Introduction
The field service technician industry plays a crucial role in maintaining and repairing equipment across various sectors.
Technicians ensure that machinery operates efficiently, minimizing downtime and improving productivity.
This industry spans multiple fields, including manufacturing, utilities, and IT services, each requiring specialized skills and tools.
Innovations in the field service industry have become increasingly important.
As technology advances, so do the methods and tools used by technicians.
Innovations improve efficiency, accuracy, and customer satisfaction.
They also help companies reduce costs and stay competitive in a rapidly evolving market.
New technologies have transformed how technicians perform their tasks.
These advancements range from advanced diagnostic tools to sophisticated software applications.
Real-time data and remote monitoring have enhanced the capabilities of field service technicians.
The integration of these technologies has streamlined workflows and increased the effectiveness of service operations.
One significant innovation is the use of augmented reality (AR) and virtual reality (VR).
These technologies allow technicians to visualize complex systems and receive remote assistance from experts.
AR and VR provide step-by-step instructions, helping technicians perform repairs more accurately and quickly.
This reduces the need for on-site training and minimizes errors.
Development of Advanced Diagnostic Tools
Importance of Accurate Diagnostics in Field Service
Accurate diagnostics play a crucial role in field service.
Technicians rely on precise tools to identify and resolve issues swiftly.
Accurate diagnostics reduce the time spent troubleshooting and ensure that repairs address the core problem effectively.
With the right tools, technicians can provide solutions that prevent recurring issues and enhance the reliability of equipment.
Overview of Modern Diagnostic Tools such as AI-Powered Systems
Modern diagnostic tools have significantly advanced, with AI-powered systems leading the way.
These tools use artificial intelligence to analyze data and identify patterns that are not immediately apparent through traditional methods.
AI systems process vast amounts of information quickly, providing technicians with detailed insights into equipment performance.
They can detect anomalies and predict potential failures with high accuracy, making them invaluable in field service.
Benefits of Advanced Diagnostic Tools for Technicians and Customers
The benefits of advanced diagnostic tools are substantial for both technicians and customers.
For technicians, these tools reduce diagnostic time and effort.
AI-powered systems streamline the troubleshooting process, allowing for quicker and more accurate resolutions.
Detailed diagnostics help technicians pinpoint the exact cause of a problem, minimizing guesswork and repetitive repairs.
Customers also experience significant advantages.
Faster diagnostics lead to quicker service and reduced downtime.
Accurate tools ensure that repairs are completed correctly the first time, enhancing customer satisfaction and trust.
Predictive maintenance features of AI-powered systems allow for scheduling maintenance proactively, minimizing disruptions and extending equipment lifespan.
Advanced diagnostic tools also contribute to better resource management.
They enable technicians to arrive on-site with a clear understanding of the issue, reducing the need for additional visits and extra parts.
This efficiency saves both time and costs, benefiting the overall service experience.
In summary, the development of advanced diagnostic tools has transformed field service operations.
Accurate diagnostics, particularly through AI-powered systems, have enhanced both the efficiency of technicians and the satisfaction of customers.
As technology evolves, these tools will likely become even more sophisticated, further improving the field service industry.
Integration of Internet of Things (IoT) technology
How IoT Technology is Transforming Field Service Operations
The Internet of Things (IoT) is fundamentally transforming field service operations by introducing a new level of connectivity and intelligence.
IoT technology connects a network of devices and systems, allowing them to communicate and exchange data in real-time.
This connectivity means field service technicians can access and monitor equipment remotely, without needing to be physically present.
For instance, IoT sensors embedded in machinery can continuously collect data on various performance metrics, such as temperature, vibration, and pressure.
This data is sent to a central system where it is analyzed to detect potential issues before they become critical.
Technicians receive alerts about these issues, enabling them to address problems proactively rather than reactively.
This shift towards proactive maintenance not only reduces the frequency of breakdowns but also minimizes downtime, leading to significant improvements in operational efficiency.
Examples of IoT Devices Used by Field Service Technicians
A wide range of IoT devices are now used by field service technicians to enhance their work.
Smart sensors are among the most common, embedded in equipment to monitor performance metrics and environmental conditions.
These sensors can detect changes that might indicate a potential problem, such as abnormal temperature or vibration levels, and send alerts to technicians in real-time.
