Introduction
Chemical engineering focuses on designing and optimizing processes that transform raw materials into valuable products.
It combines principles from chemistry, physics, biology, and mathematics to develop efficient and sustainable solutions.
Chemical engineers play a crucial role in various industries, including pharmaceuticals, petrochemicals, and food processing.
They design processes that ensure products meet quality standards while minimizing costs and environmental impact.
Process optimization, a key aspect of chemical engineering, aims to improve the efficiency and effectiveness of production processes.
It involves analyzing and fine-tuning various parameters to achieve the best possible outcomes.
Chemical engineers use advanced techniques, such as mathematical modeling, simulation, and control systems, to optimize processes.
These techniques help in identifying bottlenecks, reducing waste, and increasing productivity.
The importance of process optimization in chemical engineering cannot be overstated.
It directly impacts the profitability and sustainability of manufacturing operations.
By optimizing processes, chemical engineers can reduce raw material consumption, energy usage, and waste generation.
This not only lowers production costs but also minimizes the environmental footprint of industrial activities.
In the pharmaceutical industry, process optimization ensures the consistent production of high-quality drugs.
It helps in scaling up production from laboratory to industrial scale while maintaining product efficacy and safety.
Optimization techniques also enable faster development and commercialization of new drugs, benefiting patients and healthcare providers.
Overview of Chemical Engineering
Chemical engineering integrates chemistry, physics, biology, and mathematics to solve industrial problems.
It focuses on process design, optimization, and scaling up production.
Chemical engineers aim to improve efficiency, safety, and sustainability in various industries.
Chemical engineering involves the application of scientific principles to develop processes and products.
It encompasses designing equipment, controlling operations, and improving production methods.
Chemical engineers optimize processes to minimize waste and reduce energy consumption.
Definition of Chemical Engineering
Chemical engineering combines multiple disciplines to convert raw materials into valuable products.
It involves designing processes to produce chemicals, fuels, pharmaceuticals, and food.
Chemical engineers work to enhance product quality, efficiency, and environmental sustainability.
Key Roles and Responsibilities of Chemical Engineers
Chemical engineers play crucial roles in designing, testing, and optimizing processes.
They develop new production methods and ensure safety and compliance with regulations. Their responsibilities include:
- Designing and operating equipment for chemical production.
- Conducting research to develop new products and processes.
- Analyzing data to improve process efficiency and product quality.
- Ensuring environmental and safety standards are met.
- Collaborating with other engineers and scientists on multidisciplinary projects.
Chemical engineers also troubleshoot problems and implement innovative solutions.
They strive to increase efficiency and reduce costs in manufacturing.
Their expertise is vital in scaling up laboratory processes to industrial levels.
Importance of Chemical Engineering in Various Industries
Chemical engineering significantly impacts various industries.
In the pharmaceutical industry, chemical engineers develop processes for producing medicines and vaccines.
They ensure products meet quality standards and are safe for consumption.
In the energy sector, chemical engineers contribute to refining oil and gas and developing renewable energy sources.
They work on processes to convert raw materials into fuels, reducing environmental impact and enhancing sustainability.
The food and beverage industry benefits from chemical engineering through the development of efficient production processes.
Chemical engineers ensure food products are safe, high-quality, and produced cost-effectively.
In the environmental sector, chemical engineers develop processes to treat waste and reduce pollution.
They design systems for water purification, air quality control, and waste management.
Their work helps protect the environment and promote sustainable practices.
In the materials industry, chemical engineers develop new materials with specific properties for various applications.
They work on processes to produce polymers, ceramics, and composites used in numerous products, from electronics to construction materials.
Chemical engineering also plays a critical role in the biotechnology industry.
Chemical engineers design processes for producing biofuels, biopharmaceuticals, and biodegradable materials.
Their work contributes to advancing medical and environmental technologies.
Essentially, chemical engineering is essential across many industries.
Chemical engineers improve processes, develop new products, and ensure safety and sustainability.
Their expertise drives innovation and enhances the quality of life.
