Introduction
Aerospace engineering is a dynamic field dedicated to the design, development, and maintenance of aircraft and spacecraft.
This discipline encompasses a wide range of technologies and processes, from aerodynamics and propulsion systems to materials science and structural analysis.
As the aerospace industry continues to evolve, advancements in technology play a crucial role in driving innovation and improving performance.
Among the transformative technologies making a significant impact on aerospace engineering is 3D printing, also known as additive manufacturing.
3D printing involves creating three-dimensional objects layer by layer from digital models, allowing for precise control over the shape and properties of the materials used.
This technology has revolutionized various industries by enabling rapid prototyping, reducing production costs, and allowing for the creation of complex geometries that were previously impossible to achieve with traditional manufacturing methods.
In aerospace engineering, 3D printing is particularly revolutionary.
It offers the ability to produce lightweight, high-strength components with intricate designs, which can lead to substantial improvements in fuel efficiency and overall performance.
History of Aerospace Engineering
Aerospace engineering, the field dedicated to the design and development of aircraft and spacecraft, has a rich history marked by groundbreaking milestones and technological advancements.
Origins and Development
The origins of aerospace engineering can be traced back to the early 20th century, when pioneers like the Wright brothers made their historic first powered flight in 1903.
This achievement laid the foundation for modern aviation and sparked an era of rapid technological development.
The subsequent decades saw significant progress in aerodynamics, materials science, and propulsion systems, driven by the demands of both military and civilian aviation.
Key Milestones
Several key milestones have shaped the evolution of aerospace engineering:
- The Wright Brothers’ First Flight (1903): Orville and Wilbur Wright achieved the first controlled, powered flight, demonstrating the feasibility of human flight and setting the stage for future innovations.
- World War I and II Advances: The world wars spurred rapid advancements in aircraft design, including improvements in speed, range, and firepower. The development of jet engines and radar systems during this period revolutionized aviation.
- The Jet Age (1950s): The introduction of jet engines led to a new era of commercial aviation, characterized by faster and more efficient passenger aircraft. The Boeing 707, introduced in 1958, marked the beginning of the modern jet age.
- The Space Race (1960s): The competition between the United States and the Soviet Union to achieve space exploration milestones drove significant advancements in spacecraft design, culminating in the Apollo moon landings.
- The Space Shuttle Era (1981-2011): NASA’s Space Shuttle program facilitated reusable spacecraft technology, allowing for numerous missions to deploy satellites, conduct scientific research, and assemble the International Space Station (ISS).
Transition to Digital Technologies
In recent decades, aerospace engineering has undergone a transformative shift with the integration of digital technologies.
Computer-aided design (CAD) and simulation tools have revolutionized the design process, allowing engineers to create and test complex models with unprecedented accuracy.
Advanced materials and manufacturing techniques, such as 3D printing, have further enhanced the capabilities of aerospace engineers, enabling the creation of lightweight, high-strength components and facilitating rapid prototyping and production.
The advent of digital technologies has also improved data analysis and decision-making processes, leading to more efficient and reliable designs.
The integration of artificial intelligence and machine learning is beginning to play a role in optimizing flight systems and autonomous spacecraft operations, signaling the continued evolution of the field.
Therefore, the history of aerospace engineering is marked by pioneering achievements and continuous technological advancements.
From the Wright brothers’ first flight to the integration of digital technologies, each milestone has contributed to the evolution of modern aviation and space exploration, shaping the field into what it is today.
Evolution of 3D Printing Technology
Introduction to 3D Printing Technology and Its Applications
3D printing, also known as additive manufacturing, creates objects by layering materials.
This innovative technology builds three-dimensional objects from digital models.
Engineers design these models using computer-aided design (CAD) software, ensuring precision and customization.
3D printing uses materials such as plastics, metals, ceramics, and composites.
It offers unparalleled flexibility in creating complex shapes and structures.
Initially, 3D printing found use in rapid prototyping, but its applications have since expanded.
