Introduction
Artificial intelligence (AI) refers to the simulation of human intelligence in machines.
These machines are programmed to think and learn like humans.
AI technologies include machine learning, natural language processing, and robotics.
These innovations enable automation and enhance decision-making processes across various industries.
Industrial engineering plays a crucial role in today‘s society by optimizing processes and improving efficiency.
Industrial engineers analyze workflows to reduce waste and increase productivity.
Their work significantly impacts sectors like manufacturing, healthcare, and logistics.
By implementing efficient systems, they help organizations achieve their goals while minimizing costs.
The impact of AI on industrial engineering is profound and transformative.
AI technologies streamline operations, enabling engineers to analyze vast data sets quickly.
This capability leads to better forecasting and more informed decision-making.
AI-powered tools automate repetitive tasks, freeing engineers to focus on complex problem-solving.
Furthermore, AI enhances process design and optimization by identifying patterns that humans might overlook.
Industrial engineers can leverage AI to create smarter, more efficient systems.
As AI continues to evolve, its integration into industrial engineering will drive innovation and reshape how industries operate.
Embracing AI will allow industrial engineers to address modern challenges and contribute to a more efficient future.
History of AI in Industrial Engineering
Evolution of Artificial Intelligence in the Field of Industrial Engineering
Artificial intelligence (AI) has transformed industrial engineering over the past few decades.
The evolution of AI began with simple automation in manufacturing.
Early systems focused on repetitive tasks, increasing efficiency and reducing human error.
As technology advanced, AI evolved into more complex systems capable of decision-making.
In the late 20th century, machine learning emerged as a significant development.
This technology allowed systems to learn from data and improve over time.
Industrial engineers began to harness machine learning for predictive maintenance and quality control.
The introduction of big data further accelerated AI‘s evolution.
Industrial engineers now had access to vast amounts of data from various sources.
Analyzing this data enabled engineers to gain insights and optimize processes.
AI algorithms could identify patterns that human analysts might overlook.
Today, AI systems incorporate advanced technologies such as deep learning and natural language processing.
These innovations allow for more sophisticated applications in industrial engineering.
Engineers can utilize AI for complex problem-solving and real-time decision-making.
Key Milestones and Breakthroughs in the Integration of AI Technology
Several key milestones mark the integration of AI technology into industrial engineering.
One major breakthrough occurred with the development of computer vision systems.
These systems use AI to analyze visual data from cameras and sensors.
They enable quality control by detecting defects in real-time during production.
Another significant milestone is the rise of autonomous systems.
Industrial engineers have implemented AI-driven robots in manufacturing processes.
These robots can perform tasks with high precision and speed, enhancing overall productivity.
The introduction of AI-driven simulation tools also revolutionized industrial engineering.
Engineers can create digital twins of production systems, allowing for testing and optimization.
This capability helps identify potential issues before implementation, reducing downtime and costs.
Moreover, advancements in optimization algorithms have improved supply chain management.
AI can analyze logistics data to optimize routes and inventory levels.
These improvements lead to reduced operational costs and increased efficiency.
Examples of Successful Implementation of AI in Industrial Engineering
Many industries have successfully implemented AI technologies in their operations.
For instance, automotive manufacturers use AI for predictive maintenance.
AI analyzes data from machinery to predict failures and schedule maintenance.
This proactive approach reduces downtime and improves productivity.
In the aerospace industry, AI enhances quality control processes.
Companies employ AI-driven visual inspection systems to detect defects in components.
This automation significantly improves accuracy and reduces the risk of human error.
The consumer goods sector has also benefited from AI.
Retailers use AI for demand forecasting and inventory management.
By analyzing sales data, AI predicts customer demand, optimizing stock levels.
Additionally, AI-driven process optimization has transformed manufacturing environments.
Companies utilize AI to streamline production processes and improve resource allocation.
This leads to reduced waste and enhanced efficiency.
Lastly, AI has played a crucial role in energy management.
Industrial engineers use AI systems to optimize energy consumption in manufacturing facilities.
These systems analyze usage patterns and suggest improvements, reducing costs and environmental impact.
AI has evolved significantly within industrial engineering, driving innovations and improving efficiency.
Key milestones, such as computer vision and autonomous systems, showcase its transformative power.
Successful implementations across various industries highlight AI‘s potential to revolutionize industrial engineering practices.