Wearable IoT devices, such as smart glasses or augmented reality (AR) headsets, provide technicians with hands-free access to important information while they work.
These devices can overlay digital instructions or schematics onto the technician‘s field of view, improving accuracy and efficiency.
Predictive maintenance systems are another critical IoT application.
These systems utilize data collected from IoT sensors to predict when equipment will need servicing, thus preventing unexpected breakdowns.
This predictive capability helps technicians schedule maintenance activities during non-peak times, further reducing operational disruptions.
Impact of IoT on Efficiency and Service Quality
The impact of IoT on efficiency and service quality is profound.
On the efficiency front, IoT technology automates data collection and analysis, significantly reducing the need for manual monitoring and recording.
Technicians are freed from routine checks and can focus on more complex tasks that require their expertise.
Real-time data and predictive analytics enable early problem detection, allowing for timely intervention before issues escalate into major faults.
This proactive approach reduces the frequency of emergency repairs and extends the lifespan of equipment.
Service quality also benefits greatly from IoT integration.
Technicians have access to accurate, real-time information that enhances their decision-making capabilities.
This leads to more precise repairs and fewer service disruptions.
Faster response times, due to real-time alerts and remote diagnostics, contribute to higher customer satisfaction.
Overall, IoT technology streamlines field service operations, resulting in improved efficiency and superior service quality.
The continued evolution and adoption of IoT in field service are expected to drive even greater advancements, making operations more effective and customer-focused.
Read: The Future of Environmental Engineering Jobs
Utilization of augmented reality (AR) for remote assistance
How AR Technology Is Enhancing Troubleshooting and Repairs
Augmented Reality (AR) is transforming field service by overlaying digital information onto the real world.
Technicians use AR to view schematics, manuals, and step-by-step instructions while working.
This real-time information enhances diagnostic accuracy and speeds up repairs.
AR glasses or mobile devices display relevant data directly on the equipment, helping technicians solve issues more efficiently.
Visual cues and interactive elements guide them through complex procedures, reducing the chance of errors.
Benefits of Using AR for Remote Assistance in Field Service
AR provides significant benefits for remote assistance in field service.
It eliminates the need for specialists to travel to the job site, saving both time and costs.
Technicians in the field can receive real-time guidance from remote experts who see exactly what the technician sees.
This leads to quicker problem resolution and reduces service downtime.
Additionally, AR enables technicians to perform complex tasks with greater confidence, as they have access to real-time, accurate information and expert support.
This improves overall service quality and customer satisfaction.
Case Studies of Companies Implementing AR for Field Service Technicians
Several companies have successfully integrated AR into their field service operations.
Siemens is one example, using AR to assist its technicians with real-time overlays of technical information and repair procedures.
This approach has streamlined maintenance processes and enhanced technician efficiency.
Honeywell has also embraced AR in its field service operations.
Their AR solution provides remote guidance and interactive troubleshooting tools, improving problem-solving capabilities and reducing service times.
Technicians benefit from expert input delivered through AR, leading to more effective repairs.
Caterpillar utilizes AR to support its field service technicians working on heavy machinery.
Caterpillar‘s AR technology offers real-time instructions and diagnostic data, resulting in faster and more accurate repairs.
This innovation has improved equipment uptime and operational productivity.
In essence, AR technology is revolutionizing field service operations.
It enhances troubleshooting and repairs with real-time information, improves efficiency through remote assistance.
And has been successfully implemented by leading companies like Siemens, Honeywell, and Caterpillar.
As AR technology evolves, its impact on the field service industry will continue to grow.
Read: Sustainable Wastewater Treatment Methods
Implementation of predictive maintenance strategies
Importance of Proactive Maintenance in Reducing Downtime
Predictive maintenance is transforming field service operations by focusing on proactive measures.
Addressing potential issues before they become severe significantly reduces equipment downtime.
Instead of responding to failures after they occur, proactive maintenance identifies and mitigates problems in advance.
This approach leads to more reliable operations and lower maintenance costs.
Overview of Predictive Maintenance Tools and Software
Predictive maintenance relies on advanced tools and software to forecast equipment needs.
These tools use data from sensors installed on machinery.