Read: Comparison: Architecture Styles across American Regions.
Understanding Process Optimization
Definition of Process Optimization
Process optimization involves refining processes to achieve the best possible performance.
In chemical engineering, it plays a critical role.
It aims to enhance efficiency and productivity while minimizing costs and waste.
By optimizing processes, engineers can improve product quality, reduce energy consumption, and ensure environmental sustainability.
Process optimization is the practice of making processes as effective as possible.
It involves adjusting variables to reach optimal conditions.
This approach helps chemical engineers streamline operations, leading to significant cost savings and increased output.
Importance of Optimizing Processes in Chemical Engineering
The importance of optimizing processes in chemical engineering cannot be overstated.
Process optimization helps to reduce operational costs.
By identifying and eliminating inefficiencies, engineers can save time and resources.
This leads to lower production costs and higher profit margins.
Moreover, process optimization enhances productivity.
Optimized processes run smoothly and predictably, reducing downtime and increasing throughput.
This allows chemical plants to produce more in less time, meeting market demands efficiently.
Energy efficiency is another crucial benefit of process optimization.
By fine-tuning processes, engineers can reduce energy consumption.
This not only cuts costs but also lowers the environmental impact.
Chemical plants that optimize their processes often achieve significant reductions in their carbon footprint.
Process optimization also improves product quality.
Consistent and controlled processes produce higher quality products.
This leads to better customer satisfaction and reduced waste due to defective products.
High-quality products often command higher prices, boosting profitability.
How Process Optimization Improves Efficiency and Productivity
In addition to these benefits, process optimization promotes safety.
Optimized processes operate under controlled conditions, minimizing the risk of accidents.
Safe operations protect workers and prevent costly shutdowns and regulatory penalties.
To achieve process optimization, chemical engineers use various tools and techniques.
These include process simulation, which models processes to identify optimal conditions.
Data analysis helps engineers understand process behavior and make informed decisions.
Advanced control systems automatically adjust process variables to maintain optimal performance.
Process optimization requires a deep understanding of the processes involved.
Engineers must know the relationships between different variables.
They need to understand how changes in one area affect the whole system.
This knowledge allows them to make precise adjustments that improve overall performance.
Continuous improvement is a key aspect of process optimization.
Engineers must regularly review and refine processes.
This ongoing effort ensures that processes remain optimized as conditions change.
It also helps chemical plants to stay competitive in a dynamic market.
Essentially, process optimization is essential in chemical engineering.
It improves efficiency, productivity, energy use, product quality, and safety.
By understanding and implementing optimization techniques, chemical engineers can significantly enhance their operations.
This leads to cost savings, increased output, and a sustainable future.
Process optimization is a powerful tool that drives success in the chemical industry.
Read: 5 Essential Software Tools Every US Architect Uses.
Tools and Techniques for Process Optimization
Introduction to Various Tools Used in Process Optimization
Chemical engineers rely on a variety of tools to optimize processes.
These tools improve efficiency, reduce waste, and increase profitability.
Simulation software, like Aspen Plus and HYSYS, plays a crucial role in process optimization.
These programs model chemical processes, allowing engineers to test different scenarios and identify the most efficient configurations.
By simulating processes before implementation, engineers save time and resources.
Mathematical models are another essential tool.
They provide a quantitative framework to analyze and optimize processes.
Engineers use these models to predict how changes in variables affect the overall process.
This approach helps in fine-tuning operations to achieve desired outcomes.
The use of mathematical models ensures accuracy and reliability in process optimization efforts.
Overview of Common Techniques for Optimizing Processes
Statistical analysis techniques are vital in process optimization.
Methods like Design of Experiments (DOE) and Six Sigma help identify key factors influencing process performance.
By analyzing data, engineers can pinpoint areas needing improvement.
These techniques enable systematic changes that lead to significant enhancements in process efficiency and product quality.
Control systems play a pivotal role in maintaining optimized processes.
Advanced control strategies, such as Model Predictive Control (MPC), allow for real-time adjustments.