By embracing AI, engineers can enhance productivity and navigate the future of industry.
Read: The Role of NCARB in US Architecture Licensing.
Benefits of AI in Industrial Engineering
Increased Efficiency and Productivity Through Automation
AI significantly enhances efficiency and productivity in industrial engineering.
Automation allows machines to perform repetitive tasks with precision and speed.
This reduces the time required for production processes, leading to quicker outputs.
AI-driven automation also minimizes human error.
Machines consistently execute tasks without the fatigue that affects human workers.
This consistency boosts overall product quality and reliability.
Furthermore, AI technologies can optimize production schedules.
They analyze real-time data to determine the best workflows.
This capability ensures that resources are used effectively and production lines operate smoothly.
Incorporating AI-powered robots into manufacturing processes also improves flexibility.
These robots can adapt to various tasks and changing demands.
This adaptability allows companies to respond quickly to market fluctuations.
AI systems can monitor equipment health continuously.
Predictive maintenance reduces downtime by addressing issues before they become critical.
This proactive approach enhances overall operational efficiency and productivity.
Improved Decision-Making Processes with Predictive Analytics
AI empowers industrial engineers with predictive analytics, improving decision-making processes.
Predictive analytics uses historical data to forecast future trends and behaviors.
This capability enables engineers to make informed choices based on data-driven insights.
With predictive analytics, engineers can identify potential bottlenecks in production.
They can analyze patterns and anticipate when disruptions might occur.
This foresight allows for proactive measures to maintain smooth operations.
Moreover, predictive analytics aids in inventory management.
Engineers can forecast demand accurately, ensuring that stock levels meet customer needs.
This optimization reduces the risk of overstocking or stockouts.
AI tools also facilitate scenario planning.
Engineers can simulate different operational scenarios and evaluate their impacts.
This flexibility allows for more strategic decision-making in dynamic environments.
In addition, AI enhances workforce management.
By analyzing employee performance data, engineers can identify training needs.
This targeted approach improves workforce efficiency and productivity.
Cost Reduction and Waste Minimization Through Optimization Algorithms
AI technologies contribute to cost reduction and waste minimization through optimization algorithms.
These algorithms analyze complex systems and processes to identify inefficiencies.
By optimizing workflows, companies can reduce operational costs significantly.
One significant area of cost reduction is material usage.
AI algorithms can optimize material flows and minimize waste in production.
This optimization not only lowers costs but also supports sustainability efforts.
Furthermore, AI can optimize supply chain management.
Algorithms analyze data from suppliers, inventory levels, and customer demands.
This analysis helps companies streamline their supply chains and reduce excess costs.
Energy consumption is another critical area for cost savings.
AI systems can optimize energy usage in manufacturing processes.
By reducing energy consumption, companies can lower their utility bills and environmental impact.
AI-driven optimization leads to improved product design.
Engineers can use algorithms to test various design configurations quickly.
This capability reduces prototyping costs and accelerates time-to-market.
In conclusion, AI profoundly impacts industrial engineering.
It increases efficiency and productivity through automation, enhances decision-making processes with predictive analytics, and reduces costs through optimization algorithms.
Embracing AI technologies allows industrial engineers to drive innovation and improve overall operational effectiveness in their organizations.
Read: Exploring Architect Salary Trends: USA Analysis.
Challenges of Implementing AI in Industrial Engineering
Resistance to Change from Traditional Practices
The impact of AI on industrial engineering faces significant resistance from traditional practices.
Many organizations rely on established methods and processes.
This reliance creates a reluctance to adopt new technologies.
Employees often feel comfortable with familiar systems and workflows.
Moreover, skepticism about AI’s effectiveness contributes to resistance.
Some professionals doubt whether AI can deliver on its promises.
They fear that automation may complicate established practices rather than improve them.
This skepticism can hinder the integration of AI into existing systems.
Leadership also plays a crucial role in overcoming this resistance.
Effective change management strategies are necessary to facilitate adoption.
Organizations must communicate the benefits of AI clearly and consistently.
By highlighting success stories and demonstrating value, leaders can alleviate fears.
Training and support are essential for easing the transition.
Organizations should provide resources to help employees adapt to new technologies.
This approach can build confidence and encourage acceptance of AI-driven processes.