By analyzing this data with sophisticated algorithms, predictive maintenance software can forecast when maintenance will be required.
Real-time monitoring and alerts are crucial features, enabling timely interventions.
Notable tools include IBM‘s Maximo and GE Digital‘s Predix.
Maximo leverages AI and IoT for enhanced analytics, while Predix utilizes machine learning to predict failures accurately.
Case Studies of Companies Benefiting from Predictive Maintenance Strategies
Several companies have successfully implemented predictive maintenance strategies, demonstrating their benefits.
A leading aerospace company integrated predictive maintenance into its aircraft engine management.
This resulted in a 30% reduction in unplanned downtime and lower maintenance costs.
Enhanced operational efficiency and safety were key gains.
Another example is a major manufacturing firm that used predictive maintenance for its production lines.
By monitoring equipment conditions with predictive analytics, the firm achieved a 25% increase in equipment uptime and a 20% reduction in maintenance expenses.
This proactive approach prevented costly production stoppages.
A utility company also adopted predictive maintenance for its power grid.
Using advanced software to analyze data from grid equipment, the company experienced a 40% reduction in equipment failures.
This improvement led to better power supply reliability and operational efficiency.
In summary, predictive maintenance is vital for modern field service operations.
By investing in advanced tools and software, companies can shift from reactive to proactive maintenance.
This results in reduced downtime, lower costs, and improved equipment reliability.
The success stories of companies that have embraced these strategies highlight their significant value in today‘s competitive environment.
Read: Public Health and Environmental Engineering
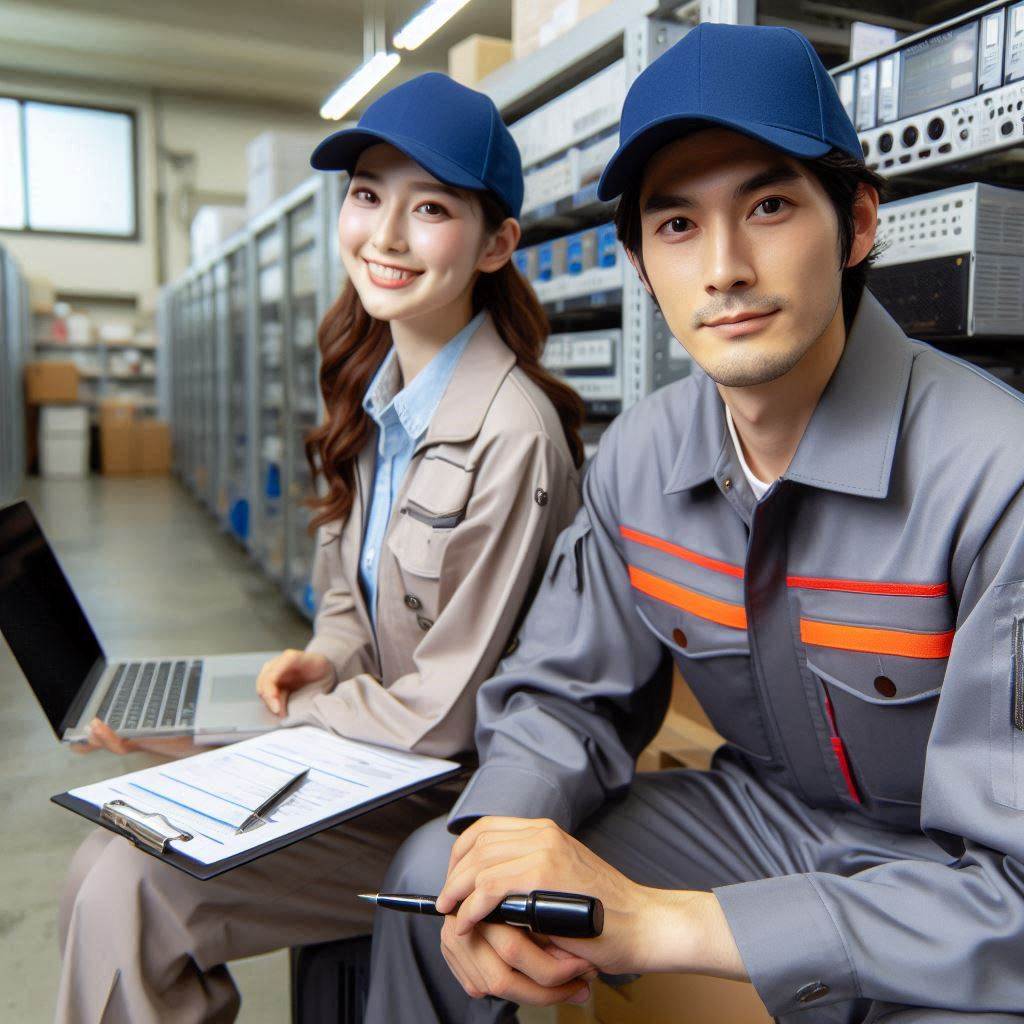
Uncover the Details: Robotics Engineering in Space Exploration: A New Frontier
Adoption of Mobile Field Service Management Apps
Importance of Real-Time Communication and Data Access for Technicians
Mobile field service management apps are revolutionizing the field service industry by enhancing real-time communication and data access.
