Introduction
Achieving accuracy in shipping and receiving is essential for businesses to run smoothly and efficiently.
Inaccuracies can lead to delays, unhappy customers, and financial losses.
When items are shipped or received incorrectly, it can result in wasted time and resources to correct the mistakes.
This can impact the overall efficiency of the operation.
Accuracy in shipping also directly affects customer satisfaction.
Customers expect their orders to arrive on time and in perfect condition.
Any mistakes can lead to frustration and dissatisfaction.
Implementing barcode systems
How barcodes can improve accuracy in tracking shipments
Barcodes use a series of black and white lines to represent data which helps in identifying packages accurately.
Benefits of using barcode technology in shipping and receiving processes
- Improved Accuracy: Barcodes reduce human error in tracking and receiving shipments.
- Time Efficiency: Scanning barcodes is quicker than manual data entry, speeding up the process.
- Real-time Tracking: Barcodes allow for real-time tracking of shipments, providing visibility.
- Inventory Management: Barcodes help in maintaining accurate inventory counts, reducing stockouts.
- Cost Savings: By reducing errors and streamlining processes, barcodes help in saving costs.
Read: Shipping and Receiving Clerk Job Outlook for 2024
Regular training for staff
Benefits of Regular Training for Staff
Training your staff on the proper procedures for shipping and receiving is essential for the smooth operation of your business.
By educating employees on the best practices, you are ensuring that they understand the importance of accuracy in handling shipments.
This knowledge will help them perform their job more efficiently and reduce errors that can lead to costly mistakes.
Increased Accuracy
Regular training can help improve accuracy in shipping and receiving by providing employees with the knowledge they need to perform their tasks correctly.
When staff members are aware of the proper procedures, they are less likely to make mistakes that can result in lost or damaged shipments.
This increased accuracy benefits both the company and the customer, as it ensures that products are delivered on time and in good condition.
Reduced Errors
Training can also help reduce errors in shipping and receiving.
When employees are properly educated on the procedures, they are less likely to make mistakes such as mislabeling packages or sending the wrong items to customers.
By reducing errors, businesses can save time and money that would otherwise be spent correcting mistakes and dealing with customer complaints.
Steps to Implement Regular Training
In order to implement regular training for staff, businesses can take the following steps:
Develop Training Materials
Create training materials that outline the proper procedures for shipping and receiving.
Transform Your Career Today
Unlock a personalized career strategy that drives real results. Get tailored advice and a roadmap designed just for you.
Start NowThis can include written manuals, online resources, or in-person training sessions.
Make sure that the materials are easily accessible to all employees and update them regularly to reflect any changes in procedures.
Schedule Training Sessions
Set aside time for regular training sessions with employees.
This can be done on a monthly, quarterly, or annual basis, depending on the needs of your business.
Make sure that all staff members are required to attend the training sessions and provide opportunities for questions and feedback.
Monitor Performance
After training sessions have been completed, monitor the performance of employees to ensure that they are applying the knowledge they have gained.
This can be done through regular performance evaluations, customer feedback, or spot-checks of shipments.
Provide feedback and additional training as needed to address any issues that arise.
Regular training for staff on proper procedures for shipping and receiving is essential for improving accuracy and reducing errors in handling shipments.
By educating employees on the best practices, businesses can ensure that products are delivered on time and in good condition, benefiting both the company and the customer.
Read: Top Colleges for Transportation Engineering Degrees
Quality control checks
The necessity of implementing quality control measures in shipping and receiving
Implementing quality control measures in shipping and receiving is crucial for ensuring accuracy in operations.
Without proper checks in place, errors and discrepancies can occur, leading to delays, loss of revenue, and customer dissatisfaction.
Types of checks that can be conducted to ensure accuracy in shipments
- Double-checking quantities: One common type of quality control check is to verify that the correct quantity of items is being shipped and received.
This can involve physically counting the items or using scanning technology to ensure accuracy. - Inspecting for damage: Another important check is to inspect items for any signs of damage before shipping them out or accepting deliveries.
This helps prevent sending out defective products and receiving damaged goods. - Matching orders with invoices: It is essential to cross-reference orders with invoices to confirm that the correct items are being shipped and received.
This helps avoid mix-ups and billing errors. - Testing product functionality: In some cases, especially with technical or specialized products, it may be necessary to conduct tests to verify that the items are functioning correctly before shipping them out.
- Tracking shipments: Implementing a tracking system for shipments can help monitor the progress of deliveries and identify any potential issues or delays along the way.
This allows for quick intervention and resolution.
By incorporating these quality control checks into your shipping and receiving processes, you can minimize errors, improve accuracy, and enhance overall efficiency in your operations.
Investing time and resources in quality control measures ultimately leads to cost savings and customer satisfaction.