Today, industries utilize 3D printing for end-use production, spare parts, and tooling.
It revolutionizes the manufacturing landscape by offering versatility and efficiency.
Advantages of 3D Printing in Manufacturing Processes
3D printing presents several advantages over traditional manufacturing methods.
One significant benefit is the reduction of material waste.
Traditional processes often involve cutting away material, which results in waste.
In contrast, 3D printing adds material only where needed, minimizing waste.
This efficiency not only saves resources but also reduces costs.
Additionally, 3D printing enables rapid prototyping and iterative design.
Engineers can quickly produce and test multiple design versions, accelerating development cycles.
This speed allows for faster innovation and reduces time-to-market for new products.
Customization is another key advantage of 3D printing.
Traditional manufacturing processes often require expensive molds and tooling, making customization costly.
With 3D printing, customization is both simple and cost-effective.
Manufacturers can produce unique or limited-edition products without significant additional costs.
This capability is especially beneficial for industries requiring tailored solutions, such as healthcare and aerospace.
Various Industries Utilizing 3D Printing for Production
Several industries have embraced 3D printing for its numerous benefits.
In aerospace, 3D printing allows for the creation of lightweight, complex components.
These components often reduce the overall weight of aircraft, improving fuel efficiency and performance.
Aerospace companies use 3D printing to produce parts like engine components, brackets, and ducting.
These parts meet stringent safety and performance standards, proving the reliability of 3D-printed components in critical applications.
The healthcare industry also leverages 3D printing for customized medical solutions.
Surgeons use 3D-printed models to plan complex surgeries, improving outcomes.
Prosthetics and implants are tailored to individual patients, ensuring better fit and function.
Additionally, bioprinting, a subset of 3D printing, holds promise for creating tissue and organ structures.
In the automotive industry, 3D printing streamlines the production of prototypes and end-use parts.
It allows for the rapid iteration of designs, leading to better-performing vehicles.
Customization options also enable manufacturers to offer personalized vehicles and components.
The consumer goods sector benefits from 3D printing’s ability to produce unique and customized products.
Companies can quickly adapt to changing consumer demands, offering personalized solutions.
Additionally, 3D printing supports sustainable manufacturing practices by reducing material waste and energy consumption.
In review, 3D printing technology offers transformative benefits across various industries.
Its applications in aerospace, healthcare, automotive, and consumer goods demonstrate its versatility and efficiency.
As the technology advances, its impact on manufacturing processes will continue to grow, driving innovation and customization. produced, and delivered.
Read: Iconic US Buildings and the Architects Behind Them.
Integration of 3D Printing in Aerospace Engineering
How Aerospace Engineers Are Incorporating 3D Printing into Their Designs
Aerospace engineers increasingly use 3D printing to innovate and streamline aircraft design.
This technology enables the creation of complex geometries that traditional methods can’t achieve.
Engineers design parts with CAD software, optimizing them for performance and weight reduction.
3D printing then brings these designs to life with precision and speed.
Engineers can produce prototypes quickly, allowing for rapid iteration and testing.
This iterative process leads to improved designs and faster development cycles.
Additionally, 3D printing supports the creation of customized parts for specific aircraft models.
Engineers can tailor components to meet unique requirements, enhancing aircraft performance and efficiency.
Benefits of Using 3D Printing Technology in Aircraft Manufacturing
3D printing offers significant benefits in aircraft manufacturing.
One key advantage is weight reduction.
By creating lightweight components, 3D printing helps improve fuel efficiency and reduce emissions.
This weight reduction also enhances aircraft performance and increases payload capacity.
Another benefit is the reduction of material waste.
Traditional manufacturing methods often involve cutting away material, leading to waste.
In contrast, 3D printing adds material only where needed, minimizing waste and reducing costs.
Moreover, 3D printing allows for the consolidation of multiple parts into a single component.
This consolidation reduces the number of joints and fasteners, enhancing structural integrity and reliability.