For field technicians, these capabilities are vital.
Real-time updates allow technicians to receive immediate job notifications and access work orders as soon as they are created.
This instant communication ensures that technicians are always informed about their tasks, any changes in priorities, or updates on customer requirements.
The ability to access data in real time improves problem-solving efficiency.
Technicians can quickly retrieve customer history, equipment details, and previous service records directly from their mobile devices.
This timely access to information enables them to diagnose issues accurately and take appropriate actions without waiting for updates from the office.
Furthermore, it reduces the chances of errors that could occur due to outdated or incomplete information.
Real-time data access helps maintain high service standards and enhances customer satisfaction.
Features of Popular Field Service Management Apps
Field service management apps are packed with features designed to optimize various aspects of service operations.
Scheduling and dispatching are among the most critical functionalities.
These tools allow managers to assign tasks to technicians based on their skills, location, and availability, ensuring that the right person is sent to the right job.
This optimization helps in managing workloads efficiently and reduces the time spent on scheduling and dispatching.
GPS tracking is another significant feature of these apps.
It provides real-time location information, allowing for efficient route planning and minimizing travel time.
This not only saves on fuel costs but also enables technicians to reach their destinations faster, improving overall service efficiency.
Inventory management within these apps helps technicians keep track of parts and equipment needed for their tasks.
This feature ensures that technicians are well-equipped for each job, reducing the likelihood of delays caused by missing parts.
Additionally, real-time reporting and documentation capabilities enable technicians to capture job details, photos, and videos instantly.
This documentation is crucial for compliance, accuracy, and future reference.
How Mobile Apps Are Increasing Efficiency and Productivity for Field Service Technicians
Mobile field service management apps are significantly boosting efficiency and productivity for field technicians.
By streamlining scheduling and dispatching, these apps reduce idle time and ensure that technicians are assigned to jobs that match their skills and proximity.
This optimization leads to a higher number of service calls completed each day, maximizing the use of available resources.
The real-time access to job details and customer history provided by these apps enhances the technicians’ ability to resolve issues quickly.
They can troubleshoot problems on-site with accurate and up-to-date information, minimizing the need for follow-up visits.
Additionally, the integration of customer feedback tools within these apps allows for immediate collection of service reviews.
This feedback is invaluable for assessing service quality and making necessary improvements.
Overall, the adoption of mobile field service management apps leads to increased operational efficiency and productivity.
Technicians benefit from streamlined processes, reduced downtime, and better management of resources.
These advancements contribute to higher customer satisfaction and a more effective field service operation.
customers, and drive operational excellence.
Transform Your Career Today
Unlock a personalized career strategy that drives real results. Get tailored advice and a roadmap designed just for you.
Start NowRead: Environmental Engineering Software and Tools
Uncover the Details: Benefits of Becoming a Telecommunications Technician
Integration of drone technology for inspections and repairs
How Drones Are Being Used in Field Service Operations
Drone technology is revolutionizing field service operations by offering an innovative approach to inspections and repairs.
Drones, or unmanned aerial vehicles (UAVs), are increasingly being deployed across various industries to perform tasks that were once challenging or hazardous for human technicians.
In field service operations, drones are used to inspect infrastructure such as power lines, cell towers, bridges, and pipelines.
