Introduction
Defining Robotics and Job Automation
Robotics involves designing and programming machines to perform tasks traditionally done by humans.
Job automation refers to the process of using these machines to execute repetitive, complex, or dangerous work with little to no human intervention.
As technology advances, robotics and automation are increasingly integrated into various industries, transforming how work is performed.
Impact of Robotics on Employment
The growing use of robotics in job automation has profoundly impacted employment across multiple sectors.
Robots now replace human workers in industries like manufacturing, logistics, and even customer service.
This shift leads to job displacement as machines take over roles that were once manual.
However, the rise of automation also creates new opportunities.
Skilled workers are increasingly needed to design, program, and maintain these robotic systems, leading to a demand for new skill sets in the workforce.
As robotics evolves, workers must adapt by acquiring new skills and transitioning into roles that complement automation.
History of Robotics and Automation
History of Robotics and Automation in the Workforce
The history of robotics and automation in the workforce began with the advent of mechanical systems designed to enhance efficiency.
In the early 20th century, industries adopted automated processes, marking a significant shift in production methods.
The introduction of the assembly line, notably utilized by Henry Ford in automotive manufacturing, revolutionized the industry.
This assembly line system used mechanical devices to streamline production, reducing manual labor and significantly increasing output.
Workers performed repetitive tasks with higher speed and consistency, transforming manufacturing processes and setting the stage for future advancements.
In the 1960s, robotics technology made a substantial leap with the creation of the first industrial robots.
Pioneers like George Devol and Joseph Engelberger developed the Unimate robot, which was first used in General Motors’ factories.
This robot was designed to handle repetitive tasks such as welding and material handling.
It marked a pivotal moment in industrial automation by demonstrating the potential of robots to replace human labor in monotonous and physically demanding tasks.
The success of Unimate set a precedent for further development and integration of robots into various industrial processes.
Evolution and Impact of Robotics Across Industries
In the 1980s and 1990s, robotics technology advanced significantly.
Robots transitioned from simple mechanical systems to complex machines with computers and control systems.
Enhanced sensors and feedback mechanisms enabled robots to perform complex tasks with greater precision.
Technological improvements allowed robots to adapt to various manufacturing processes.
They now handle:
- Assembly
- Inspection
- Material handling
These tasks are executed with increased accuracy and efficiency.
By the early 2000s, robotics technology expanded beyond manufacturing.
Industries like healthcare, logistics, and agriculture began adopting robotic systems.
In healthcare, medical robots, such as surgical assistants and diagnostic tools, emerged.
These robots enhanced surgical precision, improved patient outcomes, and reduced recovery times.
In logistics, robots revolutionized warehouse operations.
Automated systems managed:
- Inventory
- Sorting
- Packaging
These systems reduced labor costs and boosted throughput.
Agriculture also saw the integration of robotics.
Robots assisted with:
- Planting
- Harvesting
- Monitoring crops
This automation increased farming efficiency and productivity.
Today, robotics technology continues to evolve.
Innovations in artificial intelligence (AI) and machine learning drive new robotic capabilities.
Modern robots analyze data, learn from experiences, and improve performance autonomously.
Robotics now integrates into everyday life, from:
- Vacuum cleaners
- Lawn mowers
- Advanced surgical robots
- Personal assistants
This widespread adoption underscores the growing significance of robotics in various societal aspects.
Read: Future of CAD Technician Jobs in Engineering
Advantages of Robotics in the Workplace
Robotics is revolutionizing various industries by enhancing job automation.
The introduction of robotic systems in the workplace brings numerous benefits that significantly boost productivity, efficiency, and accuracy.
Here‘s an in-depth look at how robotics positively impacts job automation and its advantages.
Increased Productivity
Robots are particularly effective at performing repetitive and monotonous tasks.
Unlike humans, they do not experience fatigue or require breaks. This constant performance results in:
- Higher Output: Robots can operate continuously, driving up production rates.
Their ability to work 24/7 ensures a steady flow of output, meeting high-demand periods without compromising performance. - Consistent Quality: By executing tasks with the same precision every time, robots ensure that products meet consistent quality standards.