It also simplifies assembly processes, leading to faster production times and lower labor costs.
3D printing enables on-demand production of spare parts, reducing inventory costs and downtime.
Airlines can print replacement parts as needed, ensuring timely maintenance and repairs.
This capability is particularly valuable for remote or challenging locations where traditional supply chains are limited.
Case Studies of Successful Implementation of 3D Printing in Aerospace Engineering
Several aerospace companies have successfully implemented 3D printing in their operations.
One notable example is GE Aviation.
They use 3D printing to produce fuel nozzles for their LEAP jet engines.
These 3D-printed nozzles are five times more durable and lighter than traditionally manufactured ones.
The consolidation of parts into a single nozzle also reduces assembly time and costs.
Another case study involves Airbus. They have incorporated 3D-printed components into their A350 XWB aircraft.
These components include brackets, ducts, and cabin partitions, contributing to the aircraft’s weight reduction and fuel efficiency.
Airbus also uses 3D printing for rapid prototyping and tooling, accelerating their development processes.
Transform Your Career Today
Unlock a personalized career strategy that drives real results. Get tailored advice and a roadmap designed just for you.
Start NowNASA has also embraced 3D printing for space exploration.
They have used 3D printing to create rocket engine components, reducing manufacturing time and costs.
NASA’s engineers have also tested 3D-printed parts in space, demonstrating their durability and reliability in extreme conditions.
In general, 3D printing technology offers transformative benefits for aerospace engineering.
Engineers leverage this technology to create innovative designs, reduce weight, and minimize waste.
Successful case studies from GE Aviation, Airbus, and NASA highlight the practical applications and advantages of 3D printing.
As the technology continues to advance, its impact on aerospace engineering will only grow, driving further innovation and efficiency.
NASA, Boeing, Airbus, GE Aviation, and Lockheed Martin highlight the technology‘s potential to enhance innovation and efficiency in aerospace manufacturing.
Read: How US Architects Adapt to Climate Change Concerns
Advancements in Materials for 3D Printing in Aerospace
Overview of Materials Used in 3D Printing for Aerospace Applications
Aerospace engineers utilize a variety of materials for 3D printing to meet stringent industry standards.
Metals, such as titanium and aluminum, are commonly used for their strength and lightweight properties.
Titanium offers excellent corrosion resistance and high strength-to-weight ratio, making it ideal for critical components.
Aluminum, known for its lightness and strength, is used in non-structural parts and prototypes.
In addition to metals, engineers employ high-performance polymers like PEEK (polyether ether ketone).
PEEK is valued for its thermal stability, chemical resistance, and mechanical properties.
Composite materials, combining metals and polymers, also play a crucial role.
They offer a balance of strength, weight, and durability, essential for aerospace applications.
Development of New Materials Specifically Tailored for Aerospace Engineering
Researchers continuously develop new materials tailored for aerospace 3D printing.
These materials address specific industry challenges such as weight reduction and high-temperature performance.
One significant development is the creation of metal matrix composites (MMCs).
MMCs combine metals with ceramic or carbon fibers, enhancing strength and thermal resistance.
These composites are ideal for engine components that endure extreme temperatures.
Another innovation is the development of functionally graded materials (FGMs).
FGMs have varying compositions and properties throughout their volume, tailored for specific performance requirements.
This gradation allows engineers to design parts with optimized properties in different regions.
High-temperature polymers are also being developed for aerospace 3D printing.
Polymers like PEKK (polyetherketoneketone) can withstand extreme temperatures and harsh chemical environments.
These materials are suitable for applications like engine parts and heat shields.
Additionally, researchers are exploring nanocomposites, which incorporate nanoparticles into polymers or metals.
Nanocomposites offer improved mechanical properties, thermal conductivity, and electrical performance.
They hold promise for creating lighter and stronger components, enhancing overall aircraft performance.