Data Security and Privacy Concerns
Data security and privacy concerns pose significant challenges to AI integration in industrial engineering.
The reliance on data-driven insights raises questions about the safety of sensitive information.
Organizations must ensure that data remains secure from unauthorized access and breaches.
Implementing AI systems often requires large volumes of data.
This data collection can inadvertently expose organizations to risks.
Data leaks or breaches can lead to financial losses and reputational damage.
Consequently, companies must prioritize robust cybersecurity measures.
Compliance with data protection regulations is another critical consideration.
Organizations must adhere to laws like GDPR and CCPA.
Failure to comply can result in hefty fines and legal repercussions.
Ensuring data privacy should be a top priority during AI implementation.
Moreover, transparency in AI algorithms is essential.
Stakeholders need to understand how data is used and processed.
Providing clear information builds trust among employees, customers, and partners.
Potential Job Displacement and Workforce Retraining Needs
The rise of AI in industrial engineering raises concerns about potential job displacement.
Automation can streamline processes and reduce the need for manual labor.
As a result, some positions may become obsolete, leading to workforce challenges.
However, AI also creates new job opportunities.
Industries will require skilled professionals to manage and maintain AI systems.
This shift means that the workforce must adapt to changing demands.
Retraining initiatives are essential for addressing workforce displacement.
Organizations must invest in upskilling their employees.
Providing training programs equips workers with the skills needed to thrive in an AI-driven environment.
Collaboration between companies and educational institutions can enhance retraining efforts.
Partnerships can help develop curricula focused on AI technologies and applications.
This approach prepares the workforce for future challenges and opportunities.
In closing, AI’s impact on industrial engineering faces challenges like resistance to change, data security concerns, and potential job displacement.
Organizations must implement effective change management strategies to overcome resistance.
They should prioritize data protection to mitigate security risks.
Finally, investing in workforce retraining initiatives will ensure that employees remain valuable contributors in an AI-enhanced environment.
By addressing these challenges, the industrial engineering sector can harness AI’s full potential.
Read: Comparison: Architecture Styles across American Regions.
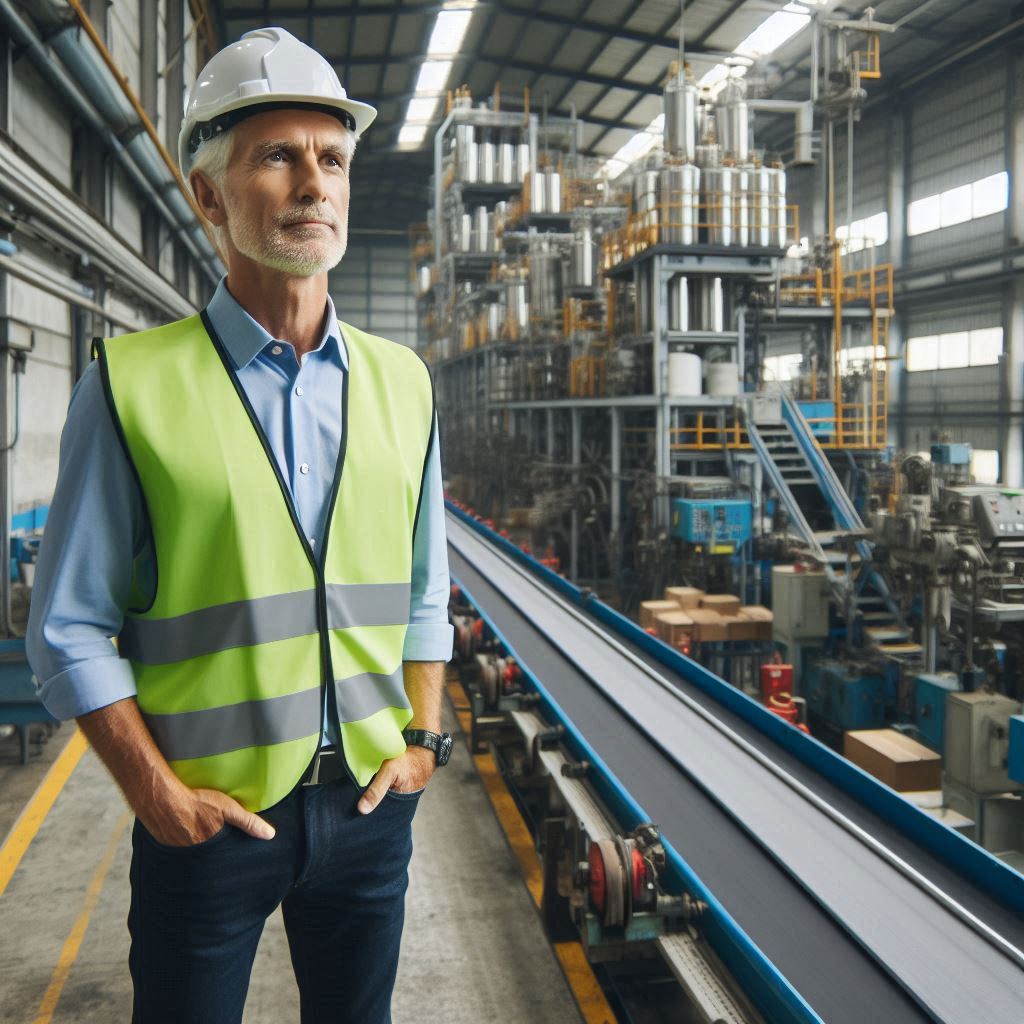
Current Applications of AI in Industrial Engineering
Robotics and Automation in Manufacturing Processes
Artificial Intelligence (AI) significantly impacts robotics and automation in manufacturing processes.
AI enhances the capabilities of robots, enabling them to perform complex tasks.
These advanced robots can adapt to changing environments and handle diverse operations.
Automated systems improve efficiency and reduce human error in manufacturing.
AI-powered robots can work tirelessly without fatigue.
This consistency leads to increased production rates and higher quality outputs.
