Introduction
A robotics engineer is a professional who designs, builds, and tests robots and robotic systems.
They use mechanical, electrical, and computer engineering to develop automated solutions that boost efficiency and productivity in various industries.
Robotics engineers play a crucial role in developing new applications for robots, ensuring that these systems operate safely and efficiently.
Their work involves not only the initial design and construction of robots but also ongoing maintenance, troubleshooting, and upgrades to ensure optimal performance.
In today’s rapidly advancing technological landscape, the demand for robotics engineers is growing significantly.
Industries such as manufacturing, healthcare, and logistics increasingly rely on automation to improve operations and reduce costs.
As a result, companies are seeking skilled robotics engineers to develop and implement robotic systems that can meet these needs.
This surge in demand creates a promising career path for aspiring robotics engineers, offering opportunities to work on cutting-edge technologies and innovative projects.
Educational Requirements for Becoming a Robotics Engineer
Typical Degree Programs Needed
To become a robotics engineer, you typically need a strong educational foundation in engineering.
Most robotics engineers start by earning a bachelor’s degree in a related field such as mechanical engineering, electrical engineering, or computer engineering.
These programs provide essential knowledge in areas like mathematics, physics, and programming, which are crucial for robotics.
Many aspiring robotics engineers pursue specialized degree programs in robotics engineering or mechatronics.
These programs offer in-depth coursework focused on designing and building robotic systems.
They cover topics like automation, control systems, artificial intelligence, and robotic kinematics.
Additional Certifications and Training
In addition to a degree, obtaining certifications can enhance your qualifications.
For example, certifications in programming languages like Python or C++, which are often used in robotics, can be beneficial.
Certification in robotics through professional organizations, such as the Robotics Industries Association (RIA), can also add value to your resume.
Continuing education is vital in robotics engineering due to rapid technological advancements.
Engaging in workshops, online courses, or training programs helps you stay updated with the latest trends and tools in the field.
Many engineers also choose to pursue a master’s degree or Ph.D. in robotics to deepen their expertise and increase job prospects in research or academia.
To become a robotics engineer, you typically need a bachelor’s degree in engineering.
Specialized degree programs are also important.
Earning certifications and pursuing continuous learning are essential to excel in this dynamic field.
Designing and Building Robots: A Comprehensive Guide
The Process Of Creating A Robot From Start To Finish
Creating a robot from start to finish is an intricate and multi-faceted process that requires a blend of creativity, technical expertise, and meticulous planning.
The journey of robot creation involves several distinct phases, each critical to ensuring that the final product is both functional and reliable.
Below is a detailed breakdown of the entire process, from initial concept to final deployment.
The Various Components Involved In Robot Design
Conceptualization and Planning
The robot design process begins with conceptualization and planning.
This initial stage is crucial as it lays the foundation for all subsequent steps.
Engineers and designers start by defining the robot’s primary purpose.
Identify the specific tasks the robot will perform.
Determine if it will operate in a controlled environment, such as a factory, or in unpredictable settings, like disaster sites.
Answering these questions shapes the overall design strategy.
In this phase, engineers also consider the robot’s target audience, potential applications, and the broader impact of its deployment.
Detailed research is conducted to understand the needs and challenges associated with the intended tasks.
This information guides the brainstorming process, where different ideas and design possibilities are explored.
Sketches, diagrams, and rough models are often created to visualize the concepts.
Budget and timeline considerations are also addressed during planning.
Engineers must balance the project’s financial constraints with the desired features and capabilities.
Potential risks, such as technical challenges or material shortages, are identified, and contingency plans are developed.
Mechanical Design
Once the concept is clear, the next phase involves the mechanical design of the robot.
This step is all about translating ideas into detailed, workable designs.
Engineers use Computer-Aided Design (CAD) software to create precise 3D models of the robot.
These models include every mechanical component, from the overall structure to the smallest screws.
The robot’s frame is designed to be both strong and lightweight, allowing it to support all necessary components while remaining mobile.
The design must accommodate all the actuators, joints, and sensors required for the robot’s operation.
Engineers also consider the robot’s movement, whether it will need wheels, tracks, or legs, and design these elements accordingly.
Material selection is another critical aspect of mechanical design.
Engineers choose materials based on factors such as strength, durability, weight, and cost.
For instance, a robot designed for heavy lifting might use steel for its frame, while a drone might rely on lightweight carbon fiber.
Prototyping is often part of this phase, with engineers building physical models to test the mechanical design.