Impact of Material Innovation on the Performance and Efficiency of Aircraft
Material innovation in 3D printing significantly impacts aircraft performance and efficiency.
Lightweight materials reduce the overall weight of aircraft, leading to improved fuel efficiency.
This reduction in weight also allows for increased payload capacity and longer flight ranges.
High-strength materials enhance the structural integrity of aircraft components, improving safety and reliability.
The use of advanced composites and alloys allows engineers to design parts that withstand extreme conditions without compromising performance.
Materials tailored for high-temperature applications improve engine efficiency.
These materials can endure higher operating temperatures, increasing engine performance and reducing fuel consumption.
The development of corrosion-resistant materials extends the lifespan of components, reducing maintenance costs and downtime.
Additionally, the ability to create complex geometries with optimized materials enhances aerodynamic performance.
Engineers can design parts that minimize drag and improve fuel efficiency.
The customization of material properties through 3D printing enables the production of parts with specific performance characteristics.
This customization leads to more efficient and optimized aircraft designs.
As new materials are developed, the potential for further improvements in aircraft performance and efficiency grows.
Material innovation in 3D printing continues to drive advancements in aerospace engineering, contributing to safer, more efficient, and more sustainable aviation.
Read: The Intersection: Architecture & Tech in Modern USA.
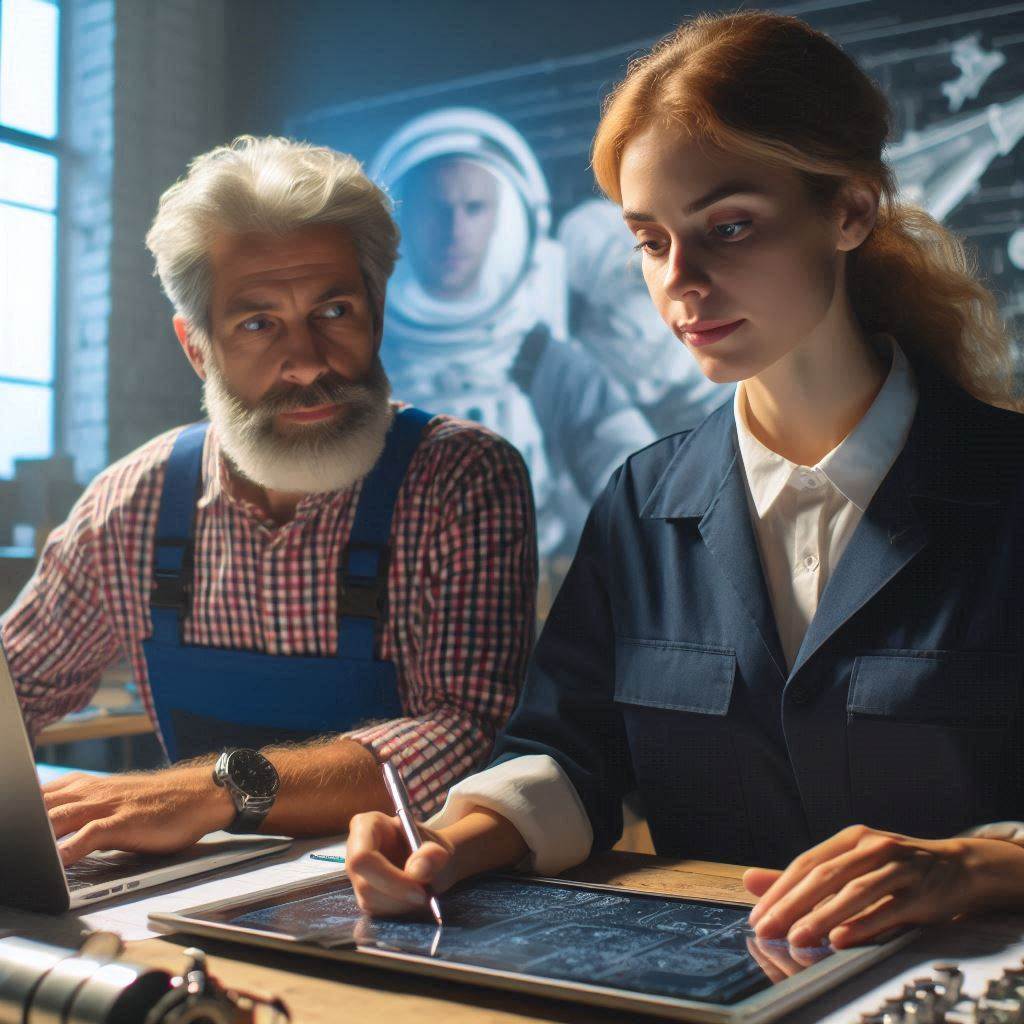
Challenges and Limitations of 3D Printing in Aerospace Engineering
Obstacles Faced in Implementing 3D Printing Technology in Aerospace
Implementing 3D printing technology in aerospace presents several challenges.
