with manufacturers or in-house production teams is essential.
This collaboration ensures everyone is aligned on timelines and budgets.
Collaborating with Manufacturers or In-House Production Teams to Establish a Production Timeline and Budget
First, establish a clear production timeline.
Begin by outlining key milestones.
Identify phases such as material sourcing, prototyping, and final production.
Each phase requires careful planning.
Make sure to allocate enough time for each step.
A well-structured timeline keeps the project on track.
Next, discuss the budget with your production team.
Determine the costs associated with materials, labor, and overhead.
Keep in mind that unexpected expenses may arise.
Set aside a contingency fund to address these issues.
A transparent budget fosters trust between designers and manufacturers.
Sourcing Materials and Coordinating Production Processes
Sourcing materials is another critical component of production planning.
Research various suppliers to find quality materials.
Consider sustainability and cost-effectiveness when making selections.
Create a list of preferred suppliers and evaluate their offerings.
Request samples to ensure materials meet design specifications.
Coordinate closely with your suppliers during this phase.
Confirm availability and lead times for materials.
Discuss any potential delays that may impact the timeline.
Good communication prevents misunderstandings and ensures a smooth production process.
Once materials are sourced, initiate production processes.
Work closely with your production team to set clear expectations.
Outline quality standards and production methods.
Establish a workflow that maximizes efficiency.
This collaboration helps prevent bottlenecks and maintains momentum.
Regularly monitor the production process.
Schedule check-ins with your team to review progress.
Address any issues as they arise to keep the project on schedule.
Open lines of communication are vital for a successful production phase.
In addition, gather feedback during production.
Engage with manufacturers to understand their challenges.
This feedback can provide insights into potential improvements.
Being receptive to suggestions enhances the overall quality of the final product.
As production nears completion, prepare for final inspections.
Ensure that the finished furniture meets design and quality standards.
Conduct thorough quality checks before shipping to clients.
This attention to detail reflects your commitment to excellence.
In summary, production planning is a vital step in furniture design.
Collaborating with manufacturers and sourcing materials effectively sets the stage for success.
Establishing timelines and budgets ensures a smooth transition from concept to creation.
Embrace this process to bring your design vision to life.
Discover More: Exploring the Art of Hand Lettering and Calligraphy
Quality Control and Finishing
Quality control and finishing are vital steps in the furniture design process.
These steps ensure the final product meets both aesthetic and functional standards.
After constructing the furniture, conduct a thorough inspection.
Check for any defects in materials and craftsmanship.
This inspection helps identify any issues that need correction.
Inspecting the Final Product for Quality Assurance and Compliance with Design Specifications
Start by examining the structure of the piece.
Look for any misalignments or weak joints.
Ensure all components fit together seamlessly.
Next, assess the surface quality.
Inspect for scratches, dents, or other imperfections.
A flawless surface enhances the overall appeal of the furniture.
Once you’ve completed the inspection, it’s time to apply finishes.
Finishing is crucial for both appearance and protection.
Choose finishes that complement the design and enhance durability.
Common finishes include paint, stain, and upholstery.
Each finish has unique properties and benefits.
Applying Finishes Such as Paint, Stain, or Upholstery to Enhance the Appearance and Durability of the Furniture Piece
When selecting a paint, consider the color and sheen.
A glossy finish can make a piece look modern and sleek.
Conversely, a matte finish may evoke a more rustic feel.
Test samples of your chosen paint to ensure the desired look.
Apply multiple coats if necessary to achieve a uniform finish.
Stains can highlight the natural beauty of wood.
They add depth and character while protecting the surface.
Choose a stain that aligns with your design vision.
Test different shades on scrap wood to see the final result.
Apply the stain evenly and allow it to dry fully before adding a protective coat.
Upholstery adds comfort and style to furniture.
Select fabrics that are durable and easy to clean.
Consider the texture, color, and pattern when making your choice.
High-quality upholstery enhances the value of your piece.
Always use proper techniques for cutting and attaching fabric.
After applying finishes, conduct a final inspection.
Check that all surfaces are even and free of defects.
Ensure the finishes are dry and cured according to the manufacturer‘s guidelines.
This step is essential for achieving a professional look.
Essentially, quality control and finishing are crucial for any furniture design.
A meticulous inspection ensures the product meets your standards.
Applying the right finishes enhances both the beauty and longevity of the piece.
By following these steps, you guarantee that your furniture will impress and endure.
This commitment to quality reflects your dedication to the craft.
Conclusion
The furniture design process thrives on collaboration and iteration.
Designers, craftsmen, and clients all play vital roles.
Open communication fosters innovation and creativity.
Each team member brings unique perspectives, enhancing the design.
Feedback loops are essential for refining concepts.
Designers should welcome input from all stakeholders.
This iterative approach leads to better solutions.
Attention to detail sets great designs apart.
Every element matters, from the choice of materials to the finishing touches.
Designers must consider functionality and aesthetics.
A well-crafted piece of furniture blends form and function seamlessly.
Small details can elevate a design from ordinary to extraordinary.
Precision in measurements ensures a perfect fit for intended spaces.
Craftsmanship is equally important in furniture design.
Skilled artisans transform ideas into tangible pieces.
Their expertise brings designs to life with quality and durability.
Investing time in craftsmanship yields lasting value.
Furniture should not only look beautiful but also withstand the test of time.
Every design decision should reflect a commitment to quality.
This commitment resonates with clients and consumers alike.
High-quality furniture becomes a centerpiece in any space.
It tells a story and enhances the environment.