These prototypes help identify potential issues with the design and provide an opportunity to make adjustments before full-scale production begins.
Electrical System Development
With the mechanical design in place, attention turns to the robot’s electrical system.
The electrical design phase involves creating the circuitry that will power the robot and enable it to function.
Engineers start by designing the power supply system, which must be reliable and capable of delivering consistent power to all components.
The selection of microcontrollers, sensors, and actuators is crucial in this stage.
Microcontrollers serve as the brain of the robot, processing information and sending commands to the actuators, which in turn perform physical actions.
Sensors allow the robot to interact with its environment by providing data on variables such as temperature, distance, or pressure.
Circuit design and layout are key elements of this phase.
Engineers must ensure that all components are properly connected, that signals are transmitted efficiently, and that power is distributed evenly.
This requires careful planning to avoid issues such as signal interference or power surges.
Testing the electrical system is an iterative process.
Engineers test individual circuits and components before integrating them into the larger system.
Any issues detected during testing are addressed promptly, with revisions made to the design as needed.
Software Programming
Programming is the next critical step, where the robot’s software is developed.
This software controls all aspects of the robot’s operation, from basic movements to complex decision-making processes.
Engineers write code that is tailored to the specific tasks the robot will perform, ensuring that it can operate autonomously or under human supervision.
The software development process often starts with creating algorithms that dictate the robot’s behavior.
These algorithms are translated into code using programming languages such as Python, C++, or Java, depending on the robot’s requirements.
Simulations are a key part of software development.
Engineers test the software in virtual environments to observe how the robot responds to different scenarios.
This allows them to identify and fix bugs before deploying the software to the actual robot.
Once the software is deemed stable, it is integrated into the robot’s hardware.
Engineers conduct further testing, this time in real-world conditions, to ensure that the software works seamlessly with the robot’s mechanical and electrical systems.
Integration and Assembly
After designing and developing all individual components, engineers move on to the integration and assembly phase.
This stage involves bringing together the mechanical, electrical, and software elements into a cohesive and functioning system.
Assembly requires precision and attention to detail, as even minor misalignments can affect the robot’s performance.
Engineers carefully assemble the robot’s frame, install actuators and sensors, and connect the electrical system.
Wiring is particularly important, as poor connections can lead to malfunctions.
Once the robot is fully assembled, engineers conduct a series of integration tests.
These tests ensure that all components work together as intended and that the robot performs its tasks correctly.
Any issues discovered during integration are addressed, with adjustments made to the assembly or design as needed.
Testing, Refinement, and Deployment
The final stage of robot creation is rigorous testing and refinement.
Engineers subject the robot to a variety of tests designed to evaluate its performance, durability, and safety.
These tests often replicate real-world scenarios to ensure the robot can handle the conditions it will face during operation.
Testing is an iterative process.
Engineers identify any weaknesses or flaws and refine the design to address them.
This may involve tweaking the software, reinforcing mechanical components, or adjusting the electrical system.
Once the robot passes all tests and meets the required performance standards, it is ready for deployment.
Engineers may continue to monitor the robot during its initial operation, making further refinements if necessary.
Designing and building a robot is a complex, multi-phase process that requires expertise in mechanical, electrical, and software engineering.
From the initial concept to final deployment, each stage is critical to ensuring that the robot functions as intended.
Engineers carefully plan, precisely design, and thoroughly test robots, enabling them to perform various tasks in different environments.
They push the boundaries of technology with every new achievement.
Read: Future of CAD Technician Jobs in Engineering
Programming and Coding in Robotics Engineering
Programming skills are fundamental in robotics engineering.
They enable engineers to instruct robots on how to perform specific tasks, making them essential for the development and operation of robotic systems.
Importance of Programming Skills
Programming allows engineers to translate complex algorithms into instructions that robots can follow.
Without coding, robots would be unable to process data, make decisions, or perform tasks.
Programming is the foundation that brings robotic designs to life, making it a critical skill for anyone in the field.
In robotics engineering, programming skills are crucial for developing the software that controls robotic hardware.
Engineers use programming to create algorithms for motion control, sensor integration, and data processing.
These skills also allow engineers to simulate and test robotic behaviors before actual deployment, saving time and resources.
Common Programming Languages in Robotics
Several programming languages are commonly used in robotics, each serving specific purposes:
- Python: Python is widely used due to its simplicity and versatility. It’s often used for scripting, automation, and data analysis in robotics.
- C++: C++ is known for its performance and efficiency, making it ideal for real-time systems and low-level hardware control.