Equipped with high-resolution cameras and sensors, drones can capture detailed images and videos from difficult-to-access locations.
These UAVs are particularly useful in inspecting areas that are hard to reach or dangerous for human workers.
For instance, drones can fly over power lines and substations, providing a comprehensive view of their condition without the need for scaffolding or climbing equipment.
This capability allows for more thorough inspections and enables technicians to identify potential issues with greater accuracy.
By integrating drones into field service operations, companies can achieve greater efficiency and effectiveness.
Drones can quickly cover large areas and provide real-time data, which speeds up the inspection process.
This data is invaluable for assessing the condition of infrastructure, planning maintenance, and making informed decisions about repairs.
Benefits of Using Drones for Inspections in Hard-to-Reach Areas
The use of drones for inspections in hard-to-reach areas offers several key benefits.
One of the primary advantages is enhanced safety.
Drones eliminate the need for technicians to work in hazardous conditions, such as high elevations or confined spaces.
This significantly reduces the risk of accidents and injuries, as inspections can be conducted from a safe distance.
Another significant benefit is the ability of drones to provide real-time data.
Traditional inspection methods often involve time-consuming processes and potential delays.
In contrast, drones deliver instant feedback through high-quality visuals and data, enabling technicians to quickly identify and address issues.
This immediate access to information helps in making timely decisions, which is crucial for maintaining the integrity of critical infrastructure.
Drones also offer cost savings by reducing the need for specialized equipment and personnel.
For example, traditional inspections might require expensive scaffolding or aerial lifts.
Drones eliminate these costs by performing inspections efficiently and safely from the air.
This reduction in operational costs, combined with the improved accuracy and speed of inspections, translates into significant savings for companies.
Examples of Companies Leveraging Drone Technology in the Field Service Technician Industry
Several companies are leading the way in leveraging drone technology for field service operations, demonstrating its transformative impact across various industries.
Pacific Gas and Electric (PG&E) is a prominent example.
PG&E utilizes drones to inspect power lines and substations.
The drones provide high-resolution images and videos that help detect potential issues before they become major problems.
This proactive approach enhances the reliability and safety of the power grid, minimizing outages and disruptions.
In the telecommunications industry, Verizon employs drones to inspect cell towers.
These drones capture detailed images and videos of tower structures, allowing technicians to assess their condition without the need for climbing.
This method not only improves inspection efficiency but also reduces the costs associated with tower maintenance and repairs.
The oil and gas sector also benefits from drone technology.
Shell uses drones for pipeline inspections, flying along pipelines to detect leaks, corrosion, and other issues.
The drones provide comprehensive visual data that aids in timely maintenance and helps prevent environmental damage, ensuring the safety and sustainability of pipeline operations.
In the construction industry, Skanska utilizes drones to survey construction sites.
The drones capture aerial footage that helps monitor project progress, verify compliance with safety standards, and manage quality control.
This technology enhances project management and provides valuable insights into site conditions.
These examples highlight how drone technology is enhancing field service operations across various sectors.
By improving safety, efficiency, and data accuracy, drones are becoming an integral tool for modern field service technicians.
See Related Content: Internship Tips for Aspiring Geotechnical Engineers
Conclusion
In this blog, we explored significant innovations in the field service technician industry.
We examined how remote diagnostics and augmented reality enhance problem-solving efficiency.
Mobile apps have streamlined workflow management, making communication and scheduling more efficient.
IoT sensors provide real-time monitoring, allowing technicians to address issues proactively.
Drones offer aerial inspections, reducing the need for manual, time-consuming checks.
These technologies have revolutionized the industry.
Remote diagnostics cut down service times and reduce on-site visits.
Augmented reality improves technician training and troubleshooting with visual aids and step-by-step guidance.
Mobile apps enable seamless integration of service requests and technician schedules, leading to faster response times.
IoT sensors ensure preventive maintenance, minimizing downtime and extending equipment lifespan.
Drones enhance inspection accuracy and safety by accessing hard-to-reach areas.
The positive impact of these innovations is clear.
They increase operational efficiency, reduce costs, and improve service quality.
Technicians can now handle more complex tasks with greater accuracy and less delay.
Companies experience enhanced customer satisfaction and streamlined operations, leading to a competitive edge in the market.