This uniformity helps in reducing variations and maintaining high-quality output.
In sectors such as automotive manufacturing and electronics, robotics systems are utilized to operate round the clock.
This capability not only increases the overall productivity of operations but also allows companies to meet tight deadlines and fulfill large orders efficiently.
Transform Your Career Today
Unlock a personalized career strategy that drives real results. Get tailored advice and a roadmap designed just for you.
Start NowEnhanced Efficiency
Robotics optimizes operational workflows by automating tasks that would otherwise require manual intervention.
The efficiency benefits of robotics include:
- Streamlined Operations: Robots are designed to handle complex and repetitive sequences with minimal human oversight.
This automation reduces the need for manual handling and intervention, streamlining production processes. - Reduced Downtime: Robotics systems are highly reliable and less prone to errors compared to human labor.
This reliability minimizes the frequency of breakdowns and maintenance issues, contributing to reduced operational downtime.
By automating intricate processes and maintaining consistent performance, robotics helps businesses achieve smoother and more efficient operations.
This efficiency is crucial for industries with high production volumes and tight deadlines.
Improved Accuracy
Robots excel in performing tasks that require high levels of precision.
The accuracy benefits include:
- Minimized Errors: Robots are programmed to follow exact instructions, which significantly reduces the likelihood of errors.
This precision is especially valuable in tasks that require meticulous attention to detail, such as assembly and calibration. - Enhanced Quality Control: Robots ensure high standards of quality by consistently executing tasks with precision.
Robotics ensures high standards of product quality and reliability in the pharmaceutical and electronics industries.
The ability of robots to perform tasks with exacting accuracy leads to fewer defects and enhances overall product quality.
This accuracy is particularly important for sectors where precision is critical for safety and performance.
Cost Savings
While the initial investment in robotics can be substantial, the long-term cost savings are significant.
Key aspects include:
- Lower Labor Costs: Automation reduces the dependency on manual labor, leading to substantial wage savings.
Robots handle repetitive tasks, allowing human workers to focus on more complex and value-added activities. - Decreased Operational Costs: Robotics systems are designed for efficiency, resulting in lower energy consumption and maintenance costs.
Their durability and reduced need for frequent repairs contribute to overall cost savings.
Over time, these financial benefits offset the initial investment in robotic technology, making it a cost-effective solution for many businesses.
Flexibility and Adaptability
Modern robots are versatile and can be programmed for a wide range of tasks.
This flexibility offers several advantages:
- Adaptable Workflows: Robots can be reconfigured to perform different tasks as needed, providing versatility in production processes.
This adaptability is beneficial for businesses that need to quickly switch between various products or services. - Scalability: Robotics systems allow businesses to scale their operations up or down based on demand.
This scalability helps companies adjust to market fluctuations without significant changes to their workforce.
Robots adapt to different tasks and scale operations, helping businesses stay agile and responsive to market changes.
Integrating robotics into the workplace brings numerous advantages, from increased productivity and efficiency to improved accuracy and cost savings.
As technology continues to advance, the role of robotics in job automation becomes increasingly vital.
By leveraging these benefits, businesses can enhance their operations, stay competitive, and achieve long-term success in an ever-evolving market.
Read: Top Companies Hiring CAD Technicians in the USA
Disadvantages of Robotics in the Workplace
The integration of robotics in the workplace brings efficiency and productivity, but it also poses significant disadvantages.
Understanding these drawbacks is crucial for a balanced perspective on robotics in employment.
Job Displacement and Loss of Employment
One of the most significant concerns about robotics in the workplace is job displacement.
As robots take over tasks once performed by humans, many workers find themselves out of a job.
This displacement is particularly pronounced in industries where automation can fully replace manual labor, such as manufacturing and assembly lines.
- Manufacturing Jobs: Automation in manufacturing has led to a sharp decline in factory jobs.
- Service Industry: Robots are increasingly performing tasks in customer service, reducing the need for human workers.
- Administrative Roles: Robotic process automation is eliminating traditional office roles like data entry and routine analysis.
This displacement is not just a temporary issue; it leads to long-term unemployment for many workers, especially those lacking the skills to transition to new roles.