Furthermore, AI-driven robotics allow for greater precision in manufacturing tasks.
They can perform intricate operations with accuracy that surpasses human capabilities.
This precision reduces waste and minimizes rework, resulting in cost savings.
Integration of AI in robotics also fosters collaboration between machines and humans.
Collaborative robots, or cobots, work alongside human operators.
This partnership enhances productivity and allows for more complex task execution.
AI optimizes the scheduling of manufacturing processes.
Intelligent systems can predict equipment maintenance needs, preventing downtime.
This predictive maintenance ensures smooth operations and prolongs equipment lifespan.
Supply Chain Management and Logistics Optimization
AI plays a crucial role in supply chain management and logistics optimization.
It streamlines operations by analyzing data and identifying inefficiencies.
AI algorithms predict demand patterns, allowing for more accurate inventory management.
Through predictive analytics, companies can optimize stock levels and reduce excess inventory.
This optimization minimizes carrying costs and enhances cash flow.
AI also facilitates real-time tracking of shipments, improving visibility across the supply chain.
Moreover, AI enhances route optimization for logistics operations.
By analyzing traffic patterns and delivery schedules, AI can recommend the most efficient routes.
This optimization reduces transportation costs and delivery times.
AI-powered systems can also assess supplier performance, helping companies choose the best partners.
These systems analyze factors such as delivery reliability and quality.
This information supports strategic decision-making in supply chain management.
Furthermore, AI fosters collaboration among supply chain partners.
By sharing data and insights, companies can work together to improve efficiency.
This collaboration leads to a more responsive and resilient supply chain.
Quality Control and Defect Detection Using Machine Learning Algorithms
Machine learning algorithms revolutionize quality control and defect detection in manufacturing.
These algorithms analyze data from production processes to identify patterns associated with defects.
By continuously learning from data, machine learning models improve their accuracy over time.
AI-powered quality control systems can detect defects in real-time.
Cameras and sensors equipped with machine learning algorithms monitor products during production.
These systems identify anomalies that might indicate quality issues, allowing for immediate corrective actions.
Implementing machine learning for quality control reduces reliance on manual inspections.
Automation of this process enhances speed and accuracy.
This shift leads to faster production cycles and reduced labor costs.
Machine learning algorithms can predict potential defects based on historical data.
By analyzing past production data, these algorithms identify risk factors.
This proactive approach allows manufacturers to implement preventive measures before issues arise.
Moreover, AI-driven quality control fosters continuous improvement in manufacturing processes.
By analyzing defects, manufacturers can pinpoint root causes and implement solutions.
This data-driven approach enhances overall product quality and customer satisfaction.