One major obstacle is the high cost of equipment and materials.
3D printers capable of producing aerospace-grade parts are expensive, limiting widespread adoption.
Additionally, the materials used, such as high-performance metals and polymers, can be costly.
Engineers also face difficulties in ensuring the consistency and reliability of 3D-printed parts.
Traditional manufacturing methods have well-established quality control processes, but 3D printing lacks standardized protocols.
Variations in printing conditions can lead to inconsistencies in material properties and part performance.
The complexity of aerospace components further complicates the printing process, requiring precise control and expertise.
Regulatory Hurdles and Quality Control Concerns in Aircraft Production
Regulatory hurdles significantly impact the adoption of 3D printing in aerospace.
Aviation authorities, such as the FAA and EASA, have strict standards for aircraft components.
These standards ensure the safety and reliability of parts used in flight.
However, the regulatory framework for 3D-printed parts is still evolving.
Manufacturers must demonstrate that 3D-printed parts meet or exceed traditional manufacturing standards.
This process involves extensive testing and validation, which can be time-consuming and costly.
Quality control remains a critical concern.
Ensuring that each 3D-printed part meets stringent aerospace requirements is challenging.
Variations in printer performance, material quality, and environmental conditions can affect the final product.
Implementing robust quality control measures is essential to detect and correct defects.
Non-destructive testing methods, such as X-ray and ultrasound, are often employed to inspect 3D-printed parts.
However, these methods add to the complexity and cost of production.
Establishing standardized testing and validation procedures is crucial to gaining regulatory approval and ensuring safety.
Future Prospects for Overcoming Challenges and Expanding the Use of 3D Printing in Aerospace
The future of 3D printing in aerospace holds promising prospects.
Advances in technology and materials will address many current challenges.
Researchers are developing more affordable 3D printers and materials, making the technology accessible to more manufacturers.
Improved printer reliability and consistency will reduce variations in part quality.
Enhanced quality control methods, such as real-time monitoring and feedback systems, will ensure higher standards.
The regulatory landscape is also evolving.
Aviation authorities are working with industry stakeholders to develop comprehensive guidelines for 3D-printed parts.
These guidelines will streamline the certification process, reducing time and costs.
Collaborative efforts between regulatory bodies and manufacturers will pave the way for broader acceptance of 3D-printed components.
Increased investment in research and development will drive innovation.
Partnerships between aerospace companies, research institutions, and technology providers will accelerate advancements.
These collaborations will lead to new materials, improved printing techniques, and innovative applications.
The ability to print complex geometries and customized parts will open new possibilities for aircraft design and performance.
Ultimately, while challenges exist in implementing 3D printing technology in aerospace, the future looks bright.
Ongoing advancements in technology, materials, and regulatory frameworks will overcome current obstacles.
As these challenges are addressed, the use of 3D printing in aerospace will expand, driving innovation and efficiency.
The potential for safer, lighter, and more efficient aircraft will continue to grow, transforming the future of aviation.