Loss of Skill Development
Robotics in the workplace also leads to a loss of skill development among workers.
As robots take over complex tasks, human workers have fewer opportunities to develop and hone their skills.
This results in a workforce that may struggle to adapt to new challenges or technologies.
- Reduced Hands-On Experience: Workers gain less practical experience, which is crucial for skill mastery.
- Decreased Opportunities for Training: Companies may invest less in employee training when robots perform critical tasks.
- Limited Career Advancement: Without skill development, workers find fewer opportunities for career growth and advancement.
This stagnation in skill development can make it harder for workers to remain competitive in the job market, further exacerbating the issue of job displacement.
Economic Inequality
The rise of robotics in the workplace contributes to increasing economic inequality.
While companies benefit from the cost savings and efficiency of automation, the financial gains are often not shared with displaced workers.
This creates a widening gap between the wealthy and the working class.
- Concentration of Wealth: Profits from automation tend to concentrate in the hands of business owners and shareholders.
- Reduced Wages: Workers who remain employed may face wage stagnation or even reductions as robots take over high-paying tasks.
- Unemployment: Displaced workers may struggle to find new jobs, leading to long-term economic hardship.
Economic inequality fueled by robotics can lead to social unrest and a decrease in overall economic stability.
Addressing this issue requires careful consideration of policies and strategies to ensure that the benefits of robotics are shared more equitably.
Generally, while robotics offers many advantages in the workplace, the negative impacts on employment, skill development, and economic equality cannot be ignored.
To mitigate these disadvantages, it is essential to explore solutions that balance technological advancement with human welfare.
Read: Best Online Courses for CAD Technician Training
Industries Affected by Job Automation
Robotics and automation have reshaped various industries, leading to significant changes in job roles.
As companies seek efficiency and cost savings, they increasingly turn to robotics to perform tasks once handled by human workers.
This shift has affected several industries, leading to the transformation or elimination of certain job roles. Manufacturing
Transform Your Career Today
Unlock a personalized career strategy that drives real results. Get tailored advice and a roadmap designed just for you.
Start NowManufacturing is among the industries most impacted by automation.
Robots now handle assembly lines, material handling, welding, and painting tasks.
These roles were once filled by human workers.
Automated systems have replaced repetitive tasks, leading to a reduction in manual labor jobs.
However, this shift has created demand for technicians and engineers who maintain and program these machines.
Retail
The retail industry has also felt the effects of automation.
Self-checkout kiosks and automated inventory systems have changed the landscape.
Cashiers and stock clerks face reduced job opportunities as machines take over these roles.
In warehouses, robots handle picking, packing, and sorting tasks, reducing the need for human labor.
The rise of e-commerce has further accelerated this trend, leading to the closure of brick-and-mortar stores and the loss of retail jobs.
Transportation and Logistics
Transportation and logistics have seen significant changes due to automation.
Autonomous vehicles, drones, and automated warehouses are transforming the industry.
Truck drivers, delivery personnel, and warehouse workers face the threat of job displacement.
As companies invest in self-driving technology, the demand for human drivers may decline.
However, new roles in monitoring and managing automated systems are emerging.
Agriculture
In agriculture, automation is transforming how crops are planted, maintained, and harvested.
Drones, autonomous tractors, and robotic harvesters are reducing the need for manual labor.
Tasks like planting, spraying, and picking are increasingly performed by machines.
This shift eliminates some agricultural jobs but also creates opportunities for skilled operators and machine maintenance experts.
Healthcare
Healthcare is not immune to automation.
Robots assist in surgeries, medication dispensing, and patient monitoring.
While these technologies enhance efficiency and precision, they also reduce the need for certain healthcare roles.
For example, robots performing surgeries may reduce the demand for surgical assistants.
However, automation in healthcare also creates new opportunities for roles focused on managing and maintaining these advanced technologies.
Financial Services
The financial services industry has also experienced the impact of automation.
Algorithms now handle tasks like data analysis, trading, and customer service through chatbots.
Bank tellers, financial analysts, and customer service representatives face job displacement as these roles become automated.
However, new opportunities are emerging in developing and managing financial automation systems.