- Java: Java is commonly used for building user interfaces and mobile robotics applications.
- MATLAB: MATLAB is used in robotics for algorithm development, data analysis, and simulation. It’s particularly valuable for control systems and robotics research.
- Lisp: Although less common, Lisp is used in artificial intelligence and robotics for symbolic computation and reasoning tasks.
Understanding these programming languages equips robotics engineers with the tools needed to create, test, and refine systems.
Mastery of these languages opens doors to innovative solutions and advancements in robotics technology.
Read: How to Build a Strong CAD Technician Portfolio
Testing and Troubleshooting
Testing and troubleshooting are critical aspects of robotics engineering.
They ensure that robots function as intended and are reliable in real-world applications.
The Role of Testing
Testing is essential to verify the functionality and reliability of a robot.
It involves running the robot through various scenarios to ensure that it performs tasks accurately and consistently.
Testing allows engineers to assess whether the robot meets design specifications and operational requirements.
Through rigorous testing, engineers identify potential failures or inefficiencies in the robot’s hardware and software.
This process helps in minimizing errors, improving performance, and ensuring the robot’s safety and effectiveness.
Testing is crucial for validating the robot’s ability to operate in various environments.
It ensures the robot can handle unexpected situations.
Testing also confirms the robot can interact safely with humans and other machines.
The Process of Identifying and Fixing Issues
Troubleshooting begins when testing reveals issues in a robot’s performance.
The process involves systematically identifying, diagnosing, and resolving these issues to ensure the robot operates correctly.
Transform Your Career Today
Unlock a personalized career strategy that drives real results. Get tailored advice and a roadmap designed just for you.
Start NowProblem Identification
The first step in troubleshooting is identifying the problem.
This may involve observing the robot’s behavior during testing, analyzing data logs, or receiving error reports from the system.
Diagnosis
Once the problem is identified, engineers diagnose the root cause.
This can involve inspecting the robot’s hardware, reviewing the software code, or analyzing sensor data.
Engineers may use diagnostic tools or simulations to pinpoint the exact cause of the issue.
Solution Development
After diagnosing the problem, engineers develop a solution.
This could involve rewriting code, recalibrating sensors, repairing or replacing hardware components, or adjusting algorithms.
Implementation and Testing
The solution is then implemented, and the robot is retested to ensure the issue is resolved.
Engineers run the robot through the same scenarios to verify that the problem no longer occurs and that the robot’s performance is improved.
Documentation
Finally, engineers document the issue, the diagnosis process, and the solution.
This documentation is crucial for future reference and helps in improving the overall design and development process.
Testing and troubleshooting are iterative processes.
Engineers may need to repeat these steps multiple times to ensure the robot functions optimally.
These processes are vital for creating reliable, efficient, and safe robots that can operate effectively in diverse environments.
Read: Top Companies Hiring CAD Technicians in the USA
