Introduction
Overview of Industrial Machinery Maintenance
Industrial machinery maintenance is essential for ensuring the reliable operation and longevity of equipment.
It encompasses regular inspections, preventive measures, and repairs to avoid unexpected failures.
Maintenance strategies include routine checks, lubrication, adjustments, and part replacements.
Effective maintenance minimizes downtime, boosts productivity, and extends the lifespan of machinery.
It involves both scheduled maintenance, based on time intervals or usage, and unscheduled maintenance, which addresses unexpected issues as they arise.
Proper maintenance practices are vital for maintaining safety standards and operational efficiency in industrial settings.
Importance of Staying Up-to-Date with Future Trends in Maintenance
Staying updated with future trends in industrial machinery maintenance is crucial for optimizing performance and reducing costs.
Emerging technologies such as the Internet of Things (IoT), artificial intelligence (AI), and predictive analytics are revolutionizing maintenance practices.
IoT enables real-time monitoring of machinery, allowing for early detection of potential issues.
AI and machine learning enhance predictive maintenance by analyzing data to forecast equipment failures.
Adopting these advanced technologies leads to more efficient maintenance, reducing downtime and preventing costly breakdowns.
Keeping pace with these trends ensures that maintenance strategies remain effective and competitive.
It also helps in adapting to new challenges and maintaining a high level of operational reliability and safety.
Embracing future trends is essential for maximizing the benefits of maintenance practices and achieving long-term success in industrial operations.
Increased automation in maintenance
Use of AI and Machine Learning for Predictive Maintenance
The future of industrial machinery maintenance increasingly involves AI and machine learning.
These technologies enable predictive maintenance by analyzing vast amounts of data.
AI algorithms can detect patterns and anomalies that indicate potential issues before they become critical.
Machine learning models learn from historical data to predict when equipment is likely to fail.
This approach allows for timely interventions, reducing unplanned downtime.
By forecasting potential failures, organizations can schedule maintenance more efficiently.
Predictive maintenance powered by AI helps in optimizing repair schedules, extending machinery lifespan, and improving overall reliability.
It shifts the focus from reactive to proactive maintenance strategies, enhancing operational efficiency.
Benefits of Automation in Reducing Downtime and Costs
Automation plays a crucial role in modern industrial maintenance.
Automated systems can perform routine inspections and maintenance tasks with high precision.
This reduces the need for manual intervention and lowers the risk of human error.
Automated monitoring systems continuously track equipment performance, identifying issues early.
This proactive approach helps in addressing potential problems before they escalate.
Automation also streamlines maintenance processes, making them more efficient and cost-effective.
By minimizing unexpected breakdowns, automation reduces downtime and associated costs.
It improves overall productivity and allows maintenance teams to focus on more complex tasks.
Investing in automated systems can lead to significant long-term savings and operational improvements.
Incorporating AI, machine learning, and automation into maintenance strategies marks a shift towards more intelligent and efficient practices.
These technologies provide valuable insights, enhance predictive capabilities, and streamline maintenance operations.
They enable organizations to maintain equipment better, reduce downtime, and manage costs effectively.
Embracing these future trends will lead to more reliable and cost-efficient industrial machinery maintenance.
The integration of advanced technologies ensures that maintenance practices evolve to meet the demands of modern industrial environments.
Adoption of IoT in machinery maintenance
Connecting Machinery to the Internet for Real-Time Monitoring
The future of industrial machinery maintenance is being shaped by the integration of Internet of Things (IoT) technology.
Connecting machinery to the internet allows for real-time monitoring and data collection.
Sensors installed on equipment can continuously track performance metrics, such as temperature, vibration, and pressure.
This data is transmitted to a centralized system where it is analyzed and assessed.
Real-time monitoring helps identify potential issues before they become critical problems.
It enables predictive maintenance, where maintenance actions are performed based on data-driven insights rather than scheduled intervals.
IoT connectivity provides several benefits for industrial operations.