In review, AI profoundly impacts industrial engineering across multiple domains.
Robotics and automation streamline manufacturing processes, while AI optimizes supply chain management and logistics.
Machine learning algorithms enhance quality control and defect detection, ensuring high standards in production.
By embracing AI technologies, industrial engineers can drive innovation and efficiency within their organizations.
Read: 5 Essential Software Tools Every US Architect Uses.
Delve into the Subject: Future Trends in Drafter Engineering & Technology
Future Trends in AI for Industrial Engineering
Continued Advancements in Machine Learning and Deep Learning Technologies
Advancements in machine learning and deep learning technologies significantly impact industrial engineering.
These technologies enhance decision-making processes and improve operational efficiency.
By leveraging large data sets, engineers can identify patterns and trends that were previously unnoticed.
Machine learning algorithms analyze historical data to predict future outcomes and optimize processes.
Deep learning technologies enable more complex problem-solving capabilities.
They utilize neural networks to process vast amounts of data, improving accuracy in predictions.
This capability is particularly valuable in manufacturing, where precision and reliability are crucial.
Engineers can use deep learning to enhance quality control and defect detection in production lines.
Furthermore, these technologies facilitate automation in various industrial applications.
Automated systems can learn from their environments and improve their performance over time.
This evolution reduces the need for human intervention and minimizes errors in processes.
As a result, engineers can focus on more strategic tasks that drive innovation and growth.
Integration of AI with Internet of Things (IoT) for Real-Time Data Analysis
The integration of AI with the Internet of Things (IoT) revolutionizes industrial engineering practices.
IoT devices collect vast amounts of data from sensors and machines in real-time.
When paired with AI, this data becomes invaluable for optimizing operations and making informed decisions.
AI algorithms process the data gathered from IoT devices to identify inefficiencies.
Engineers can quickly respond to issues as they arise, preventing costly downtime.
Real-time data analysis allows for immediate adjustments in production processes, leading to improved resource allocation.
Moreover, the combination of AI and IoT enhances predictive maintenance strategies.
Engineers can monitor equipment health and predict failures before they occur.
This proactive approach reduces maintenance costs and extends the lifespan of machinery.
As a result, organizations experience increased productivity and reduced operational risks.
The synergy between AI and IoT empowers industrial engineers to create smarter, more responsive systems.
Transform Your Career Today
Unlock a personalized career strategy that drives real results. Get tailored advice and a roadmap designed just for you.
Start NowPotential for Autonomous Systems and Self-Optimizing Factories
The potential for autonomous systems is transforming the landscape of industrial engineering.
Autonomous machines can perform tasks without human intervention, enhancing efficiency and safety.
These systems leverage AI to learn from their surroundings and adapt to changing conditions.
Self-optimizing factories are a prime example of this potential.
In these factories, machines communicate with each other to optimize production processes.
They analyze data in real-time, adjusting operations to maximize output and minimize waste.
Engineers play a crucial role in designing and implementing these autonomous systems.
They ensure that systems are robust, reliable, and safe for operation.
Furthermore, engineers develop algorithms that enable machines to learn and improve their performance over time.
The emergence of autonomous systems also requires new skill sets in industrial engineering.
Engineers must be proficient in AI, data analytics, and system integration to thrive in this evolving landscape.
This shift creates exciting opportunities for professionals in the field.
To sum it up, AI significantly impacts industrial engineering through advancements in machine learning, IoT integration, and autonomous systems.
These technologies enhance decision-making, optimize operations, and create self-optimizing factories.
As engineers adapt to these changes, they will drive innovation and efficiency in the industry.
Embracing AI will pave the way for a more advanced and productive future in industrial engineering.
Gain More Insights: Continuing Education for Materials Engineering Professionals
Ethical Considerations in AI for Industrial Engineering
Transparency and Accountability in Algorithm Decision-Making
Artificial Intelligence (AI) significantly impacts industrial engineering by enhancing decision-making processes.
However, transparency and accountability in algorithm decisions are critical.
Engineers must understand how algorithms make decisions to ensure reliability.
Transparent algorithms allow stakeholders to trust AI-generated outcomes.
To achieve transparency, engineers should document the algorithms’ decision-making processes.
Clear documentation helps stakeholders understand the underlying logic.