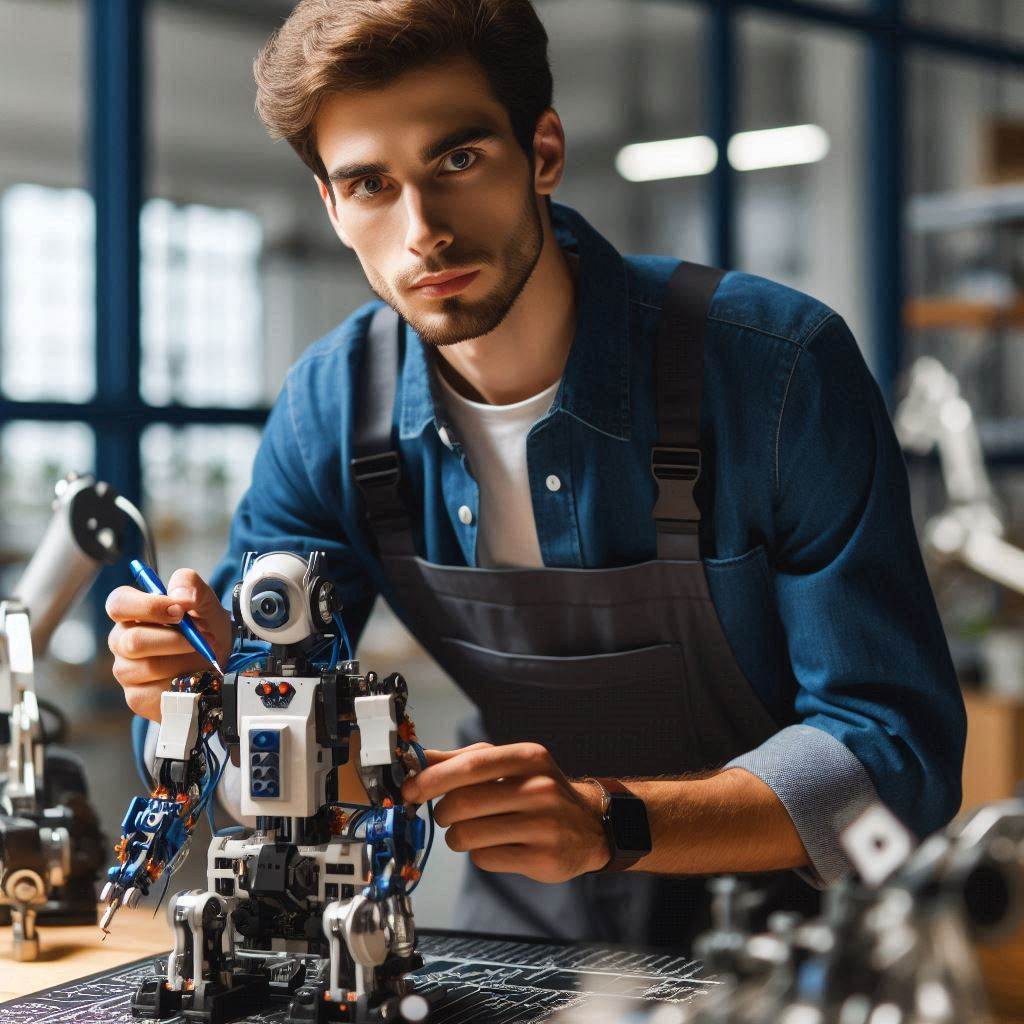
Collaboration with Other Engineers
The Importance of Teamwork in Robotics Engineering
Teamwork is the cornerstone of success in robotics engineering.
Given the complexity of robotics projects, robotics engineers must collaborate with specialists from various engineering disciplines to create robots that are not only functional but also innovative and reliable.
This interdisciplinary collaboration is essential for ensuring that all aspects of the robot, from its physical design to its software, work together seamlessly.
Without effective teamwork, even the most promising robotic concepts could fail to materialize into practical applications.
How Robotics Engineers Work With Mechanical, Electrical, And Software Engineers
Working with Mechanical Engineers
Mechanical engineers play a crucial role in robotics by focusing on the design and construction of the robot’s physical structure.
They are responsible for ensuring that the robot is durable, efficient, and capable of withstanding the demands of its intended environment.
Mechanical engineers work on aspects such as the robot’s frame, joints, and movement mechanisms, which are vital for the robot’s functionality.
For example, they may design the limbs of a robotic arm, ensuring it can lift and manipulate objects with precision.
Robotics engineers rely heavily on the expertise of mechanical engineers to create robust designs that meet specific performance criteria.
Partnering with Electrical Engineers
Electrical engineers are integral to the development of robotics, as they design and implement the electrical systems that power and control the robot.
Their work involves developing circuits, sensors, and control systems that allow the robot to perform its tasks accurately and efficiently.
Electrical engineers ensure that the robot’s power supply is stable and that the electrical components are integrated seamlessly with the mechanical parts.
For instance, they might design the circuitry that controls a robot’s motors, enabling smooth and precise movements.
The collaboration between robotics and electrical engineers is essential for creating robots that are both reliable and responsive to their environment.
Collaborating with Software Engineers
Software engineers are responsible for writing the code that dictates the robot’s actions, responses, and overall behavior.
Their work is critical for enabling the robot to interact with its environment, process information, and carry out complex tasks.
Software engineers develop algorithms that allow the robot to make decisions, adapt to new situations, and execute commands.
For example, they might program a robot to navigate through a dynamic environment, avoiding obstacles and reaching its destination.
Robotics engineers must collaborate closely with software engineers to fully integrate and optimize robot hardware and software components.
In the rapidly evolving field of robotics, such collaboration is not just beneficial but necessary.
Robotics engineers must collaborate effectively with other disciplines to drive innovation and succeed in this dynamic industry.
Read: Best Online Courses for CAD Technician Training
Research and Development
How Robotics Engineers Contribute To Advancing Technology
Robotics engineers are at the forefront of technological innovation, playing a critical role in advancing the capabilities of robots and automated systems.
Their work involves designing, testing, and refining robotic systems to make them more efficient, intelligent, and versatile.