It improves equipment reliability by catching early warning signs of malfunctions.
This proactive approach reduces unexpected breakdowns and minimizes downtime.
It also allows for more accurate scheduling of maintenance tasks, optimizing resource allocation.
Maintenance teams can access data remotely, facilitating quicker response times and more informed decision-making.
Real-time data helps in adjusting operational parameters to enhance performance and efficiency.
It can also lead to better planning and budgeting for maintenance activities.
Improving Efficiency and Effectiveness of Maintenance Processes
Advancements in technology are significantly improving the efficiency and effectiveness of maintenance processes.
Predictive maintenance, driven by IoT data, shifts maintenance from a reactive to a proactive approach.
By analyzing historical and real-time data, maintenance teams can predict when equipment is likely to fail and address issues before they occur.
This method reduces unnecessary maintenance and extends the lifespan of machinery.
Automated maintenance scheduling is another trend transforming the industry.
Software solutions use data analytics to generate optimal maintenance schedules, ensuring that tasks are performed at the right time.
Automation minimizes human error and ensures consistency in maintenance activities.
Additionally, digital twins, which are virtual replicas of physical machines, allow for simulations and scenario testing.
This technology helps in understanding how equipment will perform under various conditions and aids in planning maintenance tasks accordingly.
Artificial Intelligence (AI) is enhancing maintenance practices by analyzing vast amounts of data to identify patterns and anomalies.
AI algorithms can predict potential failures with high accuracy, providing actionable insights for maintenance teams.
Integration of AI with IoT systems allows for smarter decision-making and more efficient use of resources.
Augmented Reality (AR) is also playing a role in maintenance.
AR tools can provide technicians with real-time, hands-on guidance and visual overlays of machinery components.
This technology enhances the accuracy of repairs and reduces training time for new technicians.
Overall, the integration of IoT technology for real-time monitoring and advancements in predictive maintenance, automation, AI, and AR are revolutionizing industrial machinery maintenance.
These trends are making maintenance processes more efficient, effective, and data-driven.
They help in reducing downtime, extending equipment life, and optimizing resource use, ultimately leading to more reliable and cost-effective operations.
Read: Best Online Courses for CAD Technician Training
Use of virtual and augmented reality in training
Simulating Maintenance Scenarios for Hands-On Training
Simulating maintenance scenarios offers significant benefits for hands-on training.
Virtual reality (VR) and augmented reality (AR) technologies create immersive environments.
These simulations provide realistic experiences without the risks associated with real-world scenarios.
Trainees can interact with virtual machinery, performing tasks and troubleshooting issues in a controlled setting.
Simulation-based training helps mechanics practice complex procedures and learn from mistakes in a risk-free environment.
This approach enhances their problem-solving skills and technical knowledge.
Mechanics can gain experience with various machinery types and faults, improving their readiness for real-world challenges.
Moreover, simulations can be customized to replicate specific equipment or operational conditions.
This customization ensures that training is relevant and tailored to the needs of the organization.
By integrating simulation into training programs, organizations can better prepare their maintenance teams for the demands of modern machinery.
Enhancing Safety and Skill Development for Maintenance Professionals
Enhancing safety and skill development is a top priority for future maintenance practices.
Advances in training methods contribute to both aspects.
For example, simulation training reduces the risk of accidents during hands-on practice.
Mechanics can familiarize themselves with safety protocols and emergency procedures in a virtual setting before applying them in real scenarios.
Additionally, ongoing professional development is essential for maintaining high skill levels.
Online courses, workshops, and certifications offer opportunities for mechanics to stay current with industry advancements.
These educational resources cover new technologies, techniques, and best practices, ensuring that maintenance professionals are well-equipped to handle evolving machinery.
Safety training programs must address emerging risks and integrate the latest safety standards.
Mechanics should receive regular updates on safety protocols, equipment handling, and risk management.