The rise of robotics and automation is transforming industries and changing the job market.
While some roles are being eliminated, new opportunities are emerging for those with the skills to work alongside and maintain these technologies.
Adaptation and continuous learning are essential for workers to thrive in this new era of automation.g job market.
Read: How to Build a Strong CAD Technician Portfolio
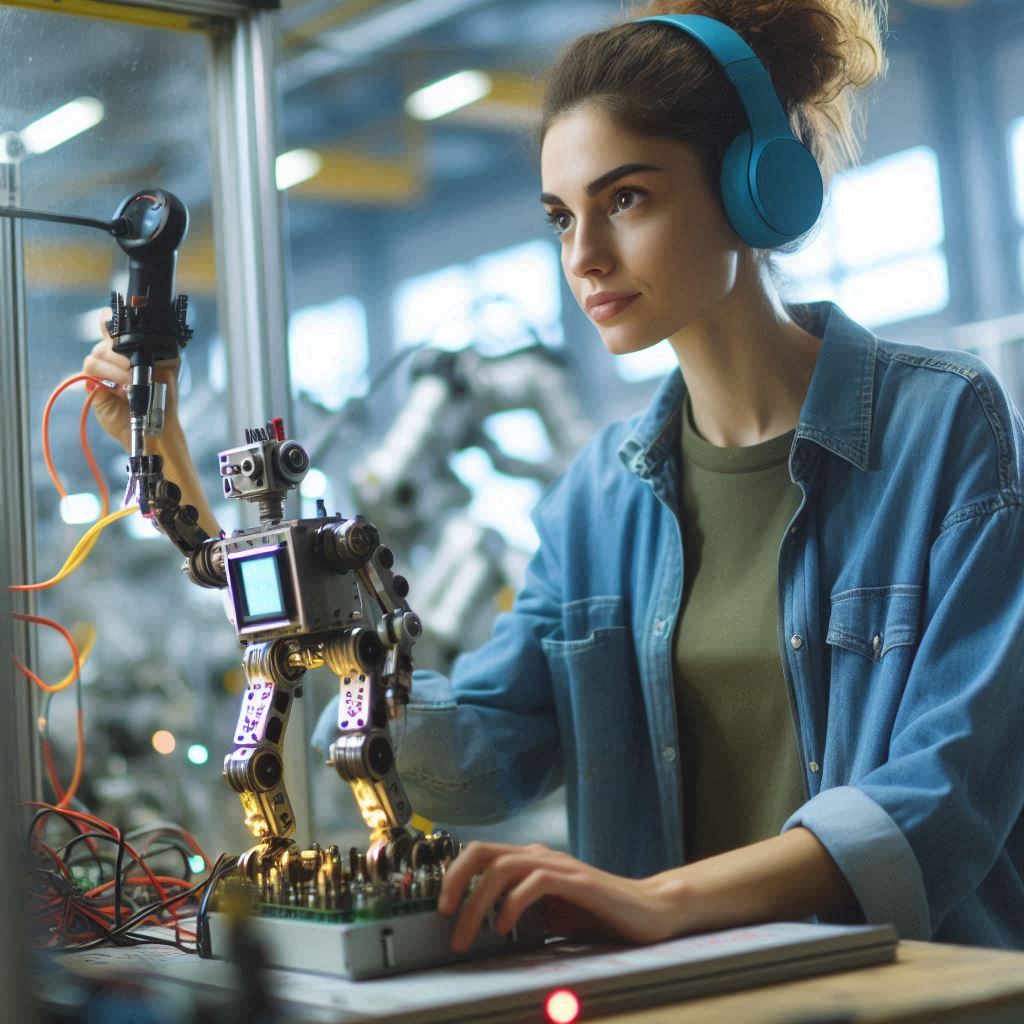
The Future of Job Automation
Predicting the Future Impact of Robotics on Employment
Robotics is rapidly reshaping industries, transforming how businesses operate.
The future of job automation presents both opportunities and challenges for employment.
As robotics continues to advance, the effects on the workforce will be profound.
Jobs involving repetitive tasks will likely be the first to experience automation.
Workers in industries such as manufacturing, logistics, and retail may face significant changes as robots take over manual tasks.