Read: Key Responsibilities of Shipping and Receiving Clerks
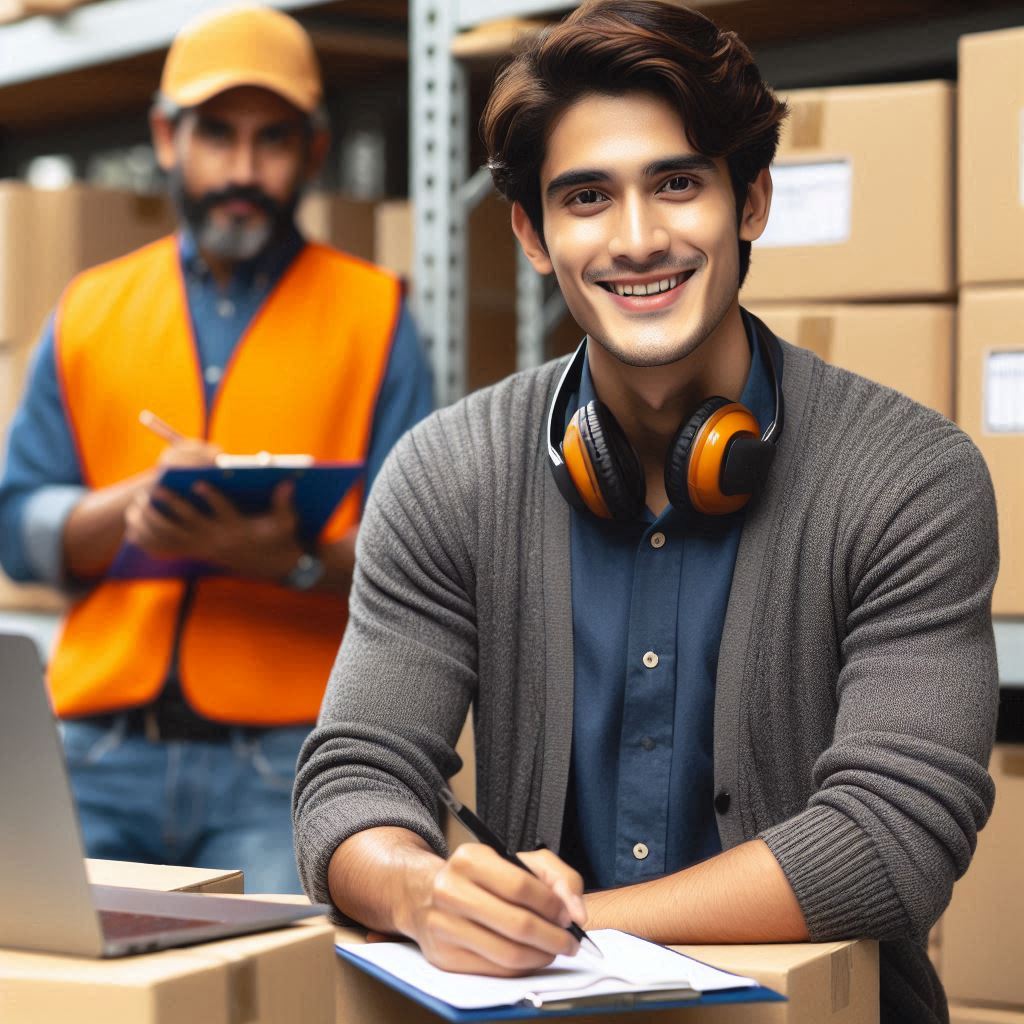
Utilizing automated systems
Automated systems play a crucial role in improving accuracy in shipping and receiving processes.
These systems offer several advantages that help streamline operations and reduce errors.
Advantages of using automated systems for tracking and managing shipments
- Increased efficiency: Automated systems can process data much faster than manual methods, reducing the time taken to track and manage shipments.
- Improved accuracy: With automated systems in place, the margin of error is significantly minimized, leading to more precise tracking and management of shipments.
- Real-time visibility: Automated systems provide real-time updates on the status of shipments, allowing for better monitoring and decision-making.
- Cost savings: By reducing errors and increasing efficiency, automated systems can help cut down on operational costs associated with shipping and receiving.
Examples of software and technology that can help improve accuracy in shipping and receiving processes
- Warehouse Management Systems (WMS): WMS software helps businesses manage and track inventory levels, order picking, packing, and shipping.
- Transportation Management Systems (TMS): TMS software optimizes the movement of goods from one location to another, ensuring timely and accurate deliveries.
- Barcode scanning technology: Barcode scanners enable quick and accurate identification of products, reducing the risk of errors in shipping and receiving.
- RFID technology: RFID tags allow for automated data capture and tracking of shipments in real-time, improving visibility and accuracy.
In short, incorporating automated systems and technologies into shipping and receiving operations is essential for enhancing accuracy, efficiency, and cost-effectiveness.
By leveraging these tools, businesses can optimize their processes, minimize errors, and deliver exceptional service to customers.
Transform Your Career Today
Unlock a personalized career strategy that drives real results. Get tailored advice and a roadmap designed just for you.
Start NowRead: Interview Tips for Shipping and Receiving Clerk Jobs
Cross-referencing orders
Why is it Important to Cross-reference Orders?
Ensuring accuracy in shipping and receiving is crucial for the success of any business.
One of the key ways to achieve this is by cross-referencing orders before they are shipped out to customers.