By focusing on safety and skill development, organizations can minimize workplace accidents and enhance overall maintenance effectiveness.
Employers can also support skill development through mentorship and peer learning.
Experienced mechanics can provide guidance and share knowledge with less experienced colleagues.
This collaborative approach fosters a culture of continuous learning and improvement within the maintenance team.
Lastly, the future of industrial machinery maintenance is marked by advancements in simulation training and a strong emphasis on safety and skill development.
Simulating maintenance scenarios provides valuable hands-on experience, preparing mechanics for real-world challenges.
Enhancing safety practices and ongoing professional development further support effective maintenance operations.
By embracing these trends, organizations can improve their maintenance strategies and ensure a skilled, safety-conscious workforce.
The integration of these approaches will drive the evolution of maintenance practices and contribute to the overall success of industrial operations.
Read: Quality Control Inspector: Technical Skills Needed
Shift towards sustainable maintenance practices
Implementing Green Technologies for Machinery Maintenance
The future of industrial machinery maintenance is increasingly focused on integrating green technologies.
Green technologies aim to reduce the environmental impact of industrial operations.
They emphasize energy efficiency and the use of sustainable materials.
Energy-efficient machinery uses less power, reducing the carbon footprint of operations.
Implementing renewable energy sources, such as solar or wind, can further decrease reliance on fossil fuels.
Eco-friendly lubricants and coolants minimize harmful emissions and are less toxic.
These substances help in reducing pollution while maintaining machinery performance.
Predictive maintenance technologies play a crucial role in minimizing waste.
By monitoring machinery conditions in real-time, they predict failures before they occur.
This approach reduces unnecessary repairs and extends the lifespan of machinery.
Smart sensors and IoT (Internet of Things) devices collect data on machinery performance, enabling more accurate predictions.
This data-driven approach helps in scheduling maintenance only when needed, avoiding excessive resource use.
Waste management practices are also evolving.
Implementing recycling programs for parts and materials helps in minimizing waste.
Proper disposal of hazardous materials ensures that they do not pollute the environment.
Workshops are adopting circular economy principles, which focus on reusing and recycling materials rather than disposing of them.
This shift reduces the demand for raw materials and lowers overall environmental impact.
Eco-design principles guide the development of new machinery with sustainability in mind.
Machines are designed to be more energy-efficient and easier to recycle at the end of their lifecycle.
Manufacturers are focusing on designing for disassembly, which simplifies the recycling process and reduces waste.
Training and awareness programs for maintenance personnel are crucial.
Educating staff on green technologies and sustainable practices promotes a culture of environmental responsibility.
Regular workshops and certifications help ensure that maintenance teams are up-to-date with the latest eco-friendly technologies and practices.
Reduce Environmental Impact and Improve Sustainability in Operations
Reducing the environmental impact and improving sustainability in industrial operations are critical goals.
Implementing green technologies significantly contributes to these objectives.
Energy-efficient machinery and renewable energy sources decrease reliance on non-renewable resources.
Eco-friendly lubricants and coolants reduce pollution and are safer for the environment.
Predictive maintenance technologies minimize waste by predicting and preventing failures before they occur.
Recycling programs for parts and materials and circular economy principles further enhance sustainability.
By designing machinery for easier recycling and focusing on reusability, industries can reduce waste and lower material demand.
Training and awareness programs ensure that staff are equipped with knowledge on green practices, promoting a culture of sustainability.
Government incentives and regulations support the adoption of green technologies, making it financially viable for companies.
Cost savings from reduced energy consumption and waste management contribute to both environmental benefits and operational efficiency.
Collaboration with technology providers ensures access to innovative, sustainable solutions tailored to specific needs.
By focusing on these strategies, industries can effectively reduce their environmental impact and enhance sustainability while maintaining operational efficiency and cost-effectiveness.