Acceleration of Job Automation Due to Technological Advancements
Technological advancements are accelerating the pace of job automation.
Innovations in artificial intelligence (AI), machine learning, and robotics are making it easier to automate complex tasks.
For example, self-learning algorithms enable robots to perform tasks previously thought impossible for machines.
As these technologies evolve, the range of jobs susceptible to automation will broaden.
Key areas likely to see increased automation include
- Manufacturing: Robotics will continue to dominate assembly lines, reducing the need for human labor.
- Retail: Automated checkout systems and inventory management robots will streamline operations.
- Healthcare: Robots will assist in surgeries and patient care, potentially replacing some roles.
- Transportation: Autonomous vehicles could eliminate many driving jobs, from taxis to long-haul trucking.
The Future Workforce: Adaptation and Reskilling
As robotics and automation grow, the workforce must adapt.
Reskilling and upskilling will become essential for workers to remain relevant in the job market.
Governments and educational institutions will play a crucial role in providing training programs that prepare workers for the future.
To prepare for the future of work
- Emphasize Lifelong Learning: Workers should continuously update their skills to keep pace with technological advancements.
- Explore New Career Paths: Transition into roles that require creativity, emotional intelligence, and complex problem-solving‘areas where humans excel over robots.
- Leverage Technology: Embrace technology to enhance productivity and create new opportunities for innovation.
Balancing Automation and Employment
While job automation may displace some jobs, it will also create new ones.
The challenge lies in managing this transition effectively.
Policymakers and business leaders must strike a balance between adopting automation and ensuring employment opportunities for all.
This may involve creating new jobs in tech-driven industries or implementing policies that support workers affected by automation.
In review, the future of job automation, driven by robotics, will undoubtedly impact employment.
Workers, businesses, and governments must prepare for the inevitable changes.
By embracing reskilling and lifelong learning, and by carefully managing the balance between automation and employment, society can navigate the challenges and opportunities presented by the rise of robotics.
The key to a successful transition lies in proactive planning and collaboration across all sectors.
See Related Content: Job Outlook for Engineering Technicians in the US
Strategies for Managing Job Automation
The rise of robotics in the workplace has raised concerns about job automation and its impact on employment.
While robotics offers significant benefits, it also poses challenges for workers.
Effective strategies for managing job automation can help mitigate these challenges and create a more balanced future.
Mitigating the Negative Effects of Robotics on Employment
To reduce the impact of robotics on employment, organizations and policymakers can implement the following solutions
- Promote Human-Robot Collaboration: Encourage collaborative robots (cobots) that work alongside humans rather than replacing them.
Cobots can perform repetitive tasks, allowing workers to focus on more complex and creative activities. - Implement Job-Sharing Programs: Implement job-sharing initiatives where multiple employees share a single role to prevent full displacement by automation.
- Support Small and Medium Enterprises (SMEs): Provide subsidies or tax incentives to SMEs adopting robotics while ensuring they retain and retrain their workforce.
- Create New Job Opportunities:Invest in sectors like healthcare, education, and creative industries to create new job opportunities and avoid automation risks.
- Encourage Ethical Robotics Development: Advocate for ethical considerations in robotics design and deployment.
Ensure technology complements human labor instead of replacing it.
Retraining and Reskilling Workers
As automation evolves, workers must adapt to the changing job market.
Retraining and reskilling are critical strategies to ensure workforce adaptability.
- Develop Lifelong Learning Programs:Encourage continuous education by offering accessible online courses, workshops, and certification programs.
These options help workers upskill and stay relevant. - Establish Government-Sponsored Retraining Initiatives: Governments can create retraining programs for workers in industries most affected by automation.
These programs should focus on in-demand skills, such as data analysis, digital literacy, and AI management. - Promote Industry-Academia Partnerships: Foster collaboration between industries and academic institutions.
Develop specialized training programs that align with current and future job market needs. - Provide Financial Support for Retraining: Provide grants, scholarships, or low-interest loans to workers pursuing retraining or higher education.
Remove financial barriers to career transitions. - Encourage Employer-Led Training: Companies should invest in employee development.