This process involves double-checking the details of each order against the actual items being packed for shipping.
By doing so, errors can be minimized, and customers can receive the correct items they ordered.
The Benefits of Double-checking Orders
Double-checking orders before they are shipped out offers a range of benefits, including:
- Reducing the likelihood of shipping the wrong items to customers
- Minimizing the chances of sending defective or damaged products
- Enhancing customer satisfaction by ensuring orders are accurate and complete
How Cross-referencing Prevents Errors
By cross-referencing orders, businesses can identify discrepancies between the order details and the actual items being prepared for shipping.
This process helps in:
- Verifying the accuracy of product descriptions, quantities, and pricing
- Checking for any special instructions or customized requests from customers
- Matching the order with the correct shipping address and delivery method
Ensuring Correct Items are Sent to Customers
When orders are cross-referenced, businesses can be confident that the correct items are being sent to customers.
This helps in:
- Avoiding costly returns or exchanges due to shipping errors
- Building trust and loyalty with customers by delivering on their expectations
- Reducing the need for customer service interventions related to order inaccuracies
Best Practices for Cross-referencing Orders
To maximize the effectiveness of cross-referencing orders, businesses should consider implementing the following best practices:
- Use a barcode scanning system to match items with the corresponding order details
- Implement a quality control process to spot-check orders before they are shipped
- Train staff on the importance of accuracy in shipping and receiving procedures
- Utilize software or technology solutions that streamline order processing and tracking
Cross-referencing orders is a critical step in improving accuracy in shipping and receiving.
By double-checking orders before they are shipped out, businesses can prevent errors, ensure the correct items are sent to customers, and ultimately enhance customer satisfaction.
Clear communication with suppliers
When it comes to improving accuracy in shipping and receiving, one crucial factor that cannot be overlooked is clear communication with suppliers.
Successful supply chain operations depend on effective communication with suppliers.
Clear communication ensures accurate and timely order fulfillment.
Strong relationships with suppliers enhance collaboration and efficiency.
When teams share information, they reduce errors and delays.
Consistent updates help maintain order accuracy and delivery schedules.
Building trust with suppliers leads to smoother operations overall.
Transform Your Career Today
Unlock a personalized career strategy that drives real results. Get tailored advice and a roadmap designed just for you.
Start NowThe need for open communication
It is essential to emphasize the need for open communication with suppliers from the very beginning of the relationship.
By fostering a culture of transparency and open dialogue, you can minimize the chances of misunderstandings or miscommunications that could lead to errors in shipping and receiving.
Make sure that your suppliers understand the importance of accurate order fulfillment and the role that clear communication plays in achieving this goal.
Ways to establish effective communication channels
- One way to establish effective communication channels with suppliers is to set clear expectations from the start.
- Provide suppliers with detailed order specifications, delivery schedules, and any other relevant information that will help them fulfill orders accurately.
- Utilize technology to streamline communication processes, such as implementing a cloud-based platform for sharing real-time updates and data with suppliers.
- Regularly check in with suppliers to address any concerns or issues that may arise, and encourage them to communicate proactively if they encounter any challenges.
- Consider organizing periodic meetings or conference calls with key suppliers to discuss performance metrics, identify areas for improvement, and strengthen the partnership.
By prioritizing clear communication with suppliers and establishing effective channels for sharing information, you can enhance the accuracy of shipping and receiving processes and build stronger relationships with your supply chain partners.
Conclusion
Accurate shipping and receiving processes are vital for any business.
They ensure timely deliveries and maintain customer satisfaction.
Inaccuracies can lead to delays, increased costs, and damaged reputations.
Therefore, businesses must prioritize accuracy throughout their operations.
Implementing effective strategies can significantly enhance accuracy.
Utilizing technology, such as barcode scanners and inventory management software, streamlines tracking and minimizes errors.
Regular training for employees is essential.
Educated staff can better understand procedures and handle discrepancies efficiently.
Additionally, establishing clear communication channels within the team fosters collaboration and prevents misunderstandings.
Conducting regular audits of shipping and receiving processes can identify potential issues.
These audits reveal patterns that may lead to errors, allowing teams to address them proactively.
Using checklists during shipping helps ensure accuracy at every step.
They guide workers through the entire process.
Each item on the list promotes thorough completion of tasks.
Checklists reduce the risk of missing important details.
Implementing them streamlines the shipping workflow effectively.
Transform Your Career Today
Unlock a personalized career strategy that drives real results. Get tailored advice and a roadmap designed just for you.
Start NowThis approach minimizes the risk of mistakes slipping through the cracks.
Encourage a culture of accountability within the organization.
When employees take ownership of their roles, they become more committed to accuracy.
Share success stories that highlight improvements in accuracy to motivate teams.
Recognizing achievements can boost morale and drive continuous improvement.
Enhancing accuracy in shipping and receiving processes is crucial for operational success.
By implementing the outlined strategies, businesses can improve efficiency and customer satisfaction.
Strive for excellence in every shipment and delivery.
Your commitment to accuracy will pay off in the long run.