Read: Quality Control Inspector: Entry-Level Guide
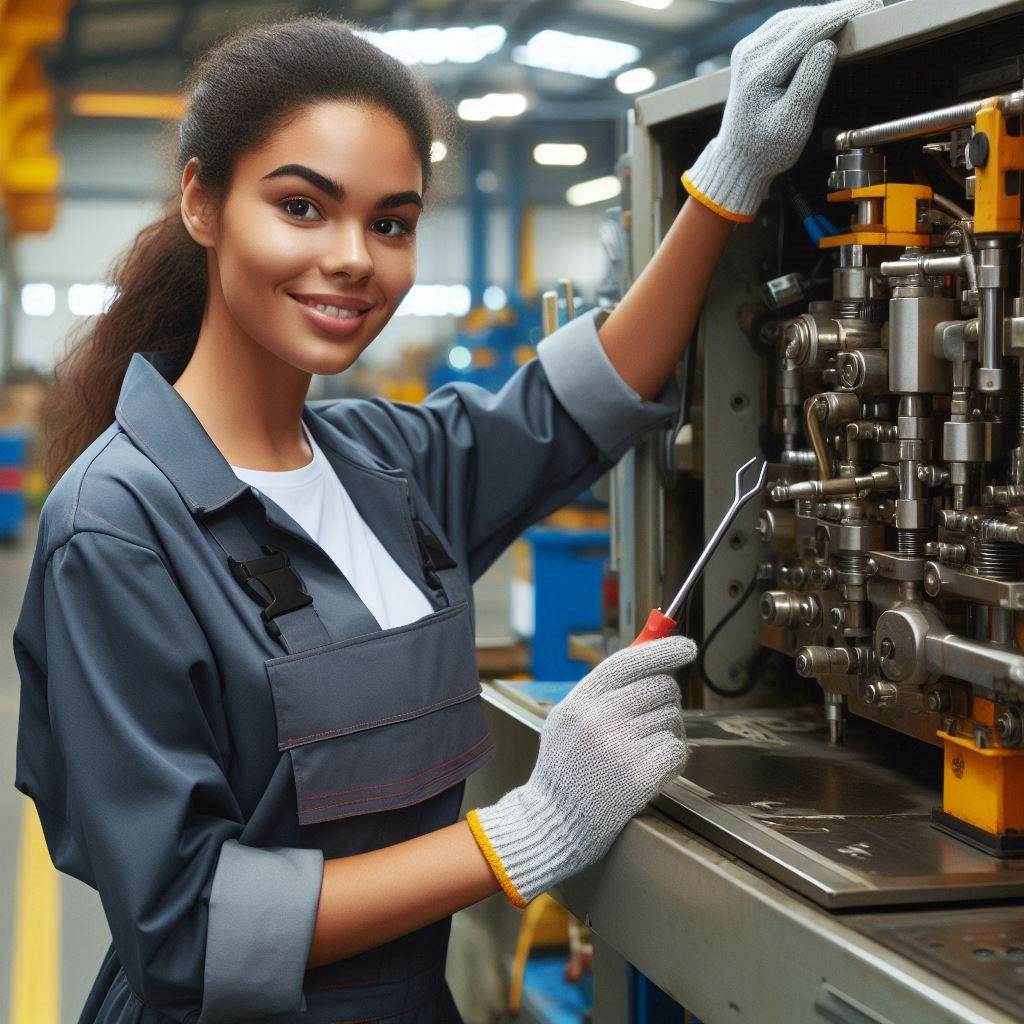
Explore Further: Engineering Technician vs Engineer: Key Differences
Integrated maintenance management systems
Centralized Software for Tracking Maintenance Schedules and Tasks
The future of industrial machinery maintenance is increasingly leaning towards centralized software solutions.
These platforms enable efficient tracking of maintenance schedules and tasks.
Centralized software integrates data from various sources into a single system.
This integration allows for real-time monitoring of equipment status and maintenance needs.
By centralizing maintenance records, organizations can streamline scheduling and ensure timely interventions.
Maintenance teams can access comprehensive equipment histories through these platforms.