Offer on-the-job training, mentorship programs, and career growth opportunities within the organization.
Embracing a Balanced Future
Successfully managing job automation requires a collaborative effort between businesses, governments, and educational institutions.
Promote human-robot collaboration, invest in retraining initiatives, and encourage ethical robotics development.
This approach will create a future where technology and human labor harmoniously coexist.
These strategies not only mitigate the negative effects of robotics on employment but also empower workers to thrive in an increasingly automated world.
Government Policies and Regulations
The Role of Government in Regulating Job Automation
Governments play a crucial role in regulating job automation and robotics.
They establish policies that guide the ethical implementation of automation technologies.
These policies aim to balance technological advancement with the protection of the workforce.
Government regulations ensure that automation benefits society as a whole, not just corporations.
By creating standards and guidelines, governments help prevent exploitation and job displacement caused by unchecked automation.
Governments also promote fair competition by setting rules for the deployment of robotics across industries.
These regulations can include:
- Labor Rights Protections: Ensuring that automation does not undermine workers’ rights and safety.
- Ethical Standards: Establishing guidelines for the ethical use of robotics in various sectors.
- Tax Incentives: Providing incentives for companies that invest in retraining programs for displaced workers.
- Monitoring and Compliance: Enforcing regulations through regular inspections and audits.
Evaluating the Effectiveness of Current Policies
While governments have implemented policies to address workforce challenges related to automation, the effectiveness of these policies varies.
In some regions, policies successfully mitigate the negative impacts of automation.
However, in others, the rapid pace of technological change has outpaced regulatory efforts.
Transform Your Career Today
Unlock a personalized career strategy that drives real results. Get tailored advice and a roadmap designed just for you.
Start NowSuccesses in Current Policies
- Retraining Programs: Some governments have launched initiatives to retrain workers for new roles in a tech-driven economy.
These programs offer skill development in areas where human labor remains essential. - Universal Basic Income (UBI) Trials: A few countries have experimented with UBI as a safety net for those displaced by automation.
Early results show promise in reducing poverty and unemployment. - Regulations on Job Displacement: Some regions have enacted laws that require companies to assess the potential impact of automation on employment.
This includes strategies for minimizing layoffs and ensuring fair severance packages.
Challenges and Gaps
- Inconsistent Implementation: Policies differ widely across regions, leading to unequal protections for workers.
In some areas, lax regulations allow companies to prioritize profits over employee well-being. - Lack of Long-Term Planning: Many current policies focus on immediate solutions rather than long-term strategies.
As a result, they may fail to address the future challenges posed by rapidly advancing automation technologies. - Insufficient Funding: Retraining and education programs often lack the necessary funding to be effective.
Without adequate resources, these initiatives cannot reach the workers who need them most.
To sum it all up, government policies and regulations are essential for managing the impact of robotics and automation on employment.
While there have been successes, challenges remain in ensuring that these policies are effective and equitable.
Governments must focus on long-term strategies and consistently implement them.
This will protect workers and ensure a smooth transition to a more automated future.
Gain More Insights: Certifications for Systems Engineers: A Comprehensive Guide
Conclusion
The impact of robotics on job automation is undeniable.
It has led to increased efficiency in various industries, but it has also resulted in the displacement of certain jobs.
As technology continues to advance, it is crucial for individuals to stay informed about the changing landscape of employment opportunities.
By understanding the potential implications of robotics on job automation, individuals can better prepare themselves for the future job market.
It is essential to adapt and acquire new skills that are in demand to remain competitive in a workforce that is increasingly automated.
As we move forward, it is important for policymakers, businesses, and individuals to collaborate and find ways to mitigate the negative impacts of job automation.
By investing in education and training programs, we can ensure that people are equipped to handle the changing demands of the labor market.
While the rise of robotics may pose challenges, it also presents new opportunities for innovation and growth.
By embracing technological advancements and being open to change, individuals can position themselves for success in a rapidly evolving economy.
Therefore, it is crucial for readers to continue staying informed about the impact of robotics on job automation and employment opportunities.
By keeping up-to-date with the latest trends and developments, individuals can proactively navigate the changing landscape of work and secure a promising future.