These systems continuously monitor process variables and make automatic corrections.
This ensures processes remain within desired parameters, reducing variability and improving stability.
Importance of Data Analysis in Process Optimization
Data analysis is the backbone of process optimization.
Engineers collect and analyze vast amounts of data from various sources.
This data includes temperature, pressure, flow rates, and chemical compositions.
By interpreting this data, engineers gain insights into process behavior and identify opportunities for improvement.
Data analysis tools, such as statistical software and machine learning algorithms, enhance the ability to process and interpret data.
These tools reveal patterns and correlations that might not be apparent through manual analysis.
Engineers use this information to make informed decisions, leading to optimized processes.
Big Data and the Internet of Things (IoT) are revolutionizing process optimization.
IoT devices collect real-time data from sensors installed throughout the process.
This data provides a comprehensive view of the entire system, allowing for more precise control and optimization.
Big Data analytics processes this information, offering actionable insights that drive continuous improvement.
Process optimization is critical for maintaining competitiveness in the chemical industry.
By using advanced tools and techniques, chemical engineers ensure processes are efficient, cost-effective, and sustainable.
These efforts lead to higher product quality, reduced environmental impact, and increased profitability.
Generally, chemical engineers employ a range of tools and techniques to optimize processes.
Simulation software, mathematical models, statistical analysis, and control systems are fundamental.
Data analysis plays a central role, with advancements in Big Data and IoT further enhancing capabilities.
By leveraging these tools, engineers drive continuous improvement, ensuring efficient and sustainable chemical processes.
Read: Decoding the Ethics & Responsibilities of US Civil Engineers
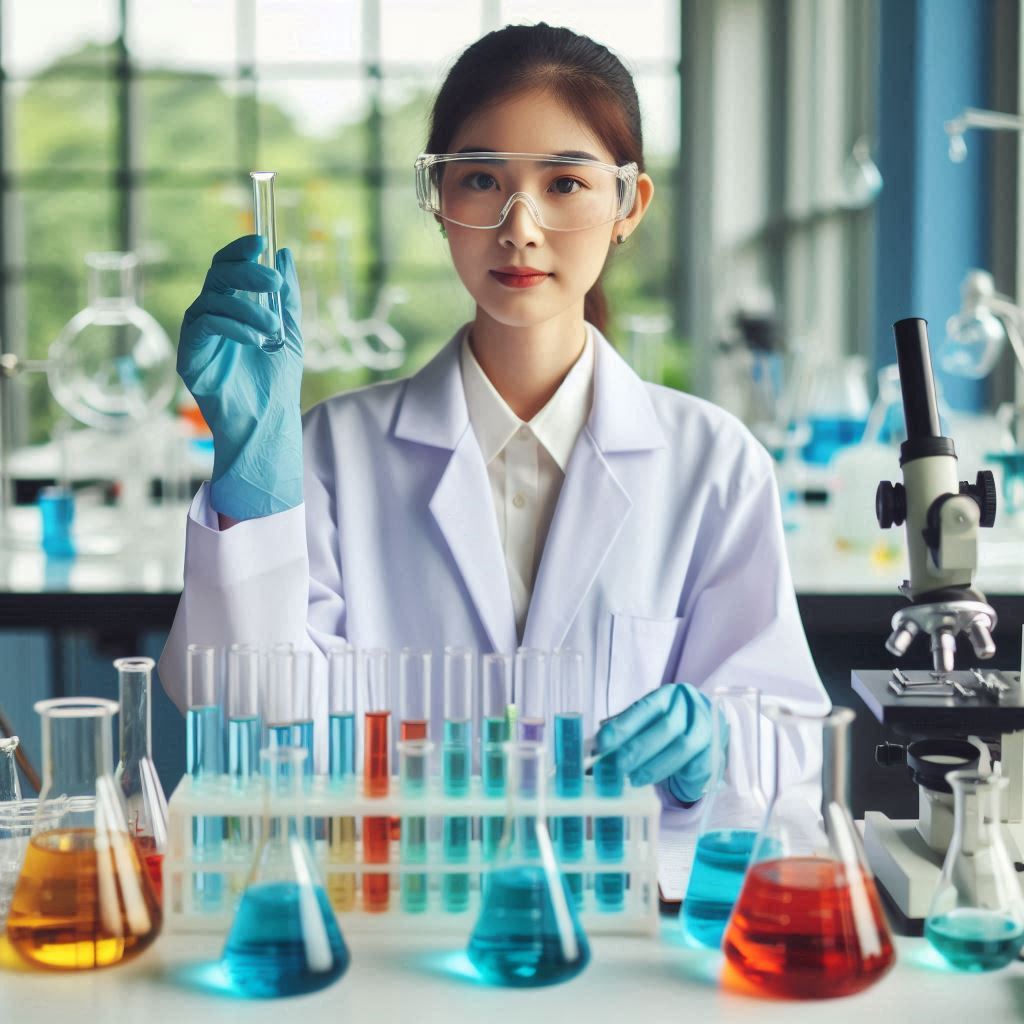
Case Studies of Successful Process Optimization
Successful process optimization in chemical engineering drives efficiency, reduces costs, and enhances product quality. In this section, we explore case studies of companies that have excelled in this area.
These examples highlight the benefits of process optimization and the lessons learned.
Examples of Companies That Have Successfully Optimized Their Processes in Chemical Engineering
BASF
BASF, a global leader in chemical production, implemented advanced process control in their ammonia synthesis.
They optimized reaction conditions using real-time data and predictive analytics.
This approach reduced energy consumption by 10% and increased yield by 5%.
BASF’s success demonstrates the power of data-driven decision-making in chemical engineering.