This access helps in predicting potential failures and planning preventive measures.
Centralized software also facilitates automated alerts for upcoming maintenance tasks, reducing the risk of oversight.
These systems often feature dashboards that provide a clear overview of all ongoing and upcoming maintenance activities.
Improved visibility into maintenance schedules enhances decision-making and resource allocation.
Streamlining Communication and Organization Within Maintenance Teams
Effective communication and organization within maintenance teams are crucial for successful machinery upkeep.
Centralized software enhances these aspects by offering integrated communication tools.
Maintenance teams can use these tools to collaborate on tasks and share updates in real-time.
This reduces the chances of miscommunication and ensures that everyone is aligned on maintenance priorities.
Streamlined communication aids in rapid response to equipment issues.
When a problem arises, team members can quickly access and review relevant information through the software.
This rapid access enables them to make informed decisions and act swiftly.
Additionally, centralized systems often allow for documentation of all communications and decisions.
This documentation provides a clear record of actions taken and facilitates better coordination among team members.
The software can also support task management by assigning responsibilities and tracking progress.
Maintenance teams can set deadlines, monitor task completion, and ensure accountability through these systems.
Enhanced organization helps in optimizing workflows and improving overall efficiency.
Maintenance personnel can focus on high-priority tasks without getting bogged down by administrative issues.
Integration of Advanced Technologies
Centralized software systems are increasingly integrating advanced technologies like artificial intelligence (AI) and machine learning.
These technologies enhance predictive maintenance capabilities by analyzing historical data to forecast potential failures.
AI algorithms can identify patterns and anomalies that might indicate future issues, allowing for more accurate scheduling of maintenance tasks.
Furthermore, integration with the Internet of Things (IoT) devices provides real-time data on equipment performance.
IoT sensors can continuously monitor machinery and feed data into centralized software.
This data helps in detecting issues early and fine-tuning maintenance schedules based on actual equipment conditions.
Centralized software for tracking maintenance schedules and tasks is revolutionizing industrial machinery maintenance.
It enhances communication and organization within maintenance teams while integrating advanced technologies for predictive maintenance.
By adopting these future trends, organizations can improve efficiency, reduce downtime, and ensure the longevity of their machinery.
Embracing these innovations positions maintenance teams for success in an increasingly complex industrial environment.
Read: Continuing Education for Radiologic Technologists
Learn More: IT Support Specialist: Hands-on Training Programs
Emphasis on cybersecurity for machinery maintenance
Protecting Sensitive Data and Machinery from Cyber Threats
As industrial machinery evolves, so does the threat of cyber attacks.
Protecting sensitive data and machinery is crucial.
Modern machinery often integrates with digital systems, making them vulnerable to cyber threats.
Hackers can exploit vulnerabilities to disrupt operations or steal critical information.
Securing these systems requires robust cybersecurity measures.
Implementing firewalls, encryption, and intrusion detection systems helps safeguard against unauthorized access.
Regularly updating software and firmware protects against new vulnerabilities.
Training employees to recognize and respond to phishing attempts is essential.
Strong access controls and authentication mechanisms prevent unauthorized users from gaining entry.
Regularly auditing security protocols ensures they remain effective against evolving threats.
Industry-specific standards and compliance requirements also guide effective cybersecurity practices.
Investing in cybersecurity solutions is not optional but necessary to maintain operational integrity.
Transform Your Career Today
Unlock a personalized career strategy that drives real results. Get tailored advice and a roadmap designed just for you.
Start NowImportance of Investing in Cybersecurity to Prevent Costly Disruptions
Investing in cybersecurity prevents costly disruptions and downtime in industrial machinery operations.
Cyber attacks can lead to significant financial losses and operational interruptions.
A successful attack can halt production, damage equipment, and compromise sensitive data.
The financial impact of a security breach extends beyond immediate losses.
It includes costs related to legal fees, regulatory fines, and reputational damage.