Read: Economic Indicators and Their Influence on US Architects
Learn More: Salary Insights for Environmental Technicians in 2024
Collaborative Efforts in Advancing Aerospace Engineering with 3D Printing
Partnerships between aerospace companies and 3D printing technology providers
Partnerships between aerospace companies and 3D printing technology providers have been pivotal in revolutionizing the aerospace industry.
By combining the expertise of aerospace engineers with the cutting-edge technology of 3D printing, these collaborations have led to significant advancements in aircraft design and production.
Transform Your Career Today
Unlock a personalized career strategy that drives real results. Get tailored advice and a roadmap designed just for you.
Start NowCollaborative Research Projects
Collaborative research projects between aerospace companies and 3D printing technology providers have been instrumental in pushing the boundaries of innovation in the aerospace industry.
These research projects are typically aimed at enhancing aircraft design, prototyping, and production processes.
Enhancing Aircraft Design and Production
One of the primary goals of collaborative efforts in aerospace engineering and 3D printing is to enhance aircraft design and production processes.
By leveraging the capabilities of 3D printing technology, aerospace engineers can create complex geometries and lightweight structures that were previously not possible with traditional manufacturing methods.
Furthermore, the use of 3D printing in aerospace engineering allows for the rapid prototyping of components and parts, reducing lead times and overall costs associated with aircraft development.
This iterative design process enables engineers to test and optimize their designs quickly, leading to more efficient and reliable aircraft systems.
Successful Collaborations and Groundbreaking Innovations
There are several examples of successful collaborations between aerospace companies and 3D printing technology providers that have resulted in groundbreaking innovations in the aerospace industry.
One such example is the partnership between Airbus and Materialise, a leading 3D printing company.
Together, Airbus and Materialise have developed novel 3D printing techniques that have been used to produce lightweight, high-performance aircraft components.
By harnessing the design freedom offered by 3D printing, Airbus has been able to optimize the weight and performance of its aircraft, leading to significant fuel savings and reduced environmental impact.
Another notable collaboration is between Boeing and Norsk Titanium, a pioneer in additive manufacturing technology.
Boeing has worked closely with Norsk Titanium to develop 3D printed structural components for its commercial aircraft, such as the Boeing 787 Dreamliner.
By using 3D printing technology to produce titanium components, Boeing has been able to reduce the weight of its aircraft and improve fuel efficiency.
This collaboration has demonstrated the potential of 3D printing in revolutionizing aircraft manufacturing processes and setting new standards for the aerospace industry.
Collaborative efforts between aerospace companies and 3D printing technology providers have played a significant role in advancing aerospace engineering and redefining aircraft design and production processes.
These partnerships have led to groundbreaking innovations that have the potential to reshape the future of the aerospace industry.
By leveraging the capabilities of 3D printing technology, aerospace engineers can continue to push the boundaries of what is possible in aircraft design and manufacturing.
As these collaborative efforts continue to evolve, we can expect to see even more exciting developments that will further enhance the performance, efficiency, and sustainability of aircraft systems.
Conclusion
3D printing technology has significantly transformed aerospace engineering, providing new possibilities for design, manufacturing, and production.
By enabling the rapid prototyping of complex components, reducing material waste, and allowing for the customization of parts, 3D printing has revolutionized how aerospace engineers approach problem-solving and innovation.
The integration of advanced materials and cutting-edge printing technologies has led to the creation of lighter, stronger, and more efficient aircraft components, enhancing overall performance and fuel efficiency.
The potential for further advancements in the field of aerospace engineering through 3D printing is vast.
Ongoing research and development efforts are likely to yield new materials, improved printing techniques, and more efficient manufacturing processes.
These innovations will continue to push the boundaries of what is possible in aerospace design and production, leading to even more significant improvements in aircraft performance, safety, and cost-effectiveness.
By fostering a culture of innovation and collaboration, the aerospace industry can continue to leverage 3D printing technology to achieve new heights in engineering excellence.