Dow Chemical Company
Dow Chemical focused on optimizing their polymer production processes.
By integrating machine learning algorithms, they identified key variables affecting product quality.
Adjustments to these variables led to a 15% reduction in waste and a 20% increase in throughput.
Dow’s experience underscores the importance of embracing digital tools in process optimization.
Shell Chemicals
Shell Chemicals optimized their ethylene production through process integration and heat recovery.
They redesigned their heat exchanger network to maximize energy efficiency.
This effort resulted in a 25% reduction in energy consumption and a significant decrease in emissions.
Shell’s success highlights the environmental and economic benefits of process optimization.
Transform Your Career Today
Unlock a personalized career strategy that drives real results. Get tailored advice and a roadmap designed just for you.
Start NowDuPont
DuPont enhanced their bioprocessing operations by optimizing fermentation conditions.
They used advanced sensors and automation to monitor and control critical parameters.
These improvements increased product yield by 10% and reduced batch cycle time by 15%.
DuPont’s case illustrates the potential of process optimization in biotechnological applications.
Bayer AG
Bayer AG optimized their pharmaceutical manufacturing processes through continuous manufacturing techniques.
They implemented inline quality monitoring to ensure consistent product quality.
This transition from batch to continuous processes reduced production time by 30% and improved overall efficiency.
Bayer’s example shows the transformative impact of modern manufacturing methods.
Benefits Achieved by Companies Through Process Optimization
The benefits achieved by these companies through process optimization are substantial.
Energy savings reduce operational costs and environmental impact.
Increased yields and throughput enhance profitability and market competitiveness.
Reduced waste improves sustainability and regulatory compliance.
These benefits collectively contribute to the long-term success of chemical engineering operations.
Lessons Learned from These Case Studies
Several key lessons emerge from these case studies.
First, data-driven decision-making is crucial.
Real-time monitoring and predictive analytics enable proactive adjustments.
Second, integrating digital tools like machine learning and automation enhances process control.
Third, process integration and energy recovery are vital for maximizing efficiency.
Finally, continuous manufacturing offers significant advantages over traditional batch processes.
These case studies of successful process optimization in chemical engineering demonstrate the transformative potential of strategic improvements.
Companies like BASF, Dow Chemical, Shell Chemicals, DuPont, and Bayer AG have set benchmarks for the industry.