Effective cybersecurity measures help mitigate these risks by protecting systems from attacks.
Investing in advanced security technologies and services provides a proactive defense.
Regularly updating and patching systems keeps defenses strong against emerging threats.
Establishing incident response plans ensures quick recovery from attacks.
Effective security also involves continuous monitoring and threat intelligence to stay ahead of potential threats.
By prioritizing cybersecurity investments, organizations protect their assets and maintain operational continuity.
Strategies for Enhancing Cybersecurity in Industrial Machinery
To enhance cybersecurity, adopt a multi-layered defense strategy.
Start with strong network security measures, including firewalls and intrusion prevention systems.
Implement encryption for data at rest and in transit to protect sensitive information.
Use secure authentication methods, such as multi-factor authentication, to restrict access.
Regularly back up critical data and test recovery procedures to ensure data integrity.
Conduct vulnerability assessments and penetration testing to identify and address weaknesses.
Educate employees about cybersecurity best practices and potential threats.
Establish clear protocols for reporting and responding to security incidents.
Collaborate with cybersecurity experts and consultants to stay updated on the latest threats and solutions.
Investing in comprehensive cybersecurity strategies ensures robust protection against evolving cyber threats.
Long-Term Benefits of Investing in Cybersecurity
Investing in cybersecurity yields long-term benefits for industrial machinery operations.
Strong cybersecurity measures enhance operational resilience and stability.
They reduce the risk of financial losses and regulatory penalties associated with data breaches.
Proactive security investments build customer trust and confidence in your organization‘s ability to protect their data.
They also ensure compliance with industry regulations and standards, avoiding legal complications.
A secure infrastructure supports uninterrupted operations and protects against costly downtime.
Long-term investments in cybersecurity improve overall efficiency by preventing disruptions and enabling smooth operations.
As cyber threats continue to evolve, maintaining a strong security posture is essential for sustaining business success.
In conclusion, protecting sensitive data and machinery from cyber threats is vital in the future of industrial machinery maintenance.
Investing in robust cybersecurity measures prevents costly disruptions and ensures operational integrity.
By adopting effective strategies and continually enhancing security practices, organizations can safeguard their assets and maintain a secure operational environment.
You Might Also Like: Laboratory Technician Career Pathways
Conclusion
Key future trends in industrial machinery maintenance highlight the shift towards advanced technologies like AI and machine learning, along with increased automation.
AI enables predictive maintenance by analyzing data patterns to foresee potential equipment failures before they occur.
This proactive approach allows for timely repairs, minimizing unplanned downtime and extending the machinery’s lifespan.
Machine learning enhances these predictions by continuously learning from historical data, refining accuracy, and optimizing maintenance schedules.
Automation is another critical trend, automating routine inspections and maintenance tasks.
Automated systems continuously monitor equipment performance, identifying issues early and reducing the need for manual intervention.
This reduces human error, streamlines processes, and cuts maintenance costs.
Businesses should adapt to these trends to ensure long-term success.
Investing in AI, machine learning, and automation will improve operational efficiency, reduce unexpected breakdowns, and lower maintenance costs.
These technologies provide valuable insights, allowing companies to manage equipment better and stay ahead in a competitive market.
Embracing these future trends is essential for maintaining a competitive edge and ensuring efficient, cost-effective industrial machinery maintenance in the evolving landscape.
[E-Books for Sale]
The Big Book of 500 High-Paying Jobs in America: Unlock Your Earning Potential
$19.99 • 500 High-Paying Jobs • 330 pages
Explore 500 high-paying jobs in America and learn how to boost your career, earn more, and achieve success!
See All 500 High-Paying Jobs of this E-Book
1001 Professions Without a Degree: High-Paying American Jobs You Can Start Now
$19.99 • 1001 Professions Without a Degree • 174 pages
Discover 1001 high-paying jobs without a degree! Unlock career tips, skills, and success strategies for just $19.99!