This understanding fosters trust and encourages collaboration among teams.
Accountability is equally essential in AI systems.
Engineers must establish who is responsible for algorithmic outcomes.
Organizations should implement protocols to address errors or unintended consequences.
These protocols help maintain accountability throughout the AI implementation process.
Moreover, regulatory frameworks can enhance transparency and accountability.
Governments and industry bodies should create guidelines for ethical AI usage.
These guidelines can ensure that organizations prioritize responsible practices in their AI development and deployment.
Fairness and Bias Mitigation in AI Systems
Fairness in AI systems is vital for industrial engineering applications.
Algorithms can unintentionally perpetuate existing biases present in the data.
Biased algorithms can lead to unfair outcomes in hiring, promotions, or resource allocation.
Therefore, engineers must actively work to mitigate bias in AI systems.
Engineers should start by evaluating the data used to train AI models.
They must identify any biases and take corrective actions.
This may involve using diverse datasets that reflect various demographics.
By ensuring diverse representation in training data, engineers can promote fairness.
Engineers can implement fairness metrics to evaluate AI systems.
These metrics help assess whether algorithms produce equitable outcomes.
Regular audits of AI systems can ensure they remain fair over time.
Continuous monitoring allows organizations to adjust algorithms as necessary.
Moreover, involving diverse teams in AI development can promote fairness.
Engineers should collaborate with social scientists, ethicists, and representatives from affected communities.
These collaborations can provide valuable insights and enhance fairness in AI systems.
Ensuring Responsible Use of AI Technology to Benefit Society as a Whole
The responsible use of AI technology is essential for maximizing its benefits.
Industrial engineers play a key role in ensuring that AI serves society positively.
Organizations should prioritize ethical considerations when developing and deploying AI solutions.
First, engineers must consider the societal implications of their AI systems.
They should assess how AI technologies impact different communities.
Understanding these effects helps engineers design solutions that promote social good.
Organizations can establish ethical review boards to oversee AI projects.
These boards can evaluate projects for potential social impacts and ethical concerns.
Involving a diverse group of stakeholders ensures a well-rounded perspective on AI technology.
Furthermore, education and training in ethical AI practices are crucial.
Engineers should receive training on the ethical implications of AI technology.
This education empowers them to make informed decisions throughout the development process.
To summarize, the impact of AI on industrial engineering is profound.
Ensuring transparency and accountability in algorithm decision-making is essential.
Mitigating bias and promoting fairness will enhance the integrity of AI systems.
By prioritizing responsible AI use, industrial engineers can contribute to a more equitable and beneficial society.
Uncover the Details: Certifications Needed for Petroleum Technicians
Conclusion
AI significantly impacts industrial engineering by enhancing efficiency and productivity across various sectors.
It streamlines operations through automation, reducing manual labor and human error.
AI-driven analytics provide valuable insights for decision-making, optimizing processes and resource allocation.
Machine learning algorithms enable predictive maintenance, minimizing downtime and operational costs.
The blog post highlighted how AI tools improve quality control and supply chain management.
By utilizing AI, engineers can identify patterns and anomalies in real-time data.
This capability allows for rapid response to potential issues, enhancing overall performance.
Industrial engineering professionals must embrace AI technology to remain competitive in the field.
Adopting these tools will empower you to make data-driven decisions and improve project outcomes.
Continuous learning about AI advancements will strengthen your skill set and career prospects.
The future of AI in industrial engineering is promising.
As technology evolves, AI will continue to shape the industry landscape.
Emerging trends like digital twins and smart factories will redefine traditional engineering practices.
Stay proactive in exploring AI applications relevant to your work.
Engage in training programs and workshops to expand your knowledge.
By embracing AI, you can lead the charge in transforming industrial engineering for the better.
[E-Books for Sale]
The Big Book of 500 High-Paying Jobs in America: Unlock Your Earning Potential
$19.99 • 500 High-Paying Jobs • 330 pages
Explore 500 high-paying jobs in America and learn how to boost your career, earn more, and achieve success!
See All 500 High-Paying Jobs of this E-Book
1001 Professions Without a Degree: High-Paying American Jobs You Can Start Now
$19.99 • 1001 Professions Without a Degree • 174 pages
Discover 1001 high-paying jobs without a degree! Unlock career tips, skills, and success strategies for just $19.99!