By pushing the boundaries of what robots can do, these engineers contribute significantly to the growth and evolution of the robotics industry.
One of the key aspects of a robotics engineer’s role is to identify challenges within existing technologies and develop solutions that enhance performance.
This can involve everything from improving sensor accuracy and processing power to creating more adaptive algorithms for autonomous decision-making.
Improving robotic systems continuously enhances functionality and opens new possibilities across industries like manufacturing, healthcare, and space exploration.
The Importance of Staying Up-to-Date with Innovations
In the rapidly evolving field of robotics, staying up-to-date with the latest innovations is crucial for success.
Technological advancements occur at a breakneck pace, with new developments and breakthroughs emerging regularly.
Robotics engineers must continuously learn and adapt to these changes to keep their skills and knowledge relevant.
Engaging with the latest research is one of the most effective ways for robotics engineers to stay informed about current trends and emerging technologies.
This involves reading academic papers, following industry publications, and participating in research projects that explore new frontiers in robotics.
By staying informed, engineers can apply cutting-edge knowledge to their work, ensuring that they are always at the forefront of innovation.
Attending industry conferences and seminars is another important practice for robotics engineers.
These events provide opportunities to learn about the latest developments, network with other professionals, and gain insights from industry leaders.
Conferences showcase groundbreaking research, new technologies, and future trends. They are invaluable for staying ahead in the field.
Additionally, participating in professional development programs is essential for maintaining and expanding expertise in robotics.
These programs can include specialized courses, workshops, and certifications that focus on the latest tools, techniques, and technologies in robotics.
By investing in their ongoing education, robotics engineers can continuously improve their skills and stay competitive in a fast-paced industry.
In fact, the role of robotics engineers in research and development is pivotal to advancing technology.
Their ability to innovate and improve robotic systems drives the industry forward.
However, to maintain their edge and continue contributing to the field, staying up-to-date with the latest innovations is not just important—it’s essential.
Through continuous learning, professional development, and engagement with cutting-edge research, robotics engineers can ensure they remain leaders in this dynamic and rapidly evolving industry.
Maintenance and Repair
The Ongoing Responsibility Of Maintaining And Repairing Robots
Maintaining and repairing robots is an ongoing responsibility crucial for ensuring their optimal performance.
Regular maintenance prevents breakdowns and extends the robot’s lifespan.
Technicians must conduct routine checks, replace worn parts, and update software.
Skills and Knowledge Needed
Technical Expertise
Technicians need a deep understanding of robotics systems, including hardware and software components.
Knowledge of mechanical, electrical, and software systems is essential.
Troubleshooting Skills
Effective troubleshooting involves diagnosing issues and identifying the root cause.
This skill requires familiarity with common problems and their solutions.
Repair Techniques
Hands-on repair skills are vital.
Technicians must know how to disassemble, replace, and reassemble parts accurately.
This includes dealing with intricate wiring and precise mechanical adjustments.
Software Proficiency
Many issues involve software.
Technicians should be skilled in updating and configuring software, as well as debugging and fixing code errors.
Attention to Detail
Precision in identifying and correcting issues is crucial.
Minor errors can lead to significant malfunctions, so attention to detail is essential.
Continuous Learning
As technology evolves, so do robotics systems.
Staying updated with the latest advancements and techniques is necessary for effective maintenance and repair.
In general, maintaining and repairing robots requires a combination of technical expertise, troubleshooting skills, and ongoing education.
Technicians must be adept at both mechanical and software-related tasks to keep robots functioning smoothly.
Transform Your Career Today
Unlock a personalized career strategy that drives real results. Get tailored advice and a roadmap designed just for you.
Start NowConclusion
Robotics engineers hold diverse and essential responsibilities, including designing, building, maintaining, and repairing robots to ensure optimal performance.
They play a critical role in creating innovative robotic systems, moving from concept to prototype, and writing code to conduct thorough testing.
Their work ensures that robots function correctly and efficiently.
A successful robotics engineer must possess a diverse skill set, including strong technical expertise in mechanical, electrical, and software systems.
Problem-solving skills are vital for diagnosing issues and developing effective solutions.
Attention to detail is crucial in every aspect of their work, from design and programming to maintenance and repair.
Additionally, strong communication skills are necessary to convey complex ideas clearly to team members and stakeholders.
To excel in their roles, robotics engineers must continually learn and adapt to technological advancements.
This commitment to growth and innovation is essential for staying at the forefront of this dynamic and rapidly evolving field.