Their experiences highlight the critical role of data, digital tools, and innovative manufacturing techniques.
Embracing these practices can drive efficiency, reduce costs, and enhance sustainability.
By learning from these examples, other companies can achieve similar success in process optimization.
Read: Top Cities for Electrical Engineering Jobs in America
Gain More Insights: Professional Organizations for Transportation Engineers
Challenges in Process Optimization
Chemical engineers face numerous challenges in optimizing processes.
These challenges can hinder efficiency and productivity.
Identifying and addressing these obstacles is crucial for successful optimization.
Here are common challenges faced by chemical engineers and strategies to overcome them.
Common Challenges Faced by Chemical Engineers in Optimizing Processes
One major challenge is the complexity of chemical processes.
Many variables and interactions make optimization difficult.
Engineers must understand each component and its effect on the process.
This requires in-depth knowledge and experience.
Another challenge is dealing with outdated equipment.
Old machinery can limit the potential for optimization.
Engineers often face the dilemma of upgrading equipment or working within existing constraints.
Both options involve significant time and cost.
Variability in raw materials is also a common issue.
Inconsistent quality or supply can disrupt optimization efforts.
Engineers need to account for these variations and develop adaptable processes.
This requires thorough testing and flexible designs.
Factors that Can Hinder the Optimization Process
Regulatory compliance is another hurdle.
Strict regulations can restrict optimization options.
Engineers must balance efficiency with adherence to laws and standards.
This often involves additional steps and documentation, slowing down the process.
Energy consumption poses a significant challenge as well.
Optimizing processes to reduce energy use without sacrificing output is complex.
Engineers need to find innovative solutions that maintain efficiency while cutting energy costs.
This often involves adopting new technologies and practices.
Human factors also play a role.
Resistance to change from staff can impede optimization efforts.
Training and communication are essential to gain buy-in from all stakeholders.
Engineers must work closely with teams to implement new processes smoothly.
Limited data availability can hinder optimization.
Accurate data is crucial for making informed decisions.
Engineers need reliable sensors and monitoring systems to collect real-time data.
Without this, optimization efforts may be based on assumptions rather than facts.
Strategies for Overcoming Challenges in Process Optimization
To overcome these challenges, engineers can employ several strategies.
First, they should invest in continuous education and training.
Staying updated with the latest technologies and methods is essential.
This enables engineers to apply the best practices in optimization.
Collaboration is another key strategy.
Engineers should work with other departments and external experts.
This provides diverse perspectives and solutions.
Cross-functional teams can tackle complex problems more effectively.
Implementing advanced data analytics is crucial.
Engineers should leverage big data and machine learning to analyze processes.
These tools can identify patterns and suggest improvements.
Real-time data analytics enable quick adjustments and optimization.
Regular maintenance and upgrades of equipment are also vital.
Engineers should schedule routine checks and invest in modern machinery.
This reduces downtime and enhances process efficiency.
Up-to-date equipment can significantly improve optimization potential.
Adopting a proactive approach to regulatory compliance helps as well.
Engineers should stay informed about changes in regulations.
Early preparation ensures compliance without disrupting optimization efforts.
This involves close monitoring of industry standards and legal requirements.
Finally, fostering a culture of continuous improvement is essential.
Encouraging innovation and feedback from all levels promotes ongoing optimization.
Engineers should create an environment where new ideas are welcomed and tested.
This leads to sustainable improvements in processes.
In summary, chemical engineers face various challenges in process optimization.
However, with the right strategies, these challenges can be overcome.
Continuous learning, collaboration, data analytics, equipment maintenance, regulatory awareness, and a culture of improvement are key to successful optimization.
See Related Content: Internship Tips for Mining Engineering Students
Delve into the Subject: Ethical Considerations in Environmental Engineering
Discover More: Environmental Engineering in Water Resource Management
Future Trends in Chemical Engineering and Process Optimization
Emerging Technologies and Trends in Process Optimization
Chemical engineering is evolving rapidly, driven by emerging technologies and trends in process optimization.
Advanced data analytics is revolutionizing how engineers optimize processes.
By leveraging big data and machine learning, engineers can now predict outcomes with greater accuracy.
This leads to more efficient processes and reduced costs.
For instance, predictive maintenance uses real-time data to foresee equipment failures before they happen.
This proactive approach minimizes downtime and enhances productivity.
Another significant trend is the integration of artificial intelligence (AI) in process optimization.
AI algorithms can analyze complex datasets and provide actionable insights.
This enables chemical engineers to make informed decisions swiftly.
AI-driven process control systems can adjust parameters in real time, ensuring optimal conditions continuously.
These advancements result in improved yield, reduced waste, and lower energy consumption.
The rise of digital twins is also transforming process optimization.
A digital twin is a virtual replica of a physical system.
Engineers use digital twins to simulate processes and test changes without disrupting actual operations.
This technology allows for experimentation and optimization in a risk-free environment.
Digital twins provide valuable insights that lead to process improvements and innovation.
Sustainability is becoming a core focus in chemical engineering.
Engineers are increasingly adopting green chemistry principles and sustainable practices.
Process optimization now often includes reducing carbon footprints and minimizing environmental impact.
Advances in bioprocessing and renewable energy sources are also shaping the future.
These trends are driving the development of more sustainable and eco-friendly processes.
Potential Impact of Advancements in Process Optimization on the Field of Chemical Engineering
The potential impact of these advancements on chemical engineering is immense.
Improved process optimization techniques lead to higher efficiency and lower costs.
This makes chemical engineering more competitive and sustainable.
Enhanced process control and predictive analytics reduce the likelihood of errors and accidents.
This results in safer working environments and better compliance with regulations.
Staying updated with the latest trends in process optimization is crucial for chemical engineers.
Continuous learning ensures engineers can leverage new technologies effectively.
Professional development programs and industry conferences offer valuable opportunities to learn about emerging trends.
Engaging with industry experts and participating in workshops can provide practical insights.
Importance of Staying Updated with the Latest Trends in Process Optimization
Online platforms like LinkedIn and industry-specific forums are excellent resources for staying informed.
Engineers can join professional groups and follow thought leaders to keep abreast of innovations.
Subscribing to relevant journals and publications also helps in staying current with technological advancements.
Basically, the future of chemical engineering and process optimization looks promising.
Emerging technologies like AI, digital twins, and sustainable practices are shaping the industry.
These advancements promise improved efficiency, sustainability, and safety.
By staying updated with these trends, chemical engineers can drive innovation and maintain a competitive edge in the field.
Continuous learning and professional development are essential for leveraging new technologies and achieving process excellence.
latest trends in process optimization, chemical engineers can drive innovation, improve operations, and contribute to the advancement of the field.
Find Out More: Top Books for Industrial Engineers
Conclusion
Process optimization in chemical engineering remains crucial for improving efficiency, reducing costs, and enhancing product quality.
Chemical engineers must prioritize process optimization in their work to stay competitive and meet industry demands.
By focusing on optimization, engineers can ensure sustainable and environmentally friendly operations.
The importance of process optimization cannot be overstated.
It allows for the efficient use of resources, minimizing waste and energy consumption.
This efficiency leads to cost savings and higher profitability for companies.
Furthermore, optimized processes contribute to consistent product quality, which is vital for maintaining customer satisfaction and loyalty.
Chemical engineers play a vital role in process optimization.
They design and implement systems that streamline operations and maximize output.
By leveraging advanced technologies and methodologies, engineers can identify inefficiencies and develop solutions to address them.
This proactive approach not only improves current processes but also prepares companies for future challenges.
To prioritize process optimization, chemical engineers should continuously seek ways to improve.
They must stay updated with the latest advancements in technology and industry practices.
Participating in professional development opportunities, such as workshops and seminars, can enhance their skills and knowledge.
Collaboration with peers and industry experts also provides valuable insights